In the past 25 years, the artificial lift industry has seen incredible changes, making hydrocarbon production smarter and more efficient. In this Q&A article, JPT talks with seven industry leaders from this field about its past, present, and future.
This conversation showcases the technological progress such as materials, digital tools, and automation and the strategic leadership that has guided the industry to new heights. Join us as we dive into the world of artificial lift and discover the innovation and expertise shaping the future of energy.
This roundtable Q&A includes the following participants:
- Greg Stephenson, chief production engineer, Occidental Petroleum
- Michael Romer, principal artificial lift engineer, ExxonMobil
- Laura Labrador, senior production engineer, Ecopetrol, and 2023–2024 chairman of the SPE Artificial Lift and Gas Well Deliquification Technical Section
- Shauna Noonan, Oxy Fellow and senior director global supply chain initiatives, Occidental Petroleum
- Jose Ernesto Jaua, global product champion, SLB
- Kevin Leslie, vice president artificial lift solutions, Weatherford International
- Dana Meadows, global portfolio director, artificial lift systems, Baker Hughes
JPT: Can you recall an experience, technical paper, or mentor that significantly influenced your early career in artificial lift? How did it shape your approach?
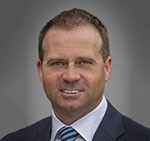
Stephenson: Numerous individuals impacted my early career, the most noteworthy being Herald Winkler, who was in the first class of SPE’s Legends of Artificial Lift awarded in 2014. I traveled to my first ATCE in New Orleans as a first-year petroleum engineering student. I distinctly remember walking the exhibit floor and seeing this little guy get mobbed by people asking him questions. I asked one of my fellow students, ‘Who is that guy? Tom Cruise?’ He told me, ‘No. That’s Wink.’
I then learned that Wink was one of the pioneers of gas-lift technology and wrote the first definitive book on the subject. At that moment, I realized that artificial lift might offer a viable career path for me. Eventually, I got to know him personally, first as a student and then as an artificial lift professional.
One of the most impactful conversations I had with him was one in which he told me, ‘I am not a gas-lift expert. You cannot be an expert in gas lift—the field is too complex. I’m still learning things, and I’ve been doing this for over 60 years!’ That encounter taught me to be humble in approaching my craft and never assume I knew everything.
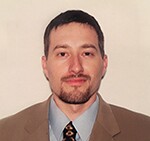
Romer: My first role in artificial lift was 2 years after I started with ExxonMobil. There was a US production artificial lift team at the time. Some people I worked with closely were Pat Underwood, Mike Johnson, Rodney Bane, and Mark Johnson. Pat was our subject matter expert (SME) for ESPs and rod pumps, and Mike was the SME for gas-lift systems.
Rodney was the group manager and had a strong artificial lift background. He was responsible for turning the group into a global one. Mark was a global artificial lift engineering resource. Most of the artificial lift team came up through the field and had great hands-on experience. My background is in electrical engineering, not petroleum, so I was fortunate to learn from them.
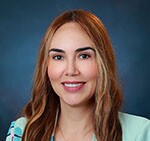
Labrador: Although it is not exactly an early influence on my career, I can say that it’s the one that most marked my history in the industry. Around a decade ago, when I was working for an operator company in Colombia, a pivotal moment occurred when I presented our progressive cavity pump (PCP) results to the worldwide artificial lift system (ALS) team.
In the audience was a remarkable woman, Shauna Noonan, the head of the worldwide ALS team for that company. Her knowledgeable comments and insightful questions left an indelible impression on me. From that day forward, I was inspired to keep working on ALS professionally and take her as a role model. Her guidance continues to shape my career, driving me to strive as a professional woman.
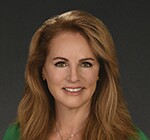
Noonan: During one of my co-op internships, Kevin Grondin was my manager with Mobil Canada, and the fields he was responsible for were gas-lifted wells. My assigned project from him was to install the first plunger-lift system in the area. That was my introduction to artificial lift; his enthusiasm made me want to learn more about it.
