After a well has produced its last oil and gas, it must be plugged and abandoned (P&A). The phrase suggests it will remain sealed forever. “What we want when we abandon a well is we never want to come back to it,” said Don Stelling, president of Chevron Environmental Management Company. Compared with the 30- to 40-year life expected of most facilities, “it is a difficult engineering standard.”
And it will be getting more difficult. The wells of the future include many in stormy seas and deep water, magnifying the cost of what the United States Bureau of Safety and Environmental Enforcement (BSEE) describes on its website as “safely plugging the hole in the Earth’s crust.”
Estimating the scale of this work is a highly inexact exercise. There are many interdependent variables affecting cost and demand.
Based on the wells that will someday need to be decommissioned, the value of the market could exceed USD 250 billion using current methods, said Martial Burguieres, vice president of marine well services for Wild Well Control, which does plugging and abandonment work. Actual demand will depend on what operators can afford and regulators require.
One sure thing is that the number of wells needing to be permanently plugged will continue to rise.
“As long as they are drilling new wells. The backlog of wells to be plugged and abandoned is humongous,” said Bart Joppe, global business development manager for plug and abandonment at Baker Hughes.
A key variable in the volume of work done is the cost per well. P&A work is the most expensive component when shutting down an offshore field. Reducing that expense is critical in places where oil companies are experiencing decommissioning price shock, such as the North Sea or offshore California, and in the deep waters of the US Gulf of Mexico.
“P&A is a massive problem. There are huge cost overruns,” said Brian Twomey, managing director of Reverse Engineering Services, which offers decommissioning advice and classes.
Plugging Without a Rig or Riser
Permanently plugging wells requires installing barriers in multiple spaces. Wellheads allow relatively easy access to production casing, but getting into the tight spaces in the surrounding annulars is a costly challenge when plugging and abandoning wells.
Wild Well Control has created a set of tools to reach those zones and set plugs without the expense of a drilling rig and riser. These diagrams highlight key steps after it has temporarily abandoned the well by installing two plugs to isolate the production zone, adding kill-weight fluid, and pulling 1,000 ft of production casing.
![]() |
![]() |
![]() |
![]() |
![]() |
![]() |
Changing Rules
Operators are also having to adapt to changing rules over the past 5 years in Norway, the United Kingdom and the US. “Regulation is becoming more stringent and the volume of work is going up,” Joppe said. “We have seen customers screaming over large increases in costs and in the volume of work. We have definitely gotten more requests for new technology.”
At the top of the technology wish list are ways to work on wells without paying for a drilling rig and riser, and tools capable of dependably doing jobs faster because even the “lighter” intervention vessels command hefty day rates. There is also more attention paid to the materials used to create lasting barriers to ensure wells never leak, because the cost of going back to fix a leaking deepwater well is punishingly high. (See sidebar on well cementing.)
Without new methods to reduce the cost, the expense of plugging and abandoning difficult wells offers a strong argument for postponing the work.
“A lot of operators will not admit it, but there is nothing in the budget to provide money for these wells” at current prices, which are both high and hard to predict, Burguieres said. “Drilling rigs should be drilling. We can handle this.”
That assertion will be tested in the Gulf of Mexico, which is a proving ground for new deepwater removal approaches. The BSEE’s “idle iron” rule sets a deadline requiring that inactive wells be plugged and production equipment be removed.
This fall, work began on removing the Red Hawk spar. Located in 5,000 ft of water, the platform is the first permanent floating structure removed from the Gulf of Mexico. The short-lived gas field, which was acquired by Anadarko when it bought Kerr-McGee, has been inactive since 2008.
Next year, Wild Well Control is planning to plug nine nonproducing wells in 7,000 ft of water in the first use of its new equipment that does not require a drilling rig or riser. The system uses equipment lowered to subsea wells using a wireline and coiled tubing to deliver the fluids and cement to plug the central casing and up to two surrounding annuli. The cost is expected to be about USD 14 million per well while options using drilling rigs and risers would run three to four times higher.
Wild Well’s subsea plugging method grew out of its experience off Angola, where the relatively shallow water allowed divers to assist.
