In 2014, Anadarko Petroleum had just a single data scientist in its ranks. Today, it has almost 20 of them working at its headquarters north of Houston.
They are joined by a couple dozen more software developers, geophysicists, and reservoir engineers who together make up the independent producer’s Advanced Analytics and Emerging Technologies (AAET) group.
The initiative evolved from a slide deck put together just over a year ago to become the “spearhead for technological transformation in the company,” said Sanjay Paranji, the vice president of technology at Anadarko and head of the AAET program.
It is a sign that things can move swiftly in this industry, and for the group to be successful, it must keep up the pace.
The ambition that Paranji shares with the industry’s other transformation leaders is to undertake rapid experimentation to uncover the advanced hardware and software that can be scaled across hundreds or thousands of wells. The longer that job takes, the more wells get drilled and produced without the benefit of new optimization technologies.
This justifies why the AAET group uses a very different blueprint compared with all other business units at Anadarko.
Management operates with a light touch, emphasizing a high degree of autonomy among its project teams; too much intervention and the cultivation of creative brainpower yields less and less. The group also moved into a reinvented workspace this year, designed specifically to spur collaboration. Even the words routinely used by the staff stand apart from industry jargon: scrums, sprints, and MVPs, or minimally viable products.
The heart of the recipe involves combining roughly equal parts of Anadarko’s recently recruited data science talent with its experienced petrotechnical workforce. The idea is to get petroleum engineers to learn all they can about data science, and for data scientists to learn all they can about petroleum engineering.
“That’s our magic,” says Paranji. “We offer them complex problems, which gets the juices flowing—and that gets them to want to stay here.”
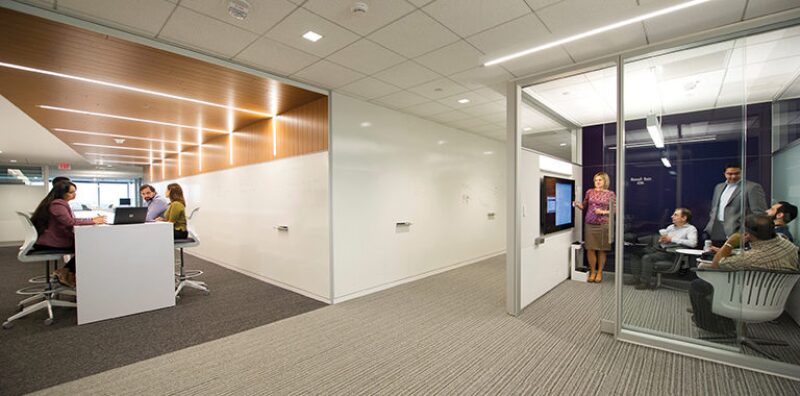
Innovating Through Failure and Cupcakes
To keep the digital train moving, Anadarko uses what is known as a scrum approach—a term borrowed from rugby where teams push the ball toward the goal together.
Four to five people make up each scrum team, of which there are eight to 10 working on various projects at any given time. Their mandate is simple: prove within 2-week sprints that an MVP is on course to make a meaningful impact, or should be dropped.
As the ubiquitous startup mantra goes, fail often and fail fast.
“To be stuck on something based on a sunk-cost bias for 6 months, and you’re trying to press on despite the fact that you have limitations in your approach, that’s a bad sign for us,” Paranji said. “You try an approach, it doesn’t work, you put it to bed, reformulate the problem, and then go after it with a different method.”
Earlier this year, a scrum team had been working on an artificial lift optimization project for a couple of months (an outlier in terms of the length of time) before it finally got the ax. To sweeten the blow, senior managers announced the news by throwing staff a cupcake party.
Despite the cancellation, the efforts uncovered a better way to acquire high-resolution data from rod lift units, a learning that will be carried into the next try.
The cupcakes were management’s way of saying they appreciated the hard work that went into the tanked project. However, the more important takeaway is that the path to a breakthrough innovation is often paved with a series of failures.
If this experimental role was placed squarely onto the asset teams, who must focus on meeting production and budget targets, the concern at Anadarko is that digital innovation would get pushed to the side as isolated pet projects, never becoming a true priority.
For Diego Molinari, a reservoir engineer working on the company’s unconventional analytics applications, being part of the AAET group has meant having more time to be creative.
“When you’re in an asset day-to-day, you’re involved in meetings and every day there is a different issue,” he said. “Here, we can really afford to be strategic, take a step back and look at the big picture and try to develop solutions that are long-term.”
