Hydraulic fracturing as it is now executed in North American shale plays may have to be replaced with a much more intricate scheme—one that better matches the complex fabric of tight reservoirs.
The impetus for an engineering overhaul is being forced by the prevalent well-to-well fracture interactions known as frac hits. These events are the subject of intensifying study by US and Canadian shale producers that have attributed them to lowering oil recovery factors from new child wells by 20-40% while inflicting even higher losses on older, yet less productive, parent wells.
How the industry manages the impact of frac hits going forward is likely to define its future growth rate.
“They’re not going away—we’re only going to be drilling more and more child wells,” said Brendan Elliot, a senior completions engineer with Devon Energy, as he advised a large gathering of petrotechnical colleagues that they need to "quantify the risk" of frac hits as early as possible in order to know what to do next.
Elliot provided a rare look into how a large shale operator is dealing with the problem during the opening session of SPE’s Hydraulic Fracturing Technology Conference (HFTC) held recently in The Woodlands, Texas. His outline highlighted the extent to which the Oklahoma City-based producer is revolving its infill development programs around frac hits.
“The things you really want to look at are where the positive and negative events are occurring,” he explained while showing an analysis program that Devon has spent the past couple of years building to visualize those outcomes. The tool, which analyzes data from more than 2,000 frac hit events, has led the company to realize that what determines whether a frac hit will benefit or hurt production comes down to time and production volumes.
While this relationship was not a new learning, Devon has quantified it to 10 months and 100,000 bbl. Once both limits have been surpassed, the expectation is that frac hits will have negative consequences on pad production. Elliot elaborated on how this trend is acted upon using the company’s three-pronged approach. Its component pieces include the design of infill wells, addressing reservoir depletion through pressure management (e.g., repressurizing tactics), and then zooming out to adjust the wider field development program.
Devon Energy’s Frac Hit Mitigation Focus:
- Horizontal completions: Adjusting completion design/strategy on new infill wells.
- Reservoir depletion: Manage pressure and stress to benefit child wells (e.g., preloading or refracturing).
- Field development: Optimize wider program to minimize depletion effects going forward (e.g., sequential/rolling developments).
The sum of these parts is a new playbook for unconventional completions, one that stands in stark contrast to the “cookie cutter” designs that gave rise to the shale revolution. Its methodical approach to decision making is aimed at gaining control over fracture growth and maximizing production from child wells.
This can be done by adjusting fluid rates in a single well scenario, or altering an entire field development plan based on the risk that frac hits pose. In just a few slides, Elliot succinctly linked together years of accumulated knowledge into a workflow that could feasibly be replicated by other companies struggling with the sector's most pressing reservoir management issue.
“These full-life cycle workflows—don’t get me wrong—these will be lengthy processes, and large projects, so we need to improve as an industry,” cautioned Elliot. “Every mitigation strategy has a risk, it’s going to be specific to each reservoir, it’s going to be variable in the black oil window and your volatile gas window, and you really must cater to the asset value and the value to protect [the resource] in place”
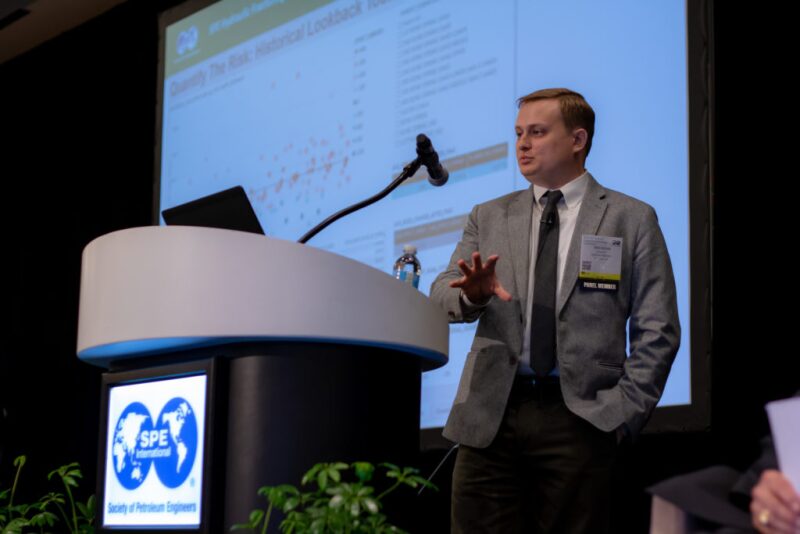
"QUANTIFY THE RISK": Brendan Elliot, a senior completions engineer at Devon Energy, said his company is putting together a plan to make on-the-fly changes to stimulation treatments as a way to mitigate frac hit impacts. Source: SPE/Jason Notoras.
