Long recognized for producing the world’s lowest-cost crude oil, Saudi Aramco is also looking to deliver shareholder value by efficiently expanding its petrochemicals business globally, and in doing so, delivering innovative downstream projects. The company’s project teams, therefore, must routinely evaluate execution risk in the development and execution of major petrochemical projects globally.
With its accountability to shareholders in mind, the company’s project leadership gathered in-depth insights into the various region-specific factors—e.g., engineering costs, equipment sourcing, contracting strategies, local construction norms—which, if left unchecked, are known to quickly erode the capital effectiveness and value of major projects.
A Two-Pronged Assessment Approach
Saudi Aramco commissioned a creative two-pronged assessment—one following a bottom-up approach, the other a top-down approach—of the potential risks associated with delivering major petrochemicals projects in four regions—China, the Kingdom of Saudi Arabia, India, and the US Gulf Coast (USGC). Wood PLC and Independent Project Analysis (IPA) Inc. were tasked by Saudi Aramco’s Facilities Planning Team to conduct independent comprehensive project risk assessments for each of the four regions.
Even the most experienced individual consultants, who will have extensive war stories to share, have only worked on a handful of large capital projects, because most large projects take over 5 years to complete. Wood and IPA, by contrast, have either executed or evaluated thousands of projects combined, including hundreds located within Saudi Aramco’s designated regions.
Wood leveraged the specialist knowledge of local offices with expertise to study engineering practices, sourcing decisions and costs, and the quality of deliverables. Wood led the bottom-up analysis of the many complex engineering decisions project teams take during project planning, development, and execution. Wood also provided expert analysis of the significant regional cost differences for major chemicals projects in each of the four regions.
Leveraging its proprietary global capital projects database, IPA conducted the top-down analysis of the execution of large petrochemical projects in the regions, using empirical and quantitative research findings to identify statistically significant differences. IPA quantified the relative cost competitiveness of each location and categorized country-specific risks based on lessons learned from past projects. With its database containing detailed project cost data collected from owner companies, IPA can assess costs from the owner’s point of view.
The authors would be remiss not to mention the research findings discussed in this article were presented just before the COVID-19 outbreak began, causing economies to shut down beginning in March 2020, altering global and regional market conditions, and perhaps permanently changing supply chains and local practices. Saudi Aramco is maintaining a feedback loop with its consultancies for this research. It is hoped that some of these engineering cost and risk assessment issues can be revisited once the pandemic subsides, hopefully in the not-so-distant future.
Cross-Functional Workshop Knowledge Sharing
Saudi Aramco convened a workshop for the two consultancies and owner project team managers to share information and set research expectations. An overarching message that came across during the workshop was how critical capital costs are to the competitiveness of downstream projects and the many opportunities that exist for tradeoffs and material cost savings. Local supply chains, the robustness of the local infrastructure, and regional market conditions were also clearly identified as requiring individual, detailed analysis.
Certain preconceptions were challenged, such as the expectation that major differences in engineering standards lead to major differences in costs. The attractiveness of lump-sum contracting strategies also took a hit. Given local norms along the USGC, for instance, owners can end up paying a premium if they enter a lump-sum arrangement.
Working hard to avoid “gold plating” is important, and certain equipment sourcing provisions ought to be challenged in some regions. Some lower cost providers are now able to deliver highly specialized and high-quality equipment to project sites.
Research Findings
Wood’s Bottom-Up Engineering Approach
The study’s objective was to provide regional cost differences for major chemicals projects, going beyond typical estimating metrics such as labor rates and taxes to examine different approaches typically taken and even differences in project scope.
The bottom-up study was executed by a cross-functional team led from Wood’s Reading, UK, office, using their Toolkit for Capital Cost Reduction, and combined the experience of Wood’s global network of local specialists and engineering offices.
The analysis was made at three levels covering regional differences for a fixed project scope, scope changes due to specific location, and company practices for a representative regional company.

Key Drivers of Regional Differences
Using extensive project execution experience and local knowledge, the Wood team developed estimating models to analyze regional differences. These differences were driven by the following major components:
- Construction labor; detailed engineering; and engineering, procurement, and construction (EPC) site supervision rates
- Workforce productivity
- Materials (within materials and labor contracts) and bulk materials costs
Equipment Sourcing—Sourcing of major equipment was identified as an important regional difference. In India and China, projects source a high proportion of standard equipment from low-cost countries. Licensed, proprietary, and specialist items such as reactors and compressors were expected to be sourced globally; however, it was observed that (in China in particular) local sources are developing for even specialist equipment.
