A number of recent studies from the US shale sector are arguing that refracturing is a generally successful practice and that high oil prices make that even more true.
New research from the Eagle Ford Shale in south Texas shows that refractured wells using liners can even outperform new wells benefiting from more modern completion designs.
The developers of the liners and packers specially designed for refracs are also reporting increased interest for their technologies as the industry leans toward more sophisticated mechanical isolation techniques.
In terms of the very lowest-hanging fruit, it is believed operators in North Dakota’s Bakken Shale are sitting on some 400 openhole wells that if refractured would generate in excess of $2 billion—and that’s at $60/bbl vs. this year’s average oil price of almost $90/bbl.
But despite the apparent progress and size of the prize, it does not appear that US shale producers are any closer to refracturing on a large scale than they were 5 years ago.
Out of all the US horizontal well stimulations performed through September of this year, a little over 2% were refracs. The figure comes from Rystad Energy which identified in public data roughly 200 refractured wells out of the 8,900 total stimulations from January to September.
Most of these refracs were in the Permian Basin spanning Texas and New Mexico and involved wells of a 2018 vintage or earlier. And most of the operators active in this space completed just between 1–4 refracs during the reporting period.
The consultancy expects that as more data filters in, the count will be around 400 refracs by year’s end. That would likely be a little over 3% of total completions and roughly in line with last year’s final tally of 409 refracs. On a percentage basis, 2022 might also look similar to the 2018 peak of 570 refracs, or 3.3% of that year’s 17,000 completions.
Justin Mayorga, a senior analyst of shale research for Rystad, said the data reflect that a healthy level of activity exists in the refrac space—but there’s little chance the 2018 record will be broken anytime soon.
“It’s a very niche market,” he said. “The companies that are doing it are probably going to continue to do it, but I don’t think refracs are going to explode in numbers next year. I see stable activity that is very similar to this year’s 2–3% of total completions.”
One reason refracs hold just a fraction of the overall completions market is because they’ve only been able to establish a limited business case in a sector that remains laser-focused on bringing in new wells. To this end, many operators active in refracturing describe how they use the technique not to boost production from older wells but more so to protect the outcomes on new child wells that share the same pad.
But the biggest obstacle facing greater refrac activity in the US, according to Rystad and other analysts, is the lack of spare pumping horsepower.
“In the short term, there is just not enough equipment,” to boost refracturing numbers off their current base, said Matt Johnson, the CEO of Primary Vision, which tracks US frac fleets.
He added that with about 290 fleets running in the US, the pressure-pumping market is only about 20 fleets away from full utilization. Johnson also said that not much, if any, added horsepower is likely coming to the US market next year.
This barrier to entry is compounded by the long-term contracts that pumping companies are demanding in the wake of the pandemic-driven attrition they suffered 2 years ago. Such contracts are considered prohibitive to the launching of small-scale pilots and dedicated refrac campaigns which are needed to gain new entrants.
While acknowledging there remain a number of challenges to wider uptake, proponents maintain that there are huge numbers of candidates spread across the big onshore US basins that are likely ripe for refracturing. Eventually, as they see it, the industry will pivot in a more concerted way to rejuvenating this inventory which may add up to tens of thousands of wells.
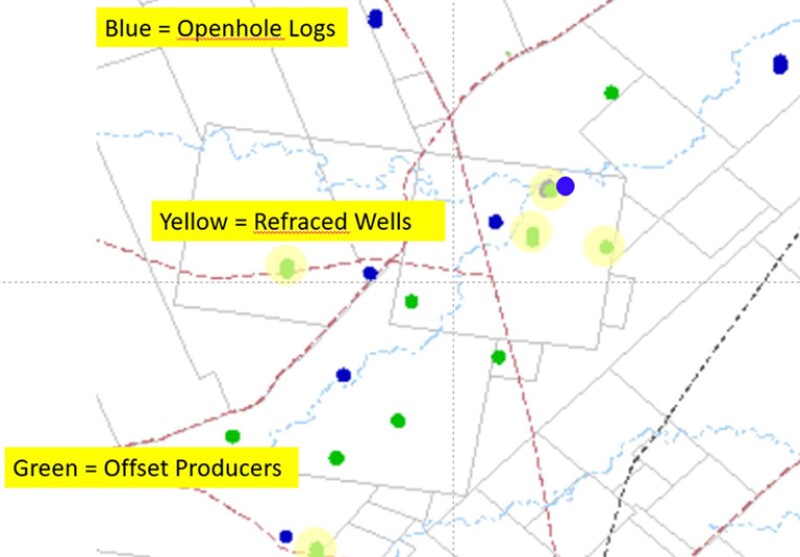
The Key Is Untouched Rock
Among those expecting a shift toward higher rates of refracturing to take shape at some point in the not-too-distant future is Robert Barba, a longtime completions consultant and CEO of Houston-based Integrated Energy Services (IES).
