Progressing cavity (PC) pumps have been around too long to be a young technology, but it is still an emerging one.
The history of this rapidly growing form of artificial lift is a study in how a community of users can continue to find ways to adapt a seemingly simple machine that can have a complicated relationship with a reservoir. What started as a better option for pumping cold, heavy, sandy crude in Canada has been adapted for high-volume production of heavy crude in Venezuela, for lifting medium-weight oil mixed with things that other pumps cannot handle well, and pumping water out of Australian coal seams to initiate natural gas production from the thousands of wells in the huge deposits.

All-metal versions are beginning to appear in heavy oil fields, after a decade of development and testing to prove they could work at temperatures far beyond what standard PC pumps could handle.
Pushing the capabilities of these pumps, which cannot reliably handle light oil, will require a new generation of elastomers. This will likely require oil and gas industry users to push chemical makers to develop elastomers with capabilities that go beyond the needs of their biggest customers, auto parts makers who use them for tires and other car components.
Several companies recently have begun trying to persuade users to turn to PC pumps powered by permanent magnetic motors downhole rather than relying on rotating rods powered by surface units. The advocates of downhole power, which has been a small part of the business, say it can allow more effective PC pump use and reduce tubing damage caused by long rod strings, which can also come apart.
Innovative new pumps are appearing, with some using the usual materials in surprising ways.
“The manufacturing of PC pumps is growing and I think everybody is trying to push the envelope a lot now,” said Shane Latoski, product manager of Oil Lift Technology, which is part of Dover Corporations’ Norris Production Solutions operation. “There are some interesting things coming through.”
The company is in the middle of a rapidly growing business—PC pump makers are also benefiting from the strong sales of mud motors, which are the different use of the original design. The growth of the PC pump business is an example of the value of adaptive reuse.
While emerging technologies are associated with scientific breakthroughs, mature businesses can find and profit from emerging opportunities that grow out of their normal business, said Pradeep Anand, president of Seeta Resources, a business consultant who has advised companies seeking such opportunities.
Cheap, Difficult, Messy Jobs
The main priority for Lonnie Dunn, global product line engineering manager at Weatherford, is “looking for places where it (a PC pump) is a natural fit and adapting it.”
That is a good description of how PC pumps became a fixture in oil production, and a test for new ideas hitting the market. What has been a natural fit for PC pumps has been a reflection of a machine with a distinct personality. PC pumps are a low-cost workhorse capable of doing difficult, often dirty jobs that other pumps cannot do.
These pumps look like simple machines. The basic design has a single moving part: A rotor pushes fluids through a series of cavities defined by an enclosure called the stator. To work well, the machine needs to be surrounded by a large body of knowledge. Predicting how a PC pump will perform in a well can be tricky because of the complex relationship between the metal rotor and the elastomer stator, which can swell, shrink, harden, blister, fall apart, and separate from its steel housing.
Even small changes in the stator can affect the ability of the helix-shaped rotor to efficiently displace fluids through a series of chambers. For it to work well, the stator must fit like a glove over the rotor. Too loose and it loses efficiency. Too tight and it can shut the pump down or damage the elastomer.
“It is like a ‘living thing’ that we are trying to engineer,” said Shauna Noonan, completion technology manager at Conoco-Phillips. “The elastomer on the inside changes shape and dimension with temperature, fluid, and gas exposure, etc., so it is very difficult to predict what the final pumping capacity and torque requirements are when it is placed in a well.”
Wide variations in the life span of similar pumps in nearby wells can reflect the well design: pump size and capacity, the elastomers used, and the way it is run.
The need for experts was recognized in the 1980s in western Canada. Companies plagued by erratic PC pump performance created an industry group to find ways to improve it in conjunction with C-FER Technologies, the research and testing organization in Edmonton that has long been a technology center for PC pumps.
“We worked with 10 to 12 companies that shared data. They worked through their problems,” said Cam Matthews, director of new technology ventures at C-FER. “It led to a course and other training opportunities at the time.” The group has grown to 35 operators and service companies covering a growing range of PC pump applications.
Recent additions include Australian companies that have begun working with C-FER, which has a tracking system looking for useful patterns in the activity of pumps, to help diagnose the root cause of pump failures or explain differences in pump performance.
