The concept of a standalone production system on the seabed with automated wellbore construction and production processes has been an industry goal for a long time. Electrification of subsea facilities and of wellbore and reservoir equipment offers many opportunities to improve operational efficiency, reduce life-of-field capital and operating expenses, and reduce carbon footprint, among other benefits.
Talk of a subsea electrification revolution being “just around the corner” has been ongoing for more than 20 years. And, millions of dollars in investments and numerous joint industry projects (JIPs) over the past decade have moved the vision closer to fruition (Fig. 1).
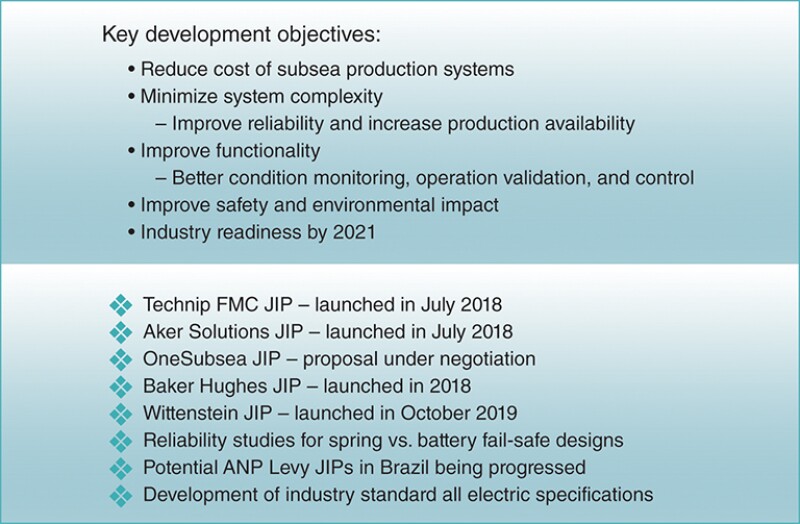
But the upstream industry continues to lag others in replacing hydraulics with electrics. The reasons echo those for slow uptake of other new technologies and methodologies—fear of change, the unknown, and failure. Now, recent events are stirring up interest and expectations.
“Four to five years ago, only a very small percentage of the buying community were making big noises about the future state of the electrified subsea or subsurface,” said John Kerr, subsea production systems and technology director for Baker Hughes, in a recent interview. “During the past 18 months the narrative has increased rapidly with many more operators looking at electrification as the base case for subsea solutions. We’ve seen a groundswell of interest to the point that we now see 3-, 5-, and 7-year lookaheads with electric solutions as the base case design concept,” Kerr said.
What has changed? “Electrification of subsea devices has always been a solution to solve specific technical needs,” said Kerr. “The predominant one was extreme long-distance stepouts, where once you get to 250 miles or so, the ability to pump hydraulic fluids through small umbilicals presented so much pressure loss that it became impractical to implement a hydraulic solution, so all-electric became the solution of choice. Now we are seeing much more understanding of what electrification can deliver in the commercial and operational sense.
“During the last 2 years, there has also been rapid adoption of dialogue around the aspect of increased carbon credentials and carbon reduction as an advantage,” Kerr continued. “The interest is much more comprehensive, driving different behavior in concept selection for operators.”
Has the pandemic played a role? The consensus of participants in a subsea electrification panel at the virtual 2020 SPE Annual Technical Conference and Exhibition (ATCE) was that unless you’re surrounded by a crisis, you’re not encouraged to change. “The moment you put someone in a crisis situation, they understand that they have to change,” said Rory Mackenzie, leader for subsea electrical technologies at Total. “2020—the pandemic, oil price collapse, and environmental issues—this created a crisis. People are now much more open to considering change.”
The panelists included Alvaro Arrazola, completions engineer, Chevron, North America Upstream; Glenn-Roar Halvorsen, project manager subsea all-electric, Equinor; Christina Johansen, managing director, Norway, TechnipFMC; Samantha McClean, intelligent wells technical advisor, BP; Rory Mackenzie, head of subsea electrical technologies, Total R&D; and Thomas Scott, global product line director, intelligent production systems and reservoir information, Baker Hughes. Edward O’Malley, director of strategy and portfolio, oilfield services, Baker Hughes, moderated the session.
Recent Advances on the Seabed
According to DNV, subsea power distribution is now a ready technology, waiting for its first application. This year, ABB qualified its subsea power distribution system—including a transformer, variable-speed drive (VSD), switchgear, and controls—and Siemens is moving closer to qualifying its system. Others, like TechnipFMC, are working on smaller, less complex systems. Baker Hughes’ modular, compact, all-electric pump (MCP) is designed to come with integrated VSDs, mitigating the need for full-on “type-3” (supply, transmission, and distribution) to provide power ranging from 750 kW to more than 11 MW to subsea systems. This includes the power equipment and electronics required to enable subsea developments to shore.
