This paper illustrates comprehensive laboratory efforts undertaken to evaluate different high-viscosity friction reducers (HVFRs) and crosslinked gel products, their successful field application supported by a robust and effective field quality-assurance/quality-control (QA/QC) process, and the critical importance of maintaining an effective field/laboratory/field cycle to optimize fluid design and maximize results. A successful execution of several treatments in a challenging shale play in the Sichuan region of China achieved record proppant placements and, just as importantly, demonstrated repeatability and consistency over time, which had not previously been attained.
Geological Setting
The Sichuan Basin in southern China is a very active unconventional play targeting the Longmaxi Shale, a high-pressure/high-temperature shallow-to-deep marine shale deposited on top of the Baota limestone during the Late Ordovician and Early Silurian ages. The highly complex subsurface geomechanical environment is considered the main root cause of widespread casing deformation and associated challenges facing hydraulic fracturing.
Approach to Fracturing Design
The complete paper details several critical components of the design, including the following:
- The perforation strategy began with a conventional three-cluster-per-stage design typically used in the Sichuan Basin, but as the appraisal progressed, a more-aggressive cluster design was implemented, reaching 11 clusters per stage.
- The shorter cluster spacing associated with the 11-cluster-per-stage design, which was the most widely used, resulted in a short spacing between the clusters of 4–5 m.
- Hybrid pumping schedules with continuous proppant ramps, diversion stages, and improved fracture-fluid performance was adopted.
- The standard approach adopted by national operators in the Sichuan Basin of using intermediate-strength proppants in unconventional play was adopted.
- To achieve continuous ramps and higher proppant concentrations needed to boost fracture continuity and wellbore connectivity, an HVFR fluid was selected in conjunction with a crosslinked gel in the last part of each proppant ramp.
- Field QA/QC is detailed in a later section of the synopsis.
Fracturing Fluid Selection
Water Quality. In general, all tested fracturing‑water samples were high-quality water with pH values close to 7 and total dissolved solids ranging between 150–320 mg/L with almost no iron content.
Water-Compatibility Tests.
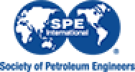