This represents a tangible example of what is described as the future of deep water well work, and one a lot of people are watching because it represents a technological leap. At the time of the interview, he said the record for wireline well work was 6,000 ft.
While rigless P&A is the norm for shallow-water plugging, where most of the wells can be reached from a dry tree on a platform, doing the same work on a subsea well where the production control equipment is on the seafloor is an emerging technology. Decommissioning practices are relying on methods developed for the larger business of maintaining producing wells.
In the North Sea, drilling rigs and risers are pulling out all the steel in some wells to allow placement of cement plugs running from rock to rock with nothing in between. It is costly, but when it comes to plugging, there are significant long-term costs to consider as well.
“Deep water is a completely different animal,” Burguieres said. The added financial and reputational risk of a botched job in deep water increases the pressure to be sure that a deepwater well is “really, really dead,” he said.
Deep Problems
While new ways of doing things are often a hard sell, there is a strong financial wind pushing innovation in plugging and abandonment, which represents from 40% to 50% of the total cost of decommissioning.
In the North Sea, cost estimates keep rising as more jobs are done. The annual Decommissioning Insight survey by the industry group Oil and Gas UK found that the average cost of plugging and abandoning a subsea exploration well there nearly doubled to USD 27.5 million in 2014, compared with the average in 2013. Development well plugging costs averaged 14% more in the latest survey.
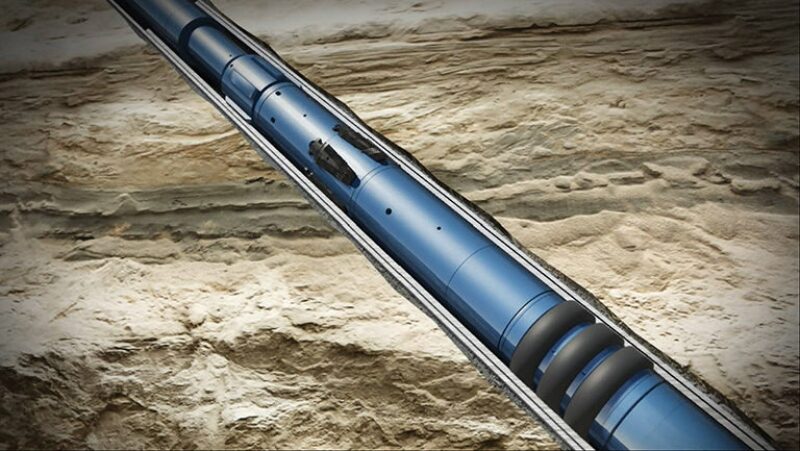
But the rising cost provides a motivation for change in the way jobs are done, which is in part a regulatory issue, and the methods used to do the work. “Decommissioning provides a great opportunity,” said Adam Davey, economics and market intelligence manager for Oil and Gas UK. It is early-in-the-cycle, well-removal work and with advances “we can knock billions off our decommissioning bill.”
While wells in the North Sea are on the continental shelf, they share many of the challenges found in deep water. They are often in relatively deep water with subsea hardware that can be hard to get past and plug.
There are majors in the North Sea doing rock-to-rock plugging. It is like a dentist drilling out the remains of a broken filling before replacing it.
“Shell is using rock-to-rock abandonment in the Brent field in the North Sea,” Twomey of Reverse Engineering said. “They go in, cut out all the casing, and put in a cement plug or epoxy plug. They span bedrock to bedrock after they have milled out the casing. I cannot argue it is the most secure way to do it. The question is: Is that needed? The expense can be quite high.”
In the Gulf of Mexico, the goal is to limit casing removal, Joppe said.
“We do as little deconstruction as possible,” Burguieres said. “You spend millions on casing. It is not permeable. It helps you on well control issues. Why would you mill up strings of casing?”
One answer to that rhetorical question is regulations requiring well owners to verify that every space is sealed within a well. The complicated well designs required for difficult-to-drill deepwater fields can create multiple isolated spaces to plug, such as constricted annuli or spaces inside casing shoes.
