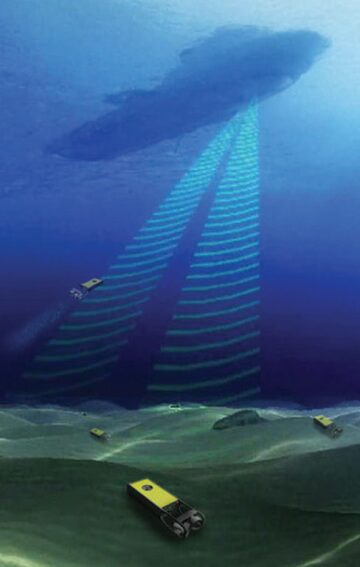
Saudi Aramco is on a mission to increase the amount of seismic data that it collects by fourfold, while reducing costs and acquisition time by half of what it spends today. Part of the company’s grand vision involves the creation of an entire fleet—3,000 units—of autonomous seismic nodes that will largely eliminate the need to contract for remotely operated vehicles (ROVs) and their support vessels for future seafloor seismic acquisition projects.
The company began work on the technology, which it calls RoboNodes, in 2012 with French seismic surveying firm CGG and Seabed Geosolutions, a joint venture formed by CGG and Fugro last year. So far, the technology has been tested in pools, lakes, and at sea. A launch and recovery system for retrieving the nodes in a timely manner, and in rough sea conditions, is also under development. Some of the challenges the project team is working to overcome involve designing a low-cost, highly accurate clock for simultaneous seismic shoots and a power-saving data recorder.
The RoboNodes are rated for 300-m depths and can be programed to “swim” to the seafloor in novel arrangements to illuminate subsurface structures that may hold hydrocarbon deposits. The nodes are controlled by an acoustic communication system and, with the push of a button, the robotic units can move to another prearranged location to begin another seismic shoot from a different angle. “You can play with the geometry,” said Constantinos Tsingas, a geophysicist who works on the RoboNode project at Saudi Aramco. “You do not have to arrange them in a uniform grid. You can put them anywhere you want, because you can send them anywhere you want.”
Tsingas said the company wants RoboNodes to provide seismic data faster, cheaper, and with more resolution than what are possible using conventional ocean-bottom nodes and cables, two widely used subsea acquisition technologies. Deployed off vessels, ocean-bottom cables collect data as sound waves from an air gun reflect off subsurface formations and into hydrophones, which are spread evenly along the inside of the cable.
“That is time consuming and costly,” said Tsingas. He added that the cables have some limitations regarding where they can be used. “You cannot access places close to a drilling rig; they will not allow you to place the cable near one. By having a flexible system like RoboNodes, we can access these areas much easier.”
Some of the same problems that limit ocean-bottom cables also limit the application of ocean-bottom nodes, a newer technology. Because of the risk of tangling up the ROV’s umbilical, or even worse, striking a man-made subsea structure, ROVs are not used to deploy ocean-bottom nodes in restrictive subsea environments. RoboNodes are many times smaller than an ROV and presumably would not suffer from the high rate of downtime incurred by ROV systems. “After they record,” Tsingas said of the nodes, “they will be able to come back, recharge their batteries, and go back down again for another mission.”
Another downside of ocean-bottom nodes is that while they can be placed in any variety of arrangements best suited to image the subsurface, each time a company wants to do a new shoot, an ROV must first locate and then relocate each node, one by one. Sometimes, this poses a challenge when the nodes become hard to find because of low visibility and the turbidity of the seafloor caused by the ROV’s thrusters. Other times, nodes have been known to sink in a muddy seafloor.
Saudi Aramco’s ultimate vision is to develop thousands of RoboNodes to speed up the company’s efforts to locate more offshore discoveries. The company hopes that by 2020, the geophysical sector of the oil and gas industry will have adopted robotic technology for seismic acquisition. Outside of Saudi Arabia, the technology may have a wider application, especially in deepwater areas wholly dependent on ROV support. “Hopefully, we can take it deeper,” Tsingas said.