The oil industry has long flirted with virtual reality (VR) and visualization tech but falling prices and technological advances mean this once-futuristic concept is becoming more practical.
The tech is appealing because oil companies have struggled to visualize complex subsurface data and effectively train their workforce. VR’s immersive nature is helping companies overcome such challenges.
Space for Cores
Physical space has long been a constraint when it comes to analyzing core samples at the YPF Technology (Y-TEC) research facility in Berisso, Buenos Aires.
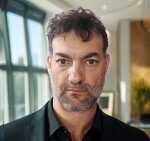
Ariel Guzzetti, lab and data manager for the subsurface services department at YPF Technology, told JPT the lab can display up to 500 linear m of physical core at any given time. Core projects tend to take between 4 and 8 months to complete because during those projects specialists require frequent access to the cores. Sometimes the facility displays optical electronic microscope images, CT scans, log plots, charts, and other data related to the cores on laptops, monitors, or printouts near the cores, such as for workshops or training sessions.
“That’s how we run out of space,” he said.
The facility can handle somewhere between five and eight projects simultaneously. “We usually have three, five, seven projects on hold, and not due to the capacity of our lab. Maybe we can do more tests, but we run out of space to lay out the cores,” he said.
Finally, Guzzetti said, people frequently travel to the Buenos Aires facility to work with the cores, which can be inconvenient or costly.
But virtual space is a different story: Enter the “miniverse,” a small virtual universe, in this case dedicated to geoscience.
With VR, it’s possible to “bring people to the rock instantaneously,” he said, and displaying relevant data is much easier. “With this technology, you can mix up the rock and the data together without the restriction of laptops or TV screens. You can display as much information as you want, all in the same area.”
With VR, experts can access and examine the cores, consult existing core data, and interact with other experts to study the samples.
Core images, scans, and other information can be used to recreate the core digitally so it can be studied and interacted with in a virtual environment.
Currently a geologist can see the structure, fractures, and facies in the core. Guzzetti emphasized that the virtual core is not the same as a digital twin of the core.
“For core description, it does not replace the actual core. It’s more for analyzing data and seeing bigger structures,” he said. But he believes a digital twin future will be here soon, with virtual cores providing higher-resolution details.
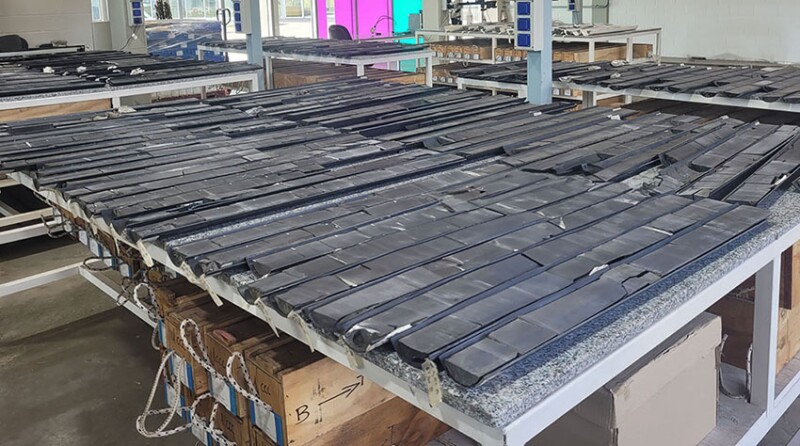
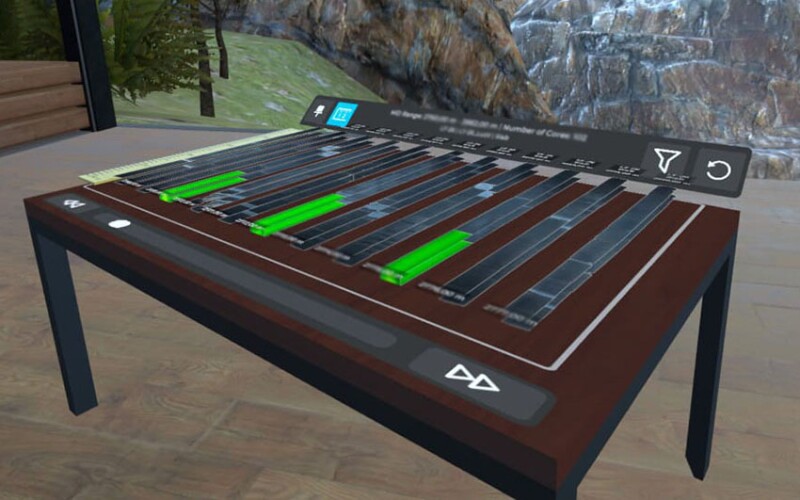
For now, though, Y-TEC is testing VR technology and plans to deploy its use within the +VacaMuerta consortium.