Regulators in Norway require that every possible leak path be cemented in plugged zones. But verifying that is a problem because currently there is often no way to see through multiple casing strings to verify if seals are present, or spot flaws, said John Hand, a technology program manager for ConocoPhillips. Getting past multiple layers of pipe is also a barrier, leading to steel removal.
For ConocoPhillips, which operates the largest field in the Norwegian North Sea, Ekofisk, postponing permanent plugging is not an option. Flooding in the aging chalk formations has caused the rock to compact, leading to subsidence. That has lowered the seabed by 9 m in places, causing subsurface shifts that has sheared some casing and bent others so much that it has blocked access to sections of the well.
The company has 100 active wells in a reservoir with 250 wellbores, and an active program to plug and abandon the wells. “As soon as we shut a well in we try to P&A it right away,” Hand said. “What we found is with the subsurface so active, the longer we leave it, the more difficult and expensive it gets.”
Deep Well Designs Create Complex Plugging Puzzles
One indication of how hard it can be to drill a deepwater well in the Gulf of Mexico is the multiple strings of casing required when dealing with narrow pressure margins. The complicated designs have multiple telescoping strings of casing, each narrower than the last, which are needed to shore up rock in spots where there is a narrow margin between the pressure needed to control the well and the level where it causes fluid loss and formation damage.
That solution can leave costly problems when it is time to plug and abandon those wells. A Bureau of Safety and Environmental Enforcement study on deepwater plugging said wells with subsea flow control equipment can increase the difficulty of getting into wells where a poorly maintained wellbore can add obstructions.
Those subsea trees are top of “wellheads without access fittings to all casing annulus sections,” said Bart Joppe, global business development manager for plug and abandonment at Baker Hughes. Getting into those spaces requires pulling casing or perforating into those zones and cementing them, he said.
In shallow water, wells are routinely plugged using intervention vessels that cost a fraction of the rate commanded by drilling rigs. The goal in deepwater is to do this work without a rig, but gaining access to those spaces, and inspecting them, are unsolved puzzles.
Wild Well Control has developed a rigless method to permanently plug a well with up to two annular spaces, which it plans to use next year to plug wells in the deep waters of the Gulf of Mexico.
Wild Well partnered with Oceaneering for its expertise in remotely dealing with subsea equipment, including balky subsea trees that have not been touched in years, said Martian Burguieres, vice president of Marine Well Services for Wild Well Control.
Rigless deepwater work requires a series of remotely controlled steps. A video of how this unique system is expected to do this job, is like watching a surgeon do arthroscopic heart surgery using a tool threaded through a vein. The whole job is expected to take about 22 days, but that could change.
To begin with, Wild Well will temporarily abandon the well by pumping in kill-weight fluid and setting two cement plugs to isolate the production zone. It has done this before by attaching a device on the wellhead that controls pressure and allows it to insert a series of tools into the well, called the 7 Series system.
All the fluids used in the job are delivered down coiled tubing. Flexible connections allow it the range of movement to compensate for the rise and fall of the intervention vessel above pumping the job.
The next step is so new it has not yet been named. The company has developed wireline tools that can be inserted into the well that can perforate into annular spaces around the main casing, flush them out, and pump in a cement barrier.
The carefully choreographed steps first employ a perforating gun to gain access to the bottom and top of the section to be plugged, which will significantly exceed the 200 ft minimum height required, Burguieres said.
Fluid is circulated to flush them out. Then epoxy resin is pumped, followed by cement for plugging. This is first done in the annular space adjacent to the production casing, and then the steps are repeated to plug the next annular.
After the outer areas are sealed, multiple cement plugs and mechanical barriers—a packer used in the job is plugged plus a metal plus is added—are used to seal the main casing, Burguieres said.
There are limits to what the tool can do. There are wells with more annular section than it can reach. Burguieres said Wild Well is working to find a way to plug more sections. It is also seeking ways to get past buildups of scale or paraffin that can block equipment on a wireline.
