Geothermal energy has been described as an engineering problem that, when solved, provides the clean, reliable, safe, and affordable energy being sought globally.
It is highly likely that the engineers who play the biggest role in solving that problem, and the technologies they adapt and advance, will come from oil and gas. There is enough energy in the earth’s crust, just a few miles down, to power all of humanity for ages, according to the US Advanced Research Projects Agency-Energy. The problem is how to tap into it safely, efficiently, and cost effectively.
After many years of failure to launch because of technology or cost limitations, new companies and technologies—and smarter ways of leveraging those that already exist—are bringing geothermal out of its doldrums, to the point that it may finally be ready to scale and become a major player in the transition to cleaner energy, according to Jamie Beard, executive director of the Geothermal Entrepreneurship Organization (GEO) at The University of Texas at Austin (UT-Austin).
“The cutting-edge technological developments in geothermal are devoted to drilling into ever-deeper, hotter, and harder rock,” she said, “and oil and gas holds the key to cost reduction for all of these concepts.”
Eric Van Oort, drilling and well engineering expert, educator, and scientist, agrees. The UT-Austin engineering professor and director of the rig automation and performance improvement in drilling (RAPID) industry consortium, said, “Fifty to seventy-five percent of the cost of geothermal development is tied up in drilling and well construction. To scale it, we have to reduce that cost.”
Designing for Extremes
Well design for geothermal wells is similar to that for oil and gas wells. The challenges arise from drilling deeper and deeper, into hotter and hotter rock. Heat ranging from 150°C (302°F) to 373°C (703°F) and above can be used to profitably generate electricity. Oil and gas well designs traditionally have not had to contend with these extremes.
Thermal considerations are unavoidable in deep geothermal well construction.
Temperature and thermal effects, chemical composition of produced fluids, and rate of production or pressure depletion pose significant challenges to well casing and design.
Nick Cameron, reservoir characterization manager at BP and leader of the supermajor’s studies into geothermal energy, said his company is using corporate data, geological understanding, and oil and gas expertise and experience to look at where their technology can reduce risk and drive down the cost of development.
“Metallurgical understanding of materials and how they handle heat is crucial to these efforts,” he said. “Fortunately, there have been significant advancements in this area in recent years.” Cameron said that much work is also being done into changing the chemical composition of the fluids that flow through the geothermal reservoirs.
Numerous oil and gas service companies are contributing to game-changing capability and cost improvements in deep (especially horizontal) well construction, logging, and materials that enable completions in ultrahigh-temperature regions; high-temperature cement and well casing that increase long-term well integrity; research and modeling of thermodynamic properties of closed-loop systems that show long-term resource life and viability; and efficiency testing of different closed-loop well architectures across a broad spectrum of geophysical conditions using different working fluids, such as water and supercritical CO2 (sCO2)—that is, above the temperature at which it is neither gas nor liquid, but has properties of both.
Baker Hughes, for one, has developed, tested, and field-deployed a 300°C directional drilling system comprising drill bits, positive-displacement motors, and drilling fluids all capable of operating at up to that temperature. The system was used in the Iceland Deep Drilling Project geothermal research well RN-15/IDDP-2 at Reykjanes, Iceland.
The well reached its target of supercritical conditions at a depth of 4.6 km in January 2017. After only 5 days of heating, the measured bottomhole temperature (BHT) was 426°C, and the fluid pressure was 4,931 psi. The drilling system is the subject of an SPE paper (IADC/SPE 189677), as is a 300°C-capable measurement-while-drilling platform that has been tested in the lab.
Bringing Up the Heat
Just as with oil and gas, tapping geothermal means not just digging into it, but also getting it to surface. Currently, there are three broad approaches to globally scalable hot-dry-rock geothermal energy—enhanced geothermal systems (EGS); advanced geothermal systems, also termed closed-loop geothermal (CLG); and hybrid systems with elements of both. Because most companies pursuing these projects are highly competitive startups that don’t share their information, technical details are sparse and public numbers on cost are not available.
CLG is considered more expensive than EGS currently, with the possible exception of a pipe-in-pipe CLG model paired with CO2 as the circulation fluid. Within CLG, concepts that require two wells and long laterals are by far the most expensive.
However, proponents argue that while upfront capital expense for these systems is more expensive than for EGS, lower long-term operating expense more than offsets higher startup costs, and environmental permits are significantly less expensive and time-consuming to obtain.
Enhanced geothermal systems (EGS). In an EGS well, the objective is to increase permeability at depth in hot, dry rock by creating an engineered, artificial version of a conventional hydrothermal reservoir. An injection well is drilled, through which water is injected at sufficient pressure to cause pre-existing fractures to re-open and create a fracture network. Once there is sufficient fractured volume to create a reservoir, a second production well is drilled into the fracture network, intersecting the created flow paths.
The resulting circulation loop allows water to flow through the enhanced reservoir, picking up in-situ heat. The heated water is then pumped to surface through the production well. Energy is produced from the resulting steam on the surface.
