Nodding donkeys. Thirsty birds. Rocking horses. All are playful nicknames for the oil and gas icon known as a pumpjack.
To the uninformed, the pumpjack is a thing-a-ma-jig that has something to do with oil, probably “fracking” because that’s what drilling rigs do, right?
But as an industry-educated and well-informed reader of JPT, you know this is inaccurate.
By whatever name you call it, you know that the pumpjack is the visible manifestation of an invisible physics equation, a mechanism buried deep underground that lifts reservoir fluids to the surface. You also know it is one type of artificial lift available in a stable of systems with equally curious and technical names like progressive cavity, plunger, jet, gas lift, and electrical submersible pump (ESP).
While there is no global repository of artificial lift statistics, industry observers estimate that 90 to 95% of the world’s producing wells use artificial lift, as noted in a 2013 JPT story on the challenges and opportunities for artificial lift.
Artificial lift, as applied in oil and gas production, has existed for over 100 years. A 2014 JPT story laid out a brief history of the practice,sharing how the walking beam principle dates back to at least 476 CE when used in Egypt, and evidence of the use of sucker rods to lift fluids has been excavated from the homes of wealthier families in the early days of the Roman Empire.
Even as we leap forward to the modern-day application of artificial lift systems, many techniques and technologies resemble their original designs. How these systems are applied has changed, especially in the past decade-plus with the emergence of shale.
As highlighted in a JPT story on the past 25 years of technology advances, the industry underwent a robust era of technology development in its rush to crack the shale development riddle. Since 1999, the industry also delivered a 36% increase in global supplies, as noted in this JPT story celebrating this industry’s biggest innovations.
1999 represents an interesting turning point in the industry’s technological journey. Also, it is the last time JPT editors took the opportunity to celebrate the publication as it turned 50 years old that year.
What follows are a few highlights from JPT’s coverage of advances and changes made in artificial lift applications and practices over the past quarter century.
Adaptation and Transformation
A circular beauty is realized in studying the history of artificial lift. For example, its place in the pantheon of published papers dates to 1925, with its first paper on a technique that is still highly relevant almost 100 years after its publication.