“We are going to give a VR headset to every consortium member,” he said. “We can even coordinate to do meetings in the virtual reality so they will not need to come to our lab to see the rocks.”
Working in the miniverse requires the use of a VR headset, and Guzzetti has been testing the Meta Quest 3 and Quest 2 versions.
“In order for this technology to really grow up, we need more headsets in the market,” he said.
Working with VR headsets doesn’t come naturally to everyone who may need to use one, but they can learn how to work the equipment fairly quickly, he added.
“Most of the people who try it need only 5 to 10 minutes to realize how to operate inside the virtual reality. In fact, what we are doing right now is if someone needs to use it, we give him the VR headset for a weekend and encourage them to try it” using entertainment software, Guzzetti said. “Within a couple of days alone or with our assistant, in 5 to 10 minutes, they are already using the system.”
He enjoys witnessing the responses of people new to VR. “It’s amazing to see the first impression when people who don’t use virtual reality and haven’t before tried this kind of technology. We introduce how to use it, and they always say, ‘Wow! I can see the core’ in virtual reality. The first impression is always a ‘Wow!’”
While learning to operate in VR using a headset may not take too long, some people cannot tolerate being in a VR environment for extended periods of time. “Some people get dizzy and are not comfortable using the helmet for long periods of time,” Guzzetti said. Limiting use to shorter periods can be helpful, or those individuals can work in mixed reality rather than full VR, he said.
Geology Field Trips
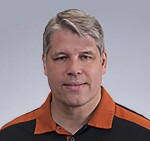
Robin Dommisse, senior 3D geomodeling advisor for the Bureau of Economic Geology (BEG) at The University of Texas at Austin, said immersive technology has evolved from the “status symbol” visualization rooms that companies were spending big dollars on at the turn of the century. Those rooms—meant to enable collaboration and decision making—tended to be larger auditoriums with expensive projectors that showed 3D images on a static screen for users to view through 3D glasses.
Such rooms fell out of fashion as companies sought solutions more conducive to collaboration.
One solution that is rising in popularity is the combination of immersive software and a VR headset. Multiple users equipped with VR headsets can gather in a virtual room to examine cores, and in these rooms, they have access to outcrop data along with subsurface data like well logs, 3D seismic, and models.
“Think of it as a transition from a standard 2D PowerPoint presentation to an interactive, 3D visual collaboration space that integrates all your geological, geophysical, and engineering data and serves as a decision-support environment,” Dommisse told JPT.
Being able to see inside the rock enables geological analysis that helps bridge understanding from outcrops to the subsurface data, he added. Integrated 3D visualization software like BaselineZ, which BEG uses, puts the digitized core data into a virtual space on a virtual table so a user can scroll, investigate, and interpret thousands of feet of core data for multiple wells in the same VR space. Users can see important rock attributes like porosity and permeability, and the software allows for the visualization of reservoir simulation results, such as to reflect various stages of a waterflood project, he said.
“You see a reservoir simulation fluid front pass through a reservoir with each time step between injectors and producers. And of course, then you can expand that to other forms of enhanced oil recovery,” Dommisse said. “It’s a real interesting way to combine not just the multiple subsurface data, but also combine the engineering interpretation together with the geological interpretation.”
While visualization and simulation are critical, he said major value comes from such an environment being able to support decision making. The more accessible and easy to use the decision support tool is, the more value it can provide, he said.
