International oil companies have been backing off growth plans in Canada’s oil sands.
Shell and Marathon have agreed to sell most of their oil sands operations. ExxonMobil recently removed 3.5 billion bbl of the ultraheavy crude from its proved reserves because it no longer plans to develop them any time soon, following a similar move by ConocoPhillips.
In a world with a surplus of oil production options, the oil sands suffers because the cost of development is high and the value of ultraheavy crude is low, with oil sands bitumen selling for USD 15/bbl less than the benchmark for light crude, and these projects require big financial commitments stretching out for decades.
“They (oil sands) are the most expensive kid on the block and that is not a good place to be,” said Ron Sawatzky, a principal researcher for InnoTech Alberta, and chair of the SPE Canada Heavy Oil Technical Conference. “US shale producers are the biggest competitors for oil sands. We cannot match the nimbleness of those guys.”
Among those competitors are ExxonMobil and ConocoPhillips, with large operations in unconventional plays in the US and Canada and significant oil sands operations.
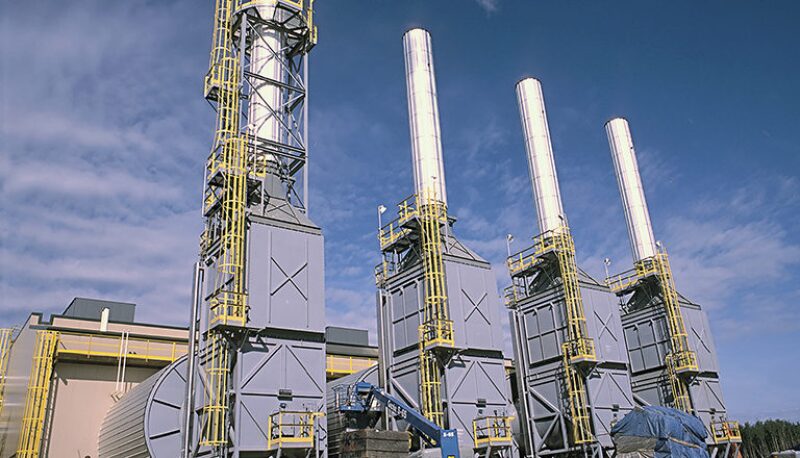
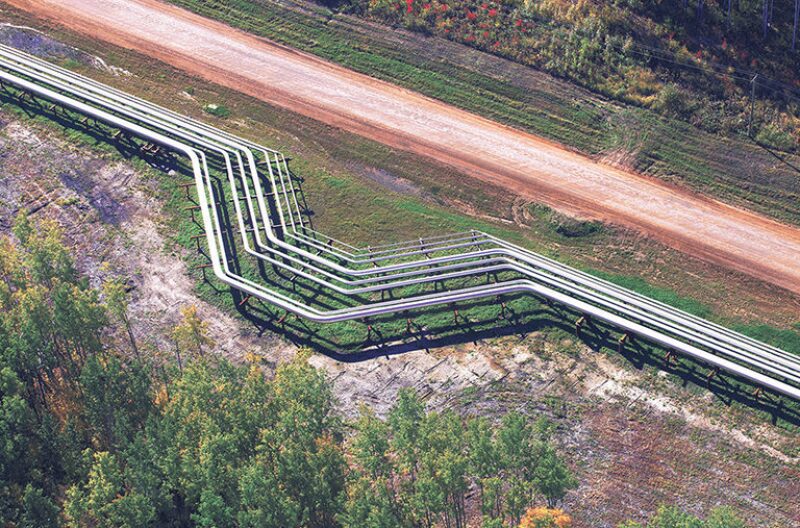
“We are seeing the same technologies and innovations driving lower costs and greater opportunities,” in the oil sands, Ryan Lance, chief executive officer at ConocoPhillips, said during a presentation at the March CERAWeek conference in Houston. But he keeps asking his oil sands team: “How can you do projects with a 3–5-year cycle time so you can adapt” to a business with big unexpected price swings.