In summing up the reasoning for his optimism, he said, “We are seeing higher recovery factors on refracs—cumulative oil plus the estimated ultimate recovery (EUR) of the refrac—than we are in new wells.”
This conclusion is drawn from a paper Barba coauthored with small private operator Armor Energy and presented at this year’s Unconventional Resources Technology Conference (URTeC).
In URTeC 3724057, Barba et al. share a case study from the Eagle Ford Shale in south Texas that involved five refractured wells that had a combined average post-refrac EUR of 13.2%. This is compared with seven new infill wells with modern completion designs that averaged an initial EUR of 7.4%.
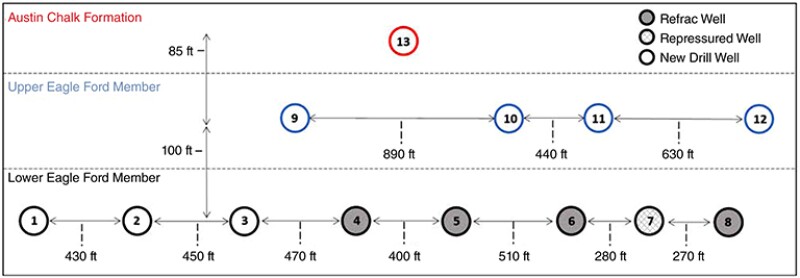
Barba emphasized that the outperformance of the refracs is “a flag that we are probably seeing fracture reorientation.”
Not everyone in the industry is sold on the impact of this concept, but it boils down to this: as the reservoir depletes and pore pressure drops, fractures from a refrac will grow into a new direction and tap previously inaccessible portions of rock.
One implication the authors from IES and Armor raised is that despite the presumed advantages a modern completion offers, fracture reorientation means a refrac can increase stimulated reservoir volume “beyond what is achievable in a new completion.”
While not directly addressing the topic of fracture reorientation, more support of the all-important idea that refracs are accessing untapped rock was provided at URTeC by Devon Energy.
The Oklahoma City-based producer investigated the effectiveness of refracturing in the Eagle Ford and confirmed that it can generate new fracture networks instead of simply opening up old fractures from the initial stimulation. The study was helped by funding from the US Department of Energy and the Gas Technology Institute.
This is a critical area of study since reactivating existing fracture networks is considered to offer far less upside. In the case study highlighted during what was a non-paper presentation at the conference, Devon staff reported the refracs lifted recovery factors on its research pad from 17% to 25%. (On such high rates, the Devon team noted the unit ranks amongst one of its most prolific in the Eagle Ford.)
This work was aided by the use of fiber optics and other technologies that were able to distinguish between the fractures created during a primary completion and those from the subsequent refrac.
Hinting at Devon’s growing confidence in refracturing, the company noted in its deal this year to buy smaller player Validus Energy that it would be gaining about 300 new drill locations along with 150 refrac candidates. The latter figure is something not often touted in shale acquisition announcements.
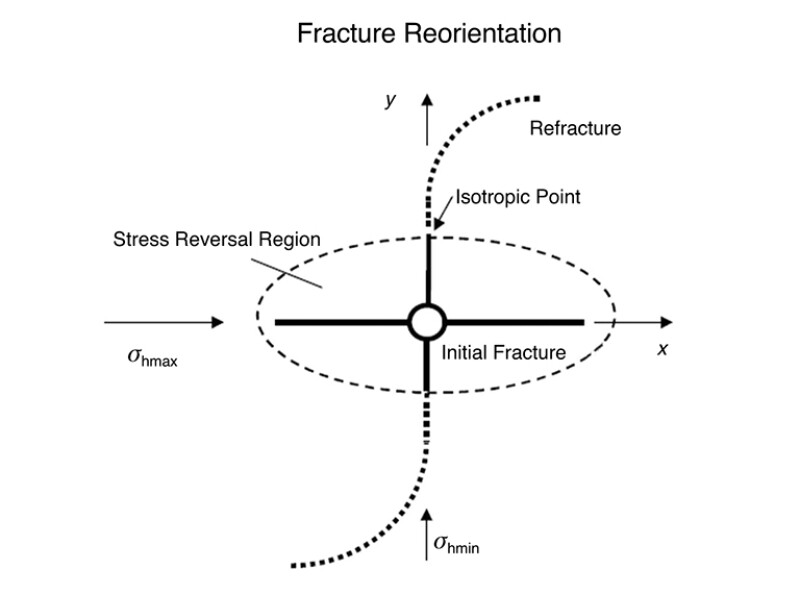
Are Liner and Packer Refracs the Way?
