Frac hits were once a painful cost of doing business for Abraxas Petroleum. But today, the San Antonio, Texas-based shale producer has softened the blows dealt by this widespread and challenging problem.
Its approach, called “active well defense,” has been put to the test amid the rolling hills of the company’s North Fork oil field in McKenzie, North Dakota.
“Necessity is the mother of invention—and that’s our story here,” said Peter Bommer, vice president of engineering at Abraxas, who noted that the driver of its strategy was not production declines, as it has been for others. Instead, active well defense is designed to prevent temporary, yet costly, production stoppages caused by unabated frac hits filling parent wells with sand.
The company starts by injecting produced water at low pressures into older, parent wells. It flows down miles of wellbore and into the formation’s partially depleted fracture networks where it has proven to prevent the damage often caused by high-pressure hydraulic fracturing of new child wells—known as frac hits.
Active well defense relies on sporadic injections to reinforce the preloaded water. To do this, Abraxas has partnered with a technology vendor Abra Controls, whose custom communications network gives engineers “real-time pressure monitoring so we can watch the wellhead pressures in the parents, and when we start to see interference, we start pushing back on it,” Bommer said.
Active well defense is now used across Abraxas’ infill program in its 3,300-acre development targeting the Bakken and Three Forks shale plays. Its genesis and evolution are covered in two technical papers, the latest of which was published at the start of the year (SPE 184851 and SPE 189860).
Renewed Trend
Examples of similar strategies have recently emerged from other major North American plays. They include BHP Billiton’s “preloads” in the Eagle Ford Shale of Texas and Canbriam Energy’s “pump-ins” in the Montney Shale of Alberta. Similar tactics are being tested in the Permian Basin and the Anadarko Basin.
This trend sits on one side of the well-defense spectrum, while on the other are the more capital-intensive projects known as cube developments that drill and complete a dozen or more wells in quick succession to avoid the downsides of reservoir depletion. Published results on injection-based well defense are encouraging, but it remains unclear whether they will scale up to stem concerns over the shale sector’s ability to sustain record output in the face of falling productivity of new child wells.
These operations are distinct from refracturing, as both Abraxas and BHP emphasize that the injections use pressures that do not open new fractures, or affect existing ones much.
Injection-based defense is not stopping frac hits, said Marcus Bayne, a fracturing supervisor with Abraxas. “But if we can interfere with the interference, then we can have the fluid we’re injecting act as a shock absorber, or a diffuser, so we don’t push solid material into the parent wellbore.”
Tom Whitfield, a production engineer at BHP who helped lead the company’s defense program, agrees that interwell communication is not fully prevented. “You’re pumping so much volume and the wells are spaced so closely together, the fracs still interfere with the existing well,” he said. “This technique prevents the damage—you don’t get the large, high-velocity fluid sweep through your existing fracture network.”
The industry is in the early stages of studying the mechanisms behind what Bayne and Whitfield described, suggesting that more diagnostic and quantitative analysis may refine these approaches.
Researchers at the University of Texas at Austin are doing some of this work through modeling to make the process more predictable. They think benefits are achieved when injections are able to increase localized rock stress. This requires replacing the compressible gas found in the existing fracture networks with the right volume of nearly incompressible water.
And since the concept of loading wells is not entirely new, this development could be considered a renewed effort.
A technical paper authored in 2010 cites the mixed results of a “frac protect” program that involved slow fluid loading of 17 wells (SPE 136757). Mike Vincent wrote the paper and, after watching the industry struggle with the challenge for years, he continues to warn clients against trying to mitigate production-harming frac hits without first having a plan to acquire critical data.
“Careful study of frac hit timing and severity, accompanied by long-term well communication evaluation, provides a direct measurement of fracture conductivity and durability,” said the independent frac consultant of Colorado-based FracWell.
During offset stimulations, he advocates using parent wells as an “antenna” since they can deliver “nearly free data” on interwell communication through supervisory control and data acquisition systems (SCADA) or digital gauges. And to draw the most usable conclusions, these sources must be time-synchronized.
With better data, some operators have even identified why frac hits sometimes generate large improvements to parent well productivity. But Vincent highlighted that the “much bigger picture” involves figuring out optimal “well spacing, development sequence, right-sizing the frac to correspond with well spacing, and how to document and demonstrate effective diversion.”
