Demand for a better way to remove carbon dioxide (CO2) from natural gas led to the creation of a new material at Rice University in Houston that does something unprecedented on the molecular scale, and might even change gas processing.
For professor James Tour, the fundamental science behind this porous carbon material created in his laboratory “is really profound.” The black powdery material developed by a Rice graduate student, Chih-Chau Hwang, absorbs nearly its weight of carbon dioxide by creating long polymer chains of carbon dioxide at a pressure level that is elevated, but easily attained, in a gas processing facility.
For Tour, it is an exciting development because the carbon dioxide polymer structure, which was observed using spectroscopy, is something that he said has never been seen in nature, and only rarely in labs at extreme pressures. But the pioneering chemist recognizes that for those developing new oilfield technologies, what matters is what it can do, not how it might do so.
Rice’s patents have been licensed by Apache Corp., which supported research seeking a new material for gas separation for the past 2½ years. On the plus side, it appears to be energy-efficient, can hold a large volume relative to its weight, and is highly selective at grabbing carbon dioxide without also removing some natural gas as well.
The investment by the independent oil company reflects the exploration and production industry’s appetite for improved methods that are more compact, cost less to run, and occupy less space. One indication of that is the increased demand for improved membrane-based separation methods, which are far more compact and adaptable to offshore environments than liquid chemical separation methods using amines.
Cameron recently began selling a new, more efficient membrane material, called PN-1 multifiber membrane element, which was developed in partnership with Petronas, the Malaysian national oil company. Better carbon dioxide removal is a pressing concern in southeast Asia, where many large gas deposits have not been developed because of carbon dioxide levels that can equal the gas in the ground.
Production growth there, and in far-flung regions from Russia to Brazil, will require dealing with higher levels of carbon dioxide and hydrogen sulfide, which often are found together and removed using similar processes.
“There is more gas in deep water from fields that are sour and have high levels of carbon dioxide,” said Ankur Jariwala, a senior product manager for gas technology at Cameron. “Facilities offshore need to be compact, efficient, and lightweight.”
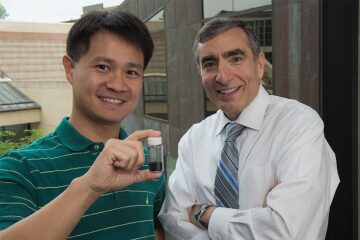
Petronas’ search for more effective separation methods includes a test of a nozzle designed to remove carbon dioxide from a high-velocity gas stream. An SPE paper (SPE 24953) explained the motivation for the project by noting that growing gas demand rewards development of gas fields with high carbon dioxide levels. Another company project considered how to profitably develop a field producing 70% carbon dioxide. “Traditionally, conventional technologies such as amines and membranes have been used for CO2 removal from natural gas. However, these technologies are economically prohibited, and to some extent, not technically viable for a footprint-constricted offshore platform,” the paper said.
There are opportunities for innovation onshore, where operators of small to medium fields sell their gas to processors at a discount rather than invest in separation equipment to reduce the carbon dioxide to the level required by pipelines.
“We are not a processing company. But when we look at all the things out there, we decided the industry is really ripe for some sort of disruptive technology change in gas processing,” said Cal Cooper, director of special projects and emerging technologies at Apache. “We need something that cheaply separates CO2 from natural gas and is a lot more practical than current systems.”
The search led Apache to Rice University where they tried various materials seeking one that could remove carbon dioxide efficiently from gas at a pressure level commonly found in a flowing gas well, and then release it with a relatively small pressure reduction. The verb suggested by Tour for this process was to “sorb,” rather than to adsorb or absorb. “Sorb means ‘to stick’ but does not imply the location or mechanism. This is so unique that better to leave the term general: sorb,” he said.
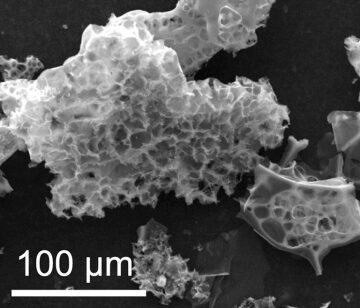
Based on laboratory testing, it appears the Rice material might be the basis of an attractive alternative. But work has just begun creating a device using this material, which could be used to test it. “Lots of stuff has to happen to commercialize it,” Cooper said. “This is a material, not really a process. It will take time and tweaking.”