As the future of refracturing depends on a number of factors, it’s important to remember that not least of them is the technology landscape. On this topic, a number of evolutionary steps have been taken in recent years which now offer operators a big menu of options.
And just like anything in life, with refracs you tend to get what you pay for. The smallest investment involves a bullhead refrac which can range between $500,000 and $1.5 million depending on location, overall frac efficiency, and amount of chemical diverters used.
The complaint most often lodged against bullheads—also referred to as the “pump-and-pray” approach—is that they tend to achieve poor perforation isolation or none at all which leads to partial and very heel-biased stimulations.
The most reliable way to successfully access previously unfractured rock is increasingly viewed as using mechanical isolation—refrac jargon for liners and packers.
A joint study IES and Primary Vision published this year found that liner refracs tend to deliver about twice the profits of bullheads while also delivering far superior parent-child defense capabilities than do diverter-based bullheads.
Barba put it bluntly in saying that “If you want to maximize net present value, you clearly want to use a liner.” However, he emphasized that bullhead refracs still deliver positive economics and because they are cheaper may be the go-to option for less‑capitalized operators.
This more sophisticated route of liner refracs comes with heightened risks over bullheading since it involves running tools downhole and drives costs up to around $3 to $4 million per well.
Houston-based Vertice Oil Tools is a developer of refrac liners and other tools that have been used in refracs across the US. The company has seen an increased number of operators approach it in recent months to complete their due diligence on liner refracs.
This is according to Alex Goodwin, director of sales and marketing for Vertice, who said high oil and gas prices are driving a renewed interest in refracturing.
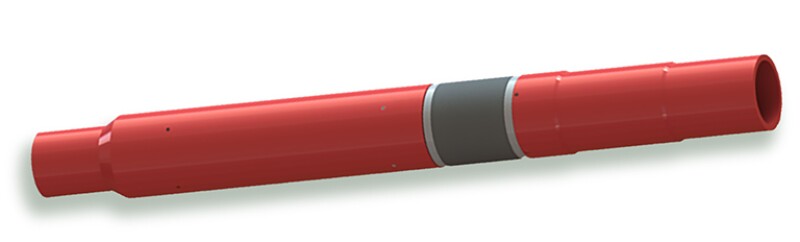
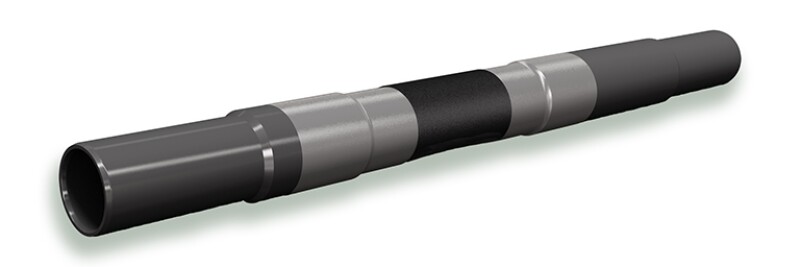
Vertice is representative of a cottage industry that has sprouted up to create liners and plugs specifically for refracturing.
“A lot of people in the refracturing space have tried to take an existing liner system that they might run into new wells and adapt or modify it for refracs,” explained Goodwin. “But the big challenge there is that the well architecture doesn’t really afford a lot of space to put the tools back inside legacy wells.”
He added that the 5½-in.-diameter casing strings commonly used across the US shale patch are a sign that few companies were counting on reentering these wells for a second go at it.
