A 2-year comprehensive effort to design, test, manufacture, and deploy a new high-pressure completion tubular (CT) for Chevron’s deepwater Gulf of Mexico (GOM) operations is presented. The completion application expected harsh, aggressive loading modes and high pressures to be encountered. The major challenge was to design, test, and manufacture a subsea-completion string that would provide efficient hydraulics during fracturing operations while ensuring mechanical and pressure integrity.
Introduction
In 2004, the first built-for-purpose CT incorporating a gas-tight, rotary-shouldered connection was developed and deployed in the GOM. Since that time, rotary-shouldered connections have evolved (this evolution is described in detail in the complete paper). Present-day connections offer improved performance, increased torsional capacity, and improved hydraulics, and have created slimmer profiles. Additionally, running and handling characteristics have been improved, providing faster makeup, reduced trip time, and decreased repair cost because of reduced connection damage.
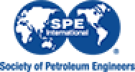