My very first SPE event was the ESP Symposium, and it was women-led. Karen Draper and Carol Magney-Grande convinced me to join the committee. That started with attending and coordinating artificial lift events and realizing that there were strong women leaders in the artificial lift space.
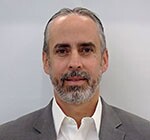
Jaua: I have been fortunate in my career to have had many great experiences in the artificial lift world. I grew up professionally in the discipline, starting in the field and working up to managing entire geographies and products at a global scale.
If I must select one incredibly enriching period, it was in 2011 when I was assigned to work in Ecuador, managing the artificial lift business covering the Andean region. I had the incredible opportunity to be part of the board of directors of the SPE local chapter, meeting many top industry and government authorities. I developed many initiatives that positively impacted the industry and promoted technologies and local talent. I also took that platform to coach and mentor young professionals.
Those moments in which I have been able to impact and contribute to a higher cause have always been the ones I have the best memories of. That experience was transformative for me, and since then, every time I change position or location, I invest effort and time to be engaged with the communities and mentor others whenever I can.
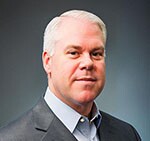
Leslie: Thinking back to my early career, one person stood out as an influence in my artificial lift career: Larry Hoes, the vice president of oil field for Lufkin Industries. Larry spent most of his career at Cameron but moved to Lufkin in the early 90s. During my career transition, Larry allowed me to showcase my abilities while working as the scheduler/planner of the Pumping Unit Facility in Lufkin, Texas, and then moved me to west Texas to manage sales and business development. Larry was a strong mentor who allowed employees to do what was needed as long as the results came through in the end. By providing this freedom, I developed my talent for sales, operations, and growth in the Permian Basin while learning multiple forms of artificial lift and the benefits of automation in the field.
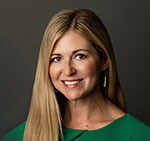
Meadows: Early in my artificial lift career, a mentor taught me to look for the value of just one more run day to an operator. That person taught me to listen and work to shape a tailored solution around the customer’s needs—not just sell them widgets. That made me view technology and development differently by asking the right questions, focusing on the business case from end to end, and framing it in a real-world application to provide a disruptive solution.
JPT: How have you seen knowledge sharing and best practices evolve within artificial lift applications over the years?
Stephenson: Artificial lift has experienced a metamorphosis while I’ve been in the industry. During the early portion of my career, virtually every technical presentation on artificial lift was delivered at a non-SPE event. This meant that most knowledge sharing was via PowerPoint, and there was never an accompanying manuscript that might find its way into OnePetro or JPT. If you weren’t physically present in the room where the presentation was delivered, you had virtually no way to access the information being shared.
That all changed with the creation of the SPE Artificial Lift Conference and Exhibition (ALCE) events in the Americas and the Middle East. These events were the brainchild of Shauna Noonan during her first term on the SPE Board of Directors. Those who work with artificial lift owe Shauna an enormous debt for this. When Shauna was the JPT technical editor for the topic she had relatively few papers to draw from. My job was significantly easier when I served in that role. The ALCE events and the ESP Symposium provided a wealth of papers from which to choose. The requirement to write a manuscript increased the technical rigor of these works and made them more useful to industry professionals.
Romer: There are more avenues for sharing now, including SPE technical sections, SPE regional artificial lift conferences, the Artificial Lift Research and Development Council (ALRDC), and through joint industry projects like C-FER’s ESP Reliability Information and Failure Tracking System, LSU’s Gas Lift Valve Performance Clearinghouse, and the ALRDC’s Horizontal Well Downhole Dynamometer Data Acquisition Project. Internally, knowledge sharing has increased with virtual events with video. Unfortunately, this has made in-person events less likely.
Labrador: Knowledge sharing has positively increased over the years. It is evident when you look back and see we have more events related to artificial lift systems and we recently got a specific SPE technical section for artificial lift (and gas well deliquification). The operators are working together to share the learning curve. Also, both operators and oilfield service (OFS) companies are documenting and publishing the lessons learned, best practices, and the knowledge acquired over time more frequently than before.
