The past 25 years marked the emergence of shale as the next frontier for oil and gas production, and JPT’s Houston office was right in the middle of it all.
Credit for starting this disruptive change goes to George P. Mitchell who led a 17-year-long effort to extract gas from the ultratight rock in the Barnett formation. A JPT story described how this effort was finally looking like a significant, profitable business in 1998 when Mitchell Energy’s engineers turned to lower-cost slickwater fracturing in their vertical wells.
The success of this trial-and-error engineering marathon drew little notice at the time. But that seed grew into a huge business based on technology that showed it was possible to profitably produce oil and gas from virtually impermeable rock using large-scale fracturing and ever-longer horizontal wells.
In the coming decades this reverberated through drilling, fracturing, and reservoir engineering, disciplines whose physics-based view of the world could not predict how that would happen.
As JPT’s staff grew with the addition of reporters covering emerging technology, there was no ignoring what was going on around us.
The magazine highlighted futuristic reservoir monitoring ideas in Saudi Arabia and advances in deepwater technology in Brazil, but the booms and busts of this high-profile business that delivered more oil than profits kept changing in interesting ways.
The first SPE Hydraulic Fracturing Technology Conference I covered in 2011 was amazing and puzzling to this technology novice. I wondered how they could create fractured areas that looked like shoe boxes.
At an early show, a speaker advised those who believed that fracturing knowledge began with shale to look back further in OnePetro.
One of those paper authors, then and now, is Dave Cramer, senior engineering fellow for ConocoPhillips, who began learning fracturing when he graduated from college with a business administration degree and got a job with Western Company of North America.
The singular change over the past 25 years is how much fracturing has been scaled up. “It like a factory out there, and it was not a factory when we started,” he said.
In the previous 25 years, fracturing experts were doing a lot of innovative things. He proudly remembers being involved in a job for Amoco where they pumped 600,000 gallons of gelled fluids and 1.3 million pounds of large-mesh sand into a 35-ft tight sandstone section of a well in the DJ Basin in Colorado.
The morning he told that story he was evaluating a well completed in Canada where ConocoPhillips used slickwater to pump 970,000 pounds of sand per frac stage.
In some ways the job in 1978 looms larger in his mind. The whole job was aimed at a single target and was sophisticated: They pumped five different fluid mixtures as the job progressed based on their lab testing and fracture modeling.
While he thinks the technical skills of those fracturing tight rock back then are underestimated, wells now with laterals that are miles long and hundreds of clusters to stimulate are so much more complex, which has created an insatiable appetite for data by engineers continually feeling pressure for greater production and efficiency.
“Diagnostics are a lot better. Back then the only thing available was treating pressure analysis,” he said. Now in addition to that there are multiple measures from fiber-optic cables, downhole images of perforations, microseismic, and multiple test sites evaluating the pros and cons of each of these diagnostic ingredients.
To keep up with the scale and pace of the jobs, the hardware and methods used to deliver the supplies and do the fracturing have rapidly evolved. There are now ways to fracture multiple wells at the same time, digitally control fracturing, and use massive pumps in a push to cut emissions and costs by phasing out diesel-fueled pumps.
After the 2014 oil price plunge, cost cutting became an obsession and engineers found cheaper alternatives.
A decade ago, operators were willing to pay to import sand from Wisconsin based on how they measured the quality of the grains. Now much of what is used is mined nearby, virtually eliminating the cost of shipping, and these fine-grained substitutes seem good enough. “We tried junkier sand and saw little to no production loss,” Cramer said.
While fracture modeling has gotten a lot more sophisticated, he said that testing by trial and error is needed because it is so hard to predict how a change will turn out when pumped into a formation.
Progress will continue depending on those who say, “Let’s try it; it sounds crazy, but let’s see how the well produces.”
What follows are highlights from JPT’s coverage of changes in fracturing, drilling, and reservoir engineering over the past 25 years.
If You Build an Automated Rig, What Do You Tell It To Do?
One vision of the future of the oil business in the late 1990s was a picture of the first driller’s cabins made by NOV.
It was a big change from the days when drillers worked on the drilling floor with a hand on the brake handle.
The display screens, joysticks, and high-performance chairs in the new drilling booths were all common sights outside drilling rigs. But this new command center was a sign that the digital world had begun to intrude on the largely hydraulics-based world of exploration and production.
“Prior to my time in the industry the focus in drilling was on more muscle and working harder,” said Trey Mebane, who now advises startups. Since then, more muscle still matters, but so do the digital control systems and data flowing from them.
