The most obvious obstacles to a big ramp‑up in global hydrogen production are well known. They include technological breakthroughs to bring down production costs along with new sources of demand from the power and transportation sectors.
Less obvious is that a small army of reservoir engineers, geologists, and other subsurface experts will be needed to understand where and how tomorrow’s hydrogen hubs will store their clean-burning fuel.
Bulk storage on the surface is considered by many experts to be simply out of the question. That means large hydrogen projects will need a subsurface component, and some think depleted oil and gas fields—with an emphasis on the latter—may fit the bill. Saline aquifers are being eyed for the role too.
But as this all suggests, no one has ever attempted to use these formations for hydrogen storage. Just four shallow salt formations, three salt domes in Texas and one salt field in the UK, represent the totality of the world’s hydrogen underground storage (HUS) capacity.
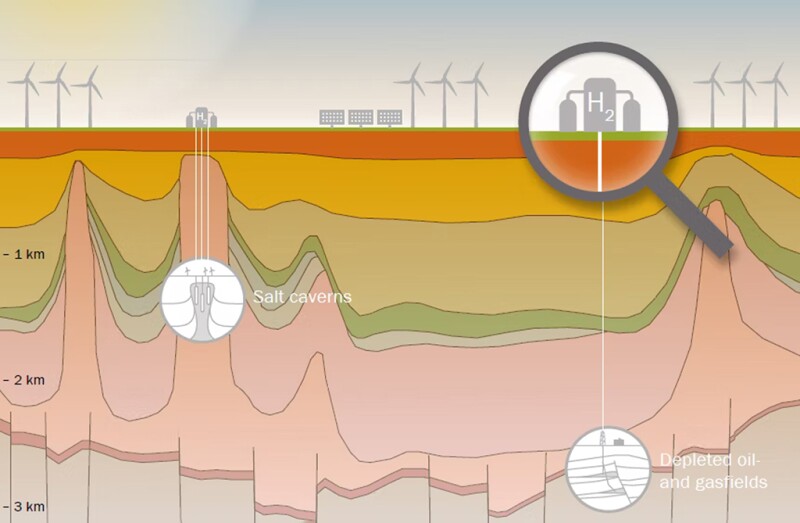
Research is underway to expand HUS in salt formations but that will not solve for the fact that they are not a geologic option for many locations where big industrial players are hoping to produce hydrogen. This includes most of Europe and most of the US outside of its Gulf Coast states.
By contrast, deeper sedimentary structures of various flavors are in no short supply but lack any material field experience that might help jumpstart the de-risking of storing several Bcf of hydrogen.
The upstream industry’s extensive experience in operating what are the closest analogues—natural gas storage and carbon capture and storage (CCS)—will help that process but there are new challenges when it comes to injecting the universe’s smallest molecule into porous media.
Topping the list is hydrogen’s strong propensity to migrate inside a reservoir (laterally and vertically) along with the potential for troublesome chemical and biological reactions.
Hydrogen may also be clean burning but it offers only about a third of the energy density as methane, which means it needs roughly three times the storage volume to deliver the same energy output to a gas-fired power plant.
Among those working to bring clarity to such issues is Mojdeh Delshad, a reservoir engineer and professor at The University of Texas at Austin. Her latest research involved using commercial reservoir simulators to model what would happen if selected gas fields and saline aquifers in the US used for CCS or natural gas storage were instead used to store hydrogen.
“We wanted to know about the challenges of hydrogen, which because of its properties—very low density, very low viscosity—is going to move in the reservoir much more quickly than CO2 and methane. And that’s exactly what we found, which means we’re going to have to do something differently with hydrogen storage in order to capture and produce what is injected,” said Delshad.
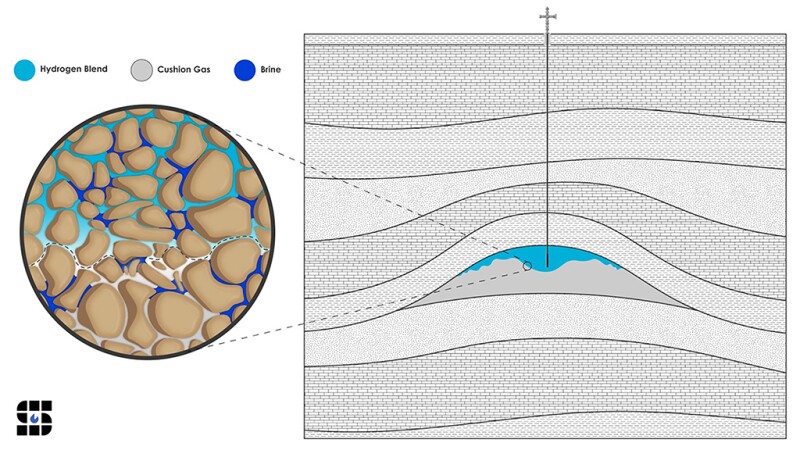
This highlights the risk that a developer’s injected product may simply migrate out of their well’s production zone and become lost somewhere in the distant corners of a reservoir or even in another formation. Leaky wells are another vector as are abandoned wellbores in a depleted field scenario.