“I think that virtual reality is going to play a much more important role in that in the future,” he said. “You don’t just bring the data together just to study it or to analyze it, but actually to use it for a real-time decision making in exploration and development scenarios. If you can do that, then, no matter how much a tool would cost, it would quickly pay for itself.”
Dommisse sees use for such tools beyond decision making at oil and gas companies. With VR technology, geology students or busy engineers—no matter where in the world they are—can take a virtual geological field trip to the same place at the same time to learn more about outcrops and the subsurface.
People from all around the world could sign into a particular virtual room and their avatars would be present for a meeting, lecture, or tour.
“It is a really big advantage if you want to either teach a number of students in multiple locations, or you want to bring expertise together from multiple locations in the world, looking at the same sort of images, models, three-dimensional displays, and so on,” Dommisse said. “We see an incredible value for training, education, and interaction.”
Even those without base-level knowledge in a topic can benefit from VR sessions.
“We’ve also done this with people who effectively have zero interest in the actual subject matter. Let’s say, if you bring somebody who’s not a geologist, like me. You invite them to a room, and they see all this type of unfamiliar stuff. For some reason, people engage more,” he said.
Seeing things in 3D makes everything easier to understand because human brains are adapted to quickly analyze complex 3D scenes, he said. “If you look at something as esoteric as a well with a well log with three-dimensional seismic with surfaces, with faults, all these typical types of geological things, when you see them in true 3D, even a layperson, a person who’s not an expert, can understand what these objects are. They see planes, they see cross sections, they see surfaces, they see maps.”
He’s seen VR efforts fail over the years, he said, and it finally seems like everything is coming together to help move VR technology into the mainstream.
“All of the technologies have kind of come together to create a perfect storm where everything becomes much, much more affordable. I tell people regularly that if you want to get into virtual reality for the oil and gas industry, all you need to do is buy a 3-year-old version of the Meta Quest 2, which now is down to $200, and then you can download tools like the BaselineZ viewer for free,” Dommisse said, although he noted BaselineZ collaboration rooms are also accessible via viewer software running on a smartphone, tablet, or laptop. “The person who creates the room pays for the room. I can invite a large number of people to my room to educate them, to interact with them, and so on. It’s really the most affordable time in history to get into virtual reality.”
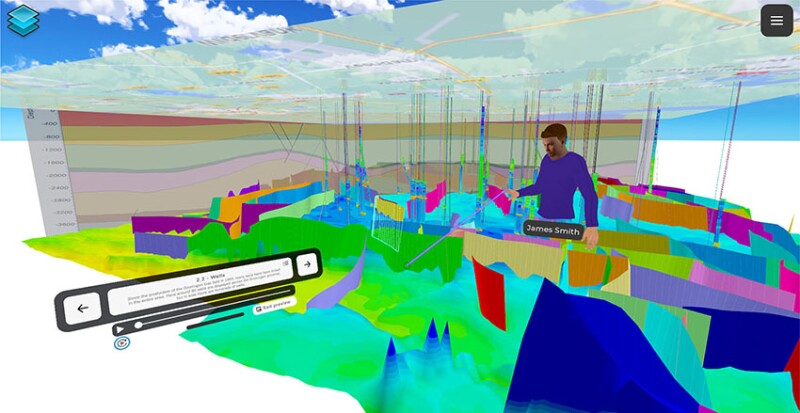
Immersion Rooms
Immersive technology helps people better visualize complex information, such as subsurface details. BaselineZ started in 2017 to enable geologists to collaborate on subsurface data in a VR environment.
“Our biggest concept was that geologist A could collaborate with geologist B anywhere in the world,” Jim Thom, business development advisor for BaselineZ, told JPT.
And while the platform, which allows users to interact with data and 3D models in an immersive environment, remotely and at scale, has been used to help geoscientists better understand subsurface data, BaselineZ has expanded its use cases.
Beyond core analysis, the other main uses are education and storytelling, he said.
An immersive environment can help “a new engineer, a new geologist, a new geophysicist, a new manager to a very complex asset” get up to speed much more quickly with a better depth of knowledge as compared to learning through slide decks, Thom said.