Despite significant government-sponsored research beginning in the 1970s, EGS has thus far been largely unsuccessful in establishing and maintaining hot-rock fracture pathways and avoiding cool-water breakthrough.
Critics of the approach point to these issues. But its proponents cite more recent advancements in hydraulic fracturing and the larger area of contact between the wellbore and the hard rock and fluid—which they say improves the rate at which heat can be extracted, and thus, well economics.
According to the US Department of Energy (DOE), while advanced EGS technologies are young and still under development, the approach has been realized successfully on a pilot scale in Europe, and the DOE is now funding demonstration projects in the US.
The DOE-funded Frontier Observatory for Research in Geothermal Energy (FORGE) is an international field laboratory located in Utah for technology development and public education on geothermal energy in general and EGS development in particular. The facility is managed by a multidisciplinary team of engineers and scientists led by the University of Utah.
Among the most vocal cheerleaders for EGS is Mukul Sharma, professor and W.A. Moncrief Jr. Centennial Endowed Chair in Petroleum Engineering at UT-Austin, a member of the US National Academy of Engineering, and founder of Geothermix Energy. Sharma, who has been a key player in the development of hydraulic fracturing, compares the current position of geothermal, and particularly EGS, to that of unconventional oil and gas in its nascent phase.
“By translating the engineering advancements that increased well productivity by a factor of four to 10 in many shale basins, I have no doubt that we will be able to successfully deploy these methods in EGS,” he said. “Today we’re drilling wells with one to three fractures; we are going for 200–300. But, even if only one in 10 connect—and we know how to do that—we can increase the contact, heat exchange rate, and economics by the same order of magnitude.”
Tim Latimer and Jack Norbeck, co-founders of Fervo Energy, believe they can improve EGS performance by using horizontal drilling techniques and distributed fiber-optic sensing to isolate multiple zones inside a well and optimize flow rates within each. The California-based startup was one of the first seven companies—and the first geothermal entity—to receive funding from Bill Gates’ $1-billion Breakthrough Energy Ventures fund.
Advanced geothermal/closed-loop geothermal systems (CLG). CLG systems follow an approach very different from that of EGS. No fluids are introduced to, or extracted from, the earth, and there is no fracturing. Instead, CLG wells overcome permeability and flow issues by circulating fluid through a downhole heat exchanger or sealed wells and pipes, picking up heat by conduction and carrying it to the surface, where it can be used for a mix of direct heat and electricity.
Like EGS, CLG systems have been around for quite some time without achieving commercialization. Also like EGS, new startups are adapting technologies from oil and gas to jump-start scaling of the approach.
Closed-loop systems can operate in a broad range of temperatures and rock compositions. This wide range not only increases the number of potential viable geothermal projects, but also allows the use of high-temperature resources (≥300°C) that dramatically increase power output.
Different concentric pipe-in-pipe and multilateral, sealed, U-loop configurations can be used to optimize site-specific costs and performance.
Closed loops make it possible to use not only water, but also alternative heat-transport fluids such as sCO2, that create a strong thermosiphon effect that can eliminate the need for an external pump.
Compact turbomachinery is scalable with sCO2, reducing capital costs. Finally, CLG energy systems can produce power from previously unproductive geothermal wells and from played-out oil and gas wells in hot strata.
Eavor Technologies and GreenFire Energy are current leaders in the development and application of CLG technology. Both have had successful initial demonstration projects. GreenFire successfully completed a field-scale demonstration of its GreenLoop technology in 2019, using an inactive well at the Coso geothermal field in Coso, California. It has ongoing commercial projects in the Philippines and California.
Eavor has been operating a $10-million pilot/demonstration project called Eavor-Lite in Alberta, Canada, since 2019. It is partnering with Enex Power Germany and others to develop new Eavor-Loop heat and power projects within Enex’s existing geothermal license area at Geretsried, in Bavaria. Construction on the initial phase of the project is expected to begin in Q3 2021.
GreenFire’s modeling and analytics capabilities make GreenLoop adaptable to a wide variety of underutilized geothermal resources at competitive prices, according to the company.
It says its high-well-density architecture optimizes power output and makes it possible to drill multiple wells from the same location, substantially reducing the cost per well and permitting economies of scale in site development, power purchase agreements, and transmission lines.
Following Eavor-Lite, Eavor has modified the geometry of its original “daisy-chain” design in its new “James Joyce” design (named for the pub where the concept was hatched, not the Irish author), which it will use in the Geretsried project (Fig. 1). By locating the two vertical wells next to one another, the design is expected to reduce physical surface footprint and enable more precise drilling.
The wells will use magnetic ranging to remain at a fixed distance from one another. Lateral wells will branch out from each vertical, staying parallel until they meet at the toe end, which Eavor says is easier than meeting in the middle. The company has also been field testing a new drilling technology designed to extend Eavor-Loop into harder, hotter rock. Eavor-Long has been tested throughout 2020 at the XRig facility in Stavanger, Norway, and is scheduled for deep field trial in the US and Canada in 2021.
