An automated machine-learning-fueled forecast approach helped ExxonMobil increase average production by more than 5% on Bakken gas lift wells optimized using the method.
Traditional ways to solve the question of how much gas to use for gas lift in the Bakken have their drawbacks, Sasha “Sha” Miao, an ExxonMobil data scientist, told an Unconventional Resources Technology Conference (URTeC) audience in Houston on 18 June.
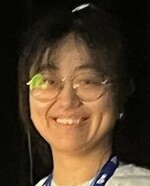
“The million-dollar question is how much gas should we inject” to produce the maximum amount of oil as the well evolves throughout its lifetime, she asked. “More is not necessarily better.”
Traditional methods to determine the optimal amount of gas to inject rely on physics models and data-driven models, she said, but both present disadvantages. While physics-based models typically provide solid results, they require extensive effort and cost for calibration, are computationally expensive, and are difficult to scale from a few wells to hundreds of wells. Additionally, she noted, such models rely on assumptions that may not be true for unconventional wells.
On the other hand, data-driven models are easier to deploy across a field but are problematic because the assets in question were sparsely instrumented and the corrosive downhole environment meant there were no bottomhole gauges to provide the data needed to feed the models.
A complicating factor was that the Bakken wells use pad compression, she added, which limited the amount of changes possible.
“The Bakken is extremely cold in the winter,” she said, and changing injection rates could introduce compressor reliability issues.
Enter the three-part automated data-driven workflow based on historical production data. A Machine-Learning-Based Gas Lift Optimization Workflow for Unconventional Fields (URTeC 4033553) details the machine learning (ML) forecaster, Bayesian optimization, and deployment stages of the workflow, which are deployed through the cloud.
ExxonMobil piloted the workflow on 30 wells across eight well pads in the Bakken and obtained greater than 5% production uplift on average and followed that up by deploying it across more than 200 gas lift and plunger-assisted gas lift wells in the Bakken.
“We forecast every well’s production on a weekly basis,” she said.
Building a Forecast
To build the ML forecaster model, ExxonMobil gathered historical daily data, such as production rate, gas injection rate, and surface pressure data, before cleaning up the data set and plotting the aggregate of the liquid production of all the pilot wells (Fig. 1).

Miao said production forecasts are similar to forecasting stock prices. Just as tomorrow’s stock price is highly correlated with today’s stock price, she said, “the production next week is highly correlated with this week’s production rate.”
ExxonMobil turned the time-series forecasting problem into a regression problem to determine which factors most affected production, she said. Unsurprisingly, she said, temporal features such as changes in past liquid production and surface pressure and temperature were the most important factors for tuning the ML model, while the gas injection rate was “somewhat important,” and the static well features were least important.
After running the model on the well, it was time for a sanity check to ensure the forecast fit in with engineering experience. The forecast, she said, should not vary dramatically from week to week but gradually evolve (Fig. 2).
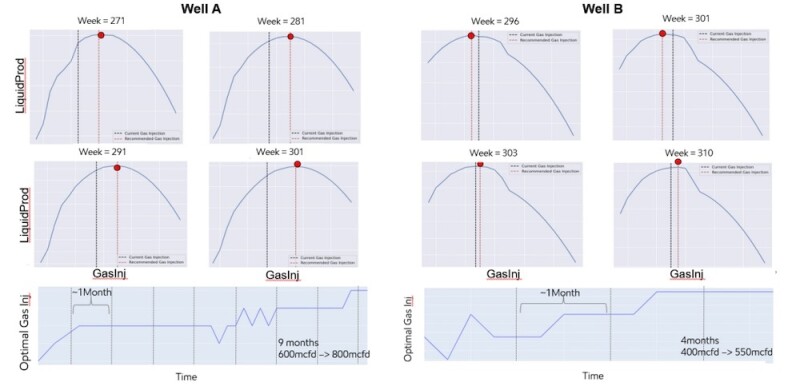
Optimizing at Scale
Optimizing gas lift on the pilot was not straightforward because the Bakken wells are on pad compression and each compressor has its own maximum and minimum required capacities. The goal was to maximize total production of all wells sharing the same compressor while keeping the total gas injection rates of all wells sharing the same compressor within the compressor’s capacity.
ExxonMobil used a Bayesian optimization method because of the scale of the problem and the efficiency of the method in dealing with large numbers of wells, she said.
Deployment Architecture
The continuous-integration/continuous-deployment workflow used through the cloud features a prediction pipeline and a training pipeline (Fig. 3), Miao said.

“This prediction pipeline is running on a weekly schedule,” she said, while the training pipeline is running monthly.
The prediction pipeline forecasts well gas lift performance curves and solves for constrained optimal gas injection rates. End users can compare predictions against true measurements and alert on large deviations for troubleshooting.
For the training pipeline, the ML model is retrained on the latest data each month, and that model is compared with the existing model. If the newer model has the better performance, it is used; but, if not, the older model is considered to be up to date and will continue running for the next month.
“We need to make sure the model is up to date,” she said.
From Pilot to Expansion
ExxonMobil started the pilot in March 2023 on about 30 wells across 8 different pads in the Bakken, resulting in an average of 5% increase in production, she said. Full deployment followed, rolling it out to more than 200 gas lift and plunger-assisted gas lift wells in the Bakken. More than 50 wells have been optimized at least once, she said, with 84% of wells near optimal and an average 7% increase in production uplift.
The approach has completely replaced physics-based approaches in the Bakken, she said.
Miao said the pilot and expansion demonstrate the effectiveness of the automated data-driven workflow using machine learning for gas lift optimization in unconventional resources.
“It is easy to scale up. It is an effective and economic solution for assets with cost and facility constraints,” she said. “This workflow has become the Bakken engineer’s routine surveillance and optimization tool to increase their production and efficiency.”