Those who work in the oil sands are learning how to react faster to prepare for when oil may again be in short supply. “At Suncor we will spend around USD 200 million on technology in 2017 because business as usual does not cut it,” said Gary Bunio, general manager, strategic technology for oil sands, at Suncor. “We are working on things we will put in over a couple years, and things that will take a decade.”
The payoff for reviving future growth is huge—oil sands resources are estimated at 135 billion bbl according to the US Energy Information Administration—and there is cash flow to invest in technology. Efficient producers such as Suncor have reduced operating costs to turn a profit with oil prices as low as USD 35/bbl.
Longer term they are trying to significantly increase the efficiency of the method used to produce bitumen production in places too deep to mine, known by the acronym for steam assisted gravity drainage—SAGD.
While ExxonMobil’s Imperial Oil unit has backed away from its major expansion schedule, it is working on projects to commercialize solvent-assisted production. In a talk to SPE young professionals about the business, Rich Kruger, the CEO of Imperial Oil, advised: “Do not underestimate the potential for technology and this industry’s ingenuity.”
The History
Canadians would not be producing a lot of oil unless they were good at getting past barriers from tight reservoir rock to crude filled with sand. Darcy Spady, a Canadian and incoming 2018 SPE president, noted at the recent combined SPE Canada Heavy Oil and SPE Canada Unconventional Resources conferences in Calgary, “We were not blessed with easy rock.”
The economic challenges facing the oil sands affect both the mines, which dig up the oil sands from near the surface, and the pairs of wells used for SAGD. This story focuses on SAGD, which demands skills normally used by petroleum engineers.
Now every element of the SAGD process is being examined in search of ways to fundamentally lower the cost, speed up development, and reduce the environmental impact.
In the short run, the focus is on reducing aboveground waste with faster drilling and lower cost completions. For example, some operators and service companies are rethinking well pad development and eyeing simplified, standardized designs that limit engineering time and the risk of cost overruns.
“Now everybody wants something that is cheaper, benefits production, and is standardized,” said Majid Saeedi, a director and reservoir engineering consultant for Saman Associates.
Longer term, there is talk about changing the scale of production add-ons using modular equipment serving smaller groups of wells, allowing additions of about 10,000 B/D rather than 30,000 B/D, which would reduce the added investment and time required.
“Everything is shifted down a level and you can respond and move more quickly when the price changes,” Sawatzky said. It is too soon to know how that will look. “It is very embryonic … nobody has a picture of it.”
Two measures for this effort are the steel and the steam required. “We want to reduce the metal we have in our facilities,” Bunio said. Greater efficiency, simpler designs, and a smaller footprint commonly mean less steel used.
A key measure of efficiency for a SAGD producer is the volume of steam needed to produce a barrel of oil. The less steam per barrel of oil, the better. If it proves possible to drastically reduce the required heat per barrel, the steel for the equipment used to heat, transport, and process the water will also be reduced.
Less steel and steam can reduce both the cost and the environmental impact. “I see no conflict in reducing cost, reducing greenhouse gases, and reducing the environmental footprint. With less metal, we use less energy and it costs less,” Bunio said.
The biggest potential savings in the steel and steam needed can be found below ground. SAGD producers have worked for years on methods that add solvent to steam, or even replace the water completely with solvent.
