Making hole has become a more difficult and complex operation as operators move into untapped horizons, especially deepwater and unconventional fields. It is this increased difficulty that is driving a growing number of companies to invest millions of dollars in advanced materials that seek to make drilling wells easier. The technologies many are working on involve not mechanical systems, but advanced chemistry and physical science. Some are using nanoparticles and others are reworking older technologies by adding new substances, all in an effort to make the undrillable drillable.
Those reaching for this prize include teams of university researchers, young technology startups, and established firms that are buying intellectual property from others so they can join the race. Different groups are designing drilling-fluid additives and other materials that they claim make unstable wellbore walls stronger by preventing and sealing fractures as the drill bit eats its way down to the pay zone.
The importance of these wellbore-strengthening objectives is well understood by drillers who have suffered sudden losses of drilling fluids into the rock formation through fractures, which can lead to gas kicks and catastrophic blowouts, or those who have had to deal with stuck pipe because of a collapsed borehole. For petroleum engineers, preventing these problems with new technology means they can design simpler, cheaper, and safer wells with fewer casing strings. For the boardroom, wellbore strengthening means executives can promise better returns and higher flow rates to investors because large-diameter casing strings can be placed into the production zone. And for the industry in general, wellbore strengthening means wells that many consider too dangerous or too hard to drill may soon become tamed.
Installing the optimum size of production casing in frontier formations, such as the Lower Tertiary trend found 30,000 ft to 40,000 ft under the Gulf of Mexico, has become one of the industry’s toughest challenges. “We are kind of at the end of what we can do with conventional casing schemes” in the deepwater environment, said Eric van Oort, a professor of petroleum engineering at the University of Texas at Austin and a 20-year engineering veteran of Shell.
Several of the new drilling materials are designed to strengthen the wellbore, acting as a fortifying agent for the exposed rock, which will safely allow casing strings to be pushed deeper, and in less time. “That is literally going to save operators hundreds of millions of dollars,” said van Oort, who is working with other researchers to develop advanced drilling-fluid materials.
The idea of wellbore strengthening revolves around pushing the drilling window wider. The drilling window is the margin of difference between the pressure it takes the drilling fluids to crack open fissures in the walls of the borehole, known as the fracture gradient, and the pore pressure of the fluids inside the rock formations. Staying inside this window is referred to by drillers as “walking the line” and it is this margin of error that dictates the design of oil and gas wells around the world (Fig. 1).
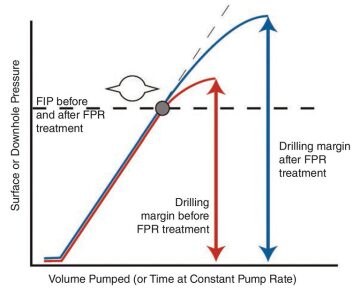
If the new materials being developed today begin to deliver a high degree of reliable wellbore strengthening, then van Oort believes operators “can start pushing their casing setting depths deeper, similar to what is done with managed-pressure drilling and dual-gradient drilling.”
He predicts that wellbore strengthening will become a more costeffective alternative to dual-gradient and managed-pressure drilling. These offshore systems work by mechanically manipulating the pressure inside the wellbore with subsea pumps and regulators. According to van Oort, Chevron’s dual-gradient system reportedly involved an investment of hundreds of millions of dollars to design and build. “These are very expensive solutions to implement,” he said.
But he also believes wellbore strengthening through drilling-fluid additives will complement managed-pressure drilling systems because they are not overlapping technologies. “Those are two independent things,” he said. “So they can actually be used to great effect in conjunction with each other.” No companies to his knowledge are using these technologies together yet, but they are using them separately. ConocoPhillips and Shell are among the companies van Oort said are considering using the two technologies in conjunction.
Onshore, wellbore strengthening applies largely to unconventional shale wells in which clay content can be relatively high. Drilling through these types of formations may be prone to lost-circulation problems, particularly with oil-based or synthetic drilling fluids, which can propagate fractures in the wellbore walls at relatively low pressures.
Drillers stay within the drilling window and try to address fluid losses and lost circulation by monitoring the level of drilling fluids in the wellbore and its density. In the old days, this was done manually by drilling fluid engineers, often called “mud men,” who would crack open bags of barite powder and dump it directly into the hole to increase the thickness and weight of the drilling fluid. Today, this is done by automatic systems, but is still a reactionary process as fluid losses often occur abruptly and without warning because it is hard to predict when a drillstring may encounter fugitive zones, fractures, and cavities.
Simplifying Well Casing
The formations that operators must drill through to reach highly pressurized deepwater reservoirs involve a geological process called “under compaction” that van Oort said results in “very high” pore pressures and low fracture gradients. The narrow drilling window that results from these conditions forces drillers to stop drilling, install casing, and then begin drilling again a dozen times or more before reaching total depth. And each time a new casing string is placed in the well, the next casing string must be smaller than the last one, forming a telescopic straw whose bottom section may be restricted to a mere 6 in., compared with the 36-in.-diameter casing at the top of the well.