That has dictated the goal for refrac liner makers to achieve an outside diameter small enough to fit into a narrow casing but with a large enough internal diameter to run plugs, perforation guns, and to pump fluid and sand at high rates. “That’s our story and why we build liners specifically for these wells which are nonstandard casing sizes of 4 in. and 3½ in. in diameter,” shared Goodwin.
Generally speaking, such diameters are the minimum needed to avoid too much pipe friction and achieve pumping rates above 50 bbl/min.
Aside from offering a high degree of isolation since they cover virtually the entire lateral, Goodwin also said liner refracs have an advantage in being operationally consistent.
“There is not a lot of complexity involved once you establish the process,” he said, noting that the biggest part of the learning curve comes with properly cleaning out old wellbores that in some cases haven’t been entered for a decade. Goodwin added that special attention to the installation is required to ensure total isolation is achieved from the top of the liner at the kickoff point in the heel.
All this is to remind that refracs require a different set of procedures than initial hydraulic fracturing jobs, and operators as well as tech developers must go through the paces.
One of the reported challenges of running liners has been the cement jobs that must squeezed into the small space between the old casing and new steel. Gaps in the cement risk lowering the efficiency of a refrac by allowing fracturing fluids from one stage to flow back into previous stages.
This issue has created an opening for an innovation from MorphPackers. The UK firm with offices in the Houston area makes liner hangers for cemented refrac liners but it is also offering operators expandable steel packers that forgo the use of cement. Instead, these packers form metal-to-metal seals against the inside of a well’s casing to provide isolation during the refrac.
In what is a familiar theme, MorphPackers has built its packers with an internal diameter (ID) of 4½ in. to match liners and with an external diameter of 5½ in. to fit inside existing casing.
“That slim design allows us to maximize the residual ID—so we sacrifice the ID less than some of the other technologies, which then allows the operator to refrac at a higher rate, which is critical to getting better post-refrac results,” said Alfredo Sanchez, CEO of MorphPackers.
Sanchez added that typical packer refracs might need 30–40 units to cover all the existing stages. Though that means running a lot of packers downhole, he said it comes at a lower cost than running heel-to-toe liners and is operationally a simple process.
Once all the packers are run to depth and covering open perforations, a ball is dropped and pumped to a seat at the toe of the liner. “Then we pressure up against it and all of the packers are going to expand and set simultaneously in one single pressure event,” said Sanchez. “There are no other moving parts and nothing is shifting around.”
Bringing Refracs to the Masses
When asked what might turn the tide in favor of more refracs, Sanchez said one thing that excites him is the increasing understanding of what makes a good refrac candidate, and related to that, the slowly growing embrace of the fracture reorientation concept.
“Most of the people I talk to believe that it is real and that it does happen—which is good,” he said. “Now, how significant is it? I think that is still up for debate.”
This underlines something key to the topic of refracs which is that another barrier involves the shale sector’s asymmetry on knowhow and experience. This goes for the geomechanics at play as it does for the proper selection of refrac technologies and knowing which wells to use them in.
To help solve this problem Barba’s IES has recently teamed up with Primary Vision to compile data from dozens of other refrac projects in the Eagle Ford.
A combined report the firms published earlier this year suggests the results of the URTeC case study by Barba et al. are widely repeatable across the play and have become the basis for a new joint industry project (JIP) the companies are seeking to launch soon.
While Johnson of Primary Vision is on the record about the constraints of the pumping market, he nonetheless is hopeful that refracturing is poised for another look by operators who are increasingly running through well inventories.
He also said, based on the early screening data he’s seen, that the Eagle Ford opportunity likely pales in comparison to that found just a few hundred miles to the northwest in the Permian.
“In the Permian, we don’t have thousands of wells, we probably have tens of thousands of wells that have these refrac opportunities,” he said.
But identifying and acting on this massive potential is going to require a lot of homework to identify the strongest candidates. The JIP hopes to help companies operating across major US basins figure that part out.
Taking it back to the Eagle Ford, IES and Primary Vision point out that earlier this year, 53 of the play’s 86 operators have not run a rig all year. For these operators, refracturing could be a capital-efficient way to improve production while remaining rigless.
Johnson said the potential JIP is likely to look into how operators can optimize their completions schedules to fit more refracs into periods of downtime. “Or does it make more sense to carve out a separate unit that just focuses on refracs? That is one of the questions right now,” he said.