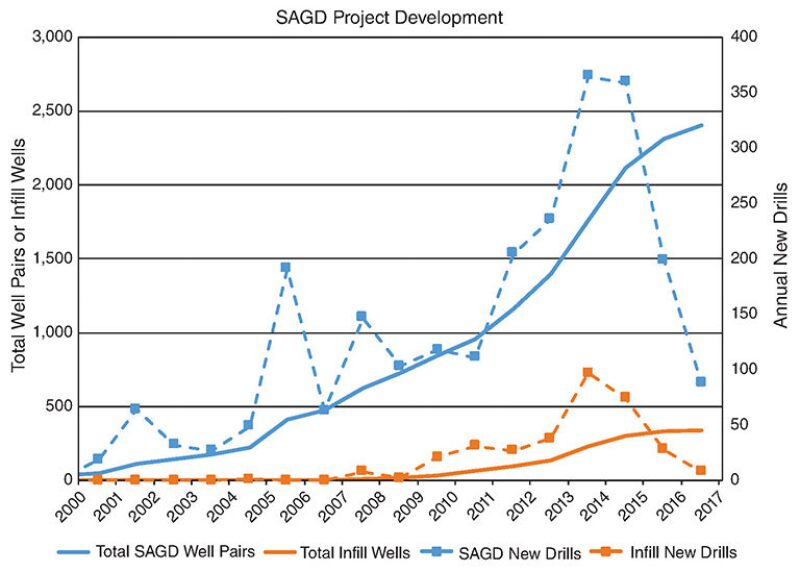
One project—in which Suncor is collaborating with three other companies and a provincial research group—is known by an acronym (ESEIEH) that is pronounced “easy,” representing the term “enhanced solvent extraction incorporating electromagnetic heating” process. It could eliminate steam production equipment on the surface altogether by deploying an underground device using electromagnetic energy to heat the rock, and solvent to mobilize the oil at about half the normal temperature.
While Imperial Oil has commercial wells using its solvent-assisted SAGD (SA SAGD) process, widespread use is far off. Most big companies have done pilot projects on solvent, but cooperative efforts in that area, or in other production-related technologies, have been rare.
However, with pressure to speed technology advances in the oil sands, there are signs of companies moving toward cooperative efforts. “We have to do it differently. Collaboration is one of those differences,” Bunio said.
Recently, an industry group created to share knowledge about ways to reduce the environmental impact of the oil sands, Canada’s Oil Sands Innovation Alliance (COSIA), eliminated a rule limiting its collaboration to projects in the area of health, safety, and the environment, allowing it to try to form projects that affect production.
“COSIA is an unprecedented collaboration in the oil and gas industry. For an industry that is very close to the chest, it is astounding we are doing it,” Kruger said.
The next step is getting member companies to agree to join groups working on specific issues. It is not an easy change, but there is no attractive alternative.
“We are not competing with each other, we are competing with light tight oil from the US and crude from Saudi Arabia,” said Bryan Helfenbaum, the technology development manager for Devon Canada who works with COSIA. He noted that sharing is rewarded. “Collaboration ... is not a zero sum game; both sides have something afterward.”
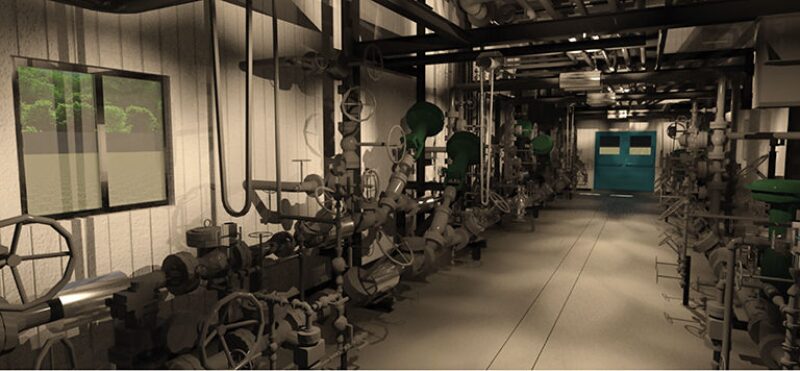
The Pad
Early signs of change in the oil sands can be found on the well pads. For example, Suncor’s new Lean Pad design targets unneeded parts that add cost, complexity, and the time required to install it all. The number of premade modules per pad is reduced from 3 to 1, and number of manual valves slashed from 230 per well pair to 30.