Clearing Out
While the industry works on rigless methods to permanently plug wells, pulling casing is the most direct way to create an unobstructed space for plugging, but the muscle required to do the job comes at a price. Since the diameter of the casing hanger is about 18¾ in. or greater, a mobile offshore drilling unit with a riser is probably going to be needed to pull it, Joppe said.
A Decom World industry survey listed more than a handful of reasons that would preclude rigless P&A work, including high pressure in the well, highly deviated wellbores, and a location where cement delivery is not practical.
It can be read as a list of technical challenges to solve for those in this sector. While rigless is considerably less costly than rigs, the day rates commanded by the intervention vessels capable of handling this equipment are sizable, no matter how it is done. That puts a premium on downhole tools that work faster and get the job done in one trip.
Those concerns shaped the design of Baker Hughes’ Harpoon cut and pull spear, which is built to lock tightly onto the casing walls to provide a strong, steady platform for cutting a pipe, and the gripping power needed to pull it out after it has been severed.
What distinguishes the Harpoon’s design is a locking mechanism requiring only a one-quarter turn to set it rather than more than 10 turns, making it easier to ensure it locks into place. The design also allows the tool to disconnect if it fails at one location, allowing it to be moved to another spot to try again.
Welltec has developed an array of electric line tools designed to push the limit of what can be done with tools that do not require a drilling rig or riser. It presented a case study at the 2014 Offshore Technology Conference about shearing a 5½-in. diameter pipe in about 3 hours of cutting time. Its goal is to do increasingly larger jobs, with a cutter now out that can do 7-in. pipe and it is working on one that can cut through the thick walls of 9⅝-in. diameter pipe, said Brian Sidle, marketing vice president for Welltec.
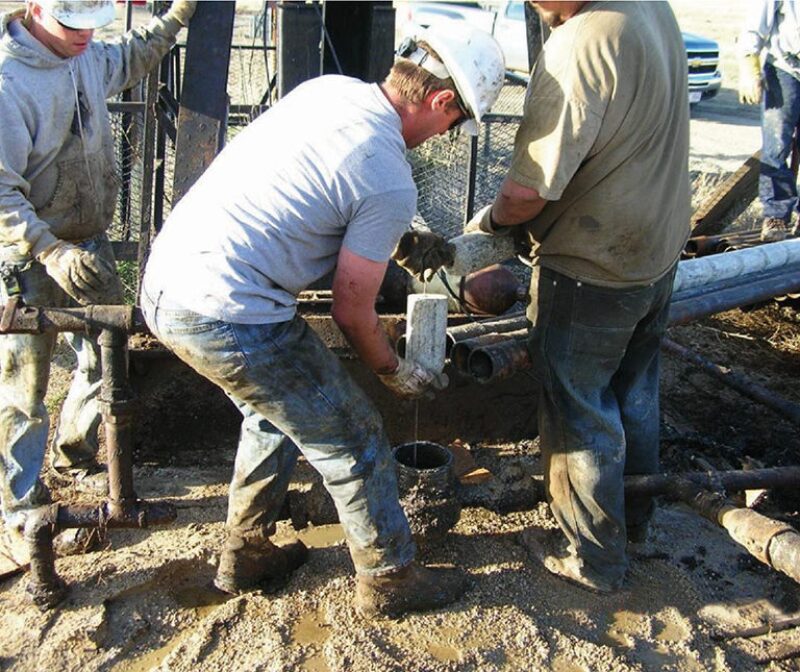
Plan B
Those working in remote places where only machines can travel need to plan for things that do not go as expected. Valves can be jammed, boreholes filled with sand, casing badly corroded, and hydrocarbons found in locations where they had never been noticed while drilling.
“When you drill through a formation that is not your primary target, you do not pay much attention to it. When it comes time for plugging and abandonment, it may not have been your production zone but you need to seal it,” Joppe said. “Secondary zones (containing hydrocarbons) can cause problems and leaking in the future.”
One of the features of Baker Hughes’ spear is a packer at one end to seal off the well above the cut if the cutting hits a pocket of gas. Welltec’s cutter is described as an “explosion-free mechanical cutter,” which is designed to not produce sparks while grinding pipe, producing fine cuttings that are not likely to cause problems. It is also designed to work on casing that has been compressed or pulled from a variety of sources, Sidle said.
