Two seemingly simple questions were raised by technical papers about drilling data: What formula did you use? What time did the event occur?
For anyone using data to analyze drilling performance or automate the process, getting both those things right is becoming increasingly important.
And as drilling relies more on digital controls and sophisticated analysis, getting those data wrong has become a serious problem.
One example is the standard measure used for the energy exerted to drill ahead—mechanical specific energy (MSE), for which there are multiple formulas to choose from. And even if the right one is used, its accuracy hangs on whether the needed steps were taken to properly gather the inputs to the formula.
Time sounds like a straightforward problem—just ensure all the clocks are in sync. The reality is that there are corporate firewalls blocking access to the reference clocks, a wide range of time-stamping practices, and an increasing amount of calculated data in the information stream based on inputs that are lost in calculation.
The MSE problem is simpler to solve but a lot of effort will be required to change the habits, and computer systems, supporting multiple formulas that can deliver significantly different results.
Different formulas for MSE and other drilling measures were created over the years for various reasons ranging from the creator’s research interests or a desire to limit the inputs needed for calculating MSE.
Pulldown menus on drilling data records have typically offered a menu of MSE options with names for formulas that vary; so, a user would need to know the formula to ensure the correct one was selected.
“When the pulldown menu offers a pick list with four types of MSE provided by the vendors, you do not know if you are using the right one now,” said Fred Dupriest, a Texas A&M professor who presented a paper on the issue at the IADC/SPE Drilling Conference and Exhibition in March (SPE 208777).
The paper reported on the work of a committee of 15 industry experts who chose a standard MSE formula which was laid out in the paper. It described how to gather the inputs and assigned names for the two approved versions—one for computing energy at the drill bit, and the other that included the drillstring.
A second paper presented at the conference described the need to begin a long-term effort to define how to accurately measure, gather, and record time data (IADC/SPE 208732).
“If data is not aligned correctly, you are not going to get the right result,” said Pradeep Annaiyappa, a senior director at Nabors for digital data initiatives at the drilling company, when presenting the time-measurement and recordkeeping paper.
The MSE StandardA standard method for calculating mechanical specific energy (MSE) has been proposed. The current use of multiple equations to calculate the energy used per volume of rock drilled presents a significant data-quality issue which has caused problems for those doing analysis or automation work. The standard is based on the original measure of MSE, the Teale equation. The two recommended equations look at this from different perspectives.
|
Solving New Problems
Timekeeping and MSE calculations have mattered for a long time, but the level of precision needed has changed now that these data points are being used for advanced analysis and automation.
In the past, the MSE formula used was not as critical because the driller was making decisions based largely on changes in the MSE trend. If the ups and downs in that measure of drilling energy expended were roughly similar, a driller could use the trend line to detect warning signals.
The data standard has changed because the absolute values of the points on those charts need to be accurate for data analysis and automation work using MSE and time-based data.
In either case it is hard to argue about the need for addressing the issues. What is going to be difficult is getting the many parties to cooperate on how things should be done, and then making adjustments that will require the changing of old habits and paying close attention to a lot of details.
“Someone has to take ownership. ‘How do I connect everything and still ensure every computer network is secure?’” Annaiyappa said.
The hardware needed for synchronizing clocks on a drilling rig—a network time-server accurate to one millisecond—does not cost much. More than one is required in areas with iffy connections such as the rig floor or the trailer on a land rig.
But there is a significant barrier to setting up the system: making the connections needed to the clocks behind corporate firewalls set up by the many companies working on a well pad.
“Most other industries do not see that problem. The owner can take responsibility and control,” Annaiyappa said.
These papers are part of a bigger challenge. “What we are trying to solve is this tsunami of information,” said Mahdi Parak, senior program manager, digital solutions for Halliburton. “We have multiple functions in well construction, and we need to connect to all of them.”
At the conference, Parak described how they brought order to a fractured drilling-rig management system where “chaos has ruled the day” (SPE 208686).
A key change was adding a timestamp to each bit of data based on its arrival time at the rig database. Nothing unusual there. “Everybody timestamps data when they receive it,” Annaiyappa said. In the not-so-distant past it “was not an issue because no one was sharing data.”
It has become an issue because the timestamps record when bits of information arrive and are stored in a database, which is often not the time the data were acquired.
Knowing the actual time may require an educated guess as to how long it took for a sensor reading to reach the surface using mud-pulse telemetry … and whether that data were included in the metadata and could be found after the fact.
Adding to the confusion are engineers who do things differently, such as using different MSE formulas. That inconsistency will bedevil anyone trying to analyze data sets calculated using different methods.
In this realm, the devil is in the metadata. Building databases that make it easy for users to find the time data they need is complicated by the fact that needs vary.