Noonan: Initially, most artificial lift events were not SPE-organized events, and the presentations/papers were not publicly available. I made it my mission to change that when I joined the SPE Board as the Production & Operations Technical Director. I created new AL events, converted the SPE Gulf Coast Section ESP event to a symposium so papers could be formally published, advocated for the AL Tech Section, and created the Legends of Artificial Lift Awards.
Jaua: Knowledge sharing has grown tremendously in the past 20 years, along with the evolution of digital technologies. In the ‘not that far’ past, we had to travel to congresses to meet peers and be exposed to newer technological developments. Nowadays, we have all the information and much more at the tip of our fingers and in every format we can imagine. From microlearning content to fully immersive technical conferences, all delivered remotely. In parallel, more communities and interest groups have been formed because now there are more domains and subdomains within the artificial lift space and, in general, in industry.
Leslie: From personal experience, the oil field grows through knowledge sharing and best practices in all facets of the industry. In the artificial lift space, engineers and supply chain utilize their knowledge of products to secure better pricing and activity. In contrast, other OFS companies utilize knowledge sharing and best practices to produce wells at a higher volume with a better mean time between failures. By sharing the learned knowledge, the OFS and E&P companies can produce at a higher production level with fewer problems. Without knowledge sharing and best practices, today’s oil and gas market would be totally different.
Meadows: Unlike in previous years, where the person who had the document in their filing cabinet was considered the expert, we now have multiple applications for data sharing on global internal operations that allow answers to pop up, lessons learned to be elevated quickly, and field instances to be shared and trended with actions.
This allows us to help our customers with solutions gained from actual cases worldwide and to develop the best technologies to address their needs using real-time operational feedback. Eagerness to share, learn, and collaborate is a large part of our culture at Baker Hughes. Technology has allowed that to advance quickly in the artificial lift field and beyond.
JPT: Is there a specific paper that helped you or your team solve a challenging problem in artificial lift? Could you elaborate on the problem and the solution?
Stephenson: The paper that has specifically influenced my work the most in recent years is an old one: SPE 179, Evaluation of Valve Port Size, Surface Chokes, and Fluid Fall-Back in Intermittent Gas Lift Installations by Kermit Brown and Frank Jessen.
This paper was published in March 1962, and more than 60 years later, it is still the most extensive exploration of intermittent gas-lift performance available to the industry. Brown explored the relationship between slug height, gas passage, surface opening pressure, and slug recovery in intermittent gas lift wells.
This is particularly relevant today because the industry has thousands of wells in unconventional resource plays that produce via continuous flow gas lift and experience rapidly declining production rates in early life. As the wells mature, the artificial lift system becomes less efficient and requires some lift revision. One of the most likely is conversion to intermittent gas lift, often using a pilot valve.
Unfortunately, the methods for designing and analyzing these wells are often antiquated and rely heavily on rules of thumb. The results can be unpredictable and/or suboptimal well performance. When I first read this paper, it inspired me to explore the issue further, ultimately leading me to Ali Hernandez’ textbook, Fundamentals of Gas Lift Engineering, published in 2016.
Using the knowledge gained from Ali’s textbook and the original paper by Kermit Brown, I built an in-house simulator for intermittent gas lift wells. This work also inspired the formation of the newly created Texas Tech Gas Lift Consortium in Lubbock, Texas.
Romer: We were looking for ways to improve gas lift and came across SPE 21639 (1991), Foamed Gas Lift, by M.G. Bernadiner from the University of Michigan. The project presented an interesting way to improve gas lift using surfactants, with both laboratory and oilfield experiments showing that it could be an effective means for producing oil from depleted reservoirs.
We thought it could be an interesting way to improve gas lift, and it led to research testing at C-FER in Edmonton, a pilot in the Gulf of Mexico, a presentation at ALRDC, and later pilot testing and application in the Delaware and Midland basins. No SPE papers were written on the ExxonMobil project, but the original paper demonstrated how somebody had done it once and that it should work.