Under US regulations, after a well has been plugged, the wellhead must be cut off 15 ft below the seafloor. International standards call for “total removal and a clear seabed,” Twomey said.
While those policies remove signs of the industry’s presence, and metal that might snag fishing nets, it also removes the wellhead designed to provide access if work is required. “If a well is to leak for any reason, you will never get back on top of it,” Burguieres said.
Rather than remove wellheads, he said, Wild Well has sought and received exceptions from regulators allowing it to leave wellheads in place on plugged wells. “There is no logical reason to cut” off the well, he said, adding that if there is a leak, “the only option is to drill a relief well.”
Cementing Alternatives Lack Critical Mass
The words plugging and cementing are used interchangeably. Regulations detail how cement should be used to plug oil and gas wells. Other materials are used with the approval of regulators, but not often. There does appear, however, to be more interest in alternatives.
“We are much more sensitive about cement quality than we were some years ago for a variety of reasons,” said Robert Byrd, vice president of consulting at TSB Offshore, who is working on a revised report on deepwater decommissioning technology for the United States Bureau of Safety and Environmental Enforcement (BSEE).
One of the motivations is the growing number of wells to plug in difficult locations, such as deep water, where the cost of fixing leaks is enormous. Another is the fallout from the Macondo blowout in 2010. The loss of lives and destruction it caused in the US Gulf of Mexico led to many changes in regulations, including ones concerning plugging and abandonment in the US and Europe.
Years before these questions were raised about cementing, Mike Cowan, a senior research fellow at the University of Texas at Austin (UT), was calling for better materials and methods for sealing wells. After three decades of work on building barriers to isolate, repair, and plug wells, he thinks the industry might be more open to reconsidering the materials and methods used to permanently seal wells. “They will (change), especially if regulators look at what it takes to have a good barrier. Cement alone is not a good barrier,” Cowan said.
During his time advising Shell Oil and Apache Corporation on how to isolate wellbores, he tested and used about every material that can be used to isolate a wellbore or plug a leak. They included monomers, which are clear liquids that can be injected into tight spaces and then harden into durable polymers for sealing cracks too small for cement to reach.
Based on his experience, cement has significant drawbacks: It does not adhere to rock or steel, it shrinks, and is brittle, all of which can lead to the risk of cracks and gaps that allow leaks. Other options offer advantages over cement, but none is a perfect replacement.
“One material will not do that. Cement will not do it alone. Resins will not do it alone. Combinations of those, most of the time, will do better,” Cowan said. For example, a steel bridge plug, followed by epoxy and then cement could be an effective combination.
Others are thinking along those lines. “I think we will see a trend where we are going to see barriers with multiple layers,” said Bart Joppe, global business development manager for plug and abandonment at Baker Hughes. “Rather than a single cement plug, you set a strong mechanical device below the cement, which is a good practice today, then cement and other materials with multiple layers with different characteristics on top.”