Digital Partnerships Abound
Despite Anadarko’s accumulation of talent within the AAET group, success will not be fully realized by going it alone.
The company is counting on the help of big tech firms such as Google and its deep learning tools for interpreting geological features to help decide where to drill next. Through its work with Schlumberger, the AAET group helped distinguish Anadarko as the first operator to put a large seismic survey into a cloud environment.
Several of the data scientists and developers in the group have been contracted, giving it the ability to throttle its resources up or down depending on the size of the project pipeline. It has also launched a crowdsourcing program that assigns projects to a digital community formed by millions of programming experts.
Startups are part of the mix too. Some are invited to work at the company with its full-time employees, which helps ensure new innovations are tailored to fit Anadarko’s needs.
Not least of all are the asset teams. The people who design the wells and produce them for years after need to believe in what the AAET group is doing. This is a defining philosophy of the group and places it in a position similar to many of the digital vendors it spends time scrutinizing.
“The advantage is that we’re already inside the door,” related Sathish Sankaran, the engineering manager in AAET. “Having said that, it’s still not easy.

Adoptability is an “Exercise in Translation”
One of the other people undergoing the hybridization process at Anadarko is Justin Hayes, a staff reservoir engineer who has been at the company for his entire decade-long career. Half of that time was spent working on unconventional formations, where he saw that traditional understandings of science and physics “were kind of broken.”
The inadequacy left a lasting impression, so when Hayes went back to school for an MBA a few years ago he was inspired to take courses in multivariate analysis, machine learning, and Python. That gave him the basics of data science without going all the way. However, the new skillset was enough to make him one of the first engineers to be pulled into the AAET program.
Working alongside Hayes in a scrum team is Vincent LeMoine, who prior to joining Anadarko was using his PhD in statistics to develop data science projects for a packaged goods retailer and a major air conditioner manufacturer. He was the second data scientist hired, and as the manager of data engineering, he earns a deeper understanding of exploration and production with each project.
The two men recently worked with Anadarko’s acquisition group that asked for a better way to analyze leasing activity shifts in shale plays. Their MVP, which took even less than the ideal 2 weeks to develop, eventually became a regularly used visualization tool that shows what other operators are up to in areas that Anadarko is also interested in, or perhaps should be.
The independence that Hayes and LeMoine were given on this project is another key characteristic of the group’s thinking. Upon accepting it from the acquisition unit, their charge was to evaluate the value of the problem being solved and balance that out with the resources required to tackle it.
“And sometimes that’s a little hard to measure,” said LeMoine, noting that when projects begin, no one can really say how much time they may take to finish. Another difficult-to-assess factor that LeMoine argues is “really important, is adoptability—what’s the probability that people are going to use it?”
The answer can depend on a scrum team’s ability to communicate. Because of his experience in an asset team, Hayes knows intimately that petroleum engineers will never settle for having answers simply delivered to them; they need to be explained. He described the process as an “exercise in translation.”
“You have to take the things we put together in code and then translate that into the steps that code took, show here’s what each of those steps mean, and here’s the end result,” he said.
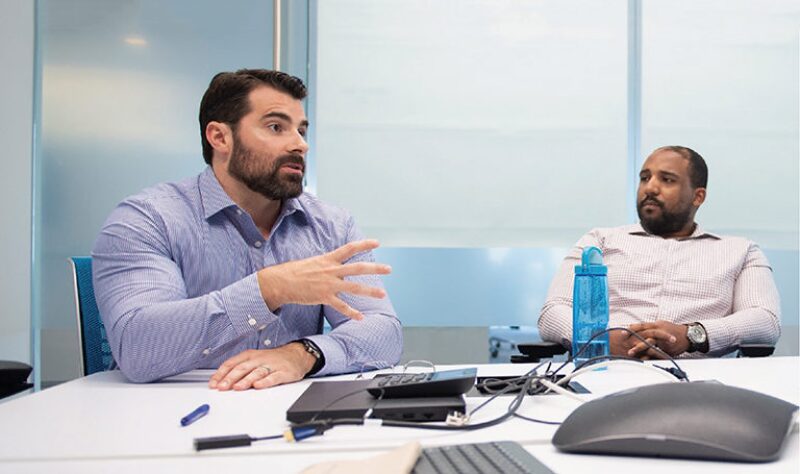
Anadarko’s Analytics Platform
The most tangible example of the change that the AAET group aims to bring Anadarko is known as IPSO, or the integrated production surveillance and optimization platform. IPSO is a combination of new monitoring and analytics technologies that ties together each of the business units involved in field development.