3D storytelling can be used to educate the public on complex projects, such as carbon capture. “Imagine the public is sitting there thinking, ‘Well, I want carbon out of the environment, but I don’t want it underneath my ranch.’ So how do you explain to them that it’s okay?” Thom asked.
3D storytelling using immersive technology can give people a much deeper understanding of the project, he said.
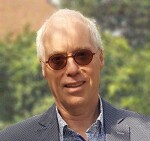
BaselineZ was originally designed for a VR environment, with users accessing the immersive environment by wearing VR headsets. But, as Gerard de Jager, director of strategy at BaselineZ, told JPT, “It turns out that a lot of people were not ready for that.”
But people are ready for a modernized version of the costly visualization rooms of the past.
One of the drawbacks of past viz rooms was the cost. Not only were they pricey, sometimes running to millions of dollars and taking months to build out, but the rooms could only display content prepared ahead of time and typically required someone to operate them.
Perhaps one of the biggest problems with viz rooms of the past is they were not conducive to collaboration, Thom said, recalling one conversation with an oil company professional.
“One of the managers said, ‘Why is it that we call these collaboration rooms when it’s more like a movie theater? How would you expect us to collaborate with these stupid (3D) glasses on in a dark room?’” he said.
In short, he explained, the design and parameters of viz rooms of the past were self-defeating. Essentially, they missed the mark.
“I called it a near miss because the industry wanted to have this,” Thom said.
Such rooms would allow companies to derive more value from high-salaried experts, and they would help promote safety, he said. “They wanted to solve all that. They invested a lot of money. There was a lot of money, time, and effort, and I call it a near miss.”
Over time, technology has evolved, and prices have dropped on many of the elements needed to create viz rooms.

Igloo Vision Ltd.’s Holly Mindel, business development manager, told JPT that viz rooms of the past were so costly partly because the previously available blending and warping software used in creating the immersive experience was military grade, expensive, and inaccessible to most businesses. Beyond that, many of the immersive rooms could only handle limited types of content and required multiple media servers to run. Finally, she said, the rooms typically required someone with experience to run them.
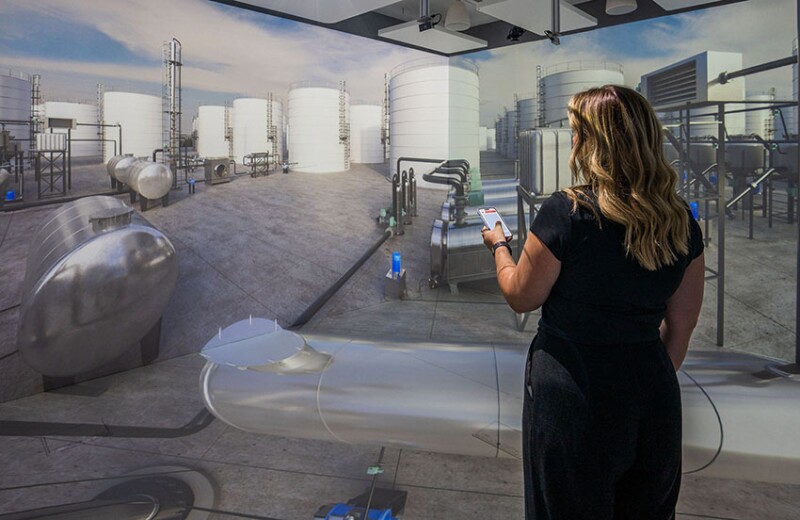
Igloo Vision, a shared immersive space company known for its immersive geodesic-shaped domes as well as cubes and cylinders, wanted to create a flexible immersive system that could be used for multiple use cases. Beyond the oil industry, Igloo customizes rooms for architecture, big tech, education, and sports. It is able to accommodate any type of content, she said.
Over time, technology has improved and much of the equipment needed has dropped in price, to the point where a smaller custom Igloo immersion room, which projects imagery onto the room’s four walls and its floor, can be built out for about $250,000 in less than a week following a consultative process that helps define and establish content development workflows.