Many Western and Middle Eastern companies have tight sourcing policies that restrict sourcing major equipment from low-cost countries. The overall effect of this can potentially save 2% of overall project cost.
Hot Project Markets—Overheating of construction markets occurs when the supply of skilled labor and other key resources cannot keep pace with demand from high numbers of competing projects. This leads to inflated labor rates, decreased productivity, and increased materials costs. In an overheated market, total cost was shown to increase by over 10%.
Modularization—Wood has extensive experience in modularized construction, which is generally employed
- When site labor rates are high and/or labor is not readily available.
- When space available, or accessibility, is severely limited.
- When weather windows limit duration or productivity at site over significant periods.
The study included the degree of modularization possible for various process and supporting units. Modularization does not always result in a cost saving; high on-site labor costs are the primary driver of potential savings. USGC project costs, for example, benefited from modularization, but Middle East and Asian projects were found to be more expensive.
Advanced Work Packaging—Advanced work packaging (AWP) is a construction methodology to provide work packs earlier and use modern tools with close liaison between engineering, planning, and construction. It has been increasingly implemented by oil majors in Western regions. Various barriers exist to application in the Middle East, India or China, including industry structure, greater supervision and shortage of specific skills, though the potential savings could be substantial. Savings of more than 1% of total project cost could be achievable for highly complex projects.
Project Scope Differences in Specific Locations—OSBL [outside battery limits] scope such as utilities and waste treatment as well as transport infrastructure and storage requirements varied widely depending on whether existing infrastructure can be utilized. Outsourcing moves costs from Capex to Opex and will change the risk profile of the project. The highest amount of third-party provision is seen in Chinese industrial parks. Similarly, recent Indian developments are also using the industrial cluster model. Third-party supply of steam and power is a major differentiator, though this would be compensated by a higher operating cost over the medium term.
Highly mature areas of development, such as the USGC, showed a significant reduction in required storage investment vs. other regions, leveraging existing strength in infrastructure and reliable pipeline supply of feeds.
Differences in Company Practices and Standards—Design standards alignment across regions and companies is relatively close for highly complex facilities with licensed process technology. In China and India this is true where projects are joint ventures with international oil companies. But the application of standards and cost-reduction practices can vary to a significant degree. This variation was driven by a desire to avoid operational risk by some vs. delivering a capital efficient project by others. These differences were shown to result in up to 5% cost variation.
Procurement Practices—Differences in vendor list requirements and how supply risk is being shared in the value chain, standardization of vendor requirements, as well as many other areas of variation were observed. These led to significant differences in vendor quotes for identical equipment, which reinforces the need for optimization of the relationship between owner, vendor, and contractor.
IPA’s Top-Down Factored Risk Assessment
IPA used its research, network of owner companies, and historical data to provide a comprehensive top‑down view of the issues an owner must consider in each of the four regions. IPA analyzed the relative competitiveness of each location, country-specific value-eroding risks, and practices used by the top performing projects to achieve peak performance.
Owners make material tradeoffs between quality, cost, and schedule through different project execution practices that result in different outcomes depending on owner priorities. Therefore, IPA conducted in‑depth analyses of the engineering, equipment, bulk materials, labor, project management, and other location-specific costs, and also analyzed differences between real projects, including various strategies for using the local supply chain.
Project Risks
IPA reviewed the risk profiles for mega chemicals projects for all four regions. Each requires a specific mitigation strategy. The risk profile for China, for example, shows a low frequency of shortages for both engineering and labor, low volatility in labor wages, and low likelihood of labor strikes. These are relatively severe risks in India. In Saudi Arabia, by comparison, the risk of contractor, procurement, or construction shortages is a far higher risk than labor disputes or inclement weather.
