Shell had a problem. It had just spent billions to bring its Appomattox find on line in the deepwater Gulf of Mexico (GOM). That development featured the oil giant’s eighth and largest floating platform in the region. The host semisubmersible weighed 125,000 metric tons—more than the largest aircraft carrier.
Shell lauded its ability to reduce project cost by 40%, based on experience gained from the development of its previous four-column production platforms in the US Gulf, including the Olympus tension-leg platform. It would transfer these learnings to its next project—the Vito find in about 4,000 ft of water, 150 miles southeast of New Orleans. The field could hold up to 300 million BOE.
At the same time the plans for Vito were being laid out, shale projects leapt to the forefront in the competition for capex dollars, and due to the comparative investment, they were winning. Industry success across the nation’s shale plays helped flood the market with oil, forcing the price per barrel down. Suddenly, spending big money on megaprojects offshore had lost much of its luster. For the US Gulf to reclaim at least some of its competitive advantage, fields could no longer be developed with massive, high-dollar facilities. A management mandate dictated that a new minimal, repeatable solution be found. After several years of study, a favorite emerged.
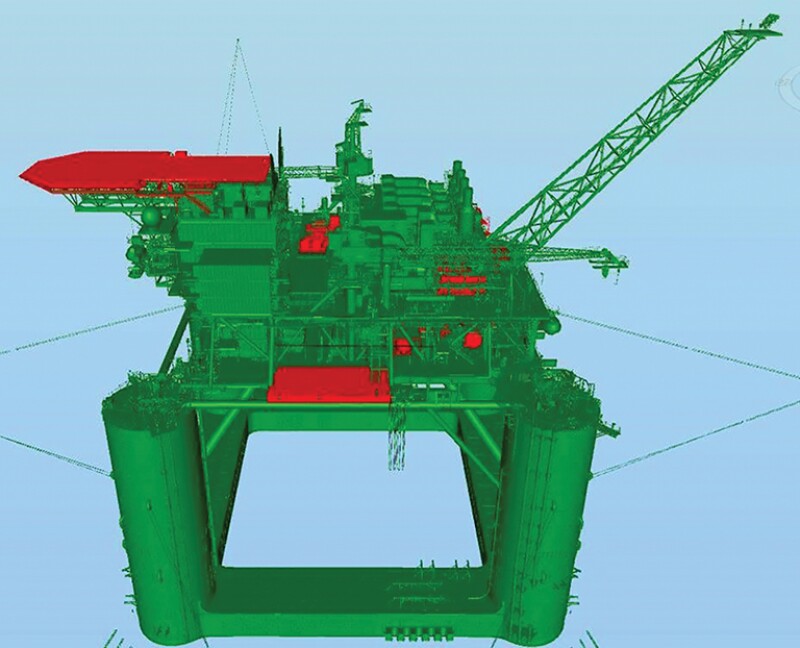
“The original concept of Vito was much larger,” said Kurt Shallenberger, Vito project manager for Shell. “The development was probably similar in size to the Appomattox project that Shell recently completed—a 40,000‑ton topsides, and a 50-year field life with a sizable gas-reinjection component to it.”
Shell’s method for arriving at the new development scheme was dubbed “Minimal Technical Scoping”—the company would start with the absolute minimum scope and then justify additions upward. The project mantra was “Simpler is safer.” The results were a simplified topsides design as well as streamlined mooring systems for the host facility.
“The redesign took it down to what I call the sweet spot of semisubmersibles—around a 10,000-ton deck,” said Shallenberger. “You had seen examples of that with LLOG’s Delta House, Independence Hub, and others like that. That was the sweet spot to where multiple fabricators can build it, multiple yards can integrate it, multiple companies can install it—and you can generally get 100,000 bbl a day through it. Now you’re in a competitive environment for all the vendors rather than just the one guy in the world who can do this. That’s what really created the opportunity for Vito. We shrunk the size and scope down to a point where it could get to a breakeven price that is competitive with the onshore folks.”
According to Shell, the breakeven price for their minimal floater design is less than $35/bbl.
Shell locked up key vendors for Vito. Jacobs Engineering Group carried out the detailed engineering and front-end engineering design studies for the Vito topsides. Sembcorp would build the host and integrate the topsides and hull at its Tuas Boulevard yard in Singapore.
The success on paper got the halls around Shell’s Houston and New Orleans offices buzzing. If they could apply this to Vito, and it worked, what could that mean for other projects in the pipeline? The operator had several discoveries in various stages of maturity, but the one that stood out in the queue was Whale—a 490 million BOE find in over 8,000 ft of water offshore Texas. While Vito’s transformation didn’t start out as a potential “design one, build two” scenario, that was the possibility that started to take shape.