“The gas lift is able to raise more oil from a well than any kind of a pump. Wells pumping 300 or 400 bbl daily have been caused to produce more than 1,000 bbl per day by the gas lift without injury to the wells,” said R.P. McLaughlin in a short paper titled “The Gas Lift Method of Pumping Wells.”
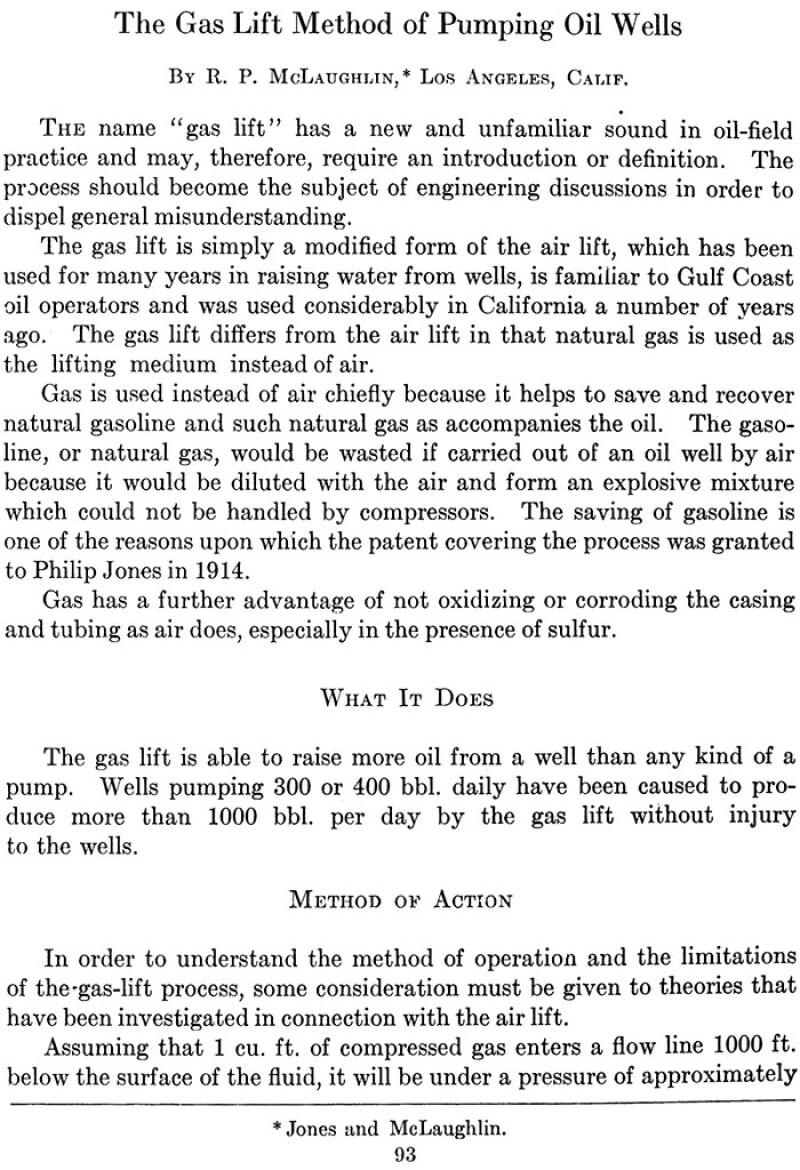
It is the oldest paper on artificial lift listed in OnePetro.
There’s an old maxim about how those who do not study history are doomed to repeat it. This rings true, especially when paired with artificial lift expert—and self-professed ESP guy—Mike Berry’s comment in a 2017 Technology Focus overview in which he said, “As much as it pains me to admit it, by the book, gas lift should be the default lift method for shale wells.”
And therein lies the circularity of artificial lift’s modern-day history. It is a space populated by innovators and tinkerers, by those that see failure as an opportunity to try again until the system works.
A 2022 JPT story on the sector’s ability to adapt and then re-adapt to meet the changing demands of production touched on how adaptation and experimentation have created a new toolbox.
“Ten years ago, you wouldn’t have seen much gas lift used in the Permian Basin. Old school, traditional methods of lift, like electrical submersible pumps or rod pumps, were used there then. Gas lift, progressing cavity pumps (PCPs), or some of the other traditional methods weren’t used because these types were not as familiar to operators. They went with what they knew,” said Shauna Noonan, 2020 SPE President and senior director of global supply chain initiatives and Fellow for Occidental Petroleum, in the article.
Industry events like those sponsored by SPE and other technical groups have brought greater awareness to the industry of the different types of lift systems used across the globe.
“By bringing all the lift types together, we can learn from one another and have more tools in our toolbox to choose from. We’re starting to see that change, especially in the growth of new wells where we’re picking the right lift method at the time, and not what they knew,” she said.
“It’s an interesting time. All the gas-lift people that used to be in Louisiana working in the Gulf of Mexico are now in Midland,” Noonan added. “Gas lift is one of the fastest-growing lift methods out there, displacing the other types.”
But gas lift didn’t get its start in the Cajun State. There’s a 1926 article available in OnePetro on its application in the Mid-Continent oil fields of Oklahoma.