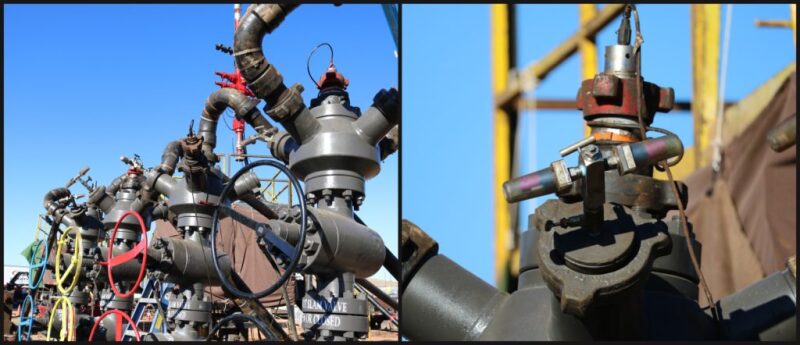
Each well being hydraulically fractured (left) in the zipper configuration are equipped with cone-shaped pressure sensors (right) that feed real-time data to completions engineers on-site and in corporate headquarters.
Keeping the Laterals Clean
The first frac hit for Abraxas came in 2011, about a year after it drilled its original well in the North Fork field. After fracturing the first two child wells, issues in the parent were glaring.
“When we went to put that well back on, rods were stuck and we went into a miserable fishing job,” recalled Bommer. The coiled-tubing work recovered the pumping unit’s rods and production tubing to reveal they were all caked with sand, shale fragments, and other debris.
The good news was that oil once again flowed from the parent, which returned to its natural production curve in a few weeks. However, the bill for the cleanup was about $450,000—imposing a substantial knock to the well’s economics.
In search of ways to avoid sanding-in more wellbores, Abraxas spent the next few years testing various strategies. Nothing worked until, in mid-2016, Bommer and his engineering team launched their injection strategy.
“It made sense to us, that if we could push fluids the other direction, then we could at least keep our laterals clean,” he explained. “And if I can get a loaded wellbore, then the only thing I need to be able to do to accomplish that is a pressure that’s capable of beating the wellhead pressure that the hit is delivering to me.”
Since implementing active well defense, the company has used it in more than 20 wells (including one in the Permian Basin) and credits it with preventing frac hits from causing wellbore damage to a large majority of them. As mentioned by Bommer, a caveat to its effectiveness is whether the reservoir is too depleted to maintain a water column in the wellbore.
Overall, Abraxas reports that production impacts from frac hits in its Bakken wells are now net-neutral, with a few wells seeing uplift. Notably, the company has also stepped up the water and proppant volumes of its fracturing treatments over an almost 18-month-long defense campaign.
Compared with cleanups, the defense economics are easily accepted by Abraxas, which has the advantage of keeping water costs low thanks to a piped water disposal unit that sits in the middle of its field. In a six-well defense project last year, costs came out to about $260,000. Horsepower represented less than half of that figure, while real-time monitoring was just under 30%.
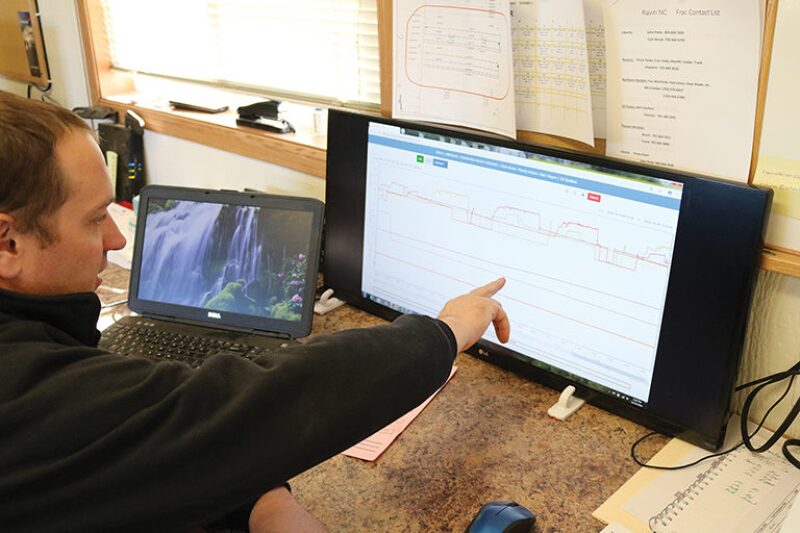
Marcus Bayne, a fracturing supervisor with Abraxas Petroleum, points to a gently rising slope indicating rising pressures in an offset well.
The Eyes and Ears of Defense
Abraxas has had help from Liberty Oilfield Services, which provides the pressure pumping muscle and did some of the early research that shaped the technique. But the eyes and ears of active well defense are furnished by Abra.