Evolving Methods
For a new material to find a place in the separation business, it will need to significantly outperform current technology. That bar has been rising significantly as improved materials are developed, and more efficient systems are designed, often combining multiple separation methods.
On the chemical side, more efficient amine systems are under development. And work continues on more effective, durable membranes that will lead to smaller, more efficient devices with less downtime.
For example, the PN-1 requires 11% less space than the current generation of membranes, which occupy a footprint that is a small fraction of the size of the earliest devices introduced in 1982, Jariwala said. The PN-1 membrane depends on a polymer material with hollow fibers to process the gas using preferential permeation. The goal is to direct faster-moving, smaller molecules of carbon dioxide and hydrogen sulfide down a different path than slower-moving hydrocarbons. The smaller molecules permeate faster into the open inner cores of hollow fibers, leaving behind a higher pressure stream of treated natural gas.
In practice, the separation is not absolute, but the latest generation is more selective, allowing it to do more per step. Jariwala said a system using the new PN-1 membrane can reduce the carbon dioxide level from 20% to 3% in a single step, compared with two steps in previous membrane methods. It also provides bulk removal of hydrogen sulfide, but it is not as selective as options such as amine, so further processing is often needed.
Others are edging into the business. Smaller system integrators are putting together systems built around longer lasting membranes. The improvements are reducing the number of steps needed for pretreatment using fibers resistant to damage by water and heavier hydrocarbons, said Charles Solomon, president of Global Industrial Water. It is aiming to expand the use of carbon dioxide separation using membranes by selling relatively compact, skid-mounted membrane systems.
General Electric Oil and Gas is doing early stage work on new methods that it hopes will lead to better ways of processing natural gas, said Todd Allhart, a spokesman for GE Global Research. It is trying to expand into natural gas processing. GE is currently in the power business, where much of the technology development is aimed at cleaning up smokestack gas, often using amine systems.
The carbon dioxide separation business can be divided into two markets: small concentrations of about 10% or less, and higher ones with more than 10%, said Steve Melzer, whose company Melzer Consulting specializes in using carbon dioxide for enhanced oil recovery (EOR). The carbon dioxide content can go up to 90% from fields where it is injected for EOR.
Higher concentrations typically require large investments and multiple processing methods. Processing is a common investment for EOR field operators, who reinject the valuable gas, which can extend the life of an old field. A bonus for those who can afford more sophisticated separation systems is that the process also yields valuable natural gas liquids.
New separation methods are needed, said Melzer, adding, “It is an underserved market in the CO2 capture world.” Cameron, the dominant supplier of membrane units used by large EOR operations, wants to significantly expand its market with a product aimed at small to medium onshore fields where the gas has a relatively low carbon dioxide content, Jariwala said.
Costs will be reduced by selling a standardized gas processing unit using membranes to convert gas with relatively low levels of carbon dioxide (about 20% or less) to pipeline quality, he said. The challenge is delivering a simple-to-operate, reliable unit that justifies an investment in the equipment and people needed to do processing in-house rather than selling it to a third party at a discount.
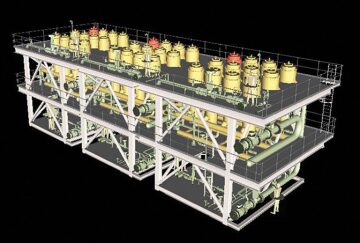
The economics of separation would become more attractive if there were a way to extract value from the carbon dioxide that is now disposed of as a waste product. Using a membrane system from Cameron, Petrobras is reinjecting carbon dioxide removed from production from the Tupi field, a giant reservoir in the pre-salt trend offshore Brazil, to reduce its emissions and possibly enhance its long-term production.
Transfer Challenges
The most widely used methods are energy-intensive processes. Amine does an excellent job of stripping out carbon dioxide, but it then must be heated to force the amine to release the trapped carbon dioxide so that it can be used again. This all goes on in tall units that look like small chemical plants that are too large for many offshore facilities.
Membranes depend on pressure differences maintained by powerful compressors, heating, and pretreatment to deal with substances that can foul costly membranes. In search of a more efficient alternative, the new material from Rice may prove to be more energy-efficient because it works at pressures and temperatures often found in fields.
