This paper reviews two newly developed novel completion systems that significantly reduce time spent performing multistage stimulation in environments where cost and consequence of failure are high. Both coiled-tubing and wireline-manipulated sliding-sleeve/valve systems and ball-drop-actuated systems have been developed and deployed, depending on the various completion and stimulation challenges faced. Since their first installation in 2009, these systems have been proven and refined in multiple wells for two major operators.
Background
For many of the fields requiring stimulation in the North Sea, cemented plug-and-perforation (plug-and-perf) completions have been used historically. It is a flexible solution in terms of the various types of stimulation designs that can be accommodated.
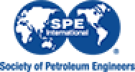