He also pointed out that publicly traded operators likely need more confidence in refracturing results before they alert investors to larger campaigns. A JIP could help in this regard by enabling participants to pool data and accelerate their learnings based on the results.
Johnson noted that while production data are publicly available, completions design data often lack specifics. “And completions data are just as important as the production data so we have to be able to evaluate that as well,” he said.
Billions in the Bakken
While Texas remains the center of most refrac activity, researchers have identified some very valuable low-hanging fruit in North Dakota’s Bakken Shale.
In URTeC 3723732, authors from the Energy & Environmental Research Center (EERC) at the University of North Dakota reviewed the production results of the roughly 270 refractured wells in the Bakken up to 2019. In using this data to scout for future candidates, one of the biggest findings from the study is that the Bakken has about 400 early-generation horizontal wells that are potential refrac candidates. Though this is based only on preliminary screening and not a recommendation, the EERC estimates the value of refracturing all those wells totals more than $2 billion.
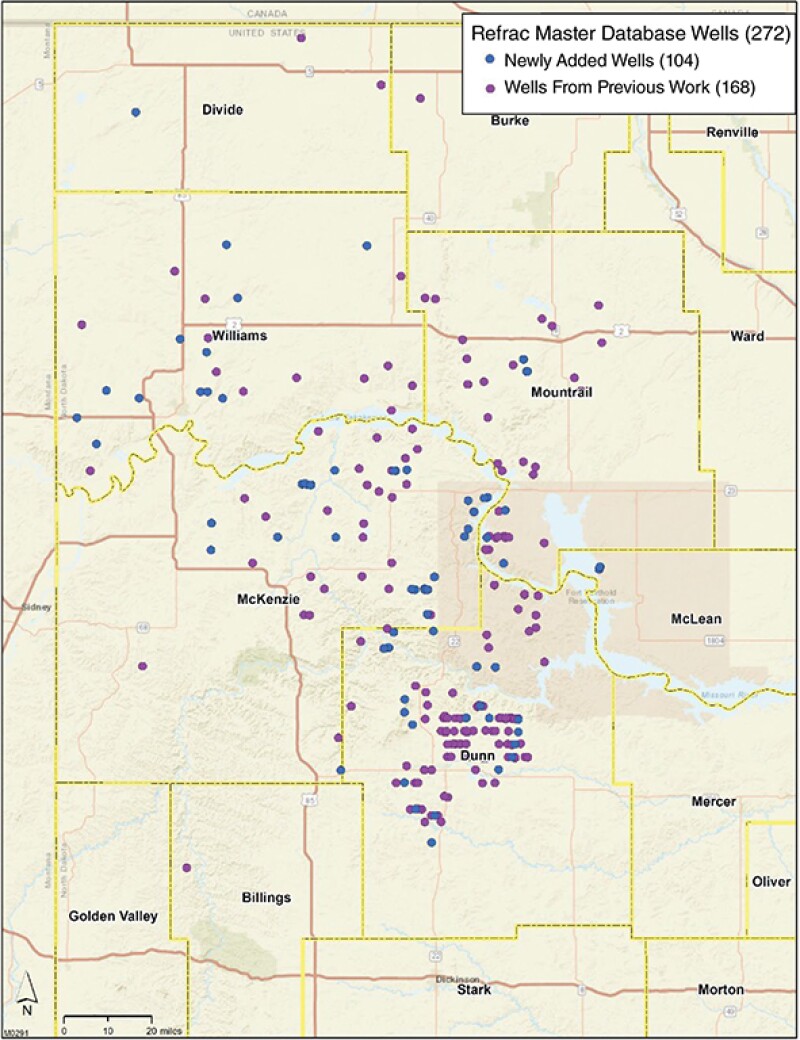
That figure includes deductions for royalties and taxes and is based on $60/bbl oil prices, reflective of when the paper was written.
Today of course, the value of these 400 wells is theoretically much greater thanks to prices of around $90/bbl. Furthermore, the EERC’s conservative assumption is that 2% of the existing production from these wells could be lost to botched refrac jobs, which is always a risk.
Paper author and EERC researcher Chantsalmaa Dalkhaa said the early-generation wells are defined as openhole wells with usually a single fracture stage.
“Most of these wells haven’t really depleted,” she explained. “So, if you refrac these wells, you could add a lot more stages and produce a lot more oil and that is reflected in the economic estimates.”