This pad is smaller, so fewer trees need to be cut for it, and can be installed in half the time.
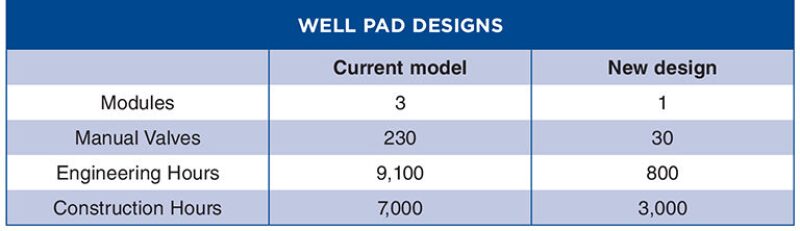
“We did this by taking apart every single system in the pad and asking, what do we need?” Bunio said. Those doing the job asked users: “What risk was it intended to reduce and is it still needed?”
While oil sands drilling has slowed as big projects wind down, pad development will need to continue to sustain production as older wells play out and wells are drilled to tap missed zones. Several companies are now selling standardized modular designs that promise lower and more predictable costs, as well as shorter development times.
An example of that is Hive Innovations, which describes what it sells as a “templated well pad offering.” Trevor Phenix, the business development vice president for the venture, describes it as a turnkey design, fabrication, and construction service. Standardized design is expected to limit the risk of overruns. Also, Hive assumes some of the cost risk that is normally borne solely by the operator.
Pad costs cover a wide range, and Phenix emphasizes that cost alone is not a good measure of value because the cheapest option may limit adjustments that could add production over the 6–12-year life of the well.
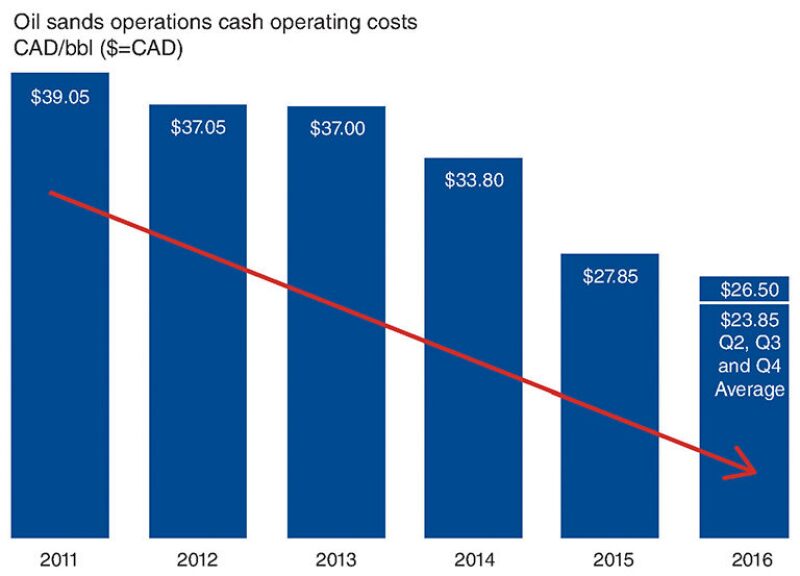
Operators are also pushing pad productivity by drilling longer horizontal wells, with laterals extending from 800 m to 1200 m, and some have gone to 1600 m, said Phenix, who also is president of Top Analysis, which developed software that mines the province’s oilfield database.
Longer laterals save money by reducing the number of wells needed to cover an area, but only make sense if the injection well is engineered to deliver the required heat and pressure over that longer distance. “You cannot extend the wellbore length and just hope it will produce,” Saeedi said.
Longer laterals add to the arguments for another technology trend—using inflow control devices. These nozzles vary the steam injections along the wellbore to ensure relatively even flow, he said.
Steam production equipment is another area where money can be saved by reducing waste. Suncor’s central processing facility design uses a heat exchanger with 50% less surface area and the facility has 20% fewer pumps than the standard.
