Petrobras, one of the world’s top offshore operators, has shared new information about how it used an ultradeepwater rig in a place where it was never intended to work—in shallow water.
What makes its recent subsea campaign novel is that the Brazilian national oil company avoided mooring the rig and instead relied on dynamic positioning (DP).
Two key pieces of technology made this possible. The first is called a blowout preventer (BOP)-tethering system which sits on the seabed and absorbs much of the load being placed onto the wellhead structure. The second is a digital twin software that determines the safety of the rig’s position during drilling.
Petrobras is not the first to accomplish such a feat in depths less than 2,000 ft. But it is among the few to recount its learnings in multiple technical papers as it did at the recent Offshore Technology Conference (OTC) in Houston.
The fresh insights surrounding the Petrobras projects stem from an initial well drilled and completed 2 years ago with a sixth-generation drillship, the Norbe VIII, owned by Brazilian contractor Ocyan.
The new well is in the Albacora field within the Campos Basin and was the first of several planned to be drilled or plugged and abandoned by Petrobras in DP-only mode.
Over a 16-day period in May 2020, the Norbe VIII worked in water depths of about 1,475 ft where it successfully tapped into a pre‑salt oil reservoir with a total depth of more than 16,000 ft.
For both firms, the project in the Campos Basin marked a first.
Never before had they used a rig in DP-only mode at such shallow depths, which amounted to about 15% of the rig’s maximum depth rating. Following the first well, Petrobras drilled at least one more in June 2021 in DP-only mode.
Notably, Petrobras was in the midst of selling off the Albacora field during its experimentation with DP-only shallow-water drilling. The mature asset was discovered by the state-run operator in 1984 about 75 miles from the coast and has been producing from post-salt reservoirs for the past 35 years.
But earlier this year, the company said it was hoping to fetch a higher price based on better‑than-expected reservoir tests from the deeper pre‑salt target it drilled in May 2020.
Why Go Shallow With Big Rigs?
Per its new papers, Petrobras considers the water depths of its DP-only projects to be “shallow;” however, other definitions hold that between 1,000 and 5,000 ft counts as a “midwater” depth. That said, the system Petrobras and its partners adopted is designed to work at depths of slightly less than 500 ft, which is shallow by anyone’s definition.
The operator and its partners offer several reasons for why DP-only has become an attractive strategy in at least one of Brazil’s shallower fields:
- Many moored semisubmersibles were scrapped or cold-stacked in recent years, leaving operators to find ways to use DP-enabled rigs for a variety of well operations.
- Traditional mooring operations can consume several days of rig time and incur additional costs with the contracting of necessary support vessels.
- DP-only helps justify drilling and well interventions in mature areas congested with subsea pipelines or protected coral reefs and marine life.
- Tethering enables newer-generation rigs with the heaviest BOPs to work on older and smaller wellheads with lower load tolerances.
Helping to complete this picture, especially the economic piece, is that Petrobras began considering its project during a prolonged period of depressed rig rates. Today, those rates are rising sharply as the world grows eager to find new sources of oil and gas.
This is quickly eroding price parity between the different asset classes and may also shrink the industry’s appetite to test the limits of a deepwater rig’s original design parameters.
All that suggests the work off Brazil may not signal an industrywide trend and is instead a demonstration of innovative opportunism. But if nothing else, what Petrobras and its partners pulled off over the past 2 years has helped redefine what has historically been considered practical or safe.
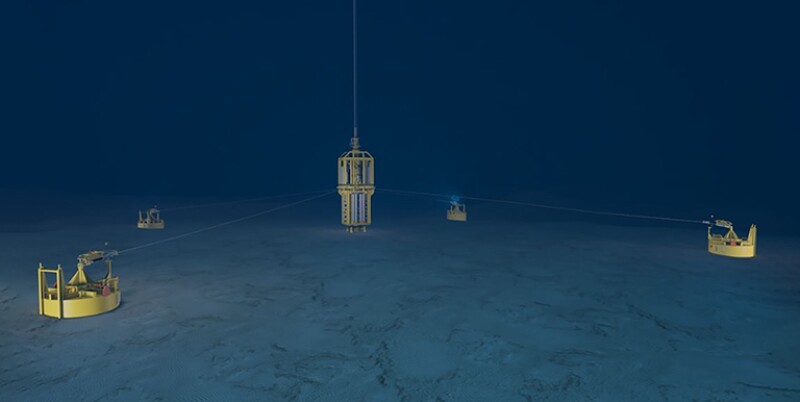
Conquering DP-Only Mode
While presenting the case study, paper coauthor Rafael Fulco, a petroleum engineer for Petrobras, highlighted that mooring operations require multiple support vessels and about a week to complete.