He was one of the newcomers hired in the mid-1990s by NOV and other service companies to make that change. It needed his knowledge of computer science and technology commercialization to help it sell a new generation of equipment.
Equipment providers had to turn to computer-based digital control systems used widely in industry when it was clear that the equipment on the next generation of offshore drilling rigs was too complex for traditional hydraulic control systems.
When he asked a driller back then about the digital displays and the first-generation autodriller, he was told that was all fine. But the best thing was working while seated on the comfortable chair in a climate-controlled cabin. All it lacked was a cupholder—a problem that was soon fixed.
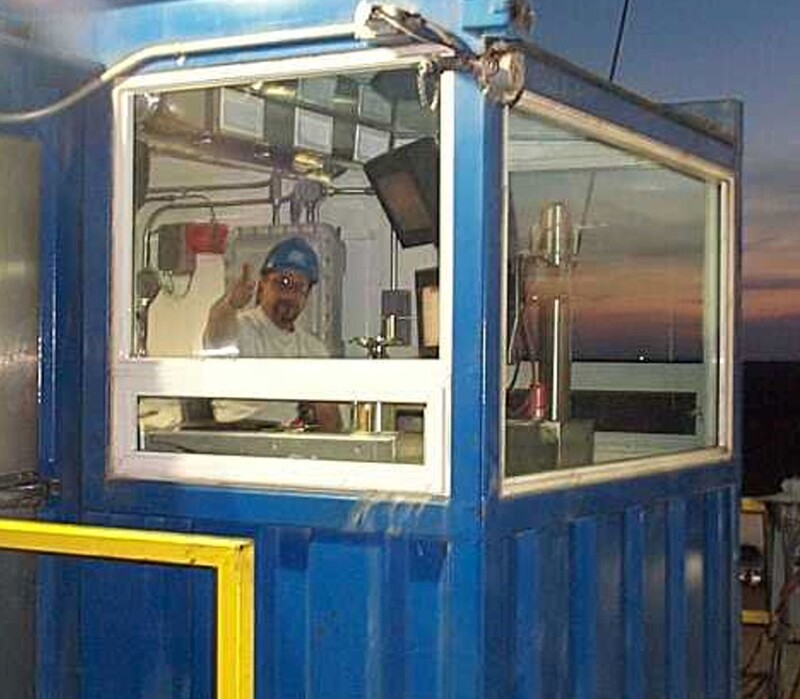
And Then
What was not obvious 25 years ago was how the digital data flow and processing power required to create this control system would eventually lead to programmable control systems that have changed the work of drilling engineers.
By 2008, the digital generation in service companies and oil companies had created the SPE Drilling Systems Automation Technical Section with a goal of moving the industry toward the day when drilling rigs would be fully automated.
At the time, the idea of pushing a button to drill a well sounded inevitable. That year, Helmerich & Payne (H&P) launched their long-term effort to gather and analyze data as the basis for innovative digital control systems. Years later they showed the value of that bet by doubling down to build a fleet of FlexRigs which offered both more brawn plus brains that reduced downtime for more efficient drilling.
In 2018, after H&P bought the company that made the program, H&P took the next logical step—feeding those commands into the drilling control system for “factory-like consistency,” said John Lindsay.
Innovative operators and service companies were focused on building the automated drilling rig of the future. The focus abruptly shifted after the 2014 oil price crash.
Apache dropped its program to develop a fully automated rig. But not long after that, it began working on ways to drill better by making the most of data, software, and advanced statistical analysis.
“We saw that there was at least a small opportunity to do something more with our rig data—that 1-Hz real-time data—by combining it and mashing it up with contextual data so that it could be something useful,” said Michael Behounek, the leader of the project who has since retired and is working as a consultant.
In other words, they wanted to figure out how best to manage the job and ensure those procedures were followed. Traditionally the driller was more likely to be told: “There is your bit, go run it, and do your best. This is a vastly different thing,”said Fred Dupriest, a Texas A&M University professor.