These are some of the reasons why Zachary Evans noted that operating a HUS project in reservoir rock will be “orders of magnitude more complex than natural gas storage.” Evans is a former engineering consultant for hydrogen storage projects and also serves as administrative chairperson of SPE’s Hydrogen Technical Section.
In explaining his cautious view on HUS outside of salt formations, he said the US industry holds many decades “of experience in storing high volumes of natural gas all across the country, injecting it, and withdrawing it at higher rates, maintaining those facilities. But when it comes to hydrogen, it’s all theoretical.”
Plenty of hurdles for sure. But none are deemed deal breakers.
Eugene Holubnyak, director of hydrogen energy research at the University of Wyoming and program chairperson of SPE’s Hydrogen Technical Section, acknowledged “there are more unknowns than knowns” with HUS. And yet, he remains optimistic that the technical obstacles are surmountable.
“We figured out a lot of things for other areas [of subsurface storage], and so I am pretty sure we will figure it out here too,” he said.
What Holubnyak likes to point out is that even as the subsurface complexities are eventually addressed, it will be another thing to connect all the economic dots to make a HUS project financially sound over the long term.
He cited a number of natural gas storage projects around the US that have acquired pore space and received all the necessary regulatory approvals but that have yet to inject a single cubic foot of gas.
“In certain cases, it’s the technical issues, that is the complexity of the project, but in other cases the market is not there, so there is not enough demand,” to make the project work, he said.
The Green Driver
Demand for hydrogen hit 94 Mt in 2021, which marked a 5% year-over-year increase, according to figures from the International Energy Agency (IEA). But in order to stay on track with net-zero goals, the IEA believes annual demand needs to almost double from 2021 levels to about 180 Mt by 2030.
It’s far from guaranteed that such an ambitious target can be met over the next decade, but as big industrial players do their part, many will opt for so-called “green” hydrogen projects that rely on wind or solar power to run hydrogen-producing electrolyzers.
Srikanta Mishra, the technical director of geo‑energy modeling and analytics for the nonprofit Battelle Memorial Institute, recently coauthored SPE 210372 which speaks to how reservoir engineering will be key to fine tuning the injection and production strategies of CCS and HUS projects.
No one can say how many reservoir engineers and other petrotechnicals might end up being needed to run the HUS side of the clean energy injection business. But Mishra said if there is a “significant bump up” in green hydrogen projects, then they are likely to provide the first job openings for those with relevant expertise.
“I think the storage requirements are primarily with respect to green hydrogen because the renewable power sources are intermittent in nature,” he explained. “When the sun shines, when the wind blows, they generate power and sometimes they end up generating surplus electricity when there’s low demand.”
It’s that extra power that can be routed to the electrolyzers and the subsequent hydrogen pumped into the subsurface for later use at a power plant during peak demand.
Such injection/production cycles would be seasonal in nature but could last for months at a time, which is one reason Mishra sees a need for the planning and modeling skills held by reservoir engineers.
By contrast, growth in “blue” hydrogen production, which combines the steam methane reforming process (used to make >95% of all hydrogen today) with CCS, will likely just offset the use of the non-blue or “grey” hydrogen that lacks the CCS component. This is according to Mishra, who sees blue hydrogen’s demand from refineries and industrial sites as creating minimal need for HUS, especially when compared with the pore space needed for the CCS components.
Mishra also expects the developers of future hydrogen hubs will not be looking to run long pipelines and will instead focus on localized geologic targets.
“So, as you look ahead, it’s going to be a source-sink matching issue,” he said. “If you have a hydrogen project in Houston for example, then you think about whether there are any salt domes nearby. If not, other potentials might include a depleted gas field.”
Making a Case for Depleted Fields
Delshad recently presented SPE 210351 which outlines some of the considerations of storing hydrogen in depleted gas fields vs. saline aquifers. While both appear to be suitable formation types for hydrogen storage, the research professor believes natural gas reservoirs will end up being the first to draw commercial interest.
