Concerns have been expressed and published about the amount of water used in Canada’s oil-sands industry. The oil-sands deposits are geographically separated from population and agricultural centers in the province of Alberta and are within some of the most prolific river basins. Analysis shows that the amounts of water used by oil-sands operations are low and sustainable. A track record of continuous improvements at existing operations and the application of new technologies will maintain the sustainability into the future.
Introduction
Canada’s oil sands are in three deposits in northern Alberta (Fig. 1). The oil-sands deposits hold 1.8 trillion bbl of oil with 169 billion bbl of economically recoverable reserves. This represents 97% of Canada’s oil reserves, which are the third largest in the world.
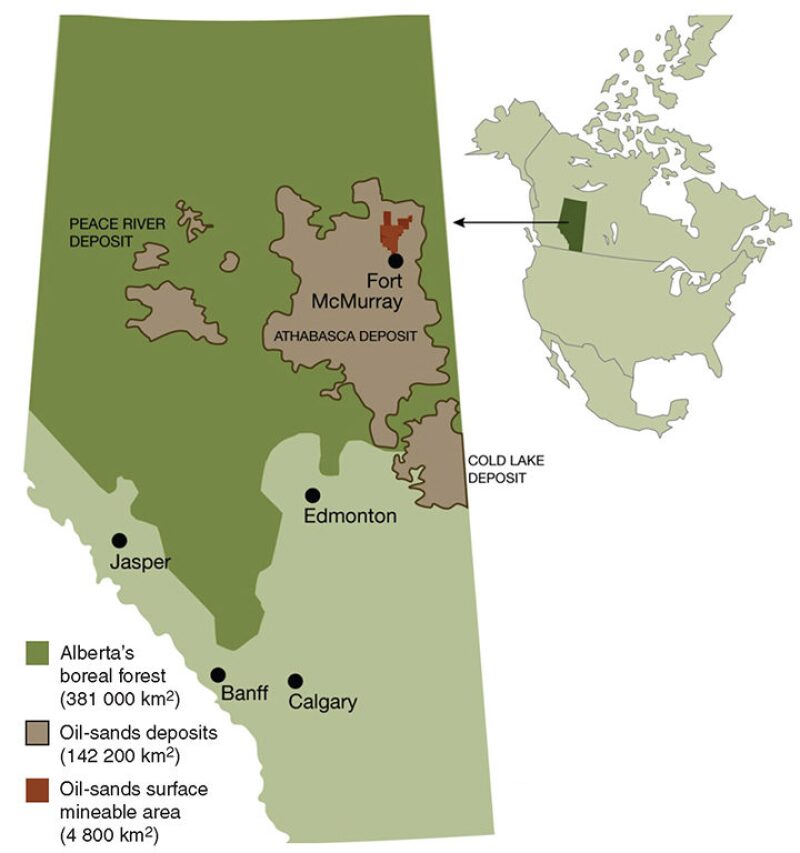
The term “oil sands” is used to describe unconsolidated bituminous sands. The oil saturation in the sands has very high viscosity and is commonly called bitumen or tar. The deposits are found within the McMurray, Clearwater, and Grand Rapids formations of the Mannville group. They are of varying depth, from near surface in some parts of the Athabasca deposit to more than 300 m deep in the Peace River and Cold Lake deposits. Where the oil sands are shallower than 70 m, they may be mined by surface strip mining. This represents 3% of the surface area of the oil sands and 20% of the reserves. The remaining 80% of reserves across all three deposits are accessible only by use of in-situ recovery methods. Both mining and in-situ methods are water based.
How Water Is Used in Canada’s Oil Sands
Because of the high viscosity of the bitumen within the oil sands (8–12°API, >50,000 cp), it does not flow easily and is difficult or impossible to recover with conventional oil methods. The vast majority of commercial operations rely on hot water or steam to reduce the viscosity of the bitumen to allow its recovery.