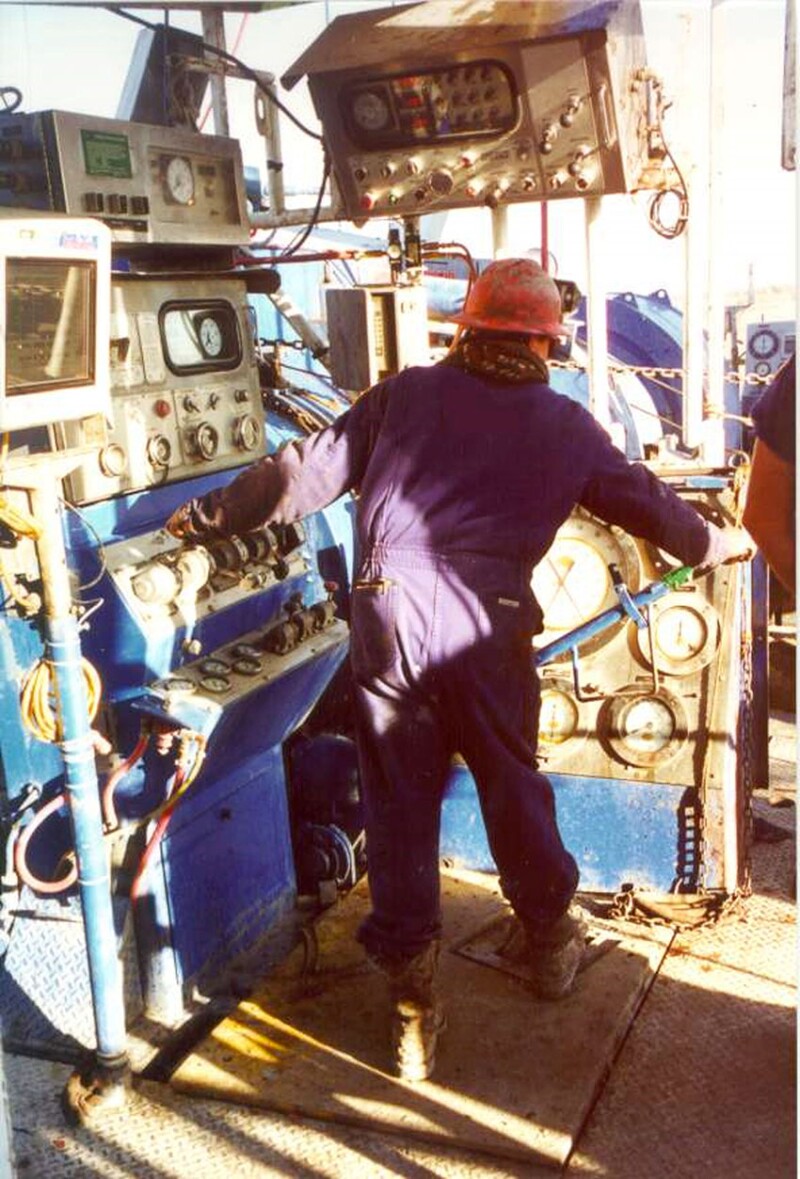
Increasingly, digital control systems on rigs make it possible to program in best practices to ensure they are followed. And the job of engineers is to look out for flaws in the system and fix them.
Matt Isbell, drilling engineering advisor for Hess, likened its process improvement program to a battle of wits. He said, “People learn from that and it’s not too long before they have ideas that can be put into practice that can improve whatever the operation is,” in this story.
Over 8 years, Apache’s drilling improvement methods delivered 10% year-over-year drilling costs savings and were used by rig crews on more than 1,700 wells in all sorts of plays.
The probabilistic drilling advisor, though, has its limits. A paper describing the system said it “only enables the opportunity—it is the field personnel and engineers taking the proper actions and decisions offered by the system that deliver the improvement.”
No Tree Roots, Please
A JPT story in 2015 asked the question: What does a fracture look like?
It was provoked by engineers and geoscientists who were irked by fracturing illustrations, like Norm Warpinski, a Halliburton fellow, who said, “They do not look like tree roots. Things do not shatter like glass and run in all directions.”
Others also complained about fracturing illustrations that looked like lightning bolts or tree roots.
While geologists pointed to natural models, Mike Smith, the founder and president of the fracturing consulting firm NSI Technologies, said, “My mental image varies by formation—by the geological environment. It depends on where you are.”
He described the force of fracturing fluid interactions with a formation. “It goes to hit the first natural fracture and turns whichever way, then goes along until it hits another fracture, splits off again, and starts off across the country.”
In the years since, there have been advances in finding ways to observe fracture growth, interactions, and how they change over time, including papers from a series of fracturing test sites.