“The challenge really was put there by our management—can you make the Vito host work?” said Shallenberger. “If you just picked it up and put it over there … could it work? Yes, you can flow oil through it. It’ll separate like a bottle of Italian salad dressing, and then you pump the oil and gas to the beach for processing. Now, what are the subtleties of that different reservoir and of that different water depth?”
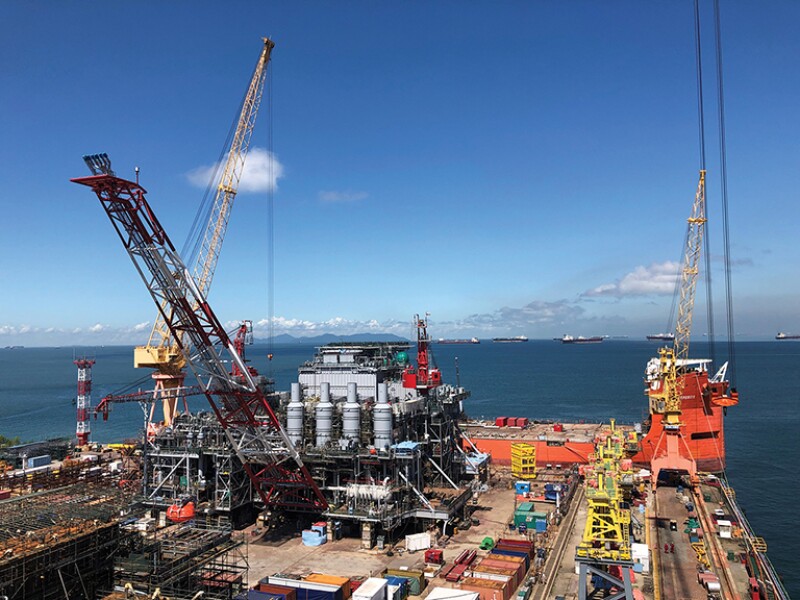
Landing a Whale
With Shell having forged what they felt was a skeleton-key-style solution to unlock deepwater GOM reserves competitively, it came time to transfer that knowledge to another project to see if the concept was truly repeatable. Once Whale was chosen and the team started to dig into the project, Shell would go on record saying that 99% of the hull and 80% of the topsides from Vito could be copied and used on the new project.
Another key driver for the replication plan was the subsurface. While Whale does have more natural gas than Vito, the fluid characteristics and overall reservoir makeup were not too dissimilar. For example, if one had a significant H2S component, that would have greatly impacted the potential for a repeatable topsides design.
“Vito is in about half the water depth of Whale,” explained Oro Awaritefe, Whale project manager for Shell. “That means that our mooring lines are longer on Whale. Our risers are longer on Whale. The points where we attach moorings and our risers needed a slightly different, stronger design than you have on Vito. That gives you that 1% hull difference. On the topsides, I think you can look at two main things. One is gas. We have about 50% more export gas on Whale than on Vito. That changes the size of the compressors and the size of the piping needed. Second, we have longer oil export lines from Whale to the shore, so we need bigger oil-pumping systems.”
The Shell team took those key differences and went to work making the necessary modifications to the established Vito host model. Vito and Whale utilize the same Solar Mars gas turbine drivers for the compression train, but Whale utilizes a larger main compressor. The compressor isn’t 50% larger, however. This is due to Vito using five times more lift gas than Whale. The lift gas must recirculate through the main compressor, which results in a much closer compressor size on Vito and Whale. The difference does introduce different piping configurations and sizes in the gas system.
“While both Vito and Whale utilize the same Sulzer pumps, the electric drivers on Whale are about 60% more powerful to account for the longer distance to shore,” said Awaritefe.
Where the equipment could simply be replicated and used, it was. Of the 69 total equipment packages, 59 (or 89%) were replicated and the same suppliers were used. On the construction side, Sembcorp once again served as the fabricator. Roughly 90% of the same suppliers and subvendors are being utilized.
“This eliminates surprises when you order the equipment,” added Awaritefe. “You know what’s coming, and there are no late-stage design changes. We have the same design contractor, the vendors from whom we buy the equipment, and Sembcorp as the construction company. To a large extent, we’ve shared teams and resources with our sister project, Vito—even our construction team in Singapore. The Shell construction team is one construction team delivering the two projects. We have people replication. We have equipment procurement replication. We have host construction replication.”