Researchers are trying to develop computer simulations able to predict how PC pumps will behave in the ground. There is a growing body of data to guide decisions about pump use, but the judgment of experienced users remains key.
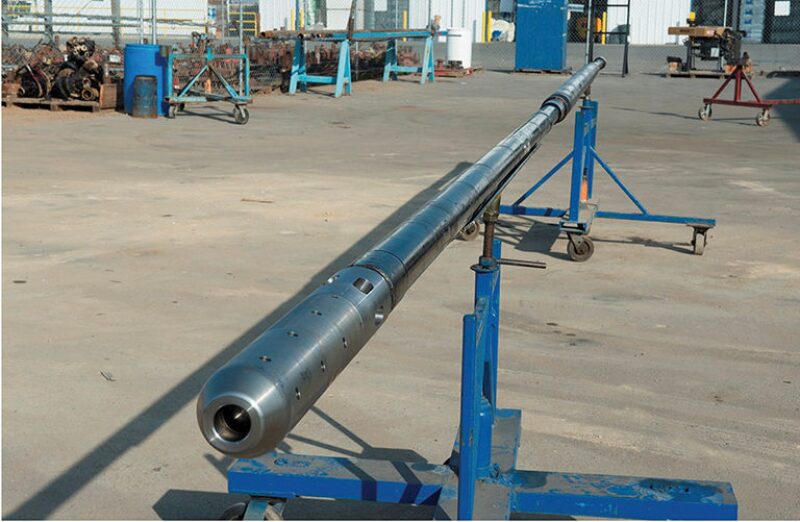
The big challenge PCPs face when moving into a new field or a new country is lack of resident knowledge,” Matthews said. The pumps are often tried in a pilot and deemed a failure, but may have succeeded if the operator understood the technology better, he added.
Slow-Motion Pump Jacks
Progressing cavity pumps were born in 1930 when French inventor René Moineau patented a pump design that was a byproduct of his search for a better compressor. It was the first of many adaptations of a machine that is the basis for pumps used to get heavy oil out of reservoirs, and is the basis for mud motors that power directional drilling units. In the decades after it went into production, it was tried in oil wells, but was mainly used by other industries, such as food processers and chemical makers, to pump steady streams of viscous, lumpy, or abrasive materials.
The evolutionary tree for most PC pump use now goes back to the 1970s, when Canadian companies saw the pumps used to pump heavy oil from shallow wells in California and saw it as a better way to lift oil from the Lloydminster area, where billions of barrels of crude were found in cold (10°C–20°C), shallow, low-pressure reservoirs where crude was mixed with a lot of sand. Oil in these Alberta fields was so thick that the down stroke of pump jacks moved in slow motion, as did the production, and the abrasive oil shortened the life of the pumps downhole.
Changes were required to make PC pumps work in an oil well. The imported pumps were underpowered, so longer pumps were improvised—a PC pumps lift is a function of the number of cavities inside—driven by upgraded surface units. The pumps rotated the wrong way. The counterclockwise spin could disconnect long rod strings to the surface that powered the pumps.
Use of the pumps grew slowly, delayed by the downturn of oil prices in the 1980s and 1990s. Its use eventually spread to Venezuela and elsewhere in South America, where the pumps and rod strings grew larger to handle the high output flows from enormous fields such as the Orinoco. To protect those large assets, operators have added elaborate instrumentation to track their performance.
PC pumps were adapted to fields producing medium-weight crude, where the capacity and presence of sand made them a good fit. That required advances in elastomers to go from cold, heavy oil, which is nearly inert, to warmer, lower-weight grades that can chemically react with them and affect performance.
The low cost of PC pumps and their ability to handle water made them a good choice for pumping water out of coal seams in the United States, and then in Australia, a booming market with around 3,000 PC pumps in use, growing to 10,000 based on planned growth in coal seam gas production, Dunn said.
The pumps had to be adapted to handle a warmer reservoir and pump water, which does not lubricate like oil. More adaptation will be required. High labor costs have made it a priority to have well designs that allow changes with a minimum of surface equipment and time. Experience has revealed a new problem: powder-fine sand mixed with fluid forms a gluelike paste that can plug a pump during shutdown, Noonan said.