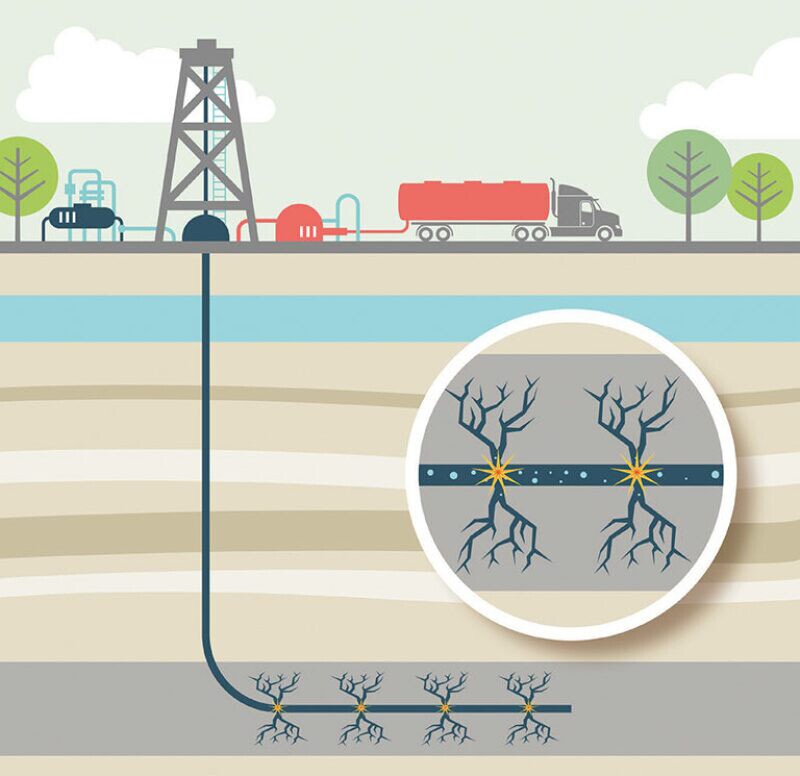
Based on those, an artist would surround the well with a massive number of fractures—most as thin as fine thread—with a few large cracks out further. On occasion a few of those can extend out thousands of feet.
The shape of the fractured area is rarely symmetrical. Sometimes growth is blocked by sizable faults. A depleted zone around an old producing well will attract fractures, which may well hit the other well, reducing production for all the wells.
Recent advances in stress monitoring can even track fracture growth. Patterns in the signal can define fracture development, which has proved more accurate than microseismic.
In seems certain by now that fractures vary.
Perfection Is in the Details
Progress downhole has come from paying attention to details, often small ones, such as holes perforated in the casing for pressure pumping.
They expected to see differences based on previous research using fiber optics indicating the first perforations in a series encountered by the fluid resulted in big fracs, while later ones were hardly stimulated. Downhole images allowed engineers to see that in their wells. And eventually, as the technology improved, measurements could be made.
That evidence led to a period of experimentation. Ultimately, that led to most operators choosing limited-entry methods to ensure all the perforation holes were stimulated. They focused on shooting uniform holes that limited flows to better distribute the water and sand based on plans to pump enough water and sand to stimulate all of them.
Flows still vary, but paying attention to those holes has proven its value.
Gummy Bears From Hell
For years, globs of black gum were flowing up from wells in Oklahoma, often clogging production equipment.
The source of these “gummy bears” remained a mystery until a story 2020 reported on a paper by Mark Van Domelen, vice president for technology at Downhole Chemical Solutions. He identified the source: Iron-rich rock in the wells was interacting with high concentrations of certain types of friction reducers to create a rubbery polymer.
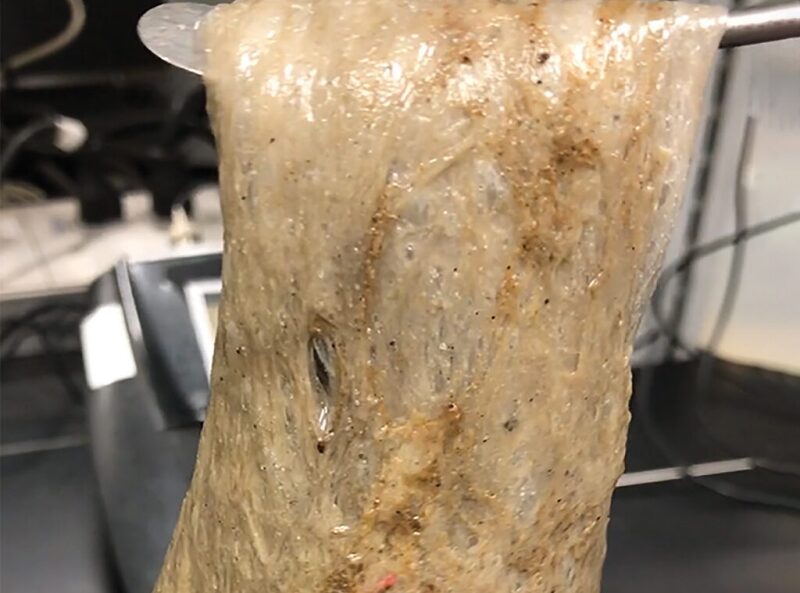
The problem was the positive charge of the polymers added to fracturing fluid to reduce resistance and often to thicken it to allow it to transport more sand. When word got out in JPT, producers in other places noticed the problems.
