The energy industry has been fueled by innovation, from seismic imaging to new well drilling and completion methods to technologies such as digital twins and advanced analytics for subsurface data.
Even with all of these developments, however, far too many wells, particularly offshore, are still delayed or over budget. In order to transform exploration activity and control costs with digital technology, the well-planning process must be improved.
Introducing innovative methods into the pore pressure and fracture gradient (PPFG) well planning work flow offers one way for exploration firms to enhance communication across the value chain and streamline the drilling process.
The Role of PPFG
Companies spend countless hours attempting to predict how to approach the subsurface for optimum well placement in hopes of avoiding costly dry holes. For offshore wells, safety is especially important, as one uncontrollable accident from a well can lead to billions of dollars in technical, environmental, and legal damage.
But in spite of these efforts, nonproductive time (NPT) still costs the energy industry tens of billions of dollars per year.
- A 2004 industry study indicated that geopressure and geomechanical problems were the source of 41% of total NPT recorded offshore. In 2009, an update to the study was shared in OTC 20220 and concluded that, in the Gulf of Mexico, wellbore instability accounted for 31% of NPT for nonsubsalt wells and 41% for subsalt wells.
- A 2019 survey by SPE found that geopressure and geomechanical problems were still the largest contributors to drilling uncertainty, leading to 36% of all NPT.
Communicating PPFG assessments through the value chain may be the key to reducing this uncertainty. This is because assessing the pressure of the fluids within rock formations and understanding the pressure needed for productive fracturing is vital for the design of an efficient and effective drilling approach.
PPFG starts during prospect and play evaluation and helps determine both the planning and selection of the well concept and the plan for execution.
The typical PPFG work flow incorporates data from offset well logs, seismic 2D/3D models, comp logs, drilling reports, and pre-drill prognosis analysis, including maps and stratigraphy.
Stakeholders apply algorithms in an attempt to tie together geological understanding, drilling history, pore pressure and stress, and regional knowledge to provide a low case, high case, and expected case (at minimum) for the presence of hydrocarbons.
For a successful PPFG approach, geologists, geophysicists, petrophysicists, and drilling engineers, who all contribute their own data inputs, must collaborate. And, on average, around four software programs are utilized in a single PPFG work flow, with Microsoft Excel still being the most frequent technology employed.
As files travel back and forth among participants, updates are slow to move through the entire work flow. The delays then begin to mount. In addition, each individual team looks at the data in its own way, for its own distinct answers, creating further inefficiencies.
The result is a fog. Areas of improvement become difficult to clearly identify. Some changes consume too much time to implement.
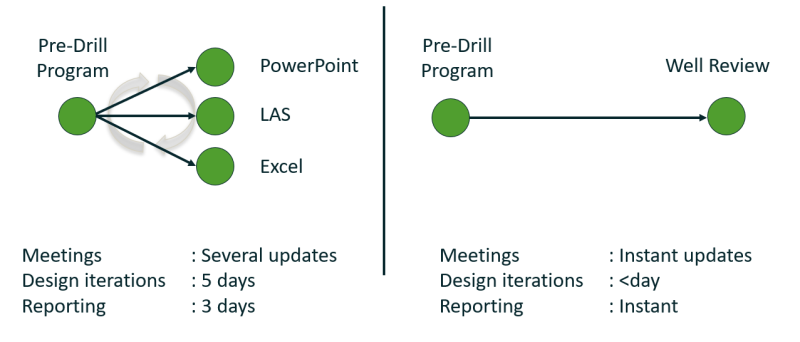
The Key: Digital Knowledge Management
New digital tools and approaches that focus on the output start at a disadvantage. In order to modernize well planning, the most effective place to begin is with the input.
This is in line with the idea that true digital transformation is needed to tie data together into a single format and source—i.e., a single version of the truth—that is multifaceted enough to provide the details that each party requires.
It also has to be dynamic. Updates must be able to flow through. Users must be able to access data easily, wherever they are, with an intuitive display of data and risks. Such a streamlined process is faster, more efficient, more effective, and as a result, less expensive.
Digital knowledge management solutions represent one of the enablers. The software technology frees experts to focus less on interpreting files and clicking buttons and more on analyzing a full data set—ultimately creating a better well-planning process. This pays dividends as expenses are curtailed to improve profitability.
This newly adopted approach allows PPFG to be performed more quickly and expands its applications in prospect risking, making it even more useful and reducing the amount of redundant activity by participants.
