Want more production from a shale well? Consider lining up the perforations.
A handful of speakers at the recent SPE Hydraulic Fracturing Technology Conference talked about improved fracturing results with oriented perforating—shooting the holes at the same place in the casing, often the top.
This breaks from designs that arranged the holes in a helical pattern with each charge angled 60° from the previous one.
“We did see indications we are getting better production from oriented perforating,” said Blake Horton, senior completions engineer for Ovintiv (SPE 204177).
Production gains were also reported by ConocoPhillips which compared production from similar wells with and without oriented perforating. The analysis was designed to filter out differences in the geology, drilling, and completions.
It concluded the value of the added production far exceeded the $20,000-per-well cost of installing the assembly, including a weight bar to tilt the perforating guns into position.
“That’s less than the undiscounted value of 400 barrels of oil. An internal study indicated that ConocoPhillips improved estimated ultimate recovery (EUR) by a minimum of 5% when using high-side-oriented perforating,” said Dave Cramer, senior engineering fellow at ConocoPhillips and an early advocate for the method.
“For an initial choked flow rate of 1,000 B/D, the payout on investment is 10 days or less,” he said.
Ovintiv declined to provide a number, but Horton said ConocoPhillips’ estimate is within Ovintiv’s range based on similar comparisons of wells with and without oriented perforating.
That number is at the low end of the estimates offered in discussions about oriented perforating performance at the conference. Higher estimates are questioned by those who doubt the test results can be sustained when the method is scaled up. What was certain is the number of users is rising and includes names such as Shell and Chevron.
“We found that oriented perforating definitely helps to treat all the clusters,” said Jon Snyder, a staff completion engineer for ConocoPhillips who presented the paper, adding, “by oriented perforating we mean that when we are perforating, we aim for the high side of the wellbore” (SPE 204203).
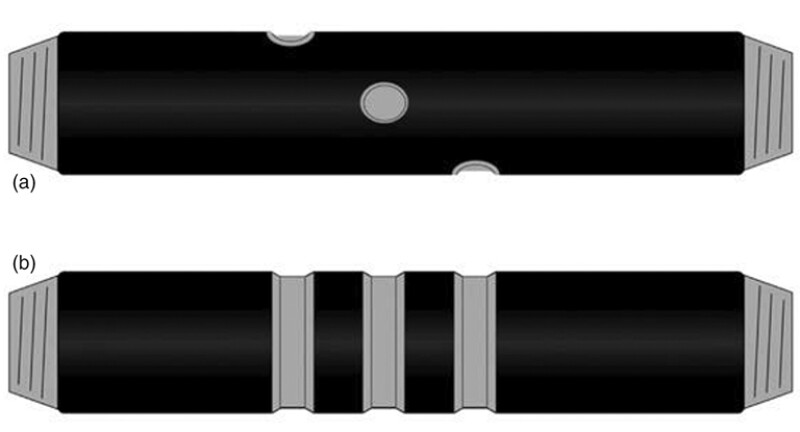
When Horton polled the audience at a recent talk, more than half of the respondents said they were using gun systems designed to orient the perforating charges at a target angle.
“A year from now, few people will not be doing oriented perforating; the advantages of it are clear,” Cramer said. He has been promoting the idea within the company for years with mixed acceptance.
The argument for orienting is simple. The shots are far more likely to be the same size if they are all shot at the same target because they are all traveling the same distance.
Equal hole size matters because that helps ensure that enough fluid and proppant are distributed more evenly among the perforations to make certain they are effectively stimulated.
Size differences of just a few hundredths of an inch can mean one hole takes in far more fluid and proppant, leading to fractures that grow excessively, which can deprive other perforations of the volume they need for fracture growth.
The impact as measured by the perforation friction—a determinant of the flow capacity—is much larger than the area added as the hole diameter increases. “Any change in diameter is huge for the equation” because that value is carried to the fourth power, Horton said.
ConocoPhillips described how it reduced the cost of perforation by eliminating the gun components used to vary the shot direction, resulting in perforation guns that it said were simpler and more reliable. The number of perforations in these wells is also limited to provide enough pressure to ensure each is stimulated.
When the perforations were oriented, Ovintiv was able to reduce the treatment pressure by 550 psi and the time it took to get to the planned treatment pressure level by 5 minutes, which “will save us a lot of money,” Horton said.