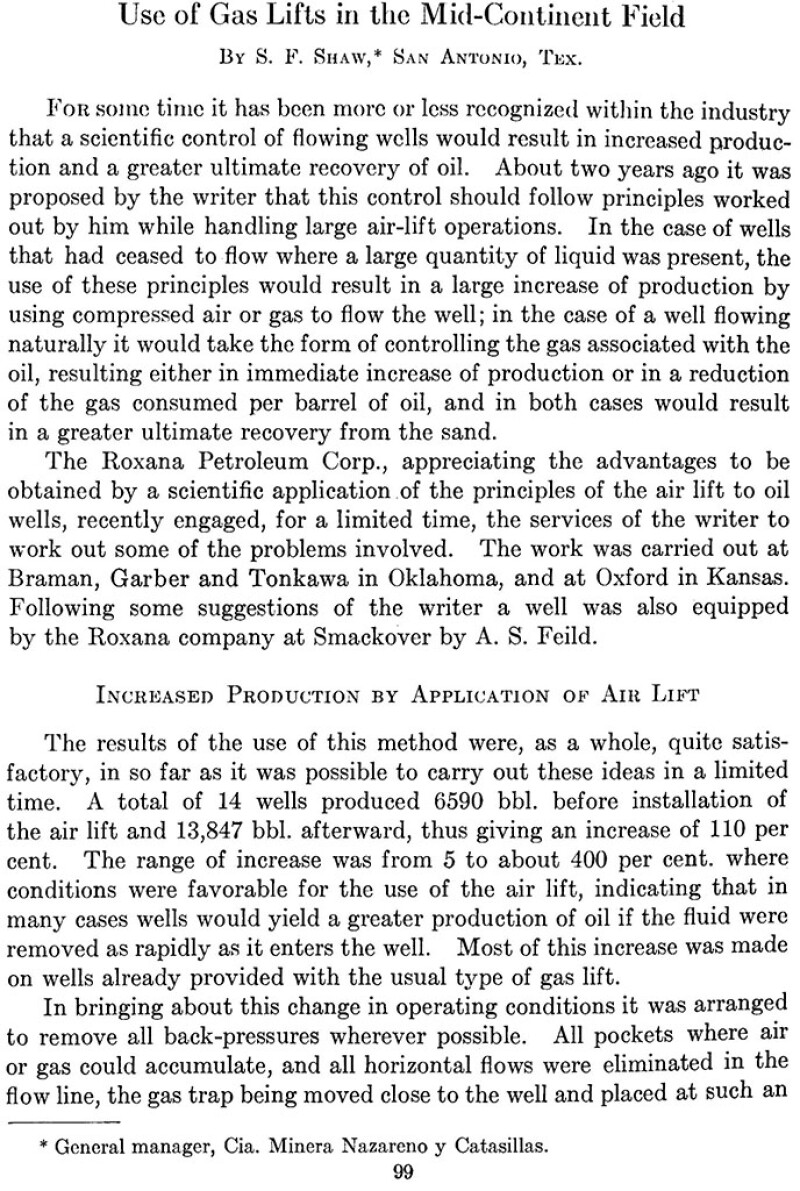
A contributor to this circularity was the limited avenues for knowledge sharing, as noted by a few in this article’s companion piece, “7 Industry Leaders Share Their Insights on the Past, Present, and Future of Artificial Lift.”
Before 2014, when SPE held its first Artificial Lift Conference and Exhibition (ALCE) in Houston, most technical presentations were delivered at non-SPE events with no technical paper accompanying them, according to Greg Stephenson, chief production engineer for Occidental Petroleum.
“If you weren’t physically present in the room where the presentation was delivered, you had virtually no way to access the information being shared,” he said, noting that the ALCE events in the Americas and Middle East, along with the ESP Symposium, have provided a wealth of papers to learn and build on.
“The requirement to write a manuscript increased the technical rigor of these works and made them more useful to industry professionals,” Stephenson said.
The 2024 edition of the ALCE–Americas will be held from 20–24 August in The Woodlands, Texas, with the theme "Modern Artificial Lift—Adapting to a Changing Industry.”
A quick check of the OnePetro database shows that in the 10 years from 1999 to 2009, 272 articles on artificial lift were published in JPT. That number grew 22% to 333 articles published between 2010 and 2020. There have been 86 articles published between 2021 and February.
Look to those innovators who accentuated the positives of gas lift and plunger lift to create the gas-assisted plunger lift (GAPL) system. The evolution of hybrid systems built from gas-lift principles can easily be traced through the pages of OnePetro and JPT.
In just one of many examples, a technical paper (SPE 48840) featured in a May 1999 Technology Focus shared how a gas-lift-jet-pump (GLJP) application delivered a significant production increase with the same gas-injection volume obtained in two wells during a test in a field located offshore Lake Maracaibo in Venezuela. The GLJP performed successfully when installed in a well containing sand with a high gas/oil ratio above the main liquid-producing zone, providing the capability to produce without surface gas injection.
A technical paper (SPE 64466) featured in a May 2001 Technology Focus shared how an ESP and automated gas-lift completion was developed to overcome production challenges in the Stag field located offshore Dampier, Australia. The flow from the well's horizontal section had a high gas fraction, continuously slugged, and carried large sand volumes. And the reservoir pressure depleted more rapidly than expected.