And, Mindel said, the rooms don’t require a dedicated operator.
This month, Igloo is opening an immersive demo room in Houston. Kitted out with 4K projectors, the room shows off the capabilities of a modern immersive room to oil and gas clients considering setting up such a facility on their own premises.
Since 2014, the company has installed a number of rooms powered by between four and 12 projectors for oil and gas clients around the world. The rooms are powered by the hardware-agnostic Igloo Core Engine, which supports use of VR, 3D, and 360-degree content, as well as web-based content, presentation and office tools, and game-engine-based content from Unity and Unreal Engine. A feature called true perspective automatically applies true-to-life perspective to 3D models. The whole room can be controlled by technical or nontechnical people using phones, laptops, game controllers, and/or tablets, and it requires a single server to run. It integrates with a number of third-party apps, including the BaselineZ digital twin and model‑viewing platform.
De Jager said BaselineZ has worked with the Igloo team to standardize the application as a plug-and-play solution for use in viz rooms. “For a core team, or for a drilling team, we have a standardized solution.”
Whether experts are gathering virtually from around the world using VR headsets or in an immersive room, the software makes it possible to bring knowledge together without the need for travel, he said.
Thom called it gathering the collective genius.
“When we drill wells in the energy business, there is a clear separation between the geology, geophysics, exploration department, and the drilling engineering department. And why is that? Because they can’t see everything together,” he said. “The drilling engineers will look at the problem in a way that says, ‘How far can I bend a pipe if I’m doing a long-reach well in deepwater?’ And the geologists will be sitting there thinking, ‘Why can’t you hit this target that’s 26,000 ft below here?’ But (the drilling engineer has) to drill through the fault in a certain way so that the well doesn’t get stuck.”
Putting the different disciplines—who may otherwise have a difficult time communicating with one another—together in an immersive room enables them to collaborate more easily because they can see all their data at the same time, he said.
“Not only can they see the geomodel but imagine now also that the engineer can have their drilling torque sitting right here” and can see what might happen if a variable is changed, he said.
Such rooms can also be used to better understand challenges that need to be solved.
De Jager said people from multiple locations were working to solve a drilling problem in India, where the very large Igloo room allowed them to see the issue at scale. “It’s not a flat screen, but it’s also at the scale of the drilling problem,” he said, adding he found it “a fascinating learning that looking at the problems in scale is helping to find the right answers.”
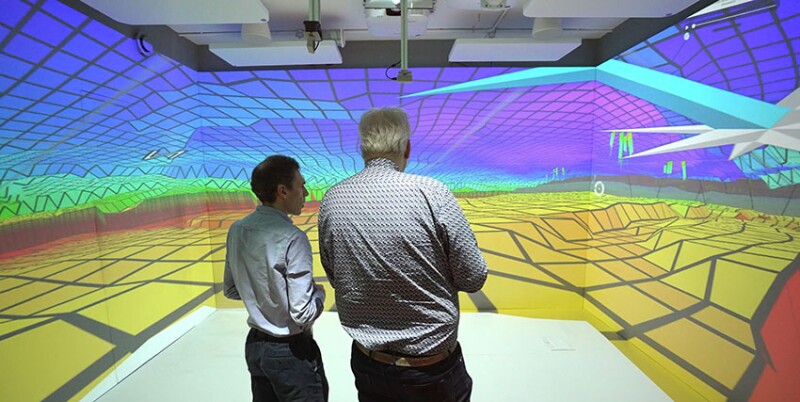
Hazard Avoidance Training
In the oil and gas industry, people train to prevent and avoid problems.

John Morgan, senior principal for energy systems at DNV, told JPT industry professionals can come to DNV’s Spadeadam Research and Testing facility in the UK to “see a real, live, full-scale fire or explosion, the sort of thing that they spend a lot of their jobs trying to avoid and prevent. Clearly, not things that you actually want to see in an oil and gas situation. But the danger is, if you’ve never seen these things, you never realize how bad a 30-ft fire is, or an explosion.”
