Many freshly graduated engineers are unsure of how to apply futuristic innovations to the oil and gas industry. They perceive the industry to be unstable, even unsustainable, in the midst of climate change concerns. Questions surrounding the longevity of the industry are increasing as cleaner energy alternatives become increasingly available and economically viable. In today’s world, many young scientists and engineers choose to focus on solutions that have lower carbon footprints and a more certain future.
The risk of the oil and gas industry completely disappearing in the near future is exaggerated. However, if the industry does not adapt and evolve with changing technologies, specific sectors of the industry may decline. For young engineers, it is critical to understand the challenges the industry will face over the next several decades to create the drive and come up with solutions the industry greatly requires.
In these times of great change, the oil and gas industry is actively and transparently addressing the social and environmental stigma surrounding it. For example, the are several initiatives in the industry toward a better and more environmental friendly approaches for the core businesses. (Ma Jingyuan et al., 2022). Major oil companies in the world have also started investing some of their resources in the renewable energy sector, and others are transitioning from being oil companies to energy companies. The push toward a greener world, in the eyes of young professionals, does not only rely on the idea that it is safer for the environment. It also relies on the realization that many of the core technologies and methods used in the oil and gas industry are very mature and have aged to the point of being nearly obsolete and not nearly as technologically appealing as they used to be.
New Generation of Inventors
As a young professional, I find that other young engineers want to apply new alternatives instead of modifying currently available systems. This gives us a greater sense of accomplishment and provides modernized solutions to long-lasting problems. Most oil and gas innovations nowadays are incremental advances to inventions made from mid-1980s to late-1990s (Edmundson, 2022). However, systems could become lighter, faster, cheaper, and be specifically manufactured for future modifications as required. Thus, this industry is a potential venue for young engineers and researchers to play a crucial role in adopting new technologies and obtaining hands-on skills in mastering modern technology creation and deployment.
Openness to continuous learning, acquiring a digital-thinking mindset, having domain knowledge, and data analytics skills are essentials that will prepare newcomers for a faster career development journey. Acquiring a digital-thinking mindset means that once there is a good understanding of how sensors, machines, and code work, at a foundation level, young researchers will be able to gain better insight into solving problems. They will also interpret data in a better way to optimize operations and accelerate deployment of new technologies in the field.
Oil and Gas Operational Digitalization in Practice
The future of oil and gas technologies seems promising and full of opportunities from a young professional’s perspective. The floor is wide open for new inventions that can perform tasks in a more disruptive way to significantly optimize operations.
Engineering has developed substantially over the past decades. The fields of mechanical, electrical, software, and petroleum engineering have developed together, and separately, in such a way that a combination of two or more of those fields have become new fields by themselves. Mechanical and electrical engineering have combined into different fields such as mechatronics, robotics, and micro-electro-mechanical systems. Petroleum and software engineering have combined into fields such as petroleum energy analytics. Many other science and engineering fields will emerge and join in time to support the digitalization initiative. This enormous step toward digitalization needs more manpower. Therefore, there will be more opportunities for young technologically minded engineers to test their skills and aptitude in the oil and gas industry.
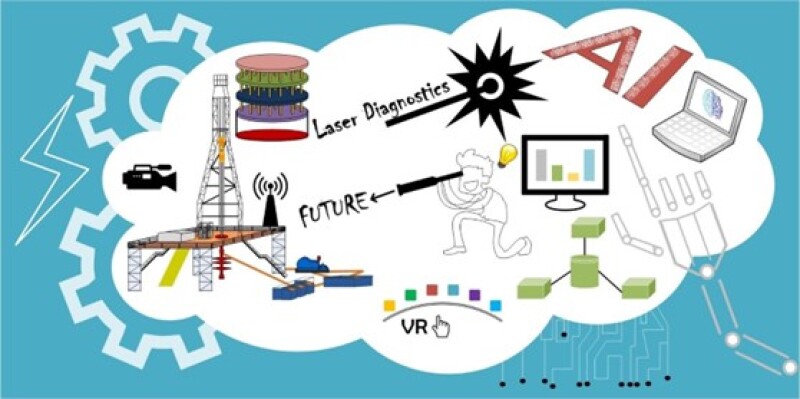
This transformation will decrease expenditures in rig/platform operation time, labor hours, human error, tool life, and resources utilized. For example, in the preoperational stage of drilling, machine learning, sensors, robotics as well as spectroscopy and laser diagnostics could be used in assessing and studying the well and its corresponding formations to better optimize drilling. Educated predictions will allow engineers to have a better judgment while working, which can save the industry expenses and increase revenue.