It has the hallmark challenges for shale production, begging whether something similar would work for shale. Maybe it has, but a paper has not been published in OnePetro or reported on in JPT. A check of OnePetro reveals that SPE 64466 has been cited in seven papers for conferences held in the Asia Pacific and Middle East regions.
Artificial Lift Tech Snapshots
Perhaps the only good thing to come out of a revolution is that people talk more. This was certainly the shale revolution's impact on artificial lift. Finding solutions to arrest the rapid decline in production was just one of many challenges the industry had to wrangle. Other issues, like gas and solids entering the wellbore and long, undulating lateral wellbores, also present pumping challenges.
Add to this various business and operational goals, like minimizing capex, opex, and downtime while maximizing the well’s life and production output, the challenges of artificially lifting shale reservoirs are complex.
Artificial lift experts warned about these challenges in a JPT story in 2015 regarding long-term production in horizontal wells. Many of these challenges remain in 2024. However, with more than 130,000 shale wells drilled and put into production in the major US basins, the industry is improving with the data and the knowledge of what will and will not work when applying artificial lift technologies.
Fortunately, new technologies are making great inroads towards improving production. Improved sucker rod coatings, better downhole separation techniques, advances in data and automation, and increased use of permanent magnet motors are all making an impact.
Improved Sucker Rods. A JPT story in November 2022 asks a question of change; namely, if a better sucker rod is built, will buyers be willing to change. Shale wells commonly produce corrosive fluids, paraffin, and asphaltenes.
One example of a sucker rod improvement discussed in the story is a protective anodic coating for continuous sucker rods that prevents corrosion and reduces drag when the rod rubs against the surrounding tubing. The paper (SPE 209751) presented at the 2022 ALCE-Americas, highlights the ChampionX product which relies on a powdered metal coating that short-circuits electrochemical reactions that cause rapid corrosion.
Better Downhole Separation. Addressing the challenge of gas and solids separation for sucker rod or ESP pumping, a relatively new design named the WhaleShark takes advantage of multiphase liquid flow reversals to ensure the pump remains full of liquid with every stroke while also protecting the pump from erratic load conditions.
SPE 209755 was presented at the 2022 ALCE and featured in a JPT story in November 2022. The Oilfy product sits above the bend of the horizontal wellbore, in the vertical section. It uses an upward-facing, open-mouth collector intake that captures liquid that naturally falls backward due to gravity.
To encourage more liquid fallback, the area above the collector is the gas separation region that has no annulus and uses an oval-shaped eccentric (on the side), rather than centric, pump intake tube designed to slow fluid velocities while improving liquid fallback downward into the collector.
Advances in Data. Another of the significant advances in artificial lift is the increasing use of digital systems and automation to capture, compute, monitor, and react to well data. Regardless of the company's size, from supermajor to smaller privately held operators, these data are critical to operations, as noted in a January 2023 JPT article on how digitalization projects are delivering returns for operators.
In it, a pair of Texas-based private operators shared how they apply data using Datagration’s PetroVisor to improve their artificial lift operations. Hess shared how it developed the digital twin of its Stampede production platform in the US Gulf of Mexico as part of a pilot project to enable process equipment condition monitoring on key topsides equipment.
