LiquidPower Specialty Products Inc. (LSPI) said it can increase the flow capacity of subsea flowlines from wells to platforms by up to 35%. Based on the company’s long history in that business, that sounds doable.
The hard part is convincing users that it can dependably deliver the chemical to the offshore wells where it is needed.
The delivery barrier has made subsea production lines one of the few oil pipeline markets not served by LSPI, whose history dates to 1979 when it began selling an additive, a drag-reducing agent (DRA), that dramatically increased pipeline flows.
The polymer was invented by scientists at what was then Conoco, in the early 1970s. Among the inventors was Yung Lee, who is still with the company which is now owned by Berkshire Hathaway.
The chemical able to increase oil flows by 80% proved popular, and its use spread around the world. Now, the maker of a product used in 80% of US oil pipelines is looking for new markets. Lines running from offshore wells to platforms look like an attractive growth market, as oil companies focus on finding oil near existing platforms where the risks and costs are low.
“It is going to be substantial. It is not huge like pipelines. Still, more and more people are going to discover oil-bearing formations away from platforms,” said Lee, engineering and technical services director for LSPI.
The short explanation for how LSPI’s DRA works is that the long molecular chains of the ultrahigh-weight polymer in a pipeline reduce turbulence. That allows more oil to flow through a pipe and reduces the pressure needed to do so.
There are offshore markets for DRA, where it is used in large lines delivering oil to shore and in multiphase lines connecting platforms.
Pipelines from subsea wells to platforms are not on the list because LSPI has been unable to find a way to deliver DRA to those remote locations.
The obvious way to do so would seem to be to pump the relatively small amount of chemical needed each day through an umbilical. For more than 15 years, LSPI tried to develop a DRA molecule that would flow dependably through the narrow tube in an umbilical.
The problem was “DRAs contain solid particles [polymer] that will coat the internal wall and eventually plug the umbilical,” according to a recent Offshore Technology Conference (OTC) paper describing the prolonged search (OTC 31054).
That problem created an opportunity for Safe Marine Transfer, which was looking for customers needing an alternative delivery method, said Art Schroeder, CEO of the Houston company.
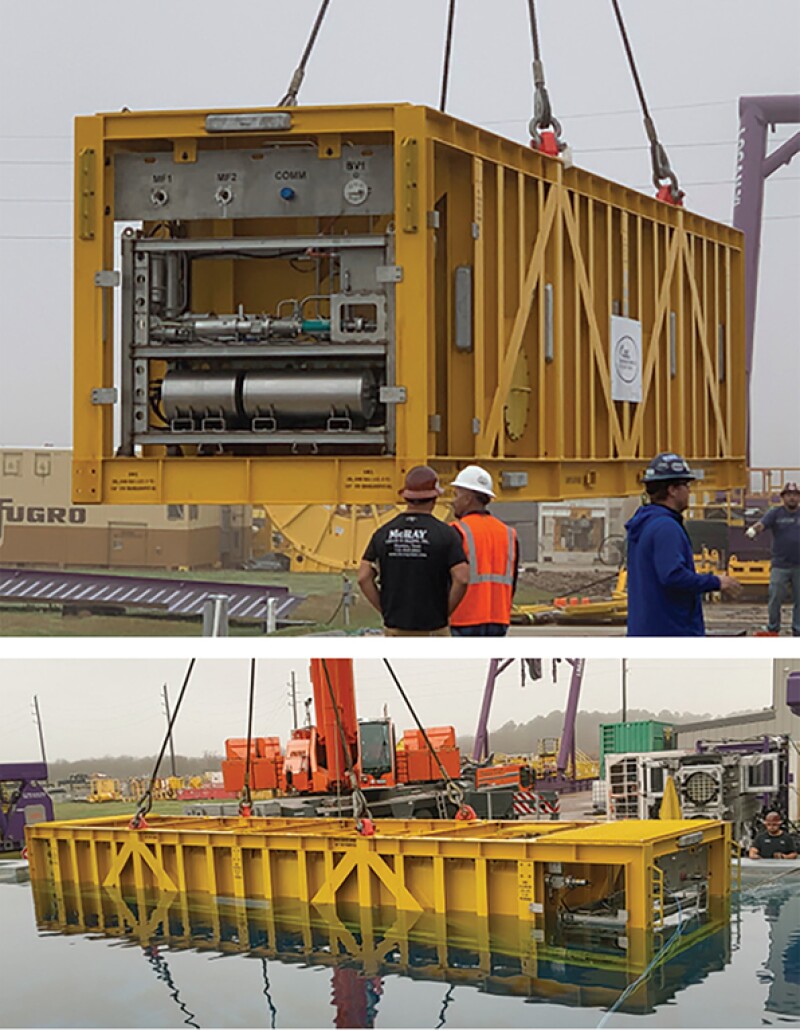
Inside the Box
Three years ago, at the OTC, LSPI met the founders of Safe Marine, who convinced them to consider delivering DRA in a box.
The box intentionally looks like a cargo container. Its dimensions—40×8×8.5 ft—make it possible to load the box on a truck and move it to a dock on its way offshore.
Inside is a large, tough bladder designed to hold 200 bbl of fluid. The container allows water to enter, equalizing the pressure so the frame can stand up to extreme deepwater pressure.
The system is equipped with a remote monitoring and control system, plus the hardware needed to connect it to a pipeline access point.
The third partner in the group is Subsea 7, which will provide the vessels and deepwater delivery and intervention expertise.
Earlier this summer, they successfully tested the subsea container in a 40-ft-deep test pool in Katy, Texas. Schroeder said it passed those tests and regulators have been satisfied so far. What they need to do now is convince a potential customer to test their chemical storage in the ocean, and for that they are reaching out to a variety of chemical suppliers.
This would not be the first time chemicals have been delivered this way. The method has been used for jobs such as well interventions, where a single delivery is required. But operations managers are wary about depending on regular deliveries to maintain production.
Based on LSPI modeling, DRA formulated for multiphase lines in frigid conditions could increase the capacity of a 6-in., 15-mile-long line from 10,000 B/D to 13,000 B/D. If the injections stopped, the capacity would revert to 10,000 B/D.
In that example, Lee estimated that 2.6 B/D of the DRA would be needed. At that rate, the 200-bbl storage unit would need to be replaced every 76 days. LSPI is working on stretching that limit, possibly by employing multiple units at a time.
An on-site electric power supply is required for the pumps and control system.
Regular subsea deliveries would not be cheap, but they would end when the production dips to the pipeline capacity.
The DRA has been effective at increasing the oil flow in lines where gas and water are also present. But as water levels go up, its effectiveness goes down. When the water cut exceeds 50%, the DRA’s benefit is negligible, Lee said.
The partners said they have met some interested potential customers. When they talk to flow-assurance engineers, Lee said, they “get really excited” about DRA.
But Schroeder said they also need support from someone in operations. They are seeking someone who does not assume the actual cost will be twice that quoted, and the benefits half as high.
For Further Reading
OTC 31054 Key Technology Qualification for Increasing Subsea Well Production via Drag Reducing Agents by A.J. Schroeder Jr., J.E. Chitwood, and T.A. Gay, Safe Marine Transfer LLC; J. Gillespie and Y. Lee, LSPI; P. Hughes and J. Verdeil, Subsea 7.