The development of conventional reservoirs has typically involved minimal logging-while-drilling (LWD) technology, usually consisting of survey, gamma ray, and possibly resistivity tools. As production from conventional reservoirs declines, the need to obtain more production from each well increases. With attention shifting toward the development of vast unconventional and source rock reservoirs, achieving and sustaining economic production rates depends on new drilling and evaluation technologies.
More information is needed about the formation target and reservoir in order to understand the challenges of these unconventional plays. When thinking about a well’s production potential, key characteristics must be taken into consideration, such as stress orientation, anisotropy, secondary porosity, natural fractures, and the potential of fracture propagation. New tools and technologies are necessary to determine these formation characteristics in the complicated reservoirs being developed.
One tool that is used to provide information for optimizing stimulation and well placement is the LWD microimager. These tools produce detailed electrical images of the borehole and show natural and induced fractures, faults, formation breakout, vugs, and other fine details of the formation. An accurate depiction of these features from high-resolution borehole images enables improvements in completion design.
When developing an LWD microimager, several factors must be addressed to achieve an optimal image quality. These include the need for
- A conductive wellbore fluid such as water-based drilling mud
- A rotating drillpipe
- Reasonable contrast between the mud resistivity and formation resistivity
- Minimal clearance between measurement electrodes and the wellbore
These parameters are common to all LWD microimaging tools and some counterpart wireline tools, and are acknowledged in the tool specifications. Knowing these key constraints and the desired measurement outcomes, Weatherford developed the high-definition SineWave microimager with two measurement electrode sizes to match the resolution capability of wireline tools and mitigate the negative effects of standoff and eccentricity in the borehole.
Advantages of LWD Microimaging
Although wireline microimaging tools have been available for more than 2 decades, the ongoing push for optimized production and the need to reduce total drilling and evaluation time has spurred a demand for LWD microimagers. While wireline microimagers can provide high-resolution borehole images after drilling, the real-time LWD borehole images can aid in the drilling process itself.
For example, true formation dip and the relative angle between the borehole and formation bedding planes can be interpreted from real-time LWD images as drilling progresses. This knowledge allows the precise geosteering of a well through the target formation. Using the fine details of the images in real time enables petrophysicists and geologists to better define the targets before the well reaches total depth.
LWD imagers have the advantage of obtaining their measurement shortly after the drill bit has penetrated the formation. This provides better wellbore images compared with wireline, because the borehole is in a better condition. Less time will have elapsed for any washout to occur and mudcake to build up, which can adversely affect image quality.
Because LWD data is acquired as the well is drilled, high-resolution images revealing fractures, faults, and stress orientations are available immediately for completion design decisions. Capturing the information while drilling also means that no additional rig time is required for logging, which helps to reduce cost, compared with post-drilling data acquisition and imaging.
The drilling process yields another unique benefit of LWD microimagers: the ability to acquire a 360° borehole image with a single 0.2-in. diameter measurement electrode. Wireline microimagers use more than 100 electrodes on six to eight pads to measure as much of the borehole as possible. Depending on the hole size, wireline microimage logs can have significant data gaps from the areas between the measurement pads, which keeps the logs from providing complete borehole surface images.
On the other hand, the SineWave LWD microimager takes advantage of the rotating drillstring to scan the full borehole wall with each pipe rotation. State-of-the-art, high-speed electronic sensors acquire more than 350 measurements per second in 128 azimuthal sectors around the borehole. The high-speed data acquisition process yields high-resolution images, even under conditions of fast drilling rates, high rotary speeds, and stick-slip drilling dynamics.
Technology Test Procedure
Testing of the LWD microimager downhole tool and electronics was a key and difficult task. Testing the tool’s configurations required knowledge of the formation and mud properties and control for those variables in the procedures.
The test configuration was created by obtaining a limestone block that had been designed at a set resistance and been machined with certain features. The block was cut to represent vugs and fractures of differing widths and depths and then set up in a tank filled with fluids of various resistivities. A tool was lowered into the test setup and allowed to rotate and to move along the block, simulating the drilling environment.
After a thorough in-house testing, a test well was drilled with the SineWave LWD microimager, and a wireline microimager was used afterward to take measurements in the same well. The LWD wellbore images had the same or better resolution compared with the wireline images (Fig. 1 above).
Benefits of Real-Time Data
One of the biggest benefits of using an LWD microimager is the ability to obtain real-time data. This data enables an early petrophysical evaluation and can be used for active geosteering of the drilling process.
The high resolution of the LWD microimaging tool displays fine details of thin bedding planes and fractures. Obtained in real time, the details can also aid in geosteering, especially in an area where the formation dip may be unknown or significant changes are present within a geologic structure. Although other LWD azimuthal gamma ray and azimuthal density imaging tools can identify structural dips and aid in geosteering, their vertical resolution of 6 in. or more may be insufficient to see all the geologic features of some wells.
If drilling in an area of very thin beds or laminations, the distinction between beds may be invisible or the bedding dips may be improperly calculated. The SineWave microimager’s high resolution allows it to identify and distinguish between the thin beds and laminations.
A recent multiwell project showed very thin beds overlying the target formation. Proper identification of the bed dips was a key factor to successful drilling and required a high-resolution image in real time. The SineWave microimager was used as the primary real-time formation evaluation measurement tool. A comprehensive prejob analysis was needed to optimize all parameters for obtaining high-quality real-time images.
The second well in this campaign provided results that exceeded expectations. The microimager accurately displayed formation dips in real time by resolving beds down to 2 in. or less and in some areas showing natural fractures, which are typically less than 1 in. wide (Fig. 2).
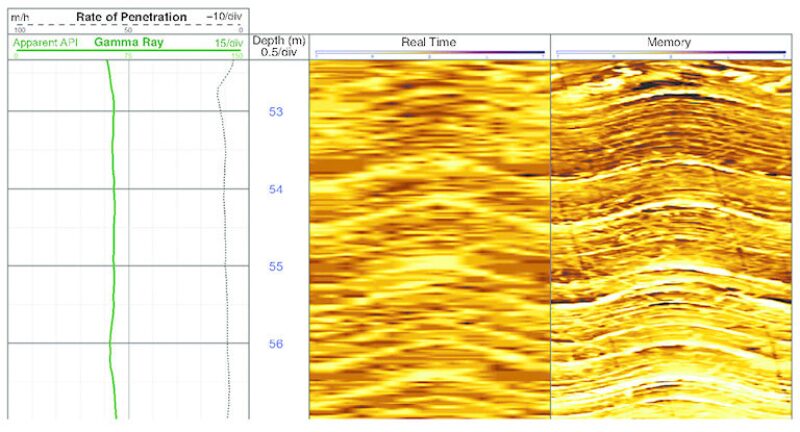
With its data-gathering capability and measurement resolution, the SineWave microimager is well suited for use in the complex reservoirs being increasingly targeted today. Applying it with other LWD tools, such as acoustic, density, porosity, formation pressure, resistivity, and spectral gamma ray sensors, enables a full characterization of the well and reservoir in real time. With a thorough knowledge of the formation, wellbore, and reservoir in real time and recorded, operators can land the well on target, optimize stimulation, and increase production.