The focus on openhole wells is simply due to the outsized potential they have compared with cased wells. The EERC review showed openhole refracs generated a median incremental EUR of 340,000 stock-tank barrels while cased‑well refracs averaged 175,000 additional barrels post‑refrac.
Additionally, gas/oil ratios (GOR) dropped by an average of 10% in the 3 months following refracs of openholes. Almost no drop in GOR was seen in the cased-hole refracs, suggesting that openhole refracs in the Bakken are more successful at accessing untapped slices of reservoir rock.
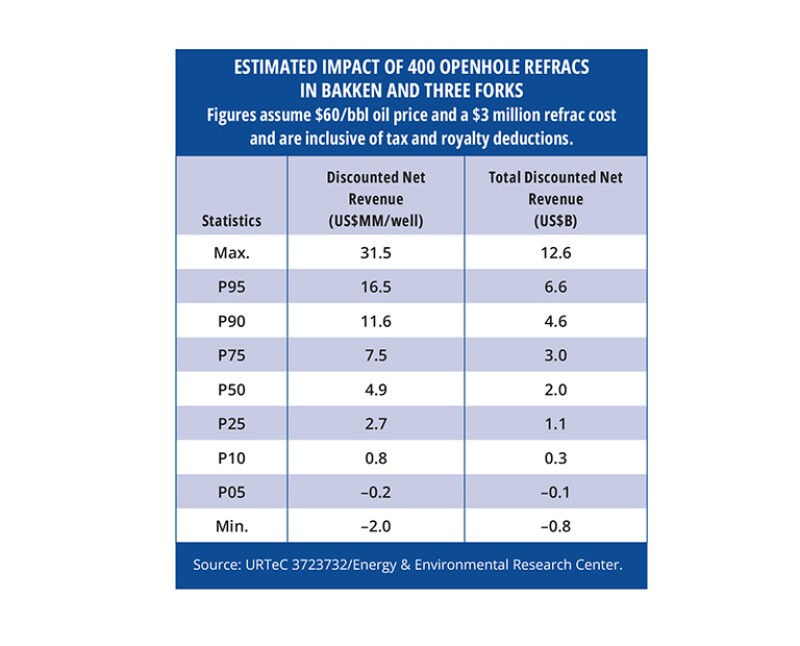
The EERC paper also raised some other interesting points including that there appear to be beneficial impacts of refracs on offset wells. The Bakken and Three Forks formations are understood to be highly connected, which may help explain such advantageous outcomes that are likely harder to come by in other tight basins.
In describing this interaction as “secondhand refracturing,” the EERC researchers found that about 70% of offset wells adjacent to a refractured well saw production uplift as a result. This is based on the post-refrac results of 161 offset wells near the Bakken’s top 50 highest-producing refracs.
One of the reasons the EERC took on its refrac study was to promote the maximization of state resources—something embedded into its research mandate.
Paper coauthor Nick Azzolina, also the assistant director for applied AI/ML at the EERC, stressed that beyond all these nuances the big picture is that a tiny fraction of the Bakken’s horizontal well population has been refractured so far.
The reason for this comes back to the idea that few things compete for capital like a new well.
“I think there’s more certainty on the outcome of drilling out a new drilling section unit than the outcomes of going back in and refracturing,” said Azzolina. “But I think the argument here is that there are 20,000 holes in the ground and that could be viewed as an opportunity.”
An evolution the researchers at the EERC are looking for is that Bakken operators shift from thinking mainly about refracturing parent wells on infill pads and toward pads entirely made up of parent wells.
“That is part of what makes an optimal DSU [drilling spacing unit]—seeing how much oil you can squeeze out of the whole volume of the DSU,” with refracturing, he said, adding that “one well is just one out of perhaps six to as much as 16 depending on the DSU.”
For Further Reading
URTeC 3724057 A Comparison of Latest-Generation Frac New Well and Refrac Results with Evidence of Refrac Reorientation by Robert Barba, Integrated Energy Services Inc; Justin Allison, Armor Energy LLC; Mark Villarreal, Enventure Global Technology.
URTeC 3723732 Refracturing in the Bakken—An Analysis of Data from Across North Dakota by Chantsalmaa Dalkhaa, Nicholas A. Azzolina, Alex Chakhmakhchev, Bethany A. Kurz, James A. Sorensen, Charles D. Gorecki, and John A. Harju, Energy & Environmental Research Center University of North Dakota.