In hydraulic fracturing, the use of diagnostic-fracture-injection tests (DFITs) can provide valuable information. When the measured pressures in such tests are outside the expected range for a given formation, however, a number of possibilities and questions can arise. A recently completed project faced just such a challenge, initially resulting in poor hydraulic-fracturing efficiency and a need to understand the root cause. To this end, a thorough analysis involving a multidisciplinary review team from several technical areas was undertaken, which is described in the complete paper.
Introduction
Block A lies adjacent to other existing hydrocarbon-producing fields, residing within a large recognized basin.
×
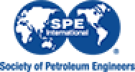
Continue Reading with SPE Membership
SPE Members: Please sign in at the top of the page for access to this member-exclusive content. If you are not a member and you find JPT content valuable, we encourage you to become a part of the SPE member community to gain full access.