Machine learning can optimize operations and make them less prone to errors. Robotics will be used in operations that are difficult for humans to execute with precision, in difficult-to-reach areas inside the wellbore and at high elevations. The field of spectroscopy and laser diagnostics can be used to measure concentration, temperature, pressure, and other fluid flow properties. This field will play a strong role in modernizing the operations. Remote sensing, process control, dynamic diagnostics, and monitoring of environmental and downhole conditions are all applications of spectroscopy and laser diagnostics (Tsai and Gardner, 1982; Tubel et al., 2001).
During the operational stage of drilling a well, semi-automating the drilling process with advisory control could be achieved in the near future by using robotics, machine learning, Internet of Things, and micro-electromechanical and nano-electromechanical (MEMS/NEMS) technologies. The MEMS/NEMS technologies are already being used in electronics-based devices such as measurement-while-drilling and logging-while-drilling (Liu and Li, 2008). Majority of sensors that are currently being used in drilling operations could be replaced by MEMS/NEMS sensors. They are light-weight, compressed in size, acquire high-reliability rates, and are also very energy efficient (George, 2003). The energy harvesting world along with MEMS/NEMS technologies will revolutionize how downhole sensors acquire energy. The compact size of the technology means that it has fewer moving parts, which makes it reliable under shocks and vibrations and in harsh environments (Miller and Erdos, 2018).
In post-drilling operations, data collected before and during a drilling job could be used in further assessments of the same drilled well, or similar nearby wells and future jobs (Aljubran et al. 2021, Gurina et al. 2022, and Koulidis et al. 2021). Machine learning and artificial intelligence can help in training models to optimize other wells. These technologies can also transform data collection as well as automate data cleansing and imputation, making the process easier for acquiring real-time drilling-related data.
Augmented reality will allow for better simulation of the borehole environment (Lee et al., 2015), which in return will help engineers in making better decisions due to better downhole representation. Lasers could be used in many different applications in the field. Further advances in both using lasers as sensors for new measurements as well as applications for communicating data are very promising in enhancing operations in terms of cost, efficiency, and quality (Soroush et al. 2022).
The use of advanced materials will also play a significant role in the digitalization journey. Advanced materials will enhance the capabilities of tools used in terms of their durability and longevity (Behera, 2022). It will also open new doors for downhole to surface communication using specific types of materials that allow internal communication, such as optical fibers in fiber-optic communication (Edouard et al., 2022). Utilizing advanced materials as well as advanced manufacturing processes such as additive manufacturing (3D printing) will expedite and simplify the process of downhole tools manufacturing (Sireesha et al., 2018).
Vision for a More Connected, Digitalized Upstream Sector
The key element in the success of the upstream sector is efficient and accurate internal communication between its different entities. From the early stages of exploration to the later stages of production, continuous data transfer and communication needs to be maintained. Digitalization will help ensure that this is carried out in an efficient and accurate way.
During the exploration part of the process, geophysicists start by deducing the existence, location, and mass of hydrocarbons. Data collected and information produced get transferred to a geologist to explore the long-term reserve restoration and the geological factors that would affect the exploration job. Drilling then takes the findings to confirm the prospective reservoir and to delineate and expand fields for long-term development. Once a well is drilled and completed, production comes into place and ensures maximum recovery of hydrocarbons. The information gathered in each step of the process needs to be precise and delivered in a very timely manner. Digitalization of all entities within the upstream sector will make the connection easier, faster, safer, and more reliable (Fig. 2).