In contrast, Petrobras was able to install its tethering system using just one supply boat, and the final hookup to the BOP was done in a single day. Importantly, that last step did not incur any additional rig time since the operation coincided with pre-drill BOP testing.
“So, you save 7 days of operation of the rig, and you save on the day rates of the boats,” added Fulco.
One reason we have not seen such operations done more often is because using deepwater rigs in DP-only in shallow water (or the low end of the midwater range) is not a straightforward operation.
The rule of thumb is that drillships and semisubmersibles must hold a position directly over the wellhead that equals no more than 5% of water depth. At depths of a mile or more, this means DP rigs can enjoy a wide area—known as a “watch circle”—to move around inside without the risk of bending the drilling riser to dangerously sharp angles.
As the limit is approached, the rig must initiate its emergency disconnect sequence to avoid serious damage to the riser, BOP, or wellhead.
The other major concern involves placing too much weight onto the BOP and the wellhead. At shallow depths, this risk is elevated with modern drillships that are far heavier than moored rigs and do not have the load-transferring advantage inherent to jackup rigs.
In sum, if the bending of the riser becomes too excessive or loads are too high, it becomes impossible to safely activate the rig’s emergency disconnect system and sail off location in a controlled manner.
To mitigate these risks, Petrobras and its drilling contractor relied chiefly on two innovations: a BOP-tethering system and a real-time marine-riser-analysis software.
They are the focus of a trio of papers presented at OTC that explain how Petrobras prepared for a multiwell campaign in DP-only.
In OTC 31980, authors with the Brazilian national oil company share how they repurposed a subsea technology originally developed to reduce wellhead fatigue by keeping BOPs from moving around too much during drilling operations.
The technology is called a BOP-tethering system and in terms of innovation, Petrobras notes that it had to create a system that was larger and stronger than the versions used simply to avoid wellhead fatigue.
“The system is very simple,” said Fulco. “We have the anchors on the seabed. We have a tensioner—that is the hardware that will pull the cables—and we make it tight with tension.”
It may be simple to describe, but Petrobras faced a number of challenges as it learned how to install the tethering system. And while it did not share dimensions in its papers, the size of the suction pile anchors proved demanding.
The company shared that due to the size of its newly built anchors that they had to be transported on a flatbed trailer around Rio de Janeiro on roads with enough clearance. This meant instead of using the shortest possible route from factory to port of about 25 miles, the one-way trip was closer to 110 miles.
Petrobras added that its initial supply boat had enough deck space to hold two anchors but that their weight meant only one could be transported at a time. The result was that it took more than 2 weeks to get all the anchors to location for the first well.
Once they were in place, Petrobras was ready to transfer many tons of load off the BOP stack and onto the tethering system. This was done in stages—starting with 4 metric tons, then to 12, and ultimately 20 metric tons.
Without the tethering system, the radius of the watch circle in which the DP drillship needed to maintain station would have been about 13 ft. This is the big problem solved by the tethering system given that the rig’s operating procedure called for an emergency disconnect if a radius smaller than about 50 ft was breached.
With the tethering system, the minimum distance the rig could drift off the wellhead’s position expanded to just over 75 ft.
But marine conditions can shift quickly and so Petrobras and Ocyan needed a way to verify what defined a safe radius. For that, they turned to a real-time riser-monitoring software developed by Houston-based engineering firm Stress Engineering Services.
The software is the focus of OTC 31709 and is described as a digital twin model of the riser. It accounts for changing environmental and operational conditions and delivers a new watch circle estimate each hour. The software was not a technology that Petrobras had relied on before.