With Abra’s wellhead-pressure sensors, operators are not reliant on visual checks of pressure gauges, or the 10–15-minute data rates that are common for SCADA, far too slow to react to pressure signals that rise in minutes or seconds.
In contrast, the small, wireless sensors typically measure pressure at 1-second intervals that can be observed almost instantly via a communications network specially designed for remote oil fields.
A decade ago, this kind of data acquisition project may have taken weeks to set up. But thanks to the rising capabilities of sensors and field communications, Abra can do it in under a day, after which it simply sends an email to engineers.
“We give them a link—there’s no software to download—and when they click, they are able to see treatment wells on one plane and offset wells on another plane, all sharing the same time stamp,” said Clinton Lott, head of special projects at Abra.
In addition to enabling rapid data access, “the time stamps are absolutely critical,” said Mike Rainbolt, a senior technical advisor at Abra. “I need to know when an event started, and I also need to know when the reaction to that event starts.”
Rainbolt was previously a completions engineer with Apache Corporation, where he spent several years studying the production impacts of frac hits. His experiences are documented in two recent papers (SPE 187192 and SPE 189853).
By tying them to the Internet’s network time protocol, each sensor’s time stamp is continuously synchronized. Rainbolt said that without accurate time stamps, engineers spend days manually reconciling SCADA and other instruments that are susceptible to time drift or not set to the same clock time.
By having all the sensors synced, and set to at least 1-second data readings, operators can get granular. One example Abra has shown involves small pressure increases that signal rock compression, or stress shadowing, and indicates that problematic fracture interactions are potentially imminent.
“Do not judge by the magnitude of the pressure increase,” advised Rainbolt. “It’s all about how much fluid and sand has moved into that well, and the offset that you’re fraccing into may already be depleted, so you wouldn’t expect to see a lot of pressure.”
Abra plans to use this data to estimate the dimensions of fracture geometry. With multiple sensors placed on both the fracturing and parent wells, Rainbolt said operators should be able to quickly determine the preferred pathways of fracture growth which, “is a way of proving asymmetry, and how much depletion affects the magnitude of asymmetry.”
From Small Waves to Big Hits
In October, Abraxas and Abra teamed up for their largest active well defense project to date. More than 20 pressure and flow sensors were installed on three pad sites in the North Fork field.
The result turned the wells into a team. Playing offense were four child wells stimulated through zipper fracturing. A couple of miles to the south sat the defenders: two pads with four wells each that pointed straight toward the zipper pad.
As pressures rise in the parent wells, completions supervisors watch their screens closely. These increases appear as small waves. Between 20–50 psi, they are initially seen as benign stress shadows. But often the waves keep growing until “all of a sudden boom, we’re getting 1,000-psi increases, and you are at full hydraulic communication at that point,” Bommer said. “It’s pretty fascinating to watch.”
The idea is to pump into parent wells before such a large spike occurs. They are first preloaded with about 1,000 bbl of water. Like a cocked piston, this column is pushed by the reactive pumping to maintain pressure inside the fractures.
Abraxas’ largest injections have totaled around 10,000 bbl for an entire pad. A majority of that volume is used whenever pressures rise, even just a few psi, as the idle pumping units are alerted to begin injecting into parent wells at a gentle rate ranging from ½ to 2 bbl/min. They do not stop until the stage is completed. This may be repeated dozens of times per completion.
“Very early on in when we started active well defense, we wouldn’t necessarily push back against every hit,” said Bayne. “But now, we’ve come to understand it is probably a good idea to do that because it seems like it can delay the progression of the intensity of the frac hits.