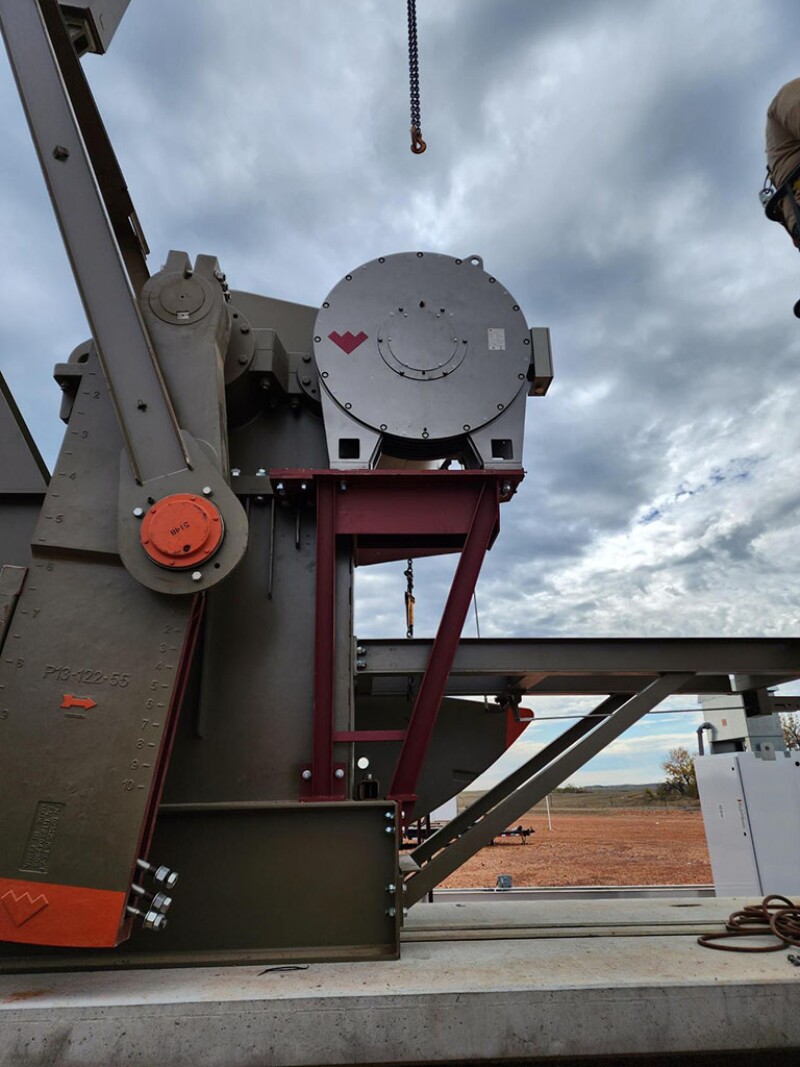
PMM. The growing adoption of permanent magnet motors (PMM) has played out on the pages of JPT, starting with a July 2009 article on their application in oil production. In it, the benefits and application of PMMs rather than asynchronous submersible electric motors used to drive ESPs at the time were discussed. PMMs in ESPs were just beginning to achieve wider application at the time.
In the more than 10 years since the article, PMMs have entered various applications. A March 2023 JPT technical synopsis shared results of how PMMs were used to help reduce the carbon footprint in artificial lift systems used in Colombia. The operator installed and operated PMMs on ESPs, PCPs with an ESP PMM, PCP PMM, and sucker rod pump.
The implementation of the PMM technology was successful, delivering power savings of more than 15% and lifting cost optimization. The energy-savings effect obtained by each system translated into a forecast reduction of 24,500 tons of carbon dioxide equivalent and aligned with the operator’s sustainability objectives.
In February, Weatherford International confirmed it had successfully installed a PMM-powered reciprocating rod-lift system in the Bakken Shale as part of a seven-well pilot test for independent producer Chord Energy. The oilfield technology provider uses a PMM on its PCP systems. It said this installation is the first application of a PMM on a reciprocating rod-lift system in its North American operations.
The past 25 years have demonstrated what Mauricio Prado, professor emeritus at The University of Tulsa, wrote in his May 2003 Artificial Lift Technology Overview that “this area, that a few years ago was seen as a mature one, is proving to still be a fertile place for innovation, research, and development.”
While it is impossible to know what the next 25 years of artificial lift advances will look like, it will certainly continue to be an engaging space to watch and report on.
This article is part of a 3-part artificial lift series as part of JPT’s 75th Anniversary content. Read more in Experts Give Career Advice for Future Artificial Lift Professionals: “Do Not be Scared to Try Something Different” and 7 Industry Leaders Share Their Insights on the Past, Present, and Future of Artificial Lift.
For Further Reading
AI Firm Ambyint’s New Bakken Deal with Equinor Moves the Industry Another Step Closer to the Edge by T. Jacobs. JPT.
Artificial Lift Experience in Malaysia and Indonesia and the Way Forward by F. Mehran, Halliburton; K. Idris, Petronas; and Dadik Kusuma, Petramina. JPT.
Permian Operators Collaborate to Improve Understanding and Performance of Unconventional Reservoirs by Y. Pradhan. JPT.
Artificial Lift Market To Reach $14 Billion in 2025 by J. Presley. JPT.
Now Is The Time for Gas Lift To Live Up to Its Potential by S. Rassenfoss. JPT.