A Call to Action
The opening panel session’s lineup also included a pair of advanced modeling experts from Schlumberger and The University of Texas at Austin (UT), who helped dissect the “science and art” of high-density infill drilling and completions. A statistic shared by Schlumberger later in the conference showed that 70% of new wells drilled in the US are infills. The US shale sector is expected to drill about 20,000 horizontal wells in 2019, per a separate report issued earlier this month.
The aggregate of the sweeping panel discussion was a call to action and set the tone for the event’s technical program, which in recent years has become dominated by frac hit-focused case studies and research papers. Yet, the amount of analysis and data-gathering work that petrotechnical professionals are being told remains left to do signals that their jobs will become even more demanding.
“There is a lot of activity here,” said George King, referencing the complex interplay of geology, geomechanics, and hydraulic fractures, “and trying to understand that is going to be difficult.” King, a prominent voice in the horizontal completions community and an engineering advisor at Viking Engineering, laid out the path forward as he sees it. The tenets, similar to Devon’s frac hit philosophy, were boiled down to these essential objectives:
- Establish data-based methods to identify frac hit risk profiles for each well during the infill development planning stage.
- Use this analysis to select one of several frac hit mitigation strategies that have recently emerged, which also requires becoming familiar with them.
- All along the way, build up a detailed characterization of the geologic and geomechanical tendencies in each specific target area.
“This is what we have to do,” emphasized King, who has authored or coauthored a number of SPE papers on the subject and is working with other engineers to promote a new taxonomy that better describes the granularities involved with the problem.
While outright frac hit prevention is not currently on the table, he believes the industry has generally proven on a small scale that the well-to-well events can be tamed into something “absolutely benign,” or even beneficial to production.
“But you’re going to have to collect the data that will allow you to make those changes,” he said, highlighting yet one more major theme of this year’s conference: frac hit data acquisition. Later in the discussion, Elliot echoed the sentiment: “You’re going to find a lot of really good information in the subsurface if you start measuring.”
One important way operators can leverage new sets of higher-resolution data will be as an input into the advanced fracture models and simulators. Ripudaman Manchanda, a research associate at UT, works on joint-industry projects where he has been helping to develop some of the newest such tools.
During the panel talk, he said advanced models can guide operators on how to tailor preventative treatments to their patch of rock, predict frac hits in the first place, and redesign child wells with potential interactions in mind.
“As you realize, this is not the completions engineer’s job, the reservoir engineer’s job, or a production engineer’s job,” he said. “This is an interdisciplinary problem that we are facing—and it requires a fully integrated approach.”
Manchanda believes that bringing all the engineering talent together should hinge in part around advanced modeling, which in the unconventional sector refers to software code that tries to account for the unique physics and geomechanics encountered in tight rock formations. He acknowledged that the technology falls short of being a true picture of the subsurface, but argued that “by using these models, we can definitely add some insight and evaluate different mitigation strategies” without relying solely on trial and error in the field.
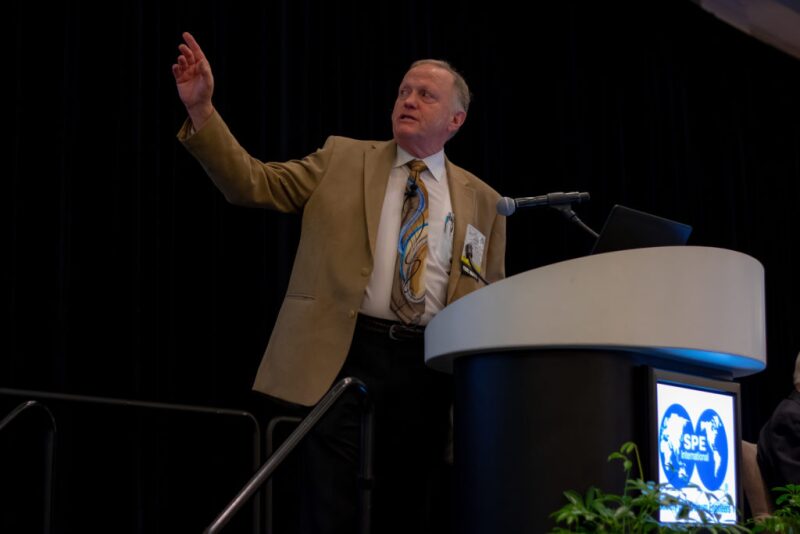
Words Matter: George King, an engineering advisor with Viking Engineering, is proposing that the industry adopt new terms to better describe what frac hits really are, how they work, and what effect they have on productivity. Source: SPE/Jason Notoras.