“The fluidless pump allows us to look at using really small, cost-effective umbilicals that don’t require any type of hydraulic conduits over the length of the seabed. This can deliver massive cost advantages,” said Kerr.
Baker Hughes is also involved in other JIPs, including two for large-bore gas fields in Western Australia.
Oceaneering announced that it will provide an alternate solution to umbilical-delivered subsea chemical injection that will reduce lead times associated with bringing wells online and will provide a scalable chemical source for the life of the field.
The Elephant in the Room
It probably won’t surprise readers to learn that in 1960, when the first subsea well technology was being developed, oil company executives saw subsea wells as the choice of last resort, and the prevailing view was that “if you can’t put your hand on it, you can’t trust it.”
There is “an elephant in the room,” and its name is mindset. In the case of subsea electrification, the elephant is accompanied by several factors, according to the ATCE panelists.
Safety concerns. All-electric and digital technologies challenge existing subsea safety philosophies. According to Mackenzie, the very first line in the subsea production system standards was, “You will control the tree hydraulically.” So, while regulations encourage innovation, existing safety standards used by the industry restrict the envelope of new solutions and may impose excessive cost. Existing industry standards and guidelines, derived from best practices for traditional technologies (such as electrohydraulic actuation and safety functions provided by spring return) and operational concepts, may not provide relevant support for demonstrating the safety of new all-electric technology. Furthermore, according to DNV, without a common approach (work processes and methods), the means for the sharing of experience and improving best practices within the industry is lacking.
Technical and business risks. Summarizing the ATCE panelists’ remarks, “We know how to manage the failures we have with hydraulics from 30-plus years of experience. Most of us are mechanical engineers; we’re not as comfortable with the electrical engineering side of things that are crucial elements of this. We’re not particularly comfortable with taking data from other industries and using it when it doesn’t have reference cases for us.” The challenge to uptake is the fear of the learning curve when it comes to reliability. There is not enough confidence to get over the hurdle of being the first to learn. And yet there were reminders from the panelists that the industry now has 20 years of experience with batteries, electronics, motors, and gear systems since launching the first electric actuators subsea in 2001, and that our experience with reliability has far exceeded our expectations.
Determination of the economics is a significant business consideration. Whether and to what extend electrification is commercially profitable will vary from region to region and from field to field.
A lack of understanding of electronics and electrical control systems and their components, and the criticality of those. “As a mechanical engineer, you have a basic understanding of how hydraulics works, and as long as you don’t have any leaks, you’re good to go,” was another comment. Even among electrical engineers working in completions, they are often more aware of limitations to electronics but lack experience in operational problem-solving. The understanding of specific electronics resides with equipment manufacturers.
Taking Electrification Downhole—What’s Behind Mindset Matters
The mindset elephant seems to occupy even more of the room when the subsea electrification topic turns to the subsurface. There is a push to take electrification—and with it, the digital oil field—to the “starting point”—the reservoir—and ultimately remove the mechanical workflows we know today. And, there is resistance. The push comes from the subsea community, which is responsible for the seabed equipment, and the resistance is from the wells community, which is responsible for well construction and integrity. To add complexity to the situation, a third discipline—reservoir engineering—is integral to the intelligent completion systems that play a key role in reservoir management.
Each of these communities and disciplines has its own goals, performance indicators, biases, and rules of engagement. Often, it is the clarity around the language and understanding with which a “technology transition” is handled that determines the successful uptake of the new technology.
“We have an entire industry of hydraulics and mechanical engineers who don’t trust electronics,” said Samantha McClean, intelligent wells technical advisor for BP. “The subsea industry has been ‘proving’ electronics for over a decade and is electrifying more and more. But it comes back to a basic difference between subsea and downhole—you can repair subsea if you get it wrong; fixing downhole is very expensive.”
McClean returned to the importance of clarity around language. “Historically in the world of hydraulics, we’ve had a ‘repair’ philosophy. In the world of electronics, we may in the early days (until we demonstrate field operation and reliability) need to move to a ‘redundancy’ philosophy,” she said. “The reason that causes concern is because ‘redundancy’ implies increasing complexity, which raises a fear about reliability, because the more complex the system, the more likely we are to experience failure. So, the balance will be struck in the design,” she said.
Language also can exacerbate mindset clashes and cloud the reality—often business-based—behind them. “If we approach technology transition from the mindset of, ‘If you adopt it, you’re a frontrunner and an early adopter, and you’re insightful; if you don’t adopt it, you have an old-fashioned mindset.’ We ignore or overlook the reality that those who are afraid to adopt the new technology have an established business edge they need to maintain, and those who are quick to adopt are trying to establish a business edge or become more competitive,” McClean explained.
