A new measurement-while-drilling (MWD) tool has been designed that can operate reliably at 200°C and 207 MPa, providing real-time direction and inclination surveys, azimuthal gamma ray, annular and internal pressure while drilling, and shock and vibration measurements. An operator in the Gulf of Thailand used this new MWD technology to drill wells in ultrahigh-pressure/high-temperature (HP/HT) reservoirs without the need to stop operation because of temperature limitations. Savings of ½ day per well have been achieved.
Introduction
Offshore drilling in the Gulf of Thailand increasingly challenges logging operations, with temperatures greater than 200°C. Hundreds of wells need to be drilled per year in this environment to fulfill long-term gas contracts. High efficiency is required in such a high-volume operation.
Existing commercial MWD and logging-while-drilling (LWD) technologies are only capable of operating up to 175°C, with an inherent decrease in reliability at higher temperatures.
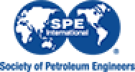