“With such a low cost and potential increase in production, it is an easy choice for us,” he said.
Same Every Time
The thinking that led to oriented perforating began with the question: Why are the sizes of holes shot using equal-sized charges significantly different from those promised by the makers of shaped charges based on their testing?
The answer was that in a well, where the shots are spread around the casing, the sizes will vary due to differences in the distance between the gun and the target in a fluid-filled pipe. Slight differences in the diameter when perforating through one-third of an inch of quality steel matters a lot to those users.
These issues became apparent when companies like EV and DarkVision began imaging and measuring perforations before and after fracturing. Those pictures consistently showed the size varied based on the wall location, with small differences growing large as flows of fracturing fluid have an outsized impact on the size of the holes that start out with larger diameters.
For example, when ConocoPhillips measured the perforations shot at a variety of angles around the casing, the hole diameters varied from 0.38 to 0.43 in., with the most common diameter representing about 35% of the shots.
Those differences shrank when oriented perforations were compared. The operator found that 80% of the holes shot in the top of the casing were 0.38 in. diameter, and the other 20% were within 0.01 in. of that.
ConocoPhillips reported that the larger hole-size variations in stages perforated at multiple angles were five times more likely to have “runaway perforations that eroded so much they took the lion’s share of stimulation,” Snyder said.
“One of the worst things about nonoriented perforating is runaway perforations,” Cramer said. While the long fractures that result can be productive early on, “they can cause havoc as you develop the field.”
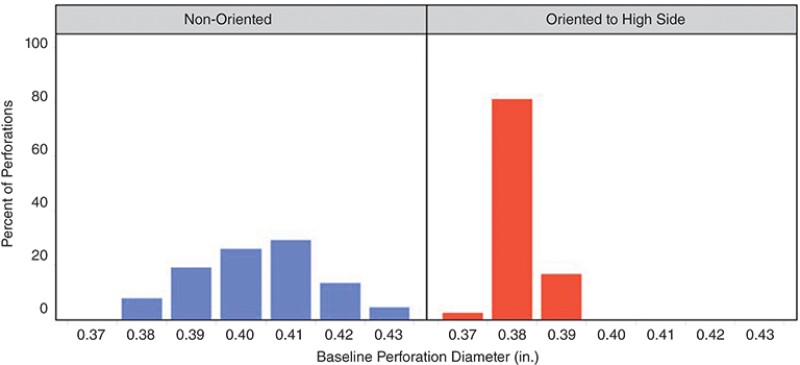
Not Just Oriented
Just orienting the perforations is not enough to ensure more production.
Ovintiv and ConocoPhillips were paying attention to other details that assured the pressure pumping delivered the treatment volume and pressure needed to effectively stimulate most of the perforations.
In other words, oriented fracturing improved the performance of limited-entry designs.
They limit the number of perforations in a stage and the size of those holes to ensure each one can create a productive fracture. The challenge is complicated by the fact that some hole locations are more likely to take in fluid and proppant than others.
Limited-entry designs broke from fracturing designs that offered as many paths out of the casing as possible in hopes of maximizing the number of fractures created.
The thinking changed based on years of papers and experience showing that fracture performance varied widely. A few dominant fractures got the largest share of the treatment.
Often this was due to heel-side bias where a large part of the treatment goes into the first or second perforation passed as the fluid flows down the hole. That can create runaway fractures that get the largest share of the treatment while others get little.
Limited-entry users say the technique significantly increases the percentage of treated clusters. Not every perforation can get the same stimulation, but Snyder said “limited entry is our best option for treating all the clusters.”
An easy way to detect if an engineer believes in limited entry is to ask them about the alternative.
Horton’s answer was: “They are blowing up everything. They shoot a ton of holes … there is stuff all over the place, it is terrible distribution.”
Limited entry is evolving as users gain a better understanding of the variables and which of them matter most based on research and field data. That data is often not disclosed, forcing others to learn the same lessons.
At this point, the definition of oriented varies depending on whom is asked. The most common is that all the perforations are aimed at a single angle.
But Ovintiv orients perforations along a horizontal plane at the middle of the side wall. The thinking is that starting sideways reduces the pressure and time needed to develop a productive fracture in the STACK formation in Oklahoma, where the maximum horizontal stress exceeds the vertical, overburden stress.