“We need to divorce individual mindsets from what we as a larger community are trying to do,” she said. “The push for electrification has been led thus far by subsea controls. In the well construction space, there is no value driver for change that directly benefits the construction delivery metrics. That leads to the mindset, ‘I’m not going to do it until you tell me it’s my problem.’ And that talks to the other reason why well construction is often seen as a blocker. The value case for electrification is long-term operation and total project capital reduction, which may increase well construction costs and delivery metrics,” McClean said.
“Additionally,” she said, “well construction (drilling and completions) people have no ownership of the long-term operability of the well. Other than when hardware fails—which explains the concern about unproven reliability—there are two measures of well construction success. The first is the ability to install something that doesn’t break. The other is the need to keep initial construction costs as low as possible yet deliver reliably (as promised) and make the project appealing from the beginning.”
McClean stressed that goal setting is often, and mistakenly, the same for both existing and new equipment. “This is a critical point,” she said. “We need to focus on understanding the environment we’re designing for, how long we need the equipment to work, and what does ‘acceptable’ look like. A piece of equipment isn’t more reliable because we used it yesterday; it’s more reliable because the design and qualification goals reflected the service environment accurately. That’s another area where the in-well equipment needs different goals than subsea equipment.”
Testing the Waters
“We don’t have proof of reliability” is a popular refrain inherent to any new technology. Many in the subsea world agree that one stumbling block has been a lack of standards.
McClean pointed out that while API and ISO standards such as API Specification 14A tell us how to design the mechanical safety valves and API Recommended Practice 17N provides a workflow for reliable subsea controls system design, the gap between the two is where the actuators sit for safety valves. To address this issue, an API Spec 19 subcommittee group for completions equipment is in the throes of developing API Spec 19E, which will define the qualification and assurance requirement for downhole electronics components to be used in conjunction with the existing equipment standards such as API Spec 14A for the safety valves and API Spec 19ICV for inflow control valves.
Another reliability issue is redundancy. “Total installed an electric safety valve 10 years ago, but it is not currently a marketable product,” said McClean. “No one at the moment has a system approach that talks to this point of ‘we are part of the control system.’ So, even if I’m developing a safety valve and I know how to develop the mechanical part of it, I need to know how the electric actuator and controls work to provide the redundancy required to deliver the reliability I need.”
The consensus is that mitigating risk requires de-risking every element and then the entire system before running it in the field. This means the testing and aging of systems destined for harsh environments should begin in benign environments as soon as possible. A run history can then be built based on gradually increasing risk factors. For example, an operator may run a hydraulic, electric, and remote-control safety valve, perform a risk analysis of each one, and then present the results to the decision review board to defend the recommended choice.
“We also need to look at our portfolio and ask, ‘Where is a low-risk environment to actually learn?’” said McClean. “In a deepwater, high-cost environment, every well is precious. While that’s true, it’s possible to identify some projects as really marginal and that without the benefits that electrification can deliver, they won’t be approved.
“When we are talking to people whose role is to deliver what they are delivering today, there is a lot more resistance, and that will just be the case until the change has happened,” she said. “But we need to talk to business managers in regions where their portfolio opportunities are marginal and there is potentially a lot more appetite for change.
“So, what if we make one of those a sacrificial project?” she continued. “We take the hit on it maybe being marginal and use it as a technology lever, and we sanction it for the learning rather than the production?”
One recommendation was to tie facilities in the Gulf of Mexico to new, smaller fields and stranded assets and build a business case.
Is Digitalization Moving Electrification Forward?
“This is one of the reasons the conversation is now more active than it has been for a while,” said Baker Hughes’ Kerr. “Because when we talk about digitalization and digital oil fields, you can’t have a digital oil field by monitoring a hydraulics system. All you get is an inferred digital oil field.
“The most basic example is that our ICV position sensors are not true position sensors,” he said. “They can give you incorrect data because they infer the position of the valve, whereas an electrical sensor will give you the correct position. Instrumented equipment supports digital innovation.”
The Bottom Line
We can’t do what we did before,” said Total’s Mackenzie. “The JIPs are in existence and starting to build case histories. They can give us both the technical argument for the spec and say whether it is fit-for-purpose. Then we have performance data.
“The other factor is ultimately if the business case pays out, and the people who are adopting these approaches are more successful in business than the companies that don’t,” he said.
For Further Reading
OTC 30515 Subsea All Electric—A Game Changing Technology Going Forward by R. MacKenzie, Total; and G. Halvorsen and H. Vedeld, Equinor.
SPE 202310 PACT—Digital, Fail-Safe, Wellhead Annulus and Production Tree Valves Actuator Control System by E. Johansen, Techni Oilfield Products; D. Fredheim, Equinor; T. Huuse, Baker Hughes, et al.
DNV Technology Outlook 2030—Subsea All Electric is Here to Stay