After decades of work on seeking alternative materials to build oilfield hardware, Saudi Aramco has formed a joint venture (JV) with Baker Hughes to begin using the materials.
The company, known as Novel Non-Metallic Solutions Manufacturing (Novel), will begin by producing pipe from reinforced thermoplastic.
The JV is hoping to expand the limits of a commercial product Baker Hughes has been manufacturing in a factory in Midland, Texas. Aramco has been researching and writing about the material in SPE papers going back to 2002.
Plastic promises to be a lighter, highly corrosion-resistant, and longer-lasting alternative to steel and offer significant savings at installation and over time. Long strings of pipe delivered on a reel can be spooled out like coiled tubing and connected without welding, which helps to speed up installation.
Alternative materials have made limited inroads against steel pipes, which have been the oilfield standard since the early days of the industry. Aramco’s goal is to push options, such as reinforced thermoplastic, into the mainstream and create jobs in Saudi Arabia.
“Non-metallic products are reshaping the industries and products we all depend on because they are more reliable, cost-effective, and offer sustainability benefits,” said Ahmad Al Sa’adi, Aramco’s senior vice president for technical services. The joint venture “reinforces our commitment to expanding the use of innovative non-metallic materials in our operations.”
For Baker Hughes the partnership supports its investment in “strategic areas like non-metallics, and our deep background in non-metallic product development will benefit a wide range of industries,” said Neil Saunders, executive vice president, oilfield equipment for Baker Hughes.
The companies have begun building a facility in King Salman Energy Park (SPARK) in Saudi Arabia’s Eastern Province where they will begin by making pipes.
While the brief press release did not offer further details, a 2018 SPE paper describing Saudi Aramco’s successful test of reinforced thermoplastic pipe for flowlines laid out some likely early challenges for the venture (SPE 193234).
That test showed the multilayered flowline, with protective layers inside and outside and fibers providing strength in between, could handle the temperature and pressure of produced gas. The cost was 30% of comparable steel pipe. A second test showed it could stand up to sour gas without difficulty (SPE 192424).
However, the paper said higher-performance tubing would be required to expand the use of reinforced thermoplastics for conventional gas production, and that Saudi Aramco should partner with a manufacturer to push the maximum temperature beyond 180o F and to build thermoplastic pipes to exceed the 6-in. diameter limit for pipes available at that time.
Baker Hughes has been working to expand the performance envelope for alternative materials. In late 2019 Baker Hughes agreed to work with Solvay to develop plastic offshore materials for higher-performance applications such as offshore flowlines and risers for use in ultradeep water.
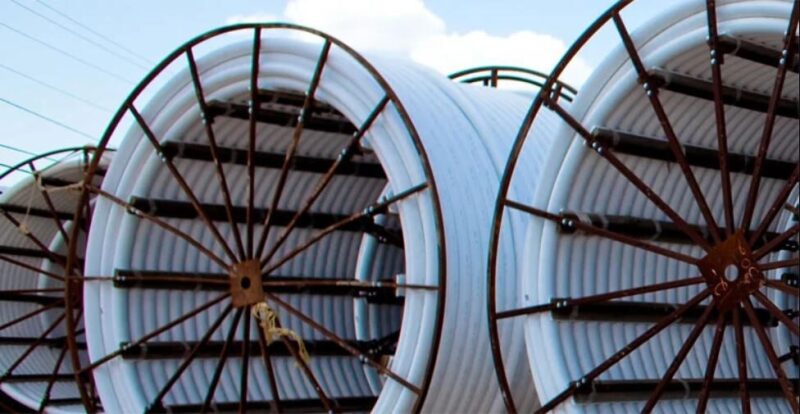
High-performance plastic tubing is rolled onto spools in West Texas to speed installation. Source: Baker Hughes