To handle so many casing strings and the hangers from which they are secured to inside deepwater wells, van Oort said the industry response has been to build larger and larger drilling rigs. But by artificially strengthening the integrity of the wellbore walls, companies will be able to use fewer hangers and a smaller number of large-diameter casing strings, “allowing for leaner and more cost-effective casing programs that smaller rigs and drillships can handle,” van Oort said.
New Modeling Needed
Runar Nygaard, an associate professor of petroleum engineering at Missouri University of Science and Technology, is researching how wellbore strengthening works using numerical models and analyzing the fracture-healing and sealing capability of different materials. He is also a lead researcher in a University of Calgary study of how nanoparticles can be used for wellbore strengthening.
Nygaard believes that enhanced numerical modeling eventually will become part of an operator’s “planning toolbox” because it will help them understand how drilling-induced fractures around the wellbore change the stress field. Knowing this ahead of time will tell companies where and how they need to apply wellbore-strengthening technology.
“For instance, if you know you are going to drill a complicated section, you know that due to wellbore strengthening, you might be able to drill with a wider mud-weight window,” Nygaard said. He added that this technology may end the conservative backstop practice of installing redundant casing that companies use to ensure wellbore stability.
Nygaard said he expects the next 2 years to be pivotal for this area of study, but stressed the need for the industry to establish new standards and bring regulators into the discussion so they can learn about the enabling effects of wellbore strengthening. “I think before we really can make a major step forward, we need to agree on some method to evaluate the materials and also how to analyze them,” he said. “We will never get the authorities to agree with more aggressive plans for the wells, with longer sections, if we do not have an open scientific basis for what we are doing, which all the companies agree with.”
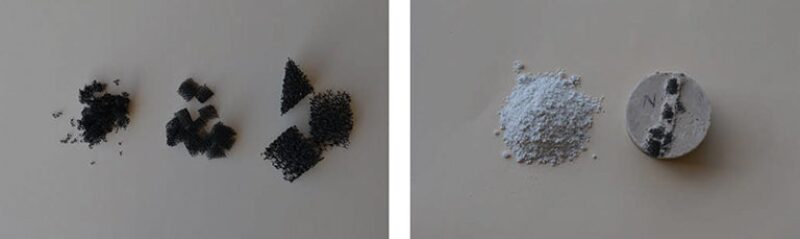
Revitalizing an Older Technology
Earlier this year, Canadian Energy Services (CES) introduced what it calls a third-generation mixed metal hydroxide (MMH) drilling fluid to markets in Canada and in west Texas, where the company is building new facilities. MMH is a technology that has been around for more than 30 years and is used as a loss-of-circulation material and for well cleaning.
CES believes its MMH product can strengthen wellbores as well by increasing the fracture gradient. “The general belief is that the MMH stops fracture propagation because of the unique rheology profile,” said Carl Smith, senior technical advisor at CES.
Until the past few years, MMH has been plagued by issues that have limited its applications. Chief among them is its incompatibility with most drilling-fluid additives and fluid thinners, and it is also highly reactive to coal seams and clay. The latter is a near-fatal flaw when drilling through many shale formations because Smith said all shale contains some amount of clay.
“If you drilled a well and you encountered a reactive clay bed, the rheology would climb up very quickly and, basically, the system could be uncontrollably thick,” he said. “Then you would try and throw in a thinner, it would turn that very thick mud into water and you could not recover it.”
CES said it has overcome these problems with new technology that inhibits the reactiveness of the MMH to other drilling-fluid additives. This is the wellbore-strengthening mechanism that widens the fracture gradient side of the drilling window, stops fluid losses, and allows a higher mud weight in the wellbore than normal. The result is a wellbore-stabilization system that has been used to drill a record long 3,300-ft lateral section in a coalbed methane formation. “And that was definitely a first,” Smith said.
MMH technology is now being deployed in the red-hot shale plays found in the Permian Basin of west Texas where it has been used in wells with lateral lengths of up to 8,000 ft. Smith said that operators there are using his company’s MMH technology to eliminate a section of intermediate casing string as they drill through a salt layer and into a shale layer that is highly fractured. “That is actually our biggest driver right now” in Texas, said Smith.
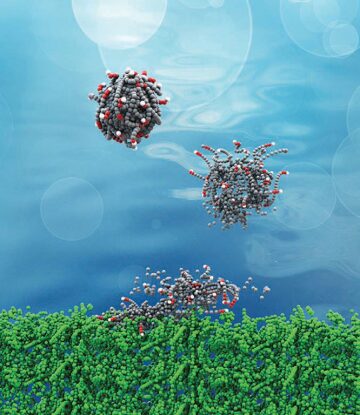
Nanomaterials Taking Shape
University of Calgary researchers have filed for patents for two types of nanomaterials made of calcium carbonate and iron hydroxide that strengthen the wellbore by sealing fractures. When the two materials are combined with graphite and are mixed into an oil-based drilling fluid during testing, 80% to 90% reductions in fluid losses were achieved. The product is being field tested in Canada, and its developers say it is showing positive results.
