To achieve optimal production from unconventional reservoirs, it is useful to determine the permeability, pore pressure, and state of stress of rock strata. An effective way to derive this information is to conduct in-situ pressure-transient tests. Because injecting fluid into or withdrawing fluid from the pore network of tight rock is difficult, diagnostic fracture injection tests (DFITs) have been used to create an analyzable pressure-decline response and to derive the minimum horizontal stress through fracture-closure identification.
Introduction
Well testing is the technique of establishing fluid flow in the reservoir by either producing from or injecting into a well and then changing or terminating the flow rate to create a transient event, usually by shutting in the well at the surface. The resulting wellbore-pressure response is then evaluated to derive reservoir properties, such as transmissibility and initial reservoir pressure.
Creating a hydraulic fracture bypasses wellbore damage and near-wellbore stress concentrations and connects the wellbore to a significant portion of the reservoir-layer thickness, enabling a representative investigation of reservoir properties.
A typical DFIT sequence is shown in Fig.
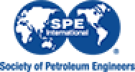