Leslie: One of the most influential technical papers impacting my team and colleagues to solve the goal for lifting higher production with rod lift continues to be SPE 176041(2015), Electric Submersible Pumping Systems vs. Long-Stroke Pumping Units: A Case Study of Economic Comparison in a Low-Volume Well. The paper captures the topic of shifting to rod lift sooner by transitioning from an ESP to a long-stroke Rotaflex pumping unit and the benefit of saving workover costs while increasing production well above traditional beam pumping systems.
The shift to rod lift sooner had been successful due to the long, slow stroke of the vertical system, allowing for increased pump fillage and higher production rates. In this case, the long-stroke system proved to reduce power costs by 37%, reduce workover costs by 91% and combined reduced opex by 62%, all while producing a fluid rate of 1,180 STB/D in either system. This has been a fantastic paper to show the benefits of transitioning to rod lift sooner with huge success.
Meadows: Permanent magnet motors (PPM) are a step change in the ESP industry. They generate high torque on startup, are highly efficient, and have a wider operating range than traditional motors. However, they can generate electricity anytime fluid flows through the pump and forces system rotation, even when powered off, energizing the power cable to the surface. A major limitation to global field adoption is the danger of this hazardous back-EMF associated with motor rotation and energization during installation, retrieval, and workover operations.
In response to this industrywide HSE problem, our team has developed the industry’s first engineered PMM safety barrier that prevents the ESP pump from spinning the PMM, eliminating voltage generation at the surface. We were excited to present this HSE innovation at the 2023 SPE Gulf Coast Section—Electric Submersible Pumps Symposium in SPE 214745, Permanent Magnet Motor Safety—The Big Short Question.
JPT: How have advancements in technology impacted artificial lift? Are there any technologies that you find particularly promising for the future?
Stephenson: Mostly, advancements in artificial lift technology have been incremental improvements. The most-used artificial lift methods have existed for decades or even longer. Technologies I think could make a difference include permanent magnet motors in ESP, sucker rod pump, and PCP installations, improved downhole gas separation and gas-handling devices, improved surveillance software, and the application of artificial intelligence/machine learning techniques.
Romer: I see technology advancements have impacted artificial lift in several ways, including:
- Remote monitoring and control improvements, including accessibility and cost—variable frequency drives versus pumpoff controllers, for example
- Ability to optimize more with less effort, providing quicker transfer of knowledge
- Data storage, communication, and sensing improvements
- Once unheard of to run bottomhole pressure gauges onshore and now they’re almost standard with gas-lift completions
- Extra digital surface sensors once required justification, but now they’re expected
- Surface-controlled (electric or hydraulic) gas lift has the potential to bring optimization to a lift method that’s notoriously difficult to optimize with additional benefits over mechanical valves. The decreasing cost of downhole electrical devices and improving reliability are spurring adoption.
- High-speed ESPs, particularly for offshore installation through-tubing, which may be able to increase the life of offshore wells as the technology increases in maturity
- Electric rod pumps are in early development, but a few vendors are working on them
Labrador: Artificial lift technology advances have allowed us to install and run the systems in more complex trajectory wells and produce them reliably. Additionally, it has allowed us to be aligned with the commitment to care for the environment.
Also, AL technology has impacted the artificial lift world positively. Who could imagine we would have more efficient motors installed at the surface and the bottom of the well? Or that we could challenge the boundaries of each AL according to the needs of the field and sufficiently produce them?
We must keep challenging our boundaries and making bigger efforts in this important part of the oil and gas industry. The relationship between OFS and E&P companies plays an important role: the operator’s needs and the service companies’ constant solutions to save on downtime and lost production.
Noonan: Instrumentation advancements allowed us to understand the physics of how artificial lift systems work internally. Before, we didn’t have the advancements in instrumentation to put sensors inside the various pumps or lift systems to really measure and understand what was happening inside. It was always theories and rules of thumb. But once we understood the fundamentals of each basic lift system, we knew how to design it properly—whether it was how we sized it or the materials used—to ensure it was the right design for the right environment. Also, permanent magnet and linear motors will make an impact (extinction of the rod string).