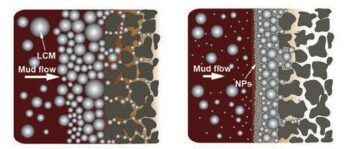
The technology works by adding small droplets of water that contain the nanoparticles to oil-based drilling fluids. These particles then fill up the fractures as they form, preventing cracks from spreading further into the formation, which has the beneficial effect of making the wellbore stronger.
What the researchers believe makes their technology special is that it can prevent major fluid losses when small amounts are added to conventional drilling fluid. “People have added nanoparticles in the 5% to 25% range—this is less than 1%,” said Geir Hareland, one of the researchers involved with the new materials and a director on the board of nFluids, the company commercializing them. Because making these tiny bits of material is an expensive process, Hareland noted that nanoparticle additives that require higher concentrations are less cost-effective.
Hareland recently left the University of Calgary to become chair of the school of chemical engineering at Oklahoma State University, where he is continuing his research on drilling-fluid technology. He believes the industry will be turning to nanoparticles because of their enhanced ability to stop fluid losses.
In addition to conducting field trials of its oil-based material, nFluids is working on applying its technology to water-based drilling fluids, which are used when oil-based fluids are too costly or incompatible with the formation being drilled.
New Lost-Circulation Material: “One Size Fits Many”
Wellbore strengthening is just one half of the drilling window battle. Lost circulation is another problem that happens when drilling fluids flow directly into the formation through fractures, both natural and those induced by drilling, and cavities in the rock called vugs. Problems related to lost circulation and drilling-fluid losses include wellbore collapse, gas kicks, and blowouts.
And since the earliest days of drilling, the industry has taken a number of common materials, ground them up, and pumped them downhole to see if they could help stop losses of drilling fluids and the clay additives that are used to provide thickness and weight. It is still common practice to use walnut shells, shredded bits of plastic, and sugarcane stalks to try to plug up holes in the wellbore. Lost-circulation materials, the industry’s umbrella term for these substances, have received mixed reviews over the years.
“In this industry, people have tried to shred everything they can” to try and find out what works best, said Hong “Max” Wang, chief technology officer of Sharp-Rock Technologies, which has developed new drilling-fluid and lost-circulation materials. “With that kind of attitude, you do not get a good product.”
One reason so many conventional loss-circulation materials fail to stop fluid losses is that fractures and vugs come in many shapes and sizes. Founded in 2010, Sharp-Rock has developed two new technologies for sealing fractures and strengthening wellbore, which Halliburton has obtained the rights to sell to the oil and gas industry. Sharp-Rock’s technologies can be used in both permeable sandstones and impermeable shale, and in water-based and oil-based drilling fluids.
Companies using these technologies onshore include EOG Resources and Hess, while Statoil and Chevron are using them offshore. Wang, a former petroleum engineer and fluids expert at Halliburton and Schlumberger, said that in the Eagle Ford Shale, operators have used close to 1,000 small-volume treatments, reporting a 90% success rate with shutting down fluid-loss zones.
The wellbore-strengthening substance is produced as a white powdery substance made from calcium carbonate particles that can be mixed into drilling fluids or pumped down while drilling in the form of a “pill” that sweeps the wellbore and plugs any fractures or holes it passes along the way to the end of the well. As the sweeping takes place, the pressure capacity of the wellbore increases.
“Because it has sealing capacity, once it touches the loss zone, it immediately shuts off the fractures and the rest will keep filling up more fractures,” said Wang. “If you can imagine inside a fracture, you would have this material accumulate for maybe a foot or two, and that is what is used to hold the pressure.”
He added that when pressure is applied to the well gradually, the material becomes densely packed into the fractures and can hold even more pressure. Wang said independent pressure tests confirmed that plugs as small as 1 mm to 5 mm can withstand pressures up to 12,000 psi.
Larger holes and fractures can be plugged when the quick-sealing fluid technology is used in conjunction with Sharp-Rock’s sponge-like material made from intertwined strands of foam rubber and cut into cubed and triangular wedge-shaped chunks. “On the surface, you never know during the time of drilling what the size and shape of the void is,” Wang said. “The idea here is you use something soft. I call it one-size fits many.”
Sharp-Rock said more independent testing has demonstrated that water can move straight through the plugging material when pressures as low as 100 psi are applied to the wellbore. As the water flows through the porous foam, it also flows through the plugging material, sealing the fracture and providing a slick filter cake on the area exposed to the wellbore, which adds lubrication.