For in-situ methods, this involves the injection of steam into the oil-sands reservoir and subsequent recovery of the bitumen once it is reduced in viscosity. For mining, the water is used to slurry the oil, transport it, and finally separate it from the ore.
Water Use for In-Situ Oil-Sands Recovery Methods. In areas too deep for mining, oil is extracted from the reservoirs by use of steam injection. The two commercial techniques currently used for in-situ recovery are cyclic steam stimulation (CSS) and steam-assisted gravity drainage (SAGD).
CSS uses the same oil wells over multiple cycles to inject steam and to recover oil (Fig. 2). Each cycle consists of three stages. In the first stage, steam at approximately 300°C is injected under pressure into the reservoir. The heat from the steam then is allowed to equilibrate in a reservoir soak stage. In the third stage, the hot and lower-viscosity oil is pumped from the reservoir along with condensed steam and sent to a central processing facility. The cycle is then repeated. A typical multiwell pad at the Cold Lake operation will go through 8–12 cycles.
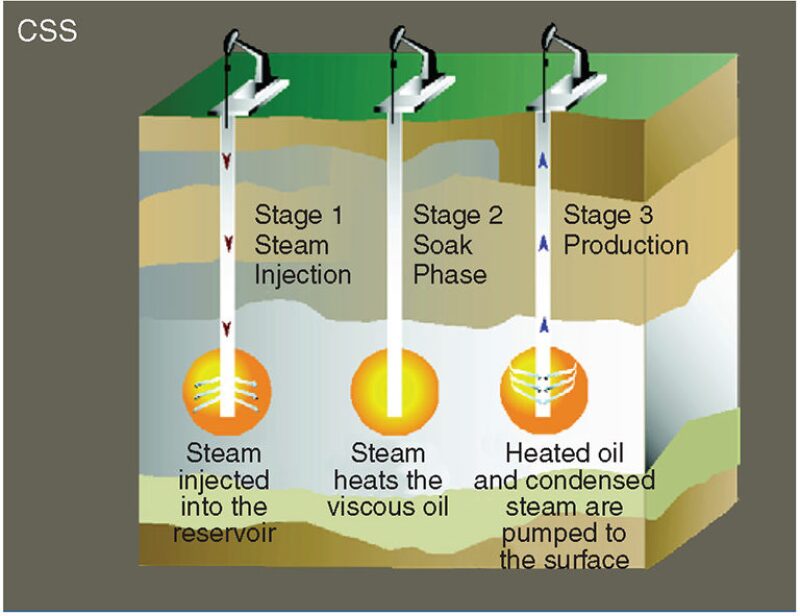
SAGD (Fig. 3) uses precision horizontal drilling to position horizontal well pairs such that one well is above the other within the oil-sands reservoir. The upper well is used to inject steam (at approximately 200–250°C) into the formation where it rises and percolates through the oil-sands deposits, creating a steam chamber. The steam displaces and heats the bitumen, which flows downward by gravity and is recovered by pumping the lower well.

For both CSS and SAGD, the water produced with the bitumen is separated and reinjected into the reservoir. The recycle rate depends on the supply and demand for steam in the operation, the quality of the produced water, and the technology used for water treatment. In all operations, if the produced-water volume exceeds the steam-injection volumes, then water must be disposed of through deep-well injection. Usually, however, and always during startup of a new operation when there is little or no produced water, the volume of produced water is less than the volume required for steam. In these cases, new water volumes (called makeup water) are required to make up for the shortfall.
Water Use for Oil-Sands Mining. Fig. 4 is a schematic of how bitumen is produced from oil-sands mining operations. After the overburden is removed from above the oil-sands ore, large shovels capable of up to 100 t/load fill large haul trucks with capacities of up to 400 t/load. The haul trucks transport the ore to a crushing facility, where it is crushed and mixed with water to create a slurry that is transported by pipeline (called hydrotransport) to a central processing facility. The agitation and mixing during hydrotransport begin the process of separating the bitumen from the oil sands. At the processing facility, the bitumen is separated from the slurry and sent to an on-site upgrader or off-site refinery. The waste products consisting of residual bitumen, sand, fine particles, and water are sent to a tailings area, where the water is separated from the solids and recycled into the process. Traditional tailings technology uses tailings ponds to settle the solids from the water.