Digitalization will not only improve the connection between different upstream entities, it will also develop each entity’s work structure in itself. For example, electric submersible pump (ESP) failures can be monitored and compensated by digitalization. Communication between nearby ESPs will allow for peer-diagnostics and performance compensation to happen in certain failure scenarios. Performance compensation between nearby ESPs will affect the reservoir’s precalculations. This in turn will affect the geologists’ and geophysicists’ calculations. The simple change at the end of the chain will require changes to be made in the first link. With digitalization, re-calibration for most efficient and optimized flow of hydrocarbons can be made. Geological and geophysical parameters will be autonomously changed. Propositions and additional fixes can be gathered and assessed from different entities rather than just production, in this case. The parts of the chain will get linked together to form a continuous circular chain.
The goal of digitalized innovations is to cut costs, increase efficiency of operations, have better access to hydrocarbon resources, and acquire solutions to common and costly challenges. With all these compelling drivers toward achieving digitalization and automation, young engineers and researchers really do have the opportunity to change the world. If the oil and gas industry can facilitate some of that ingenuity to trickle into the world of oil and gas, the industry will not only thrive, but will also open doors to new pathways that have not been thought of yet.
References
Aljubran, M., Ramasamy, J., Albassam, M. et al. 2021. Deep Learning and Time-Series Analysis for the Early Detection of Lost Circulation Incidents During Drilling Operations, IEEE Access, 9, pp. 76833–76846.
Behera, A. 2022. Advanced Plastic Materials. Adv. Mat., Springer, Cham.
Edouard, M.N., Okere, C.J., Dong, P. et al. 2022. Application of fiber optics in oil and gas field development—a review. Arab J. Geosci., 15, 539.
Edmundson, H., 2019. Ten Technologies From the 1980s and 1990s That Made Today’s Oil and Gas Industry. J. Pet. Technol. 71(03).
George, T., 2003. Overview of MEMS/NEMS technology development for space applications at NASA/JPL. Smart Sensors, Actuators, and MEMS, 5116, pp. 136–148.
Gurina, E., Klyuchnikov, N., Antipova, K. et al. 2022. Forecasting the abnormal events at well drilling with machine learning. Appl. Intel. 52, pp. 9980–9995.
Koulidis, A., Abdullatif, M., Abdel-Kader, A. G., et al. 2021. Field Assessment of Camera Based Drilling Dynamics. Paper presented at the SPE Middle East Oil & Gas Show and Conference, event canceled, November 2021.
Liu, C. and Li, J. 2008. Measurement-while-drilling (MWD) telemetry by wireless MEMS radio units. US Patent Application 11/684,386.
Jingyuan, M., Boru, X., and Yuxiu, An. 2022. Advanced developments in low-toxic and environmentally friendly shale inhibitor: A review. J. Pet, Sci. Eng., 208, Part C, 109578.
Miller, K. and Erdos, D. 2018. Technology Update: The Dawn of MEMS Sensors for Directional Drilling. Journal Pet. Technol, 70(05), pp.18–19.
Lee, S., Suh, J., and Park, H.D. 2015. BoreholeAR: A mobile tablet application for effective borehole database visualization using an augmented reality technology. Comp. & Geosci., 76, pp. 41–49.
Sireesha, M., Lee, J., Kiran, A.S.K., et al. 2018. A review on additive manufacturing and its way into the oil and gas industry. RSC Adv., 8(40), pp. 22460–22468.
Soroush, M., Mohammadtabar, M., Roostaei, M. et al. 2022. Downhole Monitoring Using Distributed Acoustic Sensing: Fundamentals and Two Decades Deployment in Oil and Gas Industries. Paper presented at the SPE Conference at Oman Petroleum & Energy Show, Muscat, Oman, March.
Tsai, B.M. and Gardner, C.S. 1982. Remote sensing of sea state using laser altimeters. Applied optics, 21(21), pp. 3932–3940.
Tubel, P.S., Williams, G., Johnson, M.H., et al. 2001. Monitoring of downhole parameters and tools utilizing fiber optics. US Patent 6,281,489.