“Why? Because you know that you can produce gas from these reservoirs and the seal integrity is there,” she explained, adding that a gas field might also offer existing infrastructure that could be repurposed for hydrogen. However, this is far from assured given the corrosive nature of hydrogen which demands high-spec pipelines and other equipment.
But assuming a gas field is selected for hydrogen storage, Delshad said it will require an extra effort to ensure both containment and optimal recovery.
Her modeling efforts began using a simple strategy involving only a single well for both the injection and production of hydrogen. This version of huff ’n’ puff is fairly standard in the world of natural gas storage, but Delshad said the models quickly showed the strategy to be uneconomic across the board when it comes to hydrogen storage.
The problem is that one well doesn’t appear to allow enough water to be pumped out to create new pore space for optimal hydrogen capacity. “So, I looked at natural gas storage projects again and found that some of them use additional producer wells,” which draw out both water and gas, she added.
In one respect, the idea is that while the number needed may vary, the producer wells will cut off the escape paths for migrating hydrogen and either sending it back to the center of a field for reinjection or further downstream to a power plant.
“In every case we modeled, these producer wells helped reduce the cushion gas volume while improving the capacity, production, and confinement,” explained Delshad.
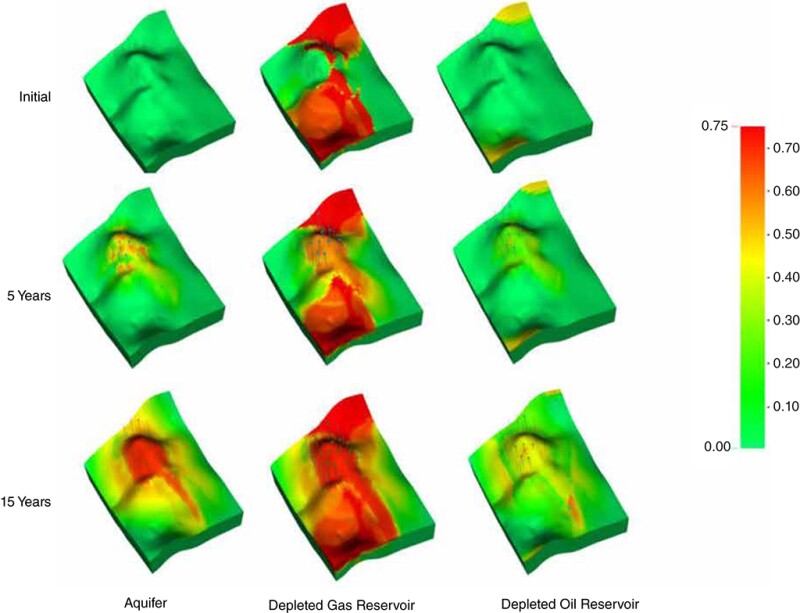
The cushion gas mentioned is key to the HUS concept in both depleted reservoirs and aquifers since it will be what’s used to maintain high-enough pressures to produce hydrogen on demand.
In cases where no other gas is used, such in those where pure hydrogen is desired, some of the injected product will serve as a cushion gas and be deemed “unrecoverable” for the duration of the project. In the event another gas can be used, such as methane, it may mix with the produced hydrogen and require additional separation systems on the surface.
What project runners will aim for is the minimal amount of cushion gas required to hit desired withdrawal rates, or the working gas volume.
In terms of comparisons, Delshad’s research suggests gas reservoirs offer the biggest bang for the buck in terms of balancing this cushion to working gas ratio over either aquifers or spent oil fields. The tradeoff is a more profound spreading of hydrogen through a gas reservoir’s high permiability matrix, hence the potential need for a strategic ring of producer wells.
The Case Against Depleted Fields
While gas reservoirs provide a familiar operating arena for many subsurface engineers, that happens to be one of the downsides.
One of the concerns raised with depleted fields is that by definition they have existing wellbores, each one representing a potential pathway to the surface. This is the same reason some CCS developers are avoiding depleted fields altogether in favor of aquifers.
Going a step further, Evans, who champions the nearly impermeable salt dome formations for HUS, questioned whether natural gas storage should even be considered a good analogue for HUS in porous media.
“I can’t stress just how small the hydrogen molecule is and so you’re really going to be worried about whether a sealing trap that’s good for natural gas will be equivalently good for hydrogen,” he said.
Evans admits that his views on HUS in reservoirs may come off as pessimistic but he said he’s not rooting against the concept.
