Recently, at the SPE Annual Technical Conference and Exhibition, I was asked a question about the ‘engineer of the future.’ As we take a pause to turn the page to next year, I believe now is a prescient time to contemplate what’s next for petroleum engineering.
Throughout my career, I’ve been able to witness great change in our industry as the shale revolution took hold making horizontal drilling and hydraulic fracturing commonplace, diagnostic and modeling tools improved in access and cost, and data became more timely and readily available. This led to a tremendous period of US energy supply growth and decades-long productivity improvements.
Looking forward, I believe there are three trends that engineers should consider: 1) applying “new” tools to solve “old” problems, 2) connecting the dots via hybrid engineering, and 3) organizing, directing, and inserting data predictions into their workflow. These are not only my views but also the views of Devon’s talented engineers.
Old problems will meet new solutions. The past decade has been dominated by unconventional horizontal development that was first pioneered in the Barnett Shale for natural gas and shortly thereafter transitioned into oil-focused development in the Bakken and Eagle Ford. Today, the Permian Basin continues to grow in total supply as the stacked pay is developed.
Engineers should take stock of the tool set we have acquired during this era with a mindset to deploy these methodologies to tier II unconventional extensions, previously developed or bypassed conventional formations, offshore and international opportunities, enhanced recovery projects such as EOR and refracturing, and new energy opportunities like geothermal. To make these future opportunities competitive and meet the global demand for energy, we will likely need a combination of price, technology, and cost improvements.
Engineers are critical to the latter two. To better illustrate these points let’s utilize examples. Drilling rig specification improvements have been coupled with material science and design improvements in bottomhole assemblies. The outcome is improved topdrives and mud pressure systems to power more durable and efficient downhole motors and bits, thus reducing failures, enhancing the efficiency of a rig’s daily footage, and enabling longer laterals. If we pivot to the completion space, our diagnostics for frac geometry have gone from limited and costly to a menu of options that provide fit-for-purpose diagnostics and costs.
Devon deployed its first permanent fiber diagnostics in unconventional shale in 2012. Today, the same system is readily available but for a much lower cost. However, more frequently Devon has supplemented this tool with dip-in fiber and a proprietary methodology called sealed wellbore pressure monitoring to gather more frequent data points for frac geometry and design. As our team conducted, in cooperation with the US Department of Energy (DOE), a novel Eagle Ford project capturing horizontal core and completion diagnostics, we recognized that our designs have tremendously improved in efficiency but still have potential to capture more of the resource via initial and secondary fracturing efforts.
If we consider the production space, a tool that has been within our systems for years is SCADA. This system historically was a controls system. During the past 2 decades it has provided the first step in a system streaming data, coupled with evermore sensors and visual cameras, to enable our local decision support center in each asset. These centers now serve as the brains of our field operations, remotely monitoring, dispatching repairs, and optimizing wells daily. These efforts have led to the upskilling of our field staff and increased our efficiencies on a well count per team member basis.
These are just a few examples as to how we, at Devon, have transformed during the shale era and this mindset should be the foundation for unlocking future industry challenges.
Hybrid engineering melds the skills of different disciplines into an improved solution. As I reflect on my own experience, one of the big changes in the shale era has been the segregation of engineering skills to build deeper capabilities. Engineers might have originally held responsibilities spanning two capabilities, perhaps three, e.g., drilling, completions, facilities, production, reservoir, and planning. The eventual segregation of job scope was beneficial as growing knowledge catalyzed segment improvements which were important as we migrated to more robust development plans.
The future trend for engineers will be the ability to meld disciplines and integrate tools to unlock more resource recovery per unit of cost. To illustrate, consider the following examples.
Subsurface optimization epitomizes the challenges of past and future development decisions. In a single-zone greenfield development, well spacing and completion design interact to achieve an economic outcome. This situation becomes more complicated when you contemplate multiple zones with connected flow units necessitating decisions about vertical spacing, sequencing, and the effects of co-development, or lack thereof, on future development. Finally, layer in the effects of time, as most operations contain a previously developed well that has undergone depletion.