"Quantify The Risk"
In a slide Elliot shared titled "Quantify The Risk," the vast majority of the frac hits were classified as harmful to production. But since the operator knows how time and produced volumes influence the outcomes, essentially providing a window of opportunity, the beneficial frac hit category holds promise to become more crowded.
One way Devon is exploiting that window is through sequentially completing wells before the scales of the depletion are tipped into negative risk territory. Referring to the concept as a “rolling development,” Elliot said, “You’re going to frac hit these wells, so just do it at the right time and the wells have a better chance of coming back.”
Elliot is working on Devon’s Delaware asset team in the Permian Basin remotely while he completes his PhD at UT. His academic work there is exploring on-the-fly completions, which have long been a talking point in the unconventional sector but are rarely executed in the field. Devon intends to adopt the practice as soon as it figures out how to get all the moving parts working in unison.
On-the-fly completions, as Devon envisions, require field data to be processed by a computer program that generates different scenarios for engineers. “Once you see a result, you have to react to what you observe,” said Elliot. “The limit for us now is the time that is required to inform the field, and the scalability of this method.”
It was suggested later during the discussion that the entire concept of changing fracture schedules (e.g., rates and proppant changes) be simplified so that field personnel can easily adapt.
One technology seen as a front-line and scalable tool is wellhead pressure monitoring. With pressure sensors tapped into all the wells inside the radius of a treatment zone, operators are essentially building arrays that detect frac hits as they form in real time.
Elliot shared an example of pressure-monitoring data from one of Devon’s horizontal wells as it was hydraulically fractured along with three neighboring wells. Only 15 minutes after initiating the pumping treatment, the plots showed pressure gently rising in the closest offset well—which he identified as the signature of a poroelastic response, or stress shadow, which can be harmless but potentially concerning. The signal was seen in all the offset wells less than halfway through the job.
“This is very repeatable,” he said about the ability to spot these signals, especially since the response was seen during every stage of the case well. Recognizing the fingerprints of poroelasticity is important, because engineers can then build a mental model, or what Elliot called a “picture of dynamic growth in time,” of where the fractures are really going in relationship to the offset wells.
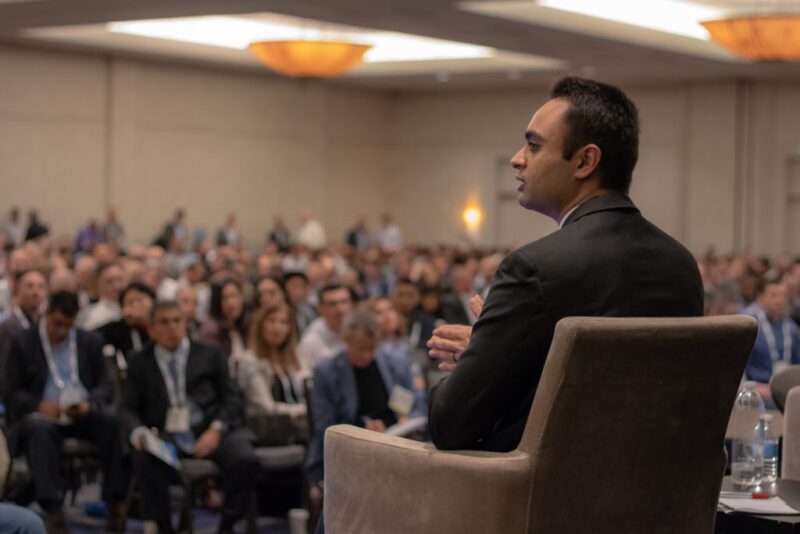
Ripudaman Manchanda, a research associate at UT, stressed the need for shale development programs to become integrated projects and lean on advanced modeling to accelerate the costly process of trial-and-error. Source: SPE/Jason Notoras.
Weighing The Many Options
Whatever frac hit mitigation plan is finally settled on by Devon relies on a decision-making process that Elliot said involves assessing the value remaining inside the parent well(s) relative to that of the new infill wells. Weighting the net present value of the two groups against each other leads to a judgment call on what type of completion and frac hit mitigation plan is worth executing.
In terms of completion strategies, Devon may choose from several options that include reducing the volume of the child well treatment or extreme-limited entry.
The economic equation also takes into account drilling schedules, proposed well spacing, parent well results vs. the first child well on a pad, and how much downtime might be associated with preparing for and then taking the frac hits.
“This is just a simple model, but it gives you an idea of what ends you can pull from,” which for mitigation strategies range from doing nothing to protect a parent well to the most capital-consuming option of refracting, explained Elliot. As these decisions are put into action, the learnings are funneled up to Devon’s overall development program, which can then take various shapes as well.