Jaua: We see the dramatic increase in lifting systems’ average run life and their survivability operating under extreme environments in the past 20 years; it is evident that technological advancements have had a huge impact on the artificial lift industry.
Artificial lift systems are installed faster, safer, last longer, and operate in wells that were impossible to operate not long ago. All thanks to improved designs, advanced materials, and evolved processes and practices.
The lifting system with the most promising growth potential is PCP, particularly the rodless version powered by downhole permanent magnet motors, which is more suitable for deviated wells.
Current elastomer compositions and manufacturing processes prevent the PCPs from surviving temperatures above 200°F and produce fluids with high aromatics content, frequently found in lighter oils.
New technologies and manufacturing processes are under development that will allow PCPs to perform in hotter wells and produce lighter oils. This will result in a viable alternative to efficiently producing wells, replacing rod lifting systems with a higher frequency of failures in deviated wells.
Leslie: The artificial lift market continues to see new technology in many shapes and forms. Whether it is advancement in a long-stroke system, a beam pumping system, advancement in ESP technology, or advancement in downhole technology, there continue to be new developments and products every year.
The one technology that continues to advance rapidly with huge impacts on field operations is the digital/automation space. The future of field operations will be centered around automation. The future will continue remote monitoring with autonomous control and failure prediction well ahead of where we are today. The autonomous field of the future will utilize sensors and monitors to detect failures before they happen, allowing operators to save on downtime and lost production. Digital integration and automation are the most impactful technologies for artificial lift in the future.
JPT: What are the most pressing challenges and opportunities facing the artificial lift sector today?
Stephenson: The most pressing challenges I see include the application of artificial lift in unconventional shale oil wells and in subsea/deepwater installations.
Shale oil wells can be challenging to lift due to their high gas-to-liquid ratios, sand production, sharp production decline in early life, and horizontal well trajectory. All these issues can decrease equipment reliability and/or deferred production.
Applying artificial lift systems in subsea installations can be challenging because of the high intervention costs associated with these wells. In a perfect world, we would like to install an artificial lift system in these applications that can survive for 10 years or more while boosting production.
Romer: I see the most pressing challenges in the following areas:
- Unconventional wells: How do you extend the economic life of wells when they aren’t designed for late-life lift: crooked wells, high gas, small casing, low rates, and long horizontals
- Lift methods designed for rapid reservoir depletion as current methods are not
- Lift method changes: knowing when it’s the right time and what to do
- Subsea: improving through-tubing options and applying artificial lift at the beginning of the well’s life because you may not be able to come back later to retrofit
Labrador: The challenge will always be to be better than yesterday and to have better performance and efficiency in ALS equipment than the previous year. Reducing the carbon footprint through ALS is a commitment we all have right now for the planet and future generations. The opportunity is to continue developing technology to make artificial lift systems more efficient and cleaner for the environment. Moreover, digital integration and automation technologies will help us to impact the future for artificial lift.
Also, being competitive in quality, performance, and price is something that can’t be left behind.
Noonan: Advancements in manufacturing have not kept pace. Many facilities have old equipment and still rely on too much human interaction, which can lead to quality-assurance issues. The technical differentiation between vendors has shrunk, so the battle for business will rely on manufacturing, assembly, and service quality.
Jaua: All oil wells eventually require artificial lift systems to produce, meaning millions of wells operating globally, requiring a constant power source available 24/7. This makes lifting systems one of the industry’s largest emitters of carbon dioxide. The greatest challenge will be the evolution of lift-system selection and sizing that puts efficiency levels as a top priority. It also represents an opportunity for those technology companies committed to developing new solutions to reduce their carbon footprint.
Leslie: There are several key challenges facing the artificial lift sector today, including limited resources, the need for consolidation, and, most importantly, a consistent supply chain with minimal reductions in delivery.
The oil and gas market has received a bad reputation as dirty and cyclical, driving young talent to avoid the industry. This reputation limits the amount of new talent in the industry, creating challenges for both E&P and OFS companies. We must find a way to recruit and retain talent better going forward.