Buyers started advising customers to avoid formulations with a positive charge when reactive chemicals are present.
It was a small problem for a huge industry, but it raised questions about other chemical reactions such as surfactants that quickly degrade in the ground or polymer gunk clogging fracture networks.
George King, a petroleum engineering consultant, offered a possible root cause based on his experience teaching. “Damn friction reducers and iron! Engineers do not understand chemistry!”
Thinking Outside the Lateral
Online mentions of the job initially sounded like something that a drilling engineer might have done on a dare. It turned out to be a way to drill a well under extreme circumstances. The horseshoe well filled a gap in a well pad after the planned vertical well for that lateral could not be drilled due to severe mud losses.
They extended another well on the pad with a curving loop over the 5,000-ft-long path of the second lateral, and then fractured it. It was all done with off-the-shelf equipment.
“What’s great about this well is not the fact that it’s new, novel, and innovative,” said David Gibson, cofounder and chief executive of drilling market research firm Gibson Reports, who followed the work. “It’s that it starts amazing conversations. Conversations about challenging the status quo—and given the current market and climate, we all need to follow Shell’s lead and think outside the box on all fronts.”
Do Not Slow Down
While the Pace-R801 was full of automated functions, “the robot is the one that gets most people interested and excited,” said Travis Purvis, senior vice president, global operations for Nabors Industries.
The amazingly adept robot drew a lot of customer interest, but humans are generally still at the controls when it comes to moving pipe. At an IADC meeting, Paul Pastusek, drilling mechanics advisor for ExxonMobil, offered a simple explanation: “Humans can move really fast.”
Drilling the Future
In the future drillers may be drilling laterals through granite to heat steam for geothermal power plants.
If that proves to be true, they may be relying on methods for faster drilling developed more than 25 years ago by Fred Dupriest, who was then working for ExxonMobil.
The high cost of drilling in hard rock has inspired ideas that sound like science fiction, like plasma drilling. But the first steps toward building massive geologic heat-transfer systems will focus on off-the-shelf drilling and fracturing equipment.
While Dupriest, who taught his method to drillers at the test site, acknowledged that progress is likely slower in what he described as “5,000 ft of kitchen countertop,” he added that “the types of issues that constrain the drill rate, and the way you deal with them, are no different.”
Dumping Old Software Friends
The chief information officer for Chevron, Bill Braun, described it as “the new slide rule.”
The line got a laugh, but he was serious. Like slide rules in the 1970s when scientific calculators came along, the venerable database tool from Microsoft is not keeping up with a business where the data sets have gotten too large for it to handle and are likely to reside on the cloud.
At the time of that 2020 speech, other programs offered heavy data management abilities as well as better collaboration tools. It came at a time when engineers in college were feeling the need to upgrade their programming and data analysis skills to compete in a job market where operators were paying close attention to digital kills.
Now, there’s another generation of AI programs built around using spoken languages, which can respond to requests, including writing code, which again raises questions about what engineers need to know about digital.
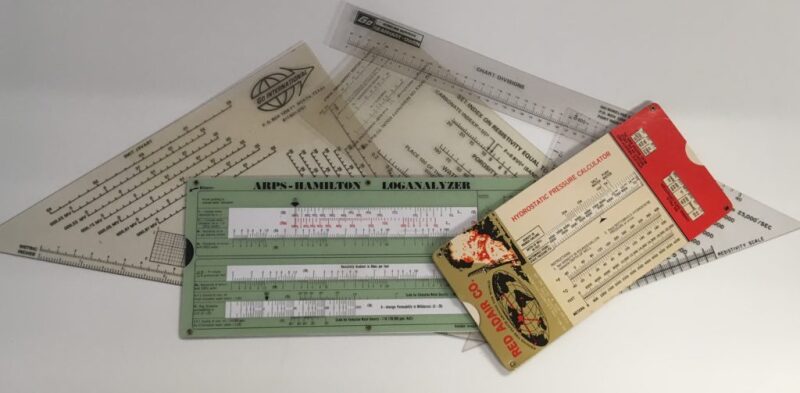