Elliot shared high-level points that sum up the various options and their tradeoffs:
Ups and Downs of Completion Strategies
- Smaller Child Completions: Reduces capital and fracture interactions, but risks under-stimulating the reservoir
- Larger Child Completion: Reduces fracture asymmetry with large pad volumes, but the downside is over-capitalization
- On-the-Fly Completions: Goal is to adjust completion in response to variabilities along the lateral, but time and tools needed to communicate changes to the field are still in development
- Pinpoint/Coil Completions: Single clusters help control frac lengths, but must be done with reduced number of fracture clusters
- Variable Shot Clusters and Extreme Limited Entry Completions: Improves fluid distribution with more near-wellbore stimulation, but there are pressure and rate limitations (equipment and tubulars) and cost is an issue
Comparing Depletion Mitigation Strategies
- Do Nothing
- Parent Well: Highest risk of cleanouts, sand loading, and reduced production
- Child Well: Underperforms 20-40% compared with parent production
- Small Volume Preload and Active Pushback (may involve chemical remediation)
- Parent well: Protected from cleanouts
- Child Well: Underperforms 20-40% compared with first order offset well
- Large Volume Parent Preloads
- Parent Well: Minimal reserve loss, parent fracture network protected
- Child well: Underperforms by 15-35% compared with first order offset well
- Recharge Parent
- Parent well: Elevates protective reservoir stress and pressure
- Child well: Improves first order offset well performance and mitigates frac asymmetry
- Refracture Parent
- Parent well: Elevates protective reservoir stress and pressure, adds incremental reserves
- Child well: Optimal first order offset well performance
Development Decisions
- Wider Well Spacing: Increase distance of wells from each other to reduce influence of new fractures, but risks abandoning reserves
- Staggered Wells (Wine Rack Configuration): Reduces direct interference and contact (sometimes) while allowing additional pay zone to be contacts, while risking a mischaracterization of the subsurface and can result in variable fracture geometries
- Cube Development: Eliminates parent wells by developing multiple wells at once, reducing the chances for well interference, but comes with longer lead times, delayed production, and is capital intensive ( > $100 million)
- Rolling Development: Optimizes infill timing so depletion has reduced negative effects, but introduces challenges to program efficiency and can be impacted by leaseholder requirements
- Slowback: Artificially slow or delay production to control depletion, but lower parent well rate-of-return
But Do We Know What Frac Hits Really Are?
Historically, anything over 100-200 PSI might be considered a frac hit, along with events registering 1,000 PSI and above. But as companies acquire more information about frac hits, or well bashing as some call them, these terms are coming under increased scrutiny.
“We know they are entrenched, but honestly, they don’t mean much,” said King, making a point that the well interactions in question are not all the same. “Some are harmful, some are helpful, some are temporary, some are long-term.”
King is pushing for the industry to use the term “fracture-driven interaction” along with a subset of several others that parse out different behaviors and outcomes. Whether the most widely used descriptor—frac hit—evaporates over time, the effort to break down the nuances is a notable data point in the sector’s maturing understanding of the issue.
Types of Fracture-Driven Interactions
- Short- and long-term tip-to-tip fracture connections:
- Fracture connections along the same wellbore
- Fracture connection to offset wellbore(s)
- Off-balance pressure behavior (unequal fracture wings)
- Connection through natural fracture systems (usually temporary)
- Near-wellbore stress shadowing and far-field fracture shadowing
- Fracture coalescence: multiple fractures joining into one fracture
- Hydraulic and stress responses: mechanical or physical damage
- Chemical: wetting, emulsions, changes
- Time-element factors: immediate or delayed interactions
Source: George King/Ali Daneshy.
It has taken years of scientific effort and field work by many industry participants to put this much of the puzzle together. The new language may help find the next pieces by recalibrating how the sector thinks about the completions process and helping it better visualize how the interconnected well system really works.
“The first thing we need to realize is that rock fabric in these shales plays an amazing, important role,” said King as he introduced a separate list of rock qualities that can define the different types of frac hits. They include mechanical properties, bedding planes, variances in the different formation layers, and how it all fits into time-dependent deformation through production—parameters that are present in all active shale reservoirs, just never in the exact same way.
Accounting for the makeup of the rock fabric, especially the weak-strength features that dominate its response to stimulations, will be critical to predicting what kind of frac hits might be observed.
Some may be physical in nature (i.e., transporting sand and fluid) or they may be the more consequential mechanical hits that damage downhole jewelry and casing beyond repair. There are also chemical interactions that can be quickly remediated if operators are aware of them, and what technological solutions are available to pursue that end.
“We need to know more about what is actually causing these things,” stressed King, issuing one more plea for the sector to adopt the right tools for this task. “These are unusual formations, and to use conventional technology in these unconventional wells means you’re going to waste a lot of money.”