Based on lab tests, the material works best at a pressure of about 30 bar (435 psi) and temperatures from 20°C to 50°C (68°F to 122°F). Tour said this is in line with the well specifications set by Apache for the project. The performance was better when the temperature was at the low end of the range or cooler, he said.
Its ability to adsorb carbon dioxide begins with the way it is made. Tour compared the process to baking a cake using baking soda, which is sodium bicarbonate. When that chemical comes in contact with water it forms carbon dioxide bubbles that leave an intricate pore network, he said. In the case of porous carbon, the cooking temperature reaches 600°C, creating a black powder that looks like finely ground charcoal with microscopic pores that offer a huge surface area per gram for storing trapped carbon dioxide.
On those pores, there are spots with sulfur or nitrogen that react with carbon dioxide. These are nucleophilic—they have a pair of electrons to contribute—pulling in carbon dioxide molecules seeking those electrons. What makes this method so promising is that each of these sites can capture and hold a long chain of carbon dioxide molecules.
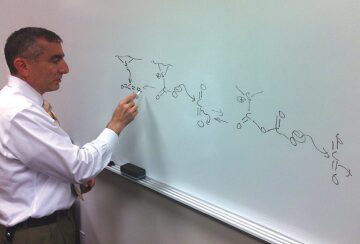
Tour describes what happens: the first carbon dioxide molecule is attacked by the electron pair from a sulfur or nitrogen site. After it attaches there, the added electrons on the first carbon dioxide molecule attract a second carbon dioxide molecule that bonds to the first. The second electron-rich molecule grabs a third carbon dioxide molecule and the process repeats, creating a polymer chain that remains stable until the pressure is reduced.
The carbon dioxide polymer chains crowd out methane from the porous carbon minimizing the amount of natural gas the material can attract.
When the pressure is reduced to the atmospheric level, the carbon dioxide polymer chains come apart and release the carbon dioxide. After the porous carbon is depolymerized, it can be used again.
Creating devices to take advantage of this new material will require some significant engineering work. “Where we stand now with powders is they are very amazing in what they can do in a beaker” in lab tests, Cooper said. “For them to be commercial, a couple things have to happen.” At the top of his list are three items:
- The carbon material must be made cheaply.
- The system needs to be able to process a constant flow of gas using the porous carbon material, which needs to be periodically depressurized to allow it to release carbon dioxide and restore its separation capacity.
- A loose powder is a bad match for fast-flowing gas.
There are methods available that can be adapted to solve the first two items and multiple possibilities for the third.
“A loose powder is a bad match for the fast flows and large volumes seen in gas processing. So we need a suitable substrate to give structure to the material,” Cooper said.
The cost of making the porous carbon has dropped, Tour said. After early work using lab chemicals, his lab has been making the porous carbon material with the lowest cost crude, which is essentially asphalt, plus either hydrogen sulfide or ammonia. It has also developed a variety of porous carbon designed to remove hydrogen sulfide.
“We came upon porous carbon 1½ years ago,” Tour said. “We published our first paper recently (Nature Communications, June 3). Within the next 6 months, there will be another two or three papers.”
To marry a material that needs to sorb and then desorb, like breathing, Apache is looking into designs using swing-cycle technologies, which have been used to solve similar problems for other processes. Apache is actively working with a number of fabrication labs and process experts to help address the problems it presents.
Apache is evaluating using pellets, membranes, or organometallic structures—compounds with carbon and metallic components.
“Since it was published, we have been bombarded by people who want to be our friends and that is encouraging,” Cooper said. “For this to be a successful disruptive technology, it will need enthusiasm from a lot of specialists.”
It must also outperform the best available options. “It will need to cost less than the current system. That is the only way a disruptive technology will become accepted. But at this point, it would be kind of a fantasy to give you numbers,” Cooper said, adding that it is impossible to predict how this will end up. “We are starting something, not ending something.”
For Further Reading
OTC 25051 Optimising Energy Footprint for Offshore CO2 Separation and Transportation (or CCS) by M.G. Mohd Noh, W.V. Hor, M.Y.J. Jalani, and M.A. Mas’od, Petronas Research.
OTC 24953 Concept Proofing of Supersonic Nozzle Separator for CO2 Separation from Natural Gas using a Flow Loop by R. Ahmad Samawe, K. Rostani, A. Mohd Jalil, M. Esa, and N. Othman, Petronas.