“I’m just very pragmatic when it comes to the application,” he said. “Right now there are a lot of unanswered questions that researchers are still tackling and that, ultimately, will have to be answered by reality when a long-term pilot is initiated.”
While the prior point on seal integrity could be equally applied to unexplored aquifers, experts are nonetheless looking at them too since they hold a couple of key advantages over depleted fields.
The first is that these saltwater-bearing rocks generally have no existing wellbores that could represent leak paths. Beyond that, saline aquifers may offer bigger overall capacities than depleted fields.
Mishra argues this is reason enough for some project runners to consider aquifers since “in a depleted field all you can do is replace the hydrocarbons that have been produced and fill up the pore space back to the original reservoir pressure.”
Exceeding that threshold, known as the fracture gradient, means risking the creation of new leak paths for fugitive hydrogen.
On Bad Reactions
Aside from migration, some portion of hydrogen might also be lost within the rock matrix itself or if it reacts with what’s still inside the reservoir.
Veins of sulfur in the rock or particles inside residual fluids, could upon contact with hydrogen, generate toxic hydrogen sulfide gas. Short of a major leak, this is one of the least desirable outcomes of any storage project. Short-term risks include hydrogen losses while long-term risks may involve formation integrity, e.g., caprock integrity. Microbial communities known to exist in reservoirs may also feast on some small share of the injected hydrogen.
Holubnyak is currently working with various stakeholders on obtaining US federal funding for a series of integrated hydrogen hubs spanning Colorado, New Mexico, Utah, and Wyoming. He said the reactivity issue does raise the bar for project developers when it comes to site characterization but said they won’t exactly have to reinvent the wheel.
“If [HUS] is anything like CCS, and in a lot of respects it is, then you will have to dig for a lot more reservoir information and prove the storage concept to the regulatory agency,” he said. “We will probably need to gather new information from new wells, and so all of this comes at an additional cost. It is expensive, but it’s doable.”
While bad reactions to hydrogen are considered to be a bigger risk than when dealing with CO2, and much more so than with methane, Mishra argues that the potential for serious problems are “extremely site-specific” and will be mitigated through proper reservoir study.
That said, he does think that the issue pretty much rules out the use of depleted oil reservoirs for hydrogen storage since they are likely to have more substances prone to a negative reaction than either a gas reservoir or an aquifer.
The other potential is that certain microbes present in the formation will consume the hydrogen and could in fact promote biological activity as more hydrogen is pumped downhole.
More research is needed to understand the true scope of this challenge, but Mishra said what’s known today suggests losses due to biological activity would be relatively minor. One industry shortcoming he does see necessary to address is that while the processes behind biological reactions are well defined, “they’re not fully understood to a point where we can model them with a great degree of certainty.”
What may end up being the most important of all hydrogen’s possible reactions is corrosion and embrittlement of steel and other materials such as the cement used for zonal isolation.
“Hydrogen will eat pipe,” said Evans, adding “that’s a known quantity, not a theoretical concern.” He acknowledged that while products rated for hydrogen-handling exist, there remains more to learn about their long-term durability.
Most of the learnings on material integrity in this regard come from the refining industry which counts as both the world’s largest producer and consumer of hydrogen.
But as Evans highlighted, “The one thing the refining industry doesn’t have is several thousand feet of downhole casing that’s in a hydrogen-rich environment for 100% of its life.”
For Further Reading
SPE 210372 Adapting Petroleum Reservoir Engineering Principles to Carbon Capture &Sequestration (CCS) and Hydrogen Underground Storage (HUS) Projects: Opportunities and Challenges by Srikanta Mishra, Battelle Memorial Institute, and Akhil Datta‑Gupta, Texas A&M University.
Energies 2022, Hydrogen Storage Assessment in Depleted Oil Reservoir and Saline Aquifer by Mojdeh Delshad, Yelnur Umurzakov, Kamy Sepehrnoori, Peter Eichhub, and Bruno Ramon Batista Fernandes, The University of Texas at Austin.
SPE 210351 Pros and Cons of Saline Aquifers Against Depleted Hydrocarbon Reservoirs for Hydrogen Energy Storage by Mojdeh Delshad, Muhammad Alhotan, Bruno Ramon Batista Fernandes, Yelnur Umurzakov, and Kamy Sepehrnoori, The University of Texas at Austin.
How To Leverage E&P Expertise for the New Energy Economy by Srikanta Mishra, Battelle Memorial Institute, and Akhil Datta‑Gupta, Texas A&M University, JPT, April 2023.