“Usually, this is a static analysis we do in the office. We consider the worst-case scenario, and the main parameter is the water depth,” explained Fulco, adding that this is justifiable in the ultradeepwater given the large errors of margin where “we have a large circle and we have a big [load] limit.”
Of course, those advantages disappear at shallower depths, hence the need for the software.
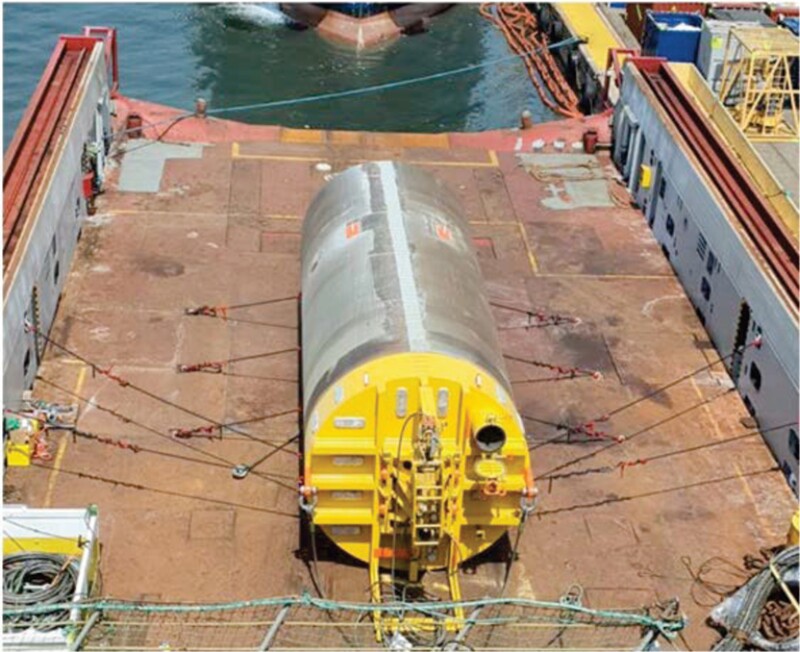
Climbing the Learning Curve
A third paper covering the Petrobras development, OTC 31859, offers some lessons learned from its initial DP-only project and a follow-up drilling operation completed in June 2021.
Drill a tophole first. Petrobras and its partners (Ocyan and Oceaneering) concluded that lost time could be mitigated by drilling a tophole prior to installing the suction anchors. This is in case the tophole is lost and/or the tensioner cables are buried by drill cuttings.
Have a backup. In the 2021 operation, one of the tensioning-system components called a well load relief (WLR) unit failed. It was believed that the equipment was jammed as the cable did not run through the system properly. A software that might have mitigated this issue was not being used during the failure. But in case of these events, it is advised that a backup WLR be available on the rig and that pilots of remotely operated vehicles (ROV) handle the cabling system with as much care as possible to avoid damage that may lead to jamming.
Use the drillstring. When a faulty tensioner needed to be replaced, Petrobras and its partners did not have a support vessel available to do the job. Instead, they devised a procedure to use the drillstring and an ROV to recover and reinstall a new tensioning system. The fix is described in the paper and required the crew to assemble an ad hoc bottomhole assembly to lift the defective tensioner up to the rig’s moonpool.
Remote monitoring. Despite extensive planning, the operation saved time and enhanced overall safety by relaying live video to teams onshore that could convey advice and guidelines to the rig crew.
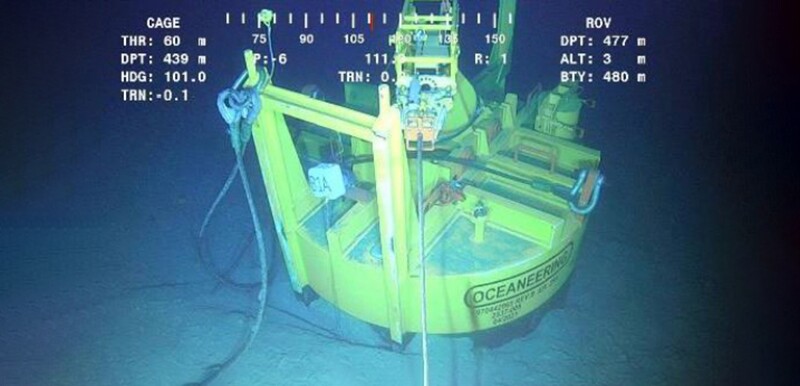
A Buyer’s Market Opened Up New Options
It would be difficult to see how the Petrobras projects, along with some other similar examples, would have materialized if not for the depressed state of the rig market during the past few years.