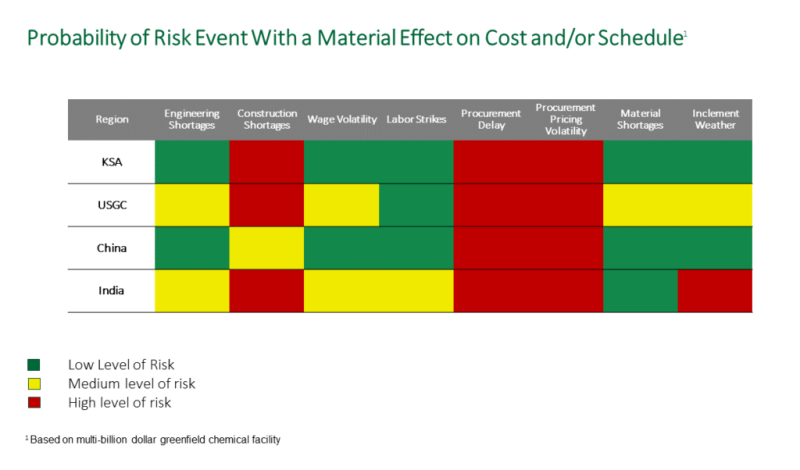
IPA also looked at the effects of each of these risks on project cost growth and schedule delay to quantify the expected values of these types of risks on project outcomes. For example, procurement delays are a high-risk event on projects in every region. When a major project experiences late delivery of materials, the knock-on effects are significant. On average, after controlling for other practices and project characteristics, a delay in the delivery of key materials extended the project’s execution schedule by 8%, which translates to more than 2 months of schedule lost. As a result of the inefficiencies late-arriving materials have on field productivity, late materials deliveries, on average, add 6% to the overall project cost.
Contracting Strategy
IPA evaluated different contracting strategies for each location. The corresponding implications for owner companies were reported. Owners are constantly looking for contracting approaches that will deliver better value for money or approaches that fit better with the company’s goals and culture.
It is important to employ the right contracting strategies and do this effectively. Differing outcomes of projects have causal links to the contracting strategies employed. For example, a reimbursable type contract will typically cost more but have a strong adherence to schedule, whereas a lump-sum contract may lead to the opposite results. Each strategy presents unique challenges and opportunities for owner companies. Consequently, it is important to tailor the contracting approach to the location, considering the market conditions, local norms, and project characteristics.
Do the Project Right
Projects can be well run or poorly executed; the difference between these far exceeds the differences due to contracting strategy and other single issues. Several key owner practices drive project performance; a key measure of this is IPA’s Front-End Loading (FEL) Index. The FEL Index is a measurement of the amount and quality of work done leading up to project authorization and incorporates elements such as site-specific factors, project execution planning, and engineering definition. Sometimes location issues affect the ability of project teams to do FEL well. Even then, project teams must commit to FEL Best Practices. To summarize, FEL works.
When megaprojects attain a “best practical” FEL rating, they can achieve cost and schedule savings of approximately 19% and 13%, respectively, compared to megaprojects that achieve the industry average FEL rating of “fair.” As a result, ensuring projects are properly defined prior to authorization is typically the single most leveraging factor when it comes to project success in every region of the world.
Ian Deakin is a facilities planning specialist with Saudi Arabian Oil Company (Aramco). He has been working in Saudi Aramco’s Facilities Planning Department for 4 years specializing in planning major petrochemical and refining projects. Originally from the UK and now living in Dhahran, Saudi Arabia, he has had the pleasure to work extensively throughout Asia, the Middle East, the US, and Europe. His specialties include project management, linear programming, and techno-economic analysis. He holds an MEng in chemical engineering from Loughborough University.
Mark Cudmore currently manages the Asset Consultancy business area within Wood’s Specialist Engineering and Consultancy division. In his technical consulting roles with Wood, and previously with KBC Consulting, he has provided strategic investment option development and economic analysis, as well as leading low investment yield and energy optimization studies. He has previously worked at the Coryton and Petit-Couronne refineries in strategy, front-end design, production planning, and various process engineering roles. He holds an MEng in chemical engineering from Loughborough University.
Mike McFadden is director of IPA’s Project Research Division. He is responsible for IPA’s research organization that leads and supports IPA’s research and develops the analytical tools IPA employs in evaluating capital projects. His areas of expertise include refining process projects, megaproject performance, and new technology project performance. He has 15 years of experience in the paper and chemicals industries. He has experience in developing and commercializing new processes and products, and many years of experience in project management. He holds an MS in chemical engineering and a BA in chemistry from the University of Virginia in Charlottesville, Virginia.
Jason Walker is the principal deputy director of research at IPA. He has led dozens of the exploration and production industry research studies and has developed statistical models and tools aimed at evaluating oil and gas developments around the world. His areas of expertise include reservoir appraisal, well construction, cost and schedule benchmarking, project research methods, statistical model development, econometrics/trend analysis, and cost normalization. He holds an M.Div. from Southwestern Baptist Theological Seminary in Fort Worth, Texas, and a BS in integrated science and technology from James Madison University in Harrisonburg, Virginia.