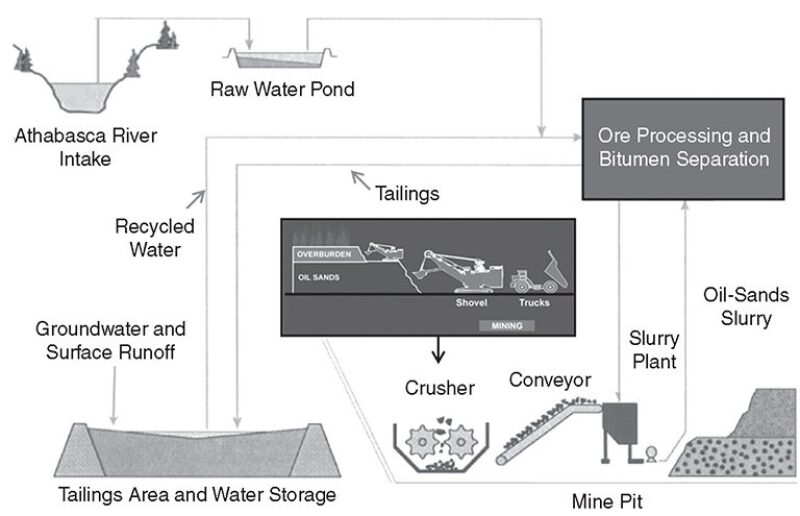
During the extraction process, the oil-sands ore is converted from a compact bitumen-bearing porous medium to a looser water-bearing tailings product. The bitumen is essentially replaced with water. However, because the tailings have more pore space than the original ore, the ratio of water used to bitumen produced is greater than unity.
The water sources for oil-sands mining operations include the recycled tailings water, Athabasca River water, groundwater, and surface water runoff. The largest overall water source is the recycled tailings water, which, after startup, represents approximately 80% of the water used in the operations.
Natural Availability of Water in Alberta’s Oil-Sands Areas
On a global scale, Canada has 7% of the annual renewable water supply and one of the largest per-capita water supplies, with an excess of 70 000 m3 available per person per year, an average drainage yield of 3.4 trillion m3/a, and national water usage of less than 10% of supply.
On the basis of 2009 numbers, the Canadian government has licensed or allocated 9.9 billion m3 of fresh water, or 7.6% of provincial supply, for use in Alberta. The oil and gas industry is allocated 830 million m3, which represents 8.4% of the provincial allocations and 0.6% of the provincial water supply.
The oil-sands industry is distributed across the northern half of the province, within the Peace, Beaver, and Athabasca river basins. The total water allocations in the Peace and Athabasca river basins are 0.4 and 4.3%, respectively. In all basins, the allocation to the oil and gas sector (which is dominated by oil-sands production in these three basins) is 3% or less of available average annual supply.
Actual Water Use, Forecast Water Use, and Continuous Improvement for Oil-Sands In-Situ Operations
The principal water sources for the in-situ thermal industry are recycled produced water, fresh surface water, fresh groundwater, and saline groundwater. With recycling performance of approximately 90%, recycled produced water is by far the largest water source used. For makeup water, historically the industry has relied on fresh water. However, over the past several decades and increasingly over the past 10 years, industry has been increasing the amount of saline makeup water as an alternative to fresh water.
Between 2002 and 2010, the growth in saline-water use has outpaced the growth in freshwater use to the extent that saline-water use has now exceeded freshwater use. In 2010, the total freshwater use was 17.5 million m3, which is split between the Beaver River basin (7.4 million m3), the Athabasca River basin (6.1 million m3), and the Peace River basin (4 million m3). These volumes correspond to only 0.02% of the average natural flows in these basins. Individually, the water use corresponds to 1.2% of Beaver River flows, 0.03% of Athabasca River flows, and 0.006% of Peace River flows.