Though the platform was developed before the group’s official formation, several members were deeply involved and remain responsible with expanding it.
The large-scale integration project, which remains novel in the industry, “fundamentally changed the way in which we do routine surveillance for both production and reservoir engineering,” said Sankaran, who authored a technical paper (SPE 187222) detailing the project.
First deployed on the company’s Gulf of Mexico Lucius spar in 2015, ISPO helped facility staff hit a 97% uptime during the 6-month startup phase. Sankaran noted that achieving such efficiency on a new offshore asset was “unique” in the company’s experience.
Today, IPSO covers all of Anadarko’s deepwater facilities where it captures, analyzes, and stores the changes happening within any of its subsea wells. Automating these processes enables Anadarko to see well performance problems start to take place in just a couple of days vs. the weeks that it took without the system.
These early warnings helped avoid several multimillion-dollar workovers, any one of which saved enough cash to cover the entire cost of the IPSO project, said Sankaran. The next mission is to get ISPO to deliver these kind of benefits to Anadarko’s shale fields.
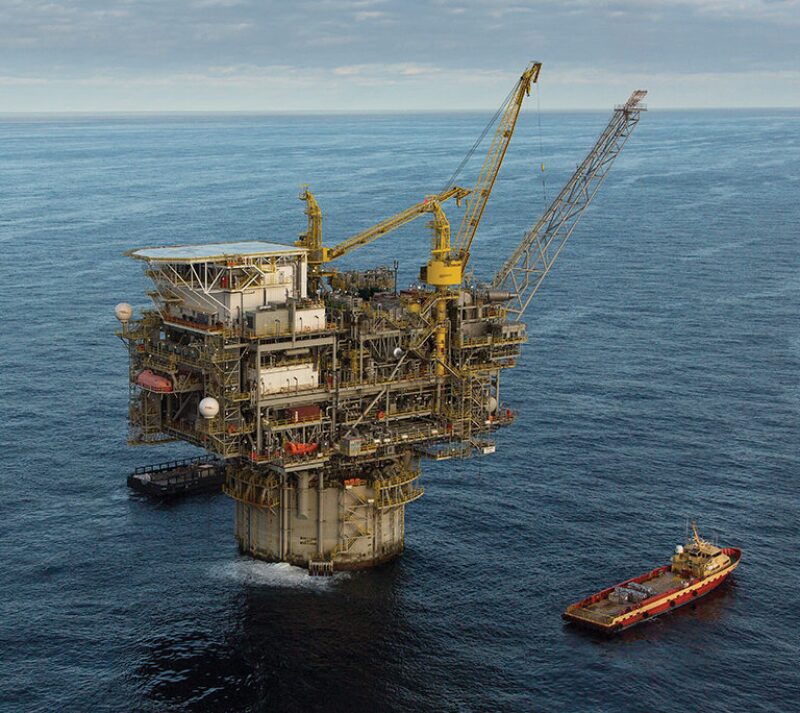
Shift in Data Access Builds Trust
IPSO represents a nascent movement in oil and gas to de-silo important data sets, and combine them in ways that gives operational staff a fuller picture of their assets. The platform accomplishes this by connecting data from otherwise disparate sources, e.g., sensors and flowmeters, and giving engineers access to all of it via a search tool.
This marks a shift from the past, one in which Anadarko’s engineers did not always know where to find certain data sets because they were stuck within isolated spreadsheets. Now, “those spreadsheets become accessible to you from just a query,” said Mike Perrotte, a data scientist working on IPSO’s unconventional expansion.
With information easier to get to, engineering teams can run more simulations and test new ideas quickly. The transparency and flexibility of the system also helps build trust, a requirement for adoptability. Perrotte compared the features to how car drivers have the ability to choose between routes on Google Maps.
“If an engineer wants to tweak with something, they can alter some parameters and then the algorithms will run at scale in the background and return back the results,” he said.
As this capability is brought online to the unconventional teams, the hope is that they will have a clearer idea of what is dictating well performance. In a booming shale field, it may not always be the result of a completion style or the reservoir rock.
“Some wells might be producing more, not because they are better wells, but because they have the facilities in place, while other areas are constrained because your midstream development hasn’t caught up,” Molinari explained.