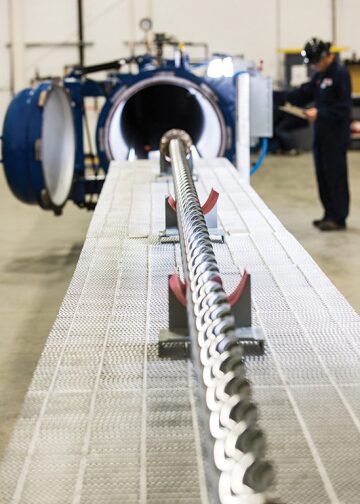
There is huge potential in the Eastern Hemisphere, where countries such as Kuwait and Oman are concentrating on developing heavy oil reserves that are well suited for PC pumps, said Dunn.
Materials Progress
The future of PC pumps and other oilfield equipment depends on the development of high-performance materials. PC pump performance relies on the capabilities of the base polymers used to make elastomers. “The base polymers are supplied by the rubber industry and it is focused on the needs of tire manufacturers,” said Noonan, an SPE technical director who cochaired the recent SPE Progressing Cavity Pumps Conference in Calgary.
There was talk among conference participants about the need for an organized effort within the oil industry to work with makers of base chemicals to create new elastomers for exploration and production. There have been signs of increasing interest on the chemical supplier side since the 2008 recession hurt the auto industry, depressing demand by tire makers, Dunn said.
Metal-on-metal pumps have a niche in high-temperature wells or in some with oil mixed with highly corrosive chemicals. A testing program paid for by ConocoPhillips and performed by C-FER validated that these pumps could run reliably in wells with temperatures up to 250°C (482°F).

The largest maker of metal-on-metal systems, PCM, has sold 320 of them worldwide, and others are showing an interest in the business. “It (PC pump) is useful because it can pump a wide range of things—crude, steam, water, gas,” said Laurent Seince, an oil and gas business development manager at PCM.
But pumps using elastomers are likely to remain the dominant option, because metal stators cost many times more and elastomers stand up better to abrasive fluids.
Others are trying ceramic parts in the pumps and switching the normal order of things in PC pumps, with a rotor made of elastomer, rather than steel, and the stator made of steel, Noonan said. The concept is so new that she would not venture a guess as to the creator’s intentions, but it might be a way to move the material most likely to fail—the elastomer—to a part that can be replaced without pulling the rest.
Rodless from Russia
Recently there has been an uptick in talk about powering PC pumps with downhole motors built around permanent magnets. The combination of PC pumps and permanent magnet motors has long been used in Russia, where users favor downhole power units as strongly as Canadians do rod drives.
There are about 250 PC pumps powered by permanent magnet motors in Russia, said Ken Saveth, senior adviser of ESP design at Borets, a major maker of permanent magnet and electric submersible pump (ESP) motors in Russia. The company has moved into the North American market and is working to convince operators of the advantages of “getting away from rods altogether” for PC pumps and ESP, he said.
The argument for change is that more wells are now drilled horizontally, and rotating rods bending along those curving paths come into contact with tubing and can cause costly damage. “If you have a deviated or a horizontal well, if you run a drive shaft through a curve, it tends to weaken or create holes in the tubing,” Saveth said.
Making the permanent magnet systems work is an engineering challenge. The companies promoting permanent magnet motors say they are a better match for PC pumps than the electric motors used for ESPs, because they rotate at nearly the same speed as the PC pumps, while the induction motors used for ESPs run many times faster.
Still, the ideal speed for the permanent magnet motor is higher than the pump. One company, Zilift is selling a torque converter using permanent magnets rather than gears that smoothly syncs machines running at different rates. The company’s investor list includes the venture capital investment arms of Chevron and Saudi Aramco.
Zilift has done one successful test in a heavy oil field in Bakersfield, California, and is working with operators to do others, said Mike Rushby, project manager at Zilift. He said the slim pumps can be installed in tubing as small as 4.5 in. The potential advantages are avoiding the cost of damage rods can cause, reduced energy consumption, and eliminating the impact of a surface unit to rotate the rod drive.

“The economics are there simply by removing the failure modes associated with the rods,” he said. “Add to that increased total recovery by placing the pump exactly where you want it and that is powerful.”