In 2010, productivity for the in-situ industry was 0.43 (17.5 million m3 of fresh water to produce 40.8 million m3 of bitumen). This value is used to project freshwater use. By 2030, this assumption results in a freshwater use of 78 million m3. However, given the trend toward saline water over the last 10 years, 78 million m3 is likely a high-volume case. If the trends over the last 10 years for reduction in fresh water are followed, then the resulting use in 2030 will be 38 million m3, with a freshwater-to-bitumen productivity of 0.21. These numbers represent a range of 0.04–0.09% of available average flows in the Peace, Beaver, and Athabasca basins and clearly represent a sustainable water use.
Actual Water Use, Forecast Water Use, and Continuous Improvement for Oil-Sands Mining Operations
All oil-sands mining occurs within the Athabasca River basin, as shown in Fig. 1. Similar to in-situ operations, the largest source of water used in the mining extraction process is recycled water. In general, approximately 80–90% of the water used to recover bitumen is recycled process-affected water. Unlike in-situ operations, however, the use and storage of process-affected water and tailings in open mine pits and tailings impoundments on the surface limit the amount of saline water that may be used in the operation. For this reason and the potential for disruption of the extraction process by some salts, the principal source of makeup water for oil-sands mining is fresh water.
Approximately 71% of the fresh water is sourced from the Athabasca River. The remaining makeup water is sourced from fresh groundwater (6%) or surface water runoff collected at the mine (23%). These values vary with the weather and the season. Because oil-sands mines take a long time to design and construct after approvals and water licenses are received, the water allocations outpace development. For these reasons, actual water usage is significantly less than allocated water. During 2009–11, an average of only 22% of oil-sands-mining allocations was used.
Water use tracks bitumen production fairly closely. Peaks in water use typically correspond to the startup of new mines or to expansions. Mines have a higher water use in startup years because it can take time to build enough water inventory to start recycling from the tailings areas. To avoid this issue, mines can partly fill tailings areas with water before operation to enable the recycling system to function earlier. In either case, there is a peak in water withdrawals during mine startup.
Recent projections show mining production will grow to 1.33 million B/D (77 million m3/a) by 2020 and 1.89 million B/D (110 million m3/a) by 2030. Using the average productivity of 2.5, Athabasca River withdrawals are forecast to be approximately 6 m3/s (194 million m3) in 2020 and approximately 9 m3/s (277 million m3) by 2030. These represent 1–1.4% of the average annual flows at Fort McMurray. In 2009, the Oil Sands Developers Group conducted a projection for two very aggressive growth cases of 2.5 million B/D and 3.5 million B/D of bitumen by 2020. It was determined that water requirements could grow to between 11 and 16 m3/s or 1.5–2.5% of the annual average flows of the Athabasca River at Fort McMurray for the two cases. Thus, even aggressive-growth cases use a small percentage of annual average natural flows.
Conclusions
Summing all of the 2030 projected freshwater demands for both in-situ recovery and oil-sands mining results in a requirement of 428 million–469 million m3, which is approximately 0.4% of the provincial water supply and 0.5% of the natural flows of the three basins containing the oil-sands deposits. Given continuous improvement and advances in technology, it is expected that these projected volumes will drop. Nonetheless, current projections show that, by 2030, only 0.4% of the water in the province of Alberta will be used to produce 80% of Canada’s total crude-oil output.
This article, written by Editorial Manager Adam Wilson, contains highlights of paper SPE 156676, “Water Use in Canada’s Oil-Sands Industry: The Facts,” by Stuart Lunn, Imperial Oil Resources, prepared for the 2012 SPE/APPEA International Conference on Health, Safety, and Environment in Oil and Gas Exploration and Production, Perth, Australia, 11–13 September. The paper has not been peer reviewed.