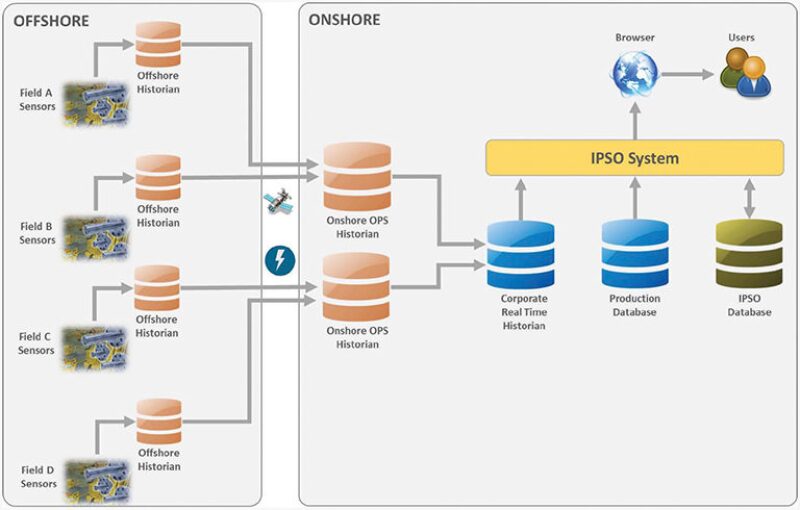
Addressing the Recruiting Challenge
In addition to scaling up hardware, operators will need to sustain their digital transformations with more people, which will be a challenge. The upstream industry has openly acknowledged in recent years that it is not the most attractive sector for data scientists.
Part of the issue has been the industry’s lack of organizational support for this new breed of talent. Anadarko recently addressed this shortcoming by approving its first career ladder for data science staff, which means it can now show potential recruits the rewards that come with a long tenure.
But despite the scarcity of data science professionals available to the industry, operators must still be choosy and look beyond a candidate’s technical capabilities. For Anadarko, that means the right data scientist is one who appreciates supporting oil and gas domain experts in achieving their goals.
“I’ve seen over those years that humility makes a good working relationship,” said Jeremy Graybill, the senior manager of data science, who was hired 4 years ago as Anadarko’s first bona fide data scientist.
He is now helping to shape its recruitment efforts for more of his kind, and noted that the highlighted virtue is actually a prerequisite for a job offer in the AAET group, not a nice-to-have.
One of the other efforts includes the physical changes Anadarko expects to help pull in, and retain, the personas it needs to keep driving the AAET project forward. Gone is the typical corporate layout—cubicles and narrow hallways lined with private offices. In its place is something that looks much more like a software startup.
“We felt from the get-go that we needed a different type of floor—that was a decision made before even forming the team,” said Jose Silva, the lead business strategist in the AAET group.
He shared that to get ideas for how the office would look, managers issued surveys, and reflected on some of their own experiences on what to keep from the conventional layouts. In the end though, the group’s floor is distinctive from the rest of the building.
In some cases, sacrifices have been made. Instead of prized corner offices with sweeping views, managers including Graybill and Silva work behind glass doors in a row of windowless offices that can comfortably fit about two people, encouraging them to walk around and interact with staff more often.
Once-blank walls and corridors are plastered with whiteboards and staff-made posters detailing how they are using particular machine learning techniques to solve production issues.
A wide and open kitchen is both a place for eating and meeting—an interior design feature inspired by the way employees brainstorm in Anadarko’s coffee shops. For the same reason, a pool table that doubles as a ping pong table sits where a conference table usually would in one of its largest meeting rooms.
Nearby is an open congregation area where product demos can be shared between the group and its internal customers. And when not using these shared spaces, engineers and data scientists do the rest of their work from private pods, couches, or long multi-person computer tables.
Though it is easy to see this as an abundance of office perks, Anadarko views it all as an experiment to see if it can promote a higher level of teamwork and communication. And for some of the group, the modern comforts will be fleeting.
Within a couple of years, domain experts like Molinari and Hayes may be asked to pack up and head back to an asset team, as others are welcomed in. In resuming more traditional roles, the two reservoir engineers will bring their knowledge of the analytics trade craft to help Anadarko’s internal adoption efforts.
If they were to stay put, Paranji thinks the group risks becoming too “research-and-development heavy” and will lack the embedded champions it needs to continue driving innovation adoption within the company.
“Even though you develop cool tools out here,” he said, “at the end of the day, you have to supervise actionable change at the asset team level for it to be real.”