Others are not convinced downhole power units will catch on in a big way. “If you take a low-cost pump and add a transformer, a power cable, and a downhole motor, it is not a low-cost system anymore,” Dunn said. He does see applications in which the fluids pumped would make a PC pump preferable to an ESP, but they are limited.
Rushby said that while the upfront cost of a downhole power system is higher, the lifetime cost comparison is favorable because of the reduced expense related to tube damage, and lower energy cost.
Users of rod drives say the cost of rod damage has been exaggerated, because there are ways to avoid it. Pumps are often located in the vertical section of wells that have a lateral. Rods run through curved pipe sections can be held away from casing walls with centralizers, protective coating can be added inside the tubing, or continuous rods can be used that do not have connections that can wear on pipes. In places with thick oil and low levels of sand, the oil may provide enough lubrication to limit damage.
At the recent SPE PC pump conference, presenters with Zilift and other companies with permanent magnet motor powered equipment were peppered with detailed questions.
Those trying to change the habits of experienced users, who have experience with downhole motors, will need to build a body of evidence to make their case to those whose long experience gives them reasons to think it will not perform better than rod drive.
Over time, with adaptation, downhole induction motor and permanent magnetic motors might find a larger place in the PC pump business, Noonan said.
Moving Into Hot Spots
The decadelong process required to sell all-metal progressing cavity pumps shows how hard it can be to convince operators that a truly new design will work in a well.
An important step along the way was a testing program created in 2008 by ConocoPhillips to validate pumps could operate at temperatures of up to 250˚C (482˚F). That is at the high end of what they would ever encounter in oil sand wells where steam-assisted gravity drainage (SAGD) is used to extract ultraheavy crude oil.
Those conditions demanded new pump designs, because the elastomers normally found in PC pumps perform poorly at high temperatures.
PCM and Robins and Meyers Energy Services, which is part of National Oilwell Varco, created all-metal versions of the pumps. Each developed a proprietary metal forming method to precisely shape high-performance steel into the complex, curving shapes needed to closely follow the helical outline of the rotors, with tolerances measured in thousandths of an inch.
While each company had certified its product to run at high temperatures, ConocoPhillips paid C-FER Technologies, a large research and testing center in Calgary, to create a test loop allowing it to simulate pumping oil in a steam-heated field.
The C-FER test required pumping fluids in a test loop with temperatures up to 250°C, with fluctuations of 100°C and occasional starts and stops, which can lead to pump breakdowns. Sensors in the loop allowed detailed observations during tests lasting 3 to 6 weeks, and afterward, the equipment was cut apart and examined for signs of wear.

It was a tough test and it led to changes. “Everyone failed the first time around, because they did not understand the conditions,” said Shauna Noonan, completions technology manager at ConocoPhillips, who led the testing program. In the second round, multiple suppliers passed with suggested improvements, which were incorporated and in some cases led to a third round of tests.
The program is completed, and sales of all-metal pumps are small, but growing. Laurent Seince, an oil and gas business development manager at PCM, said new clients are being added in North America and the Middle East and others are targeting the market.
One company developing a metal-on-metal PC pump is Oil Lift Technology, which is in the middle of an expansion program. The company, which is known for making surface components such as top drives for the rod systems, has opened a new factory. It is making PC pumps and working on developing an all-metal model.
“Metal-to-metal is a niche market, but an important one,” said Shane Latoski, a product manager at Oil Lift Technology.
For Further Reading
SPE 165469 Field Trial Results of an Innovative Heavy Oil Production System by M.J. Rushby, R. McCann, and A. McAleese, Zilift.
SPE 165654 Case Histories of Running Progressing Cavity Pumps With Submersible Permanent Magnet Motors by K.J. Saveth, Borets-Weatherford.
SPE 153944 Pressure Distribution in Progressing Cavity Pumps: Test Results and Implications for Performance and Run Life by Evan Noble and Lonnie Dunn, Weatherford.
SPE 117493 Quest to Validate and Define Performance for the High Volume Metallic Stator PCP at 250°C by S.G. Noonan, ConocoPhillips; W. Klaczek; K. Piers, C-FER Technologies; L. Seince, PCM, et al.
SPE 117521 The Progressing Cavity Pump Operating Envelope: You Cannot Expand What You Don’t Understand by S.G. Noonan, ConocoPhillips.