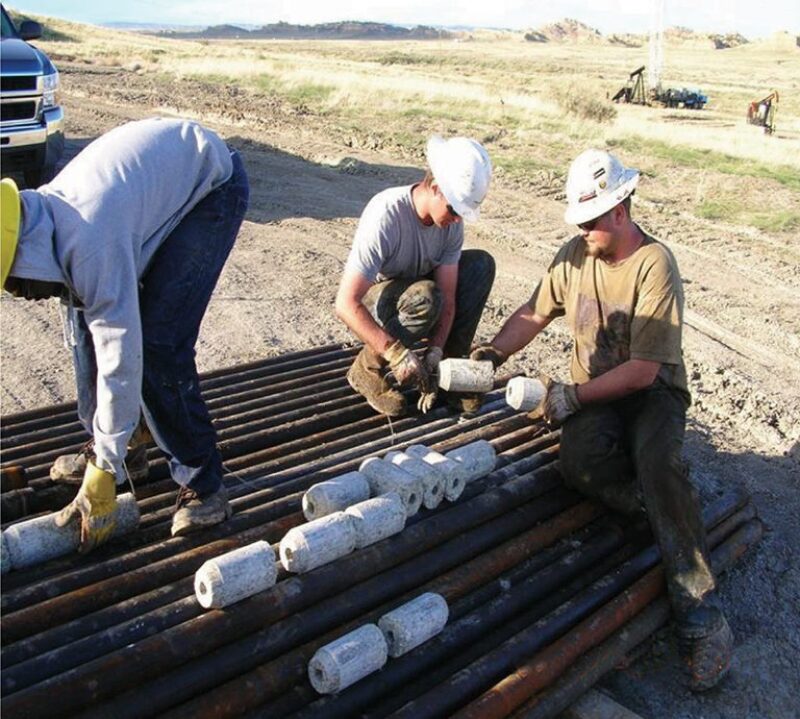
Performance Anxiety
The best way to ensure a good cement job is to carefully plan the job using materials suited for the need, carefully monitor how it is executed, and consider multiple tests because there is no one perfect test for cement quality.
In a talk titled “Cement Evaluation—A Risky Business” (SPE 170712) Glen Benge, a cementing consultant for Baker Hughes, laid out the limits of cement testing methods, none of which directly measures the quality of the barrier in place.
A pressure test does directly observe what a barrier needs to do, but it has its limits. “When we perform pressure testing, we are testing the entire well system. This includes the casing, and mechanical devices in that casing and any cement that is designed to establish a pressure barrier,” Benge said. “If the test is successful, we at least know that some of the components of the system are working, but do not know if all of them are functioning.”
Cement bond logs can assess the cement sheath around the wellbore by analyzing how sounds created by the logging tool are altered when echoing off pipe after cement has been pumped in behind the casing. A good bond should dampen the ringing sound a pipe would produce otherwise. These methods have grown increasingly sophisticated at identifying flaws by employing multiple sensors and ultrasonic sound to improve the data gathered, which is processed using improved algorithms.
Additives Change Cement Properties |
![]()
|
What they cannot do is directly observe the cement in the way an X-ray image can show a broken bone so a doctor can see what treatment is required.
When lighter cement is used, it can be hard to distinguish it from drilling fluid, which can compromise the cement evaluation. Advanced cement formulations appear differently on the log, requiring special calibration to get a good reading, Benge said during a presentation at the 2014 SPE Annual Technical Conference and Exhibition (ATCE) in Amsterdam.
Inspecting multiple layers of pipe and cement is another challenge. In a complex well there can be multiple casing strings set to the surface. Inspecting all of those using a cement bond long is a problem because “you do not have a (cement bond) log on Earth where you can do that,” he said.
The best option requires close attention to multiple performance measures: ensuring that the materials used are up to the job, using data gathering during the job to ensure it was done correctly, making sure all the measurement tools are calibrated accurately, and doing the math needed to properly evaluate the outcome.
Knowing the rock around the spot to be plugged can be critical. A paper analyzing the quality of cementing in 53 offshore wells (SPE 170667) done by two Schlumberger cement experts found that of the variables thought to contribute to better quality, the most telling was the characteristics of the rock next to the cement. The best is nearly impermeable rock, such as shale. A Canadian joint industry project done by the research organization C-FER looked at cement jobs in wells used to produce heavy oil using steam-assisted gravity drainage, and found that “geology rules” on the ultimate quality of the cement sheaf in sections above the production zone, said Cam Matthews, director of C-FER.
But detailed information on the rock in the upper zones is often limited because the attention during exploration and production was on the reservoir.
“If you do not have a good well record of the hard rock, how can you seal a well?” said Brian Twomey, managing director of Reverse Engineering Services. “This is not information you use for operations. It is a totally different game, making sure a well never leaks again.”
Barriers to Change
There are alternatives on the market. Cowan said there are service companies that are good at applying epoxy in the US and Norway, and others selling improved cement formulated to reduce cracking and shrinking.