Suncor’s technology development program is working on a next-generation device that creates both a high-pressure stream of steam and also flue gas that adds pressure and carbon dioxide into the reservoir. It is called a direct-contact steam generator because a hot stream of combusting gas comes into contact with a stream of water, creating both steam and gas.
Direct-contact generation has been an area of research for COSIA led by Suncor, which continues to work on it. One benefit is that it can use low-quality water—aiding recycling. Also, reservoir simulations by Suncor indicate that much of the injected carbon dioxide will remain in the formation.
Bunio said these smaller units can be used to boost pressure in older wells. And early tests suggest that adding flue gas may enhance production. “We see a bulk benefit in maintaining pressure and, at least in the pilot we ran, we do see a reduction in the steam/oil ratio,” Bunio said. The results showed “some change in performance” but he is not sure if that would be sustainable.
The Well
If oil sand producers could have one technology wish granted, it would likely be for solvent-assisted recovery dreams to come true.
Solvent-enhanced production has been shown to speed production and potentially increase ultimate recovery. The payoff might grow if it is possible to use only solvent, which would eliminate water treatment, since the solvent can do double duty as the diluent reducing the viscosity of oil, allowing it to be pumped through a pipeline. Suncor has tested a downhole electrical device for heating the reservoir to the lower temperature required for using just solvent, which would require only a power supply near the wellhead.
While the dream has been around for more than a decade, it is not coming true any time soon.
Given the amount of pilot testing needed, commercial use in 5 years “is probably a stretch,” Bunio said, adding that “10 years is not a stretch.”
The strongest evidence that SA SAGD is for real is Imperial’s move last year to change the status of wells from a pilot project to commercial at its Cold Lake operation. The application for the change said, “Imperial has demonstrated that SA-SAGD results in an increase in bitumen rates and improvement in the oil/steam ratio relative to the standard SAGD process.”
Imperial also applied in 2015 to use its method on a commercial basis in its Aspen project, which it said “could achieve a 25% reduction in greenhouse gas intensity and unit operating costs.” On its website, the company said that if it receives regulatory approval, it could make a final investment decision this year.
Using heated solvents to extract the oil from the sand is a tricky engineering challenge. Saeedi said that Imperial’s results showed the importance of choosing a solvent whose properties are matched to a specific reservoir. The effectiveness of the solvent depends on its phase-change behavior, which will vary depending on the temperature and pressure in the reservoir. “This will be particularly important at shallower deposits with low reservoir pressure,” said Saeedi.
Just measuring whether solvents add or speed production is difficult. A paper (SPE 185014) presented at the recent SPE Canada Heavy Oil Technical Conference by Orlando Castellanos Diaz, a research scientist for Shell Canada, said that a number of solvent pilots “reported inconclusive results mainly due to insufficient sampling.”
The paper said testing samples of the produced fluids is required to verify the numbers from an inline meter, which in this case began delivering bad data after 9 months. The hot, complex mix of fluids also damaged the sample collection system, which was redesigned to handle the mix.
Other barriers to solvent progress include reduced research spending, loss of experienced talent, and the slowdown in drilling, which reduces the number of test opportunities. An operator that has shelved growth plans in the oil sands has little incentive to spend on improving production technology.
Even operators that want to add wells are finding that it is slow going due to regulatory changes. Kruger said getting regulatory approval to add 12 wells in a field with 5,000 operating wells can take 6–9 months in Alberta, but only a couple of weeks in west Texas.
The topic of government regulation came up again and again at the SPE conferences, where the speakers mentioned US initiatives to slash government rules, driven by President Donald Trump.
“If we want to stay relevant to that 800-pound gorilla to the south of us that is overhauling its regulatory processes, we need to get after it,” Kruger said.
Continued Reading: Times are so Tough in the Oil Sands, Companies May Have to Collaborate