These are the type of challenges that only hybrid engineers can overcome. We must marry our historical experiences and learnings with future challenges across multiple disciplines to yield custom solutions. Predicting well performance has become progressively more difficult as solely relying on offset wells to inform forecasts is the way of the past. An integrated team, however, can distill the most informative variables in a grand multivariate problem to yield better solutions.
If we pivot from the subsurface to the surface, the combination of increasingly complex facilities, addition of emission reduction and monitoring expectations, and the growing need for electricity has had a profound effect on the job scope of a facility engineer. Now our engineers must give forethought to working with power providers, or in some cases, microgrids and local power generation, which require decisions years in advance of production. The inclusion of onsite continuous monitoring sensors for optimization and emissions purposes elevates the coordination to design the equipment. Lastly, the economic efficiencies of connecting multiple units into a single site must be balanced with the design requirements of varying well tie-in timing and peak rates.
As these examples illustrate, a hybrid engineer will have to integrate multiple challenges, both internal and external, to routinely design custom solutions. I expect engineers who can connect the dots will have outsized influence on teams.
Data and a future with AI. Data has been a transformational change during my career. I recall data being gathered by hand and other times via technicians who would input it into spreadsheets. Our historical systems were designed for low-quality and low-volume data. Fortunately, great change has happened as wellsites stream data, from the subsurface and surface, to organized data management systems.
When I asked engineers about the future of the industry, they all mentioned data and AI. To make it actionable I simplify this effect into two skills: data conditioning and predictions.
Data conditioning is the skill of using data science packages to gather and characterize data to feed predictions. Predictions are the output of algorithms from simple multi-what if equations to deep learning honing the algorithm based on dynamic situations and previous prediction outcomes.
The component connecting these two skill sets will be the act of coding. Coding, once reserved as a niche skill set, will be a ubiquitous tool for engineers. That change can sound daunting; however, as Devon’s engineers have demonstrated, the advance in large language models lessens the barrier to coding.
A holistic example is how Devon has made important changes to train and lower the barrier to skill development. We have initiated a data science cohort boot camp for our team members. Within this camp, experts in data engineering, architecture, and science instruct our team members and eventually coach participants to a final business project.
A production engineer recently highlighted his results in a broad forum to reinforce the approach to “learn, do, share.” This specific project captured the task of compression optimization. A necessary task in the present becomes more proactive and efficient with data improvements and AI.
For context, compression optimization is a task that engineers undertake as volumes decline and equipment becomes oversized, incurring unnecessary costs. By connecting data from operations, supply chain, and financial accounting, our team can rapidly scan the field for optimization projects and prioritize. Although this is a simple example, imagine the effects of scale with multiple assets in a decentralized field structure overseeing hundreds of compressor units. The engineer’s purpose didn’t change; the process for the task did though.
Data and AI will change our industry for the better. At the root of this change will be the empowerment of engineers to make better decisions.
In closing, I want to reflect on why I first became an engineer. The intersection of solving problems with brilliant and diverse people and global relevance provided the fuel to become an engineer. Looking forward, given the right tools and support, I’m confident our skills will be needed to provide energy to power the world, the challenges will be as rewarding as ever, and the people will make the journey memorable.
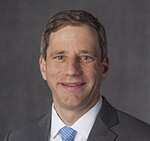
Aaron Ketter holds the position of vice president of the Mid-Continent and South Texas Business Unit for Devon Energy. His multidiscipline teams are responsible for creating and executing the corporate strategy encompassing financial performance, capital program, and business development opportunities. Prior to his current position, he held various roles at Devon including vice president Rockies Business Unit, vice president strategic planning, manager midstream and marketing, acquisition and divestitures, deepwater exploration, and multiple onshore engineering assignments.
Ketter holds an MBA from The University of Chicago Booth School of Business and a BS in petroleum engineering from The University of Oklahoma. He currently serves on boards for the Petroleum Alliance of Oklahoma, Oklahoma City Museum of Art, and Oklahoma City Urban League.