A North Sea field development included installation of long 4½-in. completion liners in the horizontal reservoir sections of each well. To minimize overall risk, the operator planned to use managed-pressure drilling (MPD). Despite the expected positive effects of MPD, a strong understanding of the downhole dynamics during deployment of the lower-completion liner was needed. To address this challenge, the operator installed a newly developed work-string-dynamics logging tool directly above the liner-hanger-running tools.
Logging-Tool Technology Overview
The logging tool is a compact and robust memory-based surveillance tool made for drillpipe-conveyed well operations.
×
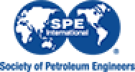
Continue Reading with SPE Membership
SPE Members: Please sign in at the top of the page for access to this member-exclusive content. If you are not a member and you find JPT content valuable, we encourage you to become a part of the SPE member community to gain full access.