An arm of Wild Well Control sells epoxy resin. Martial Burguieres, vice president of Marine Well Services for Wild Well Control, advises pumping resin ahead of cement because it resists cracking better than cement and adheres to surfaces inside wells. “It is an excellent material. It does not have the track record” of cement, he said.
Chevron uses alternatives and is looking for more, said Don Stelling, president of Chevron Environmental Management Company. It uses heavy drilling mud in between cement plugs. In California, the company has received approval from regulators to seal wells used for heavy oil production with compressed bentonite rather than cement.
“The benefit is that cement can crack and break down as the earth moves, a common California occurrence,” Stelling said. “The compressed bentonite actually continues to expand over time and creates a good seal. The downside is we have to pour it from the surface instead of pumping so only certain wells are applicable to this technology.”
For decades, bentonite has been used to plug water wells. That inspired Brian Towler, a professor at the University of Queensland, to use it in oil wells. To do so, he had to slow the tendency of bentonite to expand when moistened. The chips of bentonite used in shallow-water wells expanded before reaching the target depth in deeper oil well, leading him to compress the bentonite into a cylinder shape that expands after it reaches the correct depth. It has been used successfully in tests in US wells near the University of Wyoming, where he used to teach.
Bentonite is a sort of clay, best known as the main ingredient in kitty litter. Laboratory tests have shown a 100-ft column of compressed bentonite cylinders can stand up to pressures exceeding 20,000 psi, Towler said. Samples that have been tested until they failed have healed themselves in a few days, he added. And it costs less to use than cement, because equipment is needed to lower into a well on a wire. Next year, he is planning a test of compressed bentonite as a material for plugging coal seam gas wells in Australia.
Finding materials with promising properties is a starting point. Regulators, operators and service companies have a long list of requirements that must be met. Laboratory testing showing a material can create an effective lasting barrier is required. Cost is a consideration, and that includes what it will take to use an alternative in the field.
Proving new materials is time consuming and expensive. Cowan said change will require building a critical mass of support for a limited number of alternatives because:
- Operators require products with useful properties that are dependable and competitively priced. Their concerns include what it will take to prepare and pump a material in a well, and making sure it will set properly in a wide range of well conditions.
- Service companies can only handle a limited number of alternatives, each of which needs to generate the sales needed to profitably cover the cost of training workers and buying the equipment needed to install it.
- Regulators require tests showing barrier materials are safe and effective, which can be costly and time consuming.
Creating a critical mass will require a cooperative effort to identify a limited number of materials that can be widely used, do the technology development, and the testing needed to persuade regulators and industry decision makers to support it. “Let’s build a productive community to solve these problems, for example, JIPs (joint industry projects) on methods and placement methods,” Cowan said.
He said the University of Texas engineering school is working to expand the handful of graduate students studying cementing, and he is supporting a project to help project planners and managers focus on the most critical problems ranging from well completions to abandonments. The hope is that by highlighting the factors that could have the biggest impact, decision makers will make better calls.
While Cowan sees the need for rethinking how cementing is done, a lot can be gained by making better decisions while planning and executing jobs. “Minor improvements to the composition of what they pump and a little quality assurance and quality control in the well will make a huge difference,” he said.
For Further Reading
SPE 170712 Cement Evaluation—A Risky Business by Glen Benge, Baker Hughes.
SPE 170667 A Statistical Evaluation of Cement Placement Techniques by Use of Cement Bond Index by Surya Kiran Pallapothu, Martijn Bogaerts, Schlumberger, et al.
SPE 170886 Attenuation-Based Quantitative Cement Bond Index with LWD Sonic: A Novel Approach Applicable to all Casing and Cement Casesby Vivian Pistre, Toshihiro Kinoshita, Schlumberger, et al.
OTC 25438 Improving Overhead And Reducing Time Consumption on P&A Operations with E-line, Explosion-free, Mechanical Cutter Tool by Christian Kruger, Abderrahmane Faraoun, Welltec, et al.
OTC 23906 Offshore Well Plugging and Abandonment: Challenges and Technical Solutions by Praful C Desai, Stephan Hekelaar, Schlumberger, et al.