The artificial lift landscape has too many competitors. There is a major need for consolidation, ultimately benefiting the end user and OFS companies. Finally, most artificial lift market products are produced outside North America due to the high production cost and the demand for lower-cost products. This creates an incredible challenge for OFS companies to work diligently to find alternative countries and manufacturing centers to supply products to all customers in artificial lift. These three areas are just some of the critical challenges facing the ALS market today.
Meadows: In terms of challenges facing the artificial lift sector today, the main concerns we continue to hear from our customers are centered around increasing the run life and reliability of ESP systems, reducing costs and downtime of artificial lift systems in general, and maximizing and optimizing production. Our customers all want to unlock the lowest-carbon, shortest-cycle barrels possible. To do this, they need a partner to help them better manage power consumption and costs and boost pump speeds and production.
We all know new drilling is slowing down while the world’s energy demands grow. New energy sources can only pick up some of that demand, which means we’ll need to get better at getting more out of the reservoirs we’ve already drilled, and ESPs will be a critical part of that.
JPT: Where will artificial lift applications be heading in the next decade? Are there any emerging trends or technologies that will shape the future?
Stephenson: In the next decade, I expect to see a greater emphasis on
- Lifting low-rate, mature shale oil wells.
- Reducing emissions.
- Minimizing lift costs.
- Improving overall system reliability.
- Applying artificial lift and subsea boosting to extend the life of deepwater installations.
Romer: I expect to see in the next decade
- More PMM applications on, for example, surface pumpjacks and PCPs.
- Closed-loop optimization of surface-controlled gas-lift systems.
- Through-tubing high-speed ESPs.
- Data-driven, fieldwide artificial lift system optimization.
- Optimization and artificial lift selection based on emissions/power usage. The industry is already seeing this in some parts of the world, for example, in thermal lift applications in Alberta.
Labrador: The technologies that allow us to produce complex wells efficiently and cleanly for the ecosystem will be what will govern the next decade. The world is changing, and we must change with it.
Noonan: Material advancements will make all the difference. Rod strings will be obsolete.
Jaua: I see artificial lift applications accelerating the adoption and implementation of artificial intelligence and machine learning solutions. For instance, until today, designing, selecting, and optimizing lifting systems required a technical staff to make and control decisions.
It is already happening today—but not fully adopted—that machines are gathering and processing vast sources of historical data and, in seconds, without human interaction, selecting the best lifting system, sizing, and features required for every well. Allowing a fully autonomous operation and increased failure predictability levels make the entire operation more efficient.
Digital solutions are still in the infant stages in the artificial lift sector, but without any doubt, they are destined to lead a more efficient and sustainable O&G industry.
Leslie: The future for artificial lift will be centered around digital technology and operator energy consumption. The evolution of PMM will be significant for operating all artificial lift forms more safely and energy efficient. PMMs have already been installed on basically every form of lift today with much success, but adoption has been slow as operators are still in the testing phase. In addition, the digital space will bring new technology with capacitors and storage of excess energy to maximize efficiency and productivity in the field. These technologies are just arriving to the market and producing significant energy savings, and the future will only get better as we move forward with this new technology.
Meadows: Automation simplifies decision-making. Digital will continue to shape the future by optimizing and increasing production. Variable speed drives (VSDs) will also play an important role in reducing power consumption. We’re testing a new VSD slated for release later this year to reduce power consumption by up to 20% over our most-efficient drive. A virtual VSD interface will also be integrated, enabling operators and service companies to adjust drive settings from anywhere in the world remotely.
The switch from induction motors to PMMs is also where the future is headed. We want to ensure we’re positioned to ensure this happens as quickly and safely as possible, so we are excited to champion the industry’s first engineered PMM safety module. This new module prevents the ESP pump from spinning the PMM, eliminating voltage generation at the surface for safer, simpler operations.
This article is part of a 3-part artificial lift series as part of JPT’s 75th Anniversary content. Read more in Experts Give Career Advice for Future Artificial Lift Professionals: “Do Not be Scared to Try Something Different” and Artificial Lift: 25 Years of Change Tracked in the Pages of JPT.