Horton talked to Cramer, who sees two-sided fracturing as an unnecessary complication compared to simply focusing on a single target.
Work at ConocoPhillips has shown that fractures will grow around the casing until they find the path of least resistance to grow outward. Cramer suggested testing a shot straight up because he expects the result would be similar to the sideways perforations.
While all these discussions keep coming back to hole sizes, a paper from the fracturing conference offered another rationale for orienting along a single angle.
Xinghui Liu, a senior well stimulation advisor for Chevron Corp., compared different shot patterns using computational fluid dynamics modeling. Based on the calibration of laboratory results with field data, he concluded the force of the outflow at one perforation tends to herd the proppant that is moving to the next perforation (SPE 204182).
Liu explained that the “attractive force” of the outflow concentrates the slurry near that part of the casing, increasing the amount flowing out of later perforations.
Hitting the Target
Companies making the case for the value of oriented perforating are working to find a low-cost way to accurately hit their targets.
Ovintiv and ConocoPhillips both relied on a simple approach to raise the guns to the target angle—using a counterweight in the form of an eccentric weight bar to hold them in place.
Based on their experience, it works even if it misses the bull’s-eye by a fair margin.
Horton shared a chart with an array of dots showing the actual angle of each shot clustered around a red line representing the target. Most were within 60° of the red line.
There are more-precise methods than adding weights, such as a sealed device that rotates on bearings for more-accurate aim. But Horton said that one-time use devices cost up to $30,000 per well while the long-lasting steel bars used as eccentric weight bars are “basically free.”
And it appears there is an acceptable margin of error for oriented perforation, though there is no accepted range limit.
Cramer said he has met with service companies that have promising ideas for filling this need.
While ConocoPhillips’ oriented perforating designs call for perforations at 12 o’clock, the paper reported holes observed in wells tend to be around 10 o’clock. The authors said that may be the product of pent-up torque in the wireline.

ConocoPhillips has modified components in the gun assembly to improve its aim, changes which it may patent, Cramer said.
Snyder also said shooting at a consistent angle is more significant than the angle chosen.
Changing the exit point is not likely to change the path of the fracture created. Cramer said that geomechanical calculations using data from lab and field research indicated the hoop stress created by drilling a hole leads to a fracture growing along the wellbore until it “encounters a region of reduced stress that allows it to move out transversely.”
There is one perforation angle that is out of favor: shooting straight downward.
Effective treatment is not the problem. Since the perforation gun is normally sitting at the bottom of the casing, that is the shortest shot. It results in a larger hole, which will take in more fluid and proppant and lead to greater growth. The force of gravity can result in a higher concentration of proppant in the bottom part of the well, accelerating the erosion.
There are other downsides to shooting downward. In the short run, sand accumulates in the lower parts of the well, making it hard to image perforations, though that is not often done. In the long run, sand buildup could cover the perforations, possibly affecting production.
Those issues are minor compared to the negatives associated with shooting at both the top and bottom.
Ovintiv reported that perforating both the top and the bottom—the smallest hole was at 0° and the biggest at 180°—resulted in 550 psi more pressure due to the differences in hole sizes. The larger holes received more fluid, which resulted in in inconsistent slurry distribution and increased the effort needed to stimulate both.
When Cramer critiqued the paper, he asked Horton why it compared sideways fracturing to a pairing where the wide size differences are known to cause the sort of problem that led to oriented fracturing.
“We tested what we thought was the best with what we thought was the worst. The result was as we expected,” Horton said, adding, “We did it because many people are still shooting at the 0° to 180° orientation.”
For Further Reading
SPE 204203 Improved Treatment Distribution Through Oriented Perforating by J. Snyder, D. Cramer, and M. White, ConocoPhillips.
SPE 204177 A Shot in the Dark: How Your Post-Fracture Perforation Imaging Can Be Misleading and How To Better Understand Cluster Efficiency and Optimize Limited-Entry Perforating by B. Horton, Ovintiv.
SPE 204182 Achieving Perfect Fluid and Proppant Placement in Multistage Fractured Horizontal Wells: A CFD Modeling Approach by X. Liu, J. Wang, and A Singh, Chevron et al.