But travel can be expensive and time-consuming, so alternatives like VR training can be attractive.
“If you go to Spadeadam and see a 20-ft jet fire, it’s loud, it’s hot, all those things. You don’t forget it. If you see me standing up giving a presentation, well, maybe you might remember it for a little bit, but it’s probably not one of your highlights of the year. VR is sort of halfway between the two. It’s something that people are not using on a day-to-day basis, so they do remember it, and that means they remember the major hazard safety message that comes with it,” Morgan said.
VR training scenarios can reflect realistic tasks that might go wrong on an oil and gas site, and DNV has developed a series of immersive VR for major accident-avoidance training, which are licensed to oil and gas companies.
“The VR doesn’t quite look like offshore, but it definitely doesn’t look like a CAD model with shiny red bits and bits of green structure or whatever else that you’ve got. It looks more like an offshore environment, really making you think you are offshore,” Morgan said.
The point, though, is realistic training for hazard avoidance, he said. In one of DNV’s scenarios, a piece of scaffolding drops and impacts on a small-bore connection, which fails and releases high-pressure gas which then ignites and causes a fire.
“We have people with a bit of vertigo who don’t like that scenario at all because it’s realistic. It literally feels like you’re on the edge of a big process plant, looking 20, 30-ft over the edge,” Morgan said. “It allows people to really think they are on that site, which is why it’s so memorable, which is why it really drills home the message for them.”
The scenarios also include a running timer so users must react to situations on the same timescale as in real life. “There’s no point in doing VR if you can take a pause and give it your best answer,” he said. “You have 10 seconds to make a choice.”
He said offshore safety representatives have given “great feedback” on the scenarios, particularly regarding trainee engagement.
“You’ll go through a whole career and never see anything remotely like a major hazard,” Morgan said, which means “complacency can set in.”
Engaging the workforce during training is essential.
One of DNV’s VR training customers is Harbour Energy, and the pair delivered a case history paper on the topic in SPE 215563, presented at 2023 Offshore Europe.
In the paper, the coauthors concluded that the use of VR for accident-avoidance awareness training enhances workforce engagement at all levels of the organization. “It is clear that there remains untapped potential in the use of the VR technology for the purpose of promoting process safety, which should be further evaluated,” they wrote.
Under DNV’s commercial model for immersive training, they reinvest one-third of the licensing fees back into the VR training program to develop fresh and more-complex scenarios.
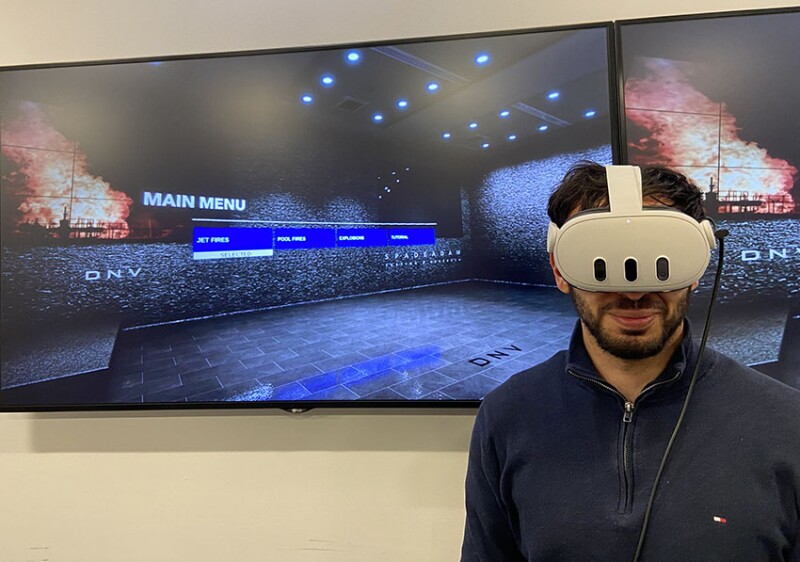
Understanding Proppant Transport
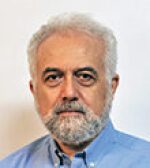
Tayfun Babadagli, a petroleum engineering professor at the University of Alberta, said his research group is using VR headsets in its research into how proppant transports in fractures, among other things. He said the idea is to visualize the model and processes three-dimensionally, studying the processes from different angles as the visual model is moved around.