“There was excessive oversupply of offshore rigs and rates had plummeted,” summed up Leslie Cook, a principal upstream supply chain analyst for Wood Mackenzie. She was referring to the effects of the last downturn in oil prices which bottomed out in 2016. To the detriment of drilling contractors’ margins, operators saw their rig options expand.
Cook pointed to the Zama exploration well drilled in 2017. Drilled by Houston-based Talos Energy in the Mexican side of the Gulf of Mexico, Zama ended up being one of the world’s biggest shallow water discoveries made in the past 20 years. It later became equally well-known for controversy as Mexican regulators stripped Talos of its operatorship in favor of national oil company Pemex.
But initially, Zama stood out to rig watchers because it was explored using a semisubmersible in just 550 ft of water. And though the rig operated in DP mode, it also used a mooring backup—making it less complex as the more recent Petrobras work.
The Talos-contracted semisubmersible nonetheless showed how operators could take advantage of a low-price environment.
“Talos was able to have more deck space, higher deck load, and they got it fairly cheap,” said Cook, adding that the day rate was almost as low as a high-spec jackup, or around $150,000 to $180,000 per day.
Also in 2017, BP and Maersk Drilling drilled a well offshore Egypt in about 935 ft of water. This project was done in DP-only mode, making it much more similar to the Petrobras effort that followed 2½ years later.
BP contracted one of Maersk’s sixth-generation rigs for the job, marking the first time either company had attempted a DP-only operation at such depths. Maersk would note after the job that its latest-generation rigs were originally designed to operate in DP-only in depths no shallower than 1,500 ft.
In circling back to Petrobras, its decision was influenced not just by low day rates but the lack of less capable rigs. The operator’s contracted fleet today almost entirely comprises deepwater drilling rigs—drillships and semisubmersibles. There are very few jackups and only a single moored rig in the region, according to Wood Mackenzie’s latest data.
Among other things, this serves to highlight that moored rigs are nearing obsolescence, or at the very least, becoming an endangered species.
Cook said there are only 44 moored rigs left anywhere on the planet and that only 32 are currently active. This translates to a marketed utilization rate among these rigs of just 63%, which is the lowest figure among all rig classes globally.
“The reason is that the average age of this [moored] fleet is 40 years old—these are the oldest rigs of the global fleet, and they are getting aged out now,” she said.
Cook added that inactive moored rigs are mostly owned by national oil companies in China, the Caspian Sea, and India. This means they are not even considered to be part of the globally marketed rig fleet and may be sticking around only due to the sunk cost they represent.
For Further Reading
OTC 31980 Changing the Game: DP Rig in Shallow Waters Using BOP Tethering System and Real-Time Riser Analysis by Magno Almeida da Silva, Rafael Rodriguez Fulco, and Marcos Correa Weidlich, Petrobras.
OTC 31859 Challenges and Lessons Learned on the First Use of Tethered BOP in a Major Operator in Brazil, Including the Replacement of the Tension System Using the Rig Drilling String by Cristiano Bernabé Cardoso, Magno Almeida da Silva, João Marcelo Mussi Baptista, Janaína Barreto Santos, Sérgio Carlos Kupski, Otávio Caniçali, and Matheus Rodrigues Resende, Petrobras; Daniel Costa and Danielle Rocha, Oceaneering; and Marcos Vinícius Sampaio Santiago, Ocyan.
OTC 31709 A Digital Twin for Computing Dynamic Watch Circles on a Dynamically Positioned MODU by Sezgin Kucukcoban and Daniel Joseph Kluk, Stress Engineering Services Inc.; Rafael Guimarães Pestana and Magno Almeida da Silva, Petrobras; Daniel Mattos Gonçalves da Costa, Oceaneering International; Rodrigo Chamusca Machado, Cristiano Venancio Xavier, and Marcos Vinicius Sampaio Santiago, Ocyan SA.