Using a hamburger as an example can help explain the problems encountered. For those worried about the burger’s taste, a time measure of how long it was cooked and how long it took to reach your plate will suffice. But if the meat tastes off, the data focus shifts to when the animal was butchered and how the meat was chilled.
Annaiyappa said the time system needs to serve the needs of “multiple vendors that are all concerned with their objective.”
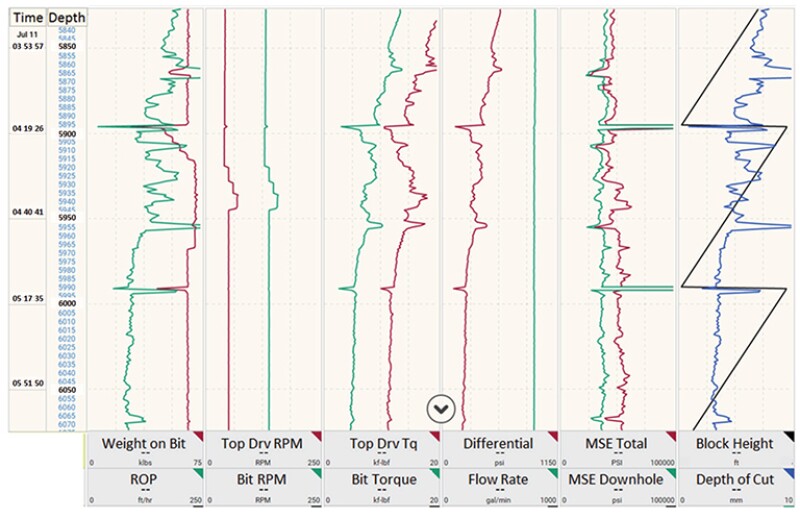
Correcting a Correction
Dupriest said standardizing the MSE formula will require “a culture change.” Getting it right requires more than using the right formula because the value of the output is a function of how well the inputs have been gathered.
The paper grew out of years of work by members of the SPE Drilling Systems Automation Technical Section who were aware of a range of drilling errors that could grow out of measurement errors.
“There are 14 potential input errors that can be quite large,” said Dupriest. About a quarter of that lengthy paper summarizes what the group decided about measurements.
The group also focused on which formula to use because over time, users tweaked the formula in ways that can generate significantly different results.
They chose the original formula developed in 1965 by a researcher cited in papers as R. Teale to calculate the energy needed to break rock.
Oil companies were heavily represented in the group that also included drilling service providers and a pair of companies whose businesses require maintaining data standards—Pason, a big name in the drilling data recorder business, and Corva, whose business has expanded from drilling monitoring and data to completions and geoscience advice.
The initial reaction to the MSE standardization paper among Corva users was positive, with some customers calling the company the week after the drilling conference to ask when the formula would be standardized, said Curtis Cheatham, vice president of research and development at the company.
It was not a surprising request for a company whose customers use its programs to create a standard view of drilling on all their projects. Corva’s programs include a handful of applications that rely on MSE inputs.
But for some of Corva’s customers, their standard MSE formula is based on a variation of the formula endorsed by the group. Their version applies a 0.35 adjustment factor to the result.
That factor was not in Teale’s equation, which was created to measure the energy required to break each type of rock. It is based on the weight on bit and torque applied at any moment.
Over time this mining tool was adopted by the oil industry. Drill-bit designers used it to test the effectiveness of new designs. Eventually, drilling engineers realized that surface measures of MSE, which reflect the energy required to break the rock plus the force added by downhole conditions, were a good indicator of what was happening downhole during drilling.
Dupriest, who was then working for ExxonMobil, played a big role in applying MSE to drilling decision making and promoting its use. For him, the aha moment was a chart buried in a paper on bit balling, which showed that MSE readings were correlated with that drilling dysfunction.
That insight grew into an MSE-based system for faster drilling based on years of work in many types of rock, some of which generated MSE charts that looked quite different.
His progress was reported in a series of SPE papers, including one where the subsurface conditions led to readings so high that Dupriest made a change in the formula. In those wells the surface MSE measures were several times higher than they had observed previously due to “ductile failure.”
While those readings were not necessarily an indication of drilling trouble, they posed a problem for Dupriest. His goal was to convince drillers to change their approach to drilling based on the results of a physics-based formula, which in those wells looked oddly high.
Adding a 0.35 adjustment solved that problem for the wells he described in the paper. In later papers, where the MSE measures were in line with lower levels observed before the paper that led to the adjustment, Dupriest dropped the adjustment factor. Using the adjustment factor in those cases made the MSE look oddly low to drillers.
Ultimately he decided it was futile to try to smooth out differences in formations, but not everyone followed his lead.
A lot of users stuck with the formula that included the adjustment, including some Corva customers who point out it was introduced in a paper by Dupriest, Cheatham said.