He said the computational models are helping to better understand the physics and mechanics of how proppants move in pore space or in fractures than when merely using 2D visualization or graphical output.
VR makes it possible to visualize what’s happening between the wall of the fracture and proppant and how the proppant transports in the reservoir environment, he said. “Even the interaction between the two proppants—they hit each other, they collide,” Babadagli told JPT. “This is why VR is helpful.”
The system his research group is using is a simple one that serves their purpose, he said. It includes a large TV screen with 3D visualization capacity, cameras, headsets, a pair of workstations with video cards and software, and a joystick control system. “3D is the main thing,” he added.
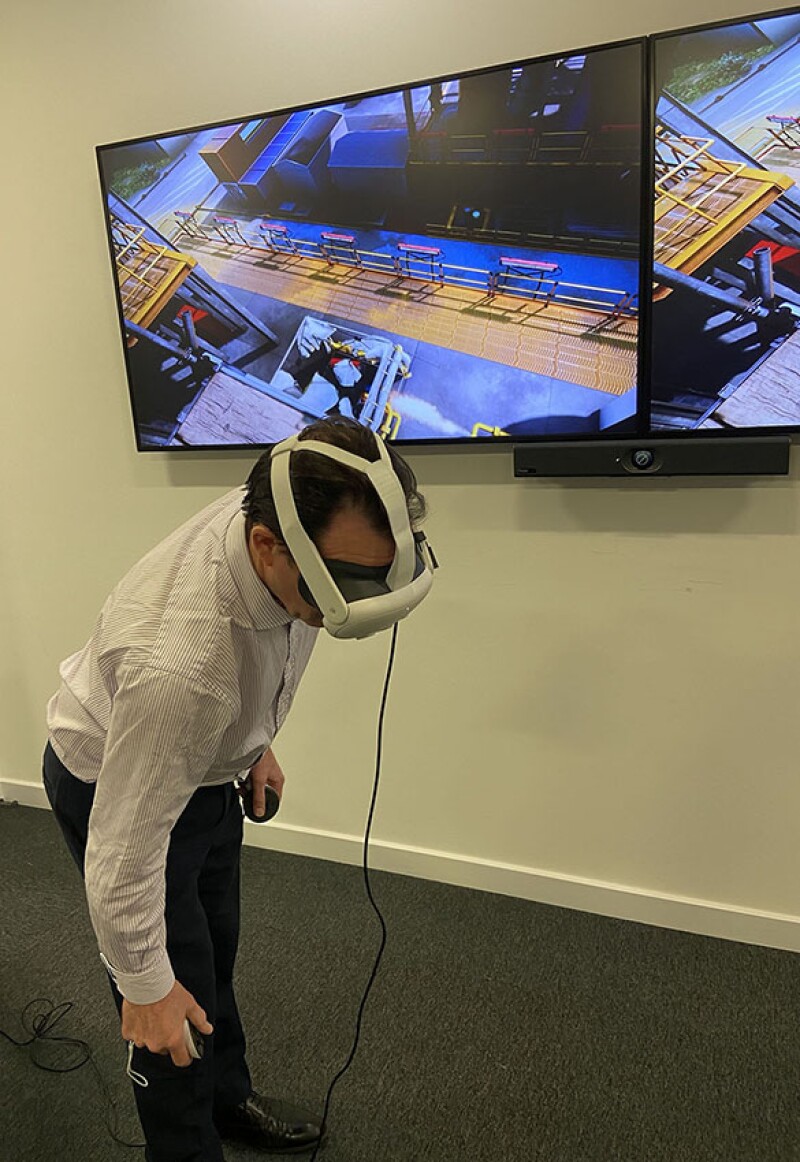
For Further Reading
SPE 215563 The Use of VR Technology for MAH Awareness Training by C. Luoma, DNV, and M. Wardrope, Harbour Energy.