As analysis moves away from locally stored spreadsheets and toward centralized data collection, pore pressure activity will increasingly be used by first movers to derisk prospects and communicate such vital information more effectively among multidisciplinary groups.
In practice at many companies today, decisions are made based on the view of a line on a plot. But with all data and interpretations accessible, these multidisciplinary teams will have more sources of information and will be empowered to understand results. In other words, they are a more effective force.
This comes together as iterations are reduced and knowledge sharing on well delivery increases. Aside from saving time, this leads to fewer errors in the field and better compliance with industry standards and regulations. Increased collaboration is widely recognized as one of the keys to identifying and resolving problems faster, which, in turn, yields improved safety profiles.
The end result is more effective project management, with better resource utilization, budget control, and alignment of project goals across the organization.
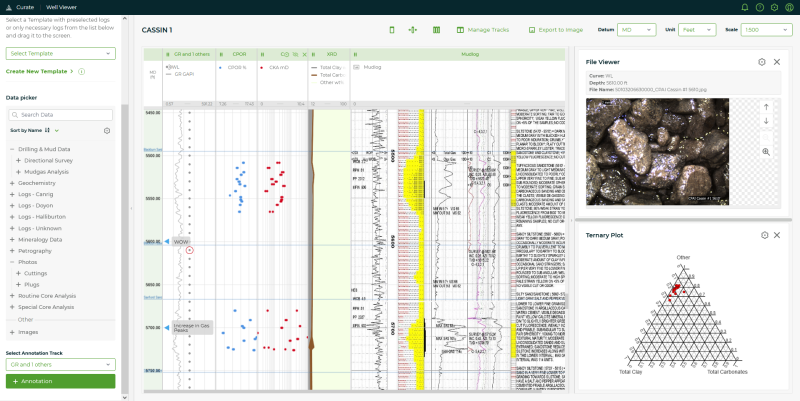
Small Improvements Lead to Big Results
Even a small improvement in time savings, quality, collaboration, safety, or project management can have a cascading effect on a drilling project as a whole. The potential results include substantial cost savings, faster delivery times, higher customer satisfaction, and better business outcomes.
Drilling costs depend on the depth of the well and the daily rig rate, which varies according to rig type, water depth, distance to shore, and drilling depth.
For example, the daily onshore rig rate is typically less than $100,000 per day, while, for deepwater offshore Gulf of Mexico, rates are more along the lines of $400,000 per day.
With offshore drilling, the price of the equipment represents around 90% of the total investment costs of an oil producer, with the involvement of about 30–40 individual companies often required to fully complete the project. The result is a great deal of data transfer among parties with varying experience levels and objectives.
Accurate pore pressure calibration and modeling can provide drilling and subsurface teams with valuable guidance in selecting parameters such as mud weight management, casing point selection, wireline sampling point selection, reservoir monitoring, and data acquisition, particularly in high-risk/low-calibrated wells. With effective communication technologies, these data points can work together to speed up the process without sacrificing safety or accuracy.
In addition, drilling depends on timely measurements and continuous circulation to maintain the safety of the wellbore. If the drilling process takes too long, time-dependent changes within the wellbore can occur—e.g., well creep, swelling, shrinkage, rock failure—that can alter the rock's mechanical properties, affect wellbore stability, and result in additional costs and difficulties in running logging tools. Technology can play a vital role in helping users focus on what matters and thus hold down the time required to drill.
Based on studies conducted by automated well control systems provider Safe Influx, a significant proportion of drilling-related incidents can be attributed to human factors, such as distractions and high workloads, with organizational issues and hardware failures also being contributing factors.
As such, it is important to consider the potential for human error in the PPFG process. The implementation of automation and intuitive technology can promote better communication both before and during drilling, thereby reducing the human factor and minimizing the likelihood of serious incidents.
Well Delivery Evolves
As companies take on more complex geological cases, reliable PPFG data becomes even more important. Ultradeep wells both onshore and offshore hold the promise of significant production but come with higher risks related to safety, environmental impact, and structural requirements. Faulty predictions because of inadequate communication are even more problematic in these contexts.
Technology works best when it helps people perform better at what they currently do. Incorporating a software solution that empowers the right data and knowledge to be immediately accessible when needed to affect decisions, rather than just adding more tools to the toolkit, is fundamental to improving the PPFG well-planning process. When this occurs, the process can be truly optimized to generate more effective outcomes that lower total costs.