Dupriest badly wants to convince people to stop using the adjustment. “That adjustment factor is wrong. It never should have been done. I never should have put it in the equation. It was part of my personal incentive for writing this paper,” he said.
Corva has developed a method for automating the conversion of historical well data that had been calculated using the 0.35 factor to allow the converted data to be used in studies based on the standard MSE formula.
When asked about the future of standardization of drilling data, Cheatham offered a comment that could apply to both projects. “I think it is absolutely a good change,” he said, adding that as is often the case in the drilling business, “It is going to be slow. It is not going to happen overnight.”
Cause and Effect
The short description of what it takes to synchronize the clocks used for drilling is pretty straightforward. A highly accurate clock frequently sends out a time signal to the many sensors and other timekeeping devices to ensure their accuracy.
The initial barriers to entry are corporate firewalls put in place to fend off hackers. There are several ways to create connections through firewalls, but Annaiyappa said convincing IT departments that these are totally secure is hard because companies are wary about intrusions.
One option puts a company’s clocks in a secure node within their digital network, where every incoming data packet is scanned to ensure it is delivering only the required time data, Annaiyappa said.
This method, known as segmentation, is used in other industries, and he said it has been tried in the oil industry. Another option is to move time syncing into a corporate cloud created for the purpose.
The IADC Cybersecurity Committee is working on a recommendation for using network segmentation, Annaiyappa said.
This is one of the issues Nabors is working on with Halliburton in a partnership to overcome barriers to time data sharing. Halliburton can play a significant role in a drilling project by providing multiple on-site services, but Parak said the key data managers are the drilling contractor and the company managing the electronic data recorder.
This may include a template to help ensure that the data needed by users are saved and can be found.
“If the source of the data provides time of acquisition, it should be the main timestamp for the data and one should not re-stamp the data,” Parak said. However, he added that “if the time of acquisition for each sensor is not being provided, then the closest time (which is the aggregation at the rig) could be considered as the timestamp.”
Many Timestamps
Time is an increasingly important data point in drilling for those trying to build a time series, automate a process, or find a bit of data.
The prime source of this information is in a timestamp, but identifying the right one can be a challenge.
Users whose data is time-stamped when it arrives at a data recorder on the rig have asked service companies to estimate the data transmission time so they can estimate when the original measurement was taken.
And sometimes those transmission time estimates go missing after a timestamp is added by a third party, said John Macpherson, a coauthor on the time paper and a Baker Hughes chief consulting scientist.
When asked about this, Parak said Halliburton “does not have that issue keeping the timestamp from other sources.” He added that sensor acquisition time is a critical bit of information.
Searching such databases, though, can be a challenge because they are organized based on timestamps, and “unfortunately, synchronized time-stamping is rarely true,” according to Annaiyappa’s paper.
There are many reasons such as the heat and vibration downhole cause sensors to malfunction. To maximize the value of the information flowing up to the drilling database, computers behind the drill bit distill the data by putting it into a formula that reduces it to a single reading, making it possible to send more-valuable information to the surface.
However, that process raises lots of questions about the time by obscuring the time of data collection and mixing real-time data acquisition with older ones.
The answer offered by the paper: “There are no solutions that shall be considered as better than others. All that matters is that the data provider is transparent about which method is used.”
After delivering the paper, Annaiyappa was asked to describe the payoff for better timekeeping and records that might motivate a company to invest the time and money required to fix things.
The paper pointed out that uncertain time measures are a problem for those developing plug-and-play equipment and applications that work seamlessly with products made by other companies. Time uncertainty adds complexity, increasing the cost and the risk of unreliable performance.
That cost sounds real but quantifying it accurately enough to satisfy an MBA during a budget session would be hard. On the other hand, addressing these problems does not cost much.
“You are not spending a lot to make this happen. It is mostly about procedures,” Annaiyappa said. Ultimately, “the market is going to push everybody to integrate.”
For Further Reading
IADC/SPE 208777 Standardization of Mechanical Specific Energy Equations and Nomenclature by Fred Dupriest, Texas A&M University; Paul Pastusek, ExxonMobil Upstream Integrated Solutions Company; Stephen Lai and Bob Best, Pason Systems; and Michael Behounek, Apache Corporation, et al.
IADC/SPE 208732 Best Practices to Improve Accurate Time Stamping of Data at the Well Site by Pradeep Annaiyappa, Nabors Corporate Services; John Macpherson, Baker Hughes; and Eric Cayeux, NORCE Norwegian Research Centre AS.
SPE 208686 Building and Deploying an Open Plug-and-Play Solution for Supervisory Well Construction Automation by Arnfinn Grøtte, AkerBP; Julien Marck, Mahdi Parak, Moray Laing, and Oddbjørn Kvammen, Halliburton.