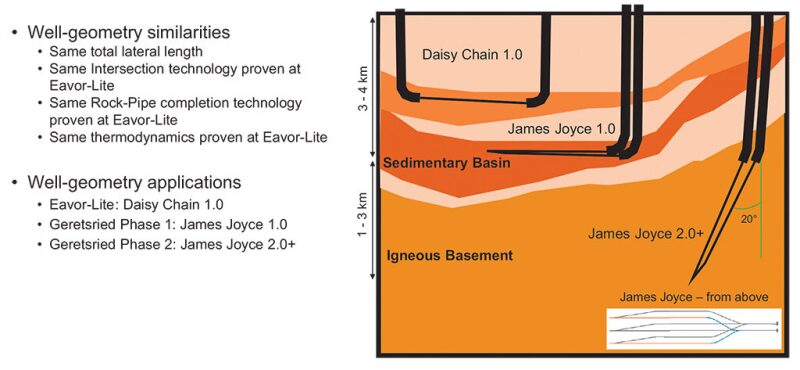
EGS/CLG Hybrid. Sage Geosystems’ approach to geothermal development combines open-to-reservoir EGS and closed-loop CLG. The Sage approach begins with drilling a well to approximately 4 to 6 km total depth.
It then uses its HeatRoot technology to propagate fractures downward, reaching at least several hundred more feet in depth and with it, much higher temperatures than the BHT of their well. The fractures are filled with a highly conductive slurry that is also convective. Then a pipe-in-pipe closed-loop heat exchange system with a supercritical circulation fluid is placed in contact with the HeatRoot network.
“Think of this system like tree roots reaching downward from the well that suck up heat from the depths and deliver it to the wellbore,” said Lev Ring, founder and CEO of Sage.
“You’ve got heat resources that would have required a well twice as deep to access, by growing some roots to feed your heat exchanger,” added Lance Cook, Sage’s president.
Blind Geothermal Picks Up Steam
At the end of December, Canada-based Deep Earth Energy Production (DEEP) announced what is being called a historic milestone with a positive well test from its Border-5HZ well, the deepest horizontal well ever drilled in Saskatchewan and the world’s first 90° horizontal fluid-production well to be drilled and hydraulically fractured for a geothermal power-generation application.
The DEEP project is essentially a directionally drilled “blind hydrothermal” resource, which puts it in the same category as conventional hydrothermal resources such as those in Iceland and other isolated areas. The resource is a hot sedimentary aquifer, meaning that there is existing water in the formation.
This type of resource is more limited than the hot and dry sedimentary rock that is fairly ubiquitous globally and, therefore, the focus of EGS, CLG, and other potentially scalable geothermal development at this point. “Blind” in this case means that there are no visible surface manifestations—such as geysers, hot springs, or fumaroles—of the heat and water underground.
How much more limited blind hydrothermal resources are than their deep, hot-rock counterparts is a pending question, and one that may attract more attention following the successful DEEP well test.
According to industry sources, there are at least three major operators looking right now at where blind hydrothermal resources may be located throughout the world.
DEEP is producing the high-temperature water in the Border-5HZ well using an electrical submersible pump and said the well was completed using a sliding-sleeve system. The company also noted that the hydraulic fracturing operation was carried out using “standard horizontal-well completion procedures.”
Drilling Ahead
“What is needed to scale geothermal to the point where it can fulfill its potential as a global energy source is specific innovation and expertise in drilling technologies—the very expertise and skills many in oil and gas already have,” Beard said.
“ I view the oil and gas industry as the most capable and resourced asset we have on the planet to solve climate change, and with geothermal they can accomplish that end by leveraging what they already know and do,” she continued. “It is oil and gas that will enable ‘geothermal anywhere.’ Across the entities within the industry I’ve engaged with, regardless of their particular current focus, there is clear agreement that the oil and gas industry can make huge and globally relevant things happen in geothermal, fast.”
Van Oort agrees. “Geothermal drillers are very knowledgeable, but they have not yet capitalized on oil and gas developments over the past 10 to 20 years,” he said. “But neither does oil and gas need to come up with absolutely new technologies for geothermal,” he continued. “We can push current technologies and apply them to geothermal to make a step change in drilling efficiency and cost reduction.
“Yes, we have some problems to overcome,” he added. “In the meantime, we have the opportunity to do significantly more with what we have by applying what we learn from data to optimize its efficiency. That’s where oil and gas expertise can really help improve things for geothermal.”
For Further Reading
IADC/SPE 189677 A 300-Degree Celsius Directional Drilling System by A. Stefánsson, R. Duerholt, J. Schroder et al. Baker Hughes.
Closed-Loop Geothermal Demonstration Project: Confirming Models for Large-Scale, Closed-Loop Geothermal Projects in California. California Energy Commission Consultant Report, June 2020.