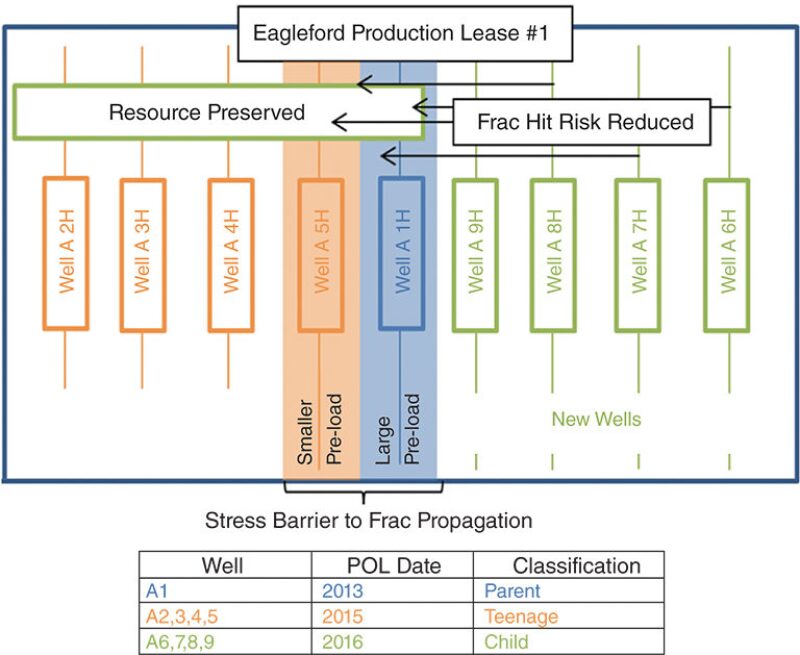
This diagram shows the concept behind BHP’s preloading strategy. Source SPE 191712.
Passively Loading Wells Works Too
Another defense practitioner is Devon Energy, which established a joint venture in the Eagle Ford with BHP in 2014. The Oklahoma City, Oklahoma-based company has tested preloading and what it calls recharging.
Recharging involves about 100,000 bbl of water, close to the initial stimulation volume. While preloads fill the fracture network, recharging goes further by changing the stress and pressure of the far-field rock. However, such large volumes of water may be cost-prohibitive for some developments.
Calgary-based Canbriam is also using a water injection practice (URTeC 2902707) in a Montney gas field. After seeing frac hits send debris into parent wells that then flowed into its production facilities, it started using preloads of about 3,500 bbl. The paper concludes the preloads create a “high-pressure halo” around older wellbores, “which further reduces the ability of the child well completion to reach and therefore damage the parent well.”
In the Eagle Ford, BHP’s engineers saw that 90% of infill wells generated frac hits. Unlike in the Bakken, their top concern was permanent and serious production losses.
Impacted parent wells had average oil flow drop by 40%, while initial child wells showed a 20% worse performance compared with the pad’s older wells. Only a few of these parent wells returned to their baselines. Some never flowed again.
Before announcing plans to sell all of its shale assets, the company spent a few years trialing preloads until it was able to reverse the troubling pattern. Details were shared by Whitfield in September at the SPE Annual Technical Conference and Exhibition (SPE 191712), who said the latest iteration represented a “100% technical and economic success.”
“The recipe is really simple: you pump a large volume, you pump it at a low rate, you preload as close to the start of the frac as possible, and our most effective preloads have involved a surfactant and solvent package,” he said.
The company found more success with large preloads that require a full day to pump 20,000 bbl of fluid. Engineers eventually began surrounding some parent wells with a combination of large preloaded wells and smaller 10,000-bbl preloads. This created what Whitfield called a “pressure barrier” around the encircled wells, enabling those parents to keep producing without seeing damaging interference from offset stimulations.
“We saw no change in pressure, we saw no change in water production, and we saw no change in oil production for any one of the fully surrounded wells,” he said.
BHP has preloaded almost 100 wells, not one of which needed remediation work. The child wells completed next to the preloads also performed above predicted type curves. The parent wells loaded with production chemicals saw more oil flow than prior to the operation likely because the additives positively altered interfacial tension and rock wettability.
“So we make the parent well better, and we get full benefit of our new infills—it’s huge,” Whitfield said.
Modeling Explains Some, But Not All Effects
BHP could not successfully describe why its approach works using commercial modeling technology. Abraxas has not used modeling to craft its strategy. But others are turning to the simulators.
Researchers at the University of Texas have developed a new modeling software that supports fluid loading, which is being used with an undisclosed operator in the Anadarko Basin. The model is explained in a paper that was presented at the recent Unconventional Resources Technology Conference and Exhibition (URTeC 2881265).
Deepen Gala, a PhD student at UT and lead author of the paper, acknowledged that the model does not account for everything happening in these scenarios; for example, how propped fractures react to the slow injection phase or when the frac hits come.
However, he said it illuminates other nuances that can help guide an operator’s defense recipes. One involves how stress increases with different fluid volumes and rates, a factor related to the amount of gas inside depleted fracture networks.
“That tends to impact how the water injection behaves, because as the gas is more compressible, you will tend to see a lower pressure increase during injection—but that does not mean you are not building up enough stress in the reservoir,” said Gala, adding that preloading strategies might be modified based on this information. “This was something that we saw as very important.”