Unmanned aerial vehicles, popularly known as drones, offer a combination of mobility, data-capture capabilities, and precision, making them invaluable tools across a multitude of sectors. Whether it’s the construction sector, which uses drones to survey and map land; the agriculture sector, which deploys drones to plant seeds and spray fertilizers; or the security industry, where they are used for surveillance of large areas, drones have become increasingly popular and versatile across industries in recent years.
The energy sector is no exception. Drones are adding value to a wide range of operations from pipeline inspections to environmental monitoring within the energy and chemicals business by performing tasks that are difficult, dangerous, or costly for humans.
Aramco began deploying drones in 2015 mainly to conduct inspections across seven facilities. Over the years, the company has expanded drone deployment. It is now deploying more than 100 drones across most of its major facilities.
While being crucial for the inspection and maintenance of onshore and offshore sites, storage tanks, and power system infrastructure, drones are also supporting a wide range of field operations, such as emergency response, security surveillance, aerial mapping, and environmental monitoring.
“The advent of drones in the oil and gas industry is a game-changer,” said Khalid Y. Al-Qahtani, Aramco’s senior vice president of engineering services. “Deploying industry-leading robotics and drone applications across Aramco’s business is driving safer, cost-effective, and more efficient practices.”
Inspection and Monitoring
Traditional asset inspections in the oil and gas sector can involve manual labor, scaffolding, and costly downtime. Inspections can also be hazardous, particularly when the sites are remote or an emergency can mean there’s a requirement to work at night.
Aramco is deploying drones as a quick and cost-effective way to inspect and monitor oil and gas assets, reducing the need for manual inspections, which can be both dangerous and time-consuming.
A Vertical Takeoff and Landing
Using drones to inspect tanks, for example, eliminates the need to erect and later dismantle scaffolding. This saves time and reduces risk, because maintenance staff are not required to work at high elevations or in confined spaces. Another benefit is that facilities such as flare stacks do not have to be shut down for inspections. Instead, a drone collects high-resolution thermal images while the flare stack is operating, checking for deformations, cracks, corrosion, and physical deterioration.
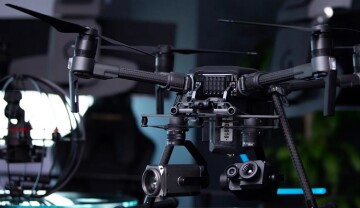
Recent advancement in Aramco’s drone deployment includes nondestructive testing, which involves collecting data about a specific material without damaging it. The company’s inspection department deploys ultrasonic testing drones that use high-frequency soundwaves to detect flaws, defects, or corrosion that may affect the performance and safety of industrial assets and infrastructure.
A special class of drones — the vertical takeoff and landing (VTOL) drone (Fig. 1) — is being used for inspections. VTOL drones are capable of flying continuously for several hours without the need for a runway during takeoff and landing, making them ideal for well monitoring, especially at giant fields where wells are spread over large areas. This class of drones is also being used for pipeline surveillance and monitoring.