The replication allowed Shell to begin cutting steel on Whale within about 2 years of the field’s discovery in Alaminos Canyon Block 772. It also enabled the deliberate concurrent overlap of the concept selection, front-end design, and execution project phases. Other successes in the replication formula included shaving 15 months from the hull engineering duration, 20% of the time usually earmarked for topsides engineering, and 50% of the overall engineering costs.
“We’ve had 75% less engineering rework on Whale than we had on Vito,” added Awaritefe. “We have 70% fewer manufacturing defects because we are asking the same manufacturer to produce the same topsides equipment. Additionally, we have zero repeat topsides equipment manufacturing defects from coming over from Vito.”
Follow the Leader
Shell is nearing the marriage point of the Vito topsides and hull in Singapore. The current plan is for the unit to be underway to the US Gulf Coast at around year-end. It will be brought to Kiewit’s yard near Corpus Christi, Texas, to undergo final commissioning and prep work ahead of a summer 2022 sail-away to the field location in Mississippi Canyon Block 985.
The project’s export lines have been installed and are lying on the seafloor awaiting hookup to the Vito host. All eight planned wells have been drilled and connected to manifolds on the seafloor.
Meanwhile, the final investment decision on Whale was formally taken just this July, with a scheduled first oil date in 2024. The Whale host is roughly 50% complete at Sembcorp in Singapore.
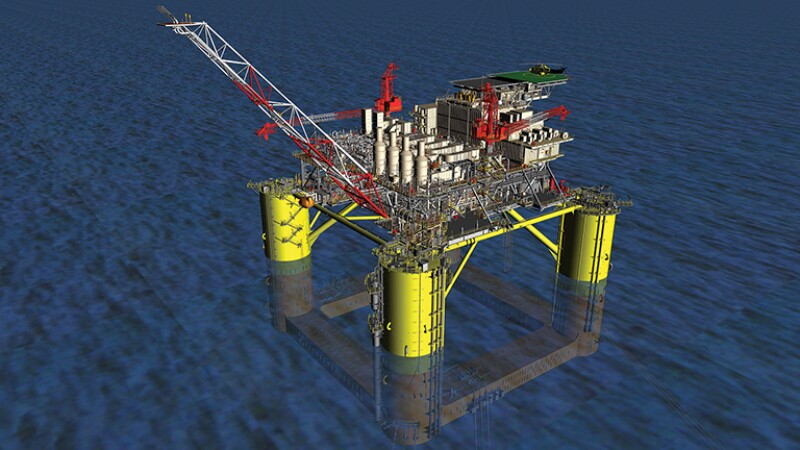
If Whale meets its onstream date in 2024, it will have gone from discovery to first oil in roughly 7.5 years, compared to Vito, which on its current schedule will take between 12 and 13 years. That means producing 100,000 B/D of oil a half-decade ahead of schedule.
“Every businessman will tell you that they want to go from discovery of the resource to generating cash faster and faster every time,” said Awaritefe. “I think that is one of the big positives in terms of our business headline for Whale. It also gives the industry confidence that Shell can do such things, especially when you look at the energy transition and the pace at which we need to move through it.”
COVID-19 did have its impacts on Whale’s schedule. Some host equipment packages for the project were slowed by as much as 6 months. Manpower availability at the host fabrication yard has also been affected. The project has had to factor in the potential for even more COVID-related impacts to host fabrication for the next 6 months to a year, since the impact of COVID on craft availability and productivity is still being felt today.
With a repeatable, low-cost solution in hand, will Shell ever return to the larger host forms that have been such an integral part of the company’s deepwater history? It is hard to tell.
“Host systems come in two sizes—too big and too small—because there’s such uncertainty in the reservoir,” said Shallenberger. “If you come in too small, let’s say like Mars, we are very, very good in our industry at debottlenecking, and you find a way to grow. It’s like buying your first house. You learn how to expand and make do. But if you come in too big, it’s like buying a 6,000-ft2 house as a newlywed. You’re banking that everything is going to go your way for the next 30 years.”
“I think we’re learning as an industry that if you can come in with something that’s adequate—like a Ford F-150—it’ll do 95% of what you want. You don’t need that F-350 with a dually. I think if we can prove these back-to-back, there is a shelf life on these things, like a model of a car. After time, things change. Rules change. Vendor equipment numbers change. The hope is that you could get on frequency, assuming you have good exploration success and that there’s a simple way to bring this stuff on.”
Shell operates Vito with a 63% working interest; partner Equinor holds the remaining 37%. Whale also is operated by Shell, holding a 60% stake; Chevron holds the remaining 40%.