Abstract
This paper reviews the properties of iron compounds (such as iron oxides, iron hydroxides, and iron sulfides) and their impact in shale produced water treatment with an emphasis on the colloidal form of these compounds (small particle size, high surface charge). A wide range of problems is associated with these compounds in produced water including emulsion stabilization, oil-coated solids, pad formation in separators, pipeline solids, and plugging of water disposal formations. In conventional oil and gas production, the role that iron plays and the mitigation strategies for these problems are reasonably well known.
In the burgeoning shale industry, the situation is quite different. Not only are iron concentrations significantly higher than in conventional produced water, but the colloidal properties of iron compounds are only recognized by a handful of specialists. In addition, other colloidal particles such as clays and silts are also present at high concentrations in the produced water. Produced water treatment to remove solids in Permian shale produced water is rather hit or miss.
We were brought to this realization a couple years ago when testing formation plugging in Permian disposal wells. This was our first foray into produced water characteristics in the Permian. We measured produced water quality for about a dozen fields that had experienced declining injectivity. In nine of these fields the produced water contained high concentrations of small particles, tough biofilm in separators, and low-permeability filter cake formation according to the Barkman-Davidson test. It took almost a year to verify the iron-related mechanisms because data and knowledge of produced water characteristics in the Permian are scarce. This paper attempts to rectify the situation by pulling together knowledge of colloidal iron in produced water. Ultimately it is hoped that this work will help in the development of new cost-effective treatment strategies for produced water reuse and/or injection for disposal.
This paper is presented in two parts.
Part A (current paper) covers
- introduction and general background
- background chemistry of iron and iron oxides in produced water
- origin of iron in shale produced water
- measurement of iron in produced water
- field observations of iron in shale produced water
- facilities problems caused by iron,
- injectivity problems caused by iron
- mitigation of colloidal iron-related problems
Part B includes a repeat of the abstract and includes a Conclusions section for the entire paper.
Introduction and General Background
Field and laboratory studies of produced water from shale formations have established the presence of small particles (<< 30 micron). This was not unexpected. Most shale produced water from the Permian and other shale fields contains relatively high concentrations of fine grain suspended solids (roughly 50 to 2,000 mg/L). Hydraulic fracturing and other mechanisms (e.g., pipeline corrosion, crushing of proppant sand, oxidation, and precipitation) generate these small particles. The surprising features of shale produced water include the high concentration of iron compounds such as iron oxides, iron oxyhydroxides, and iron sulfide, and the degree to which these compounds cause produced water treatment problems.
Problems in treating produced water containing iron compounds are not new. In conventional offshore facilities, oil-wet iron sulfide particles can cause rose buds (a form of surface sheening) when treated produced water is discharged overboard from an offshore platform. Particles of iron sulfides and iron oxides can form from corrosion processes such as oxygen intrusion and from bacterial activity (MIC—microbially induced corrosion). These particles can form in pipelines, flowlines, and process equipment involved in handling produced water as well as seawater for waterflood (Clifford et al. 1991). Formation damage and injectivity decline have been experienced in both produced water reinjection and seawater injection for waterflood. Suspended particles from pipeline corrosion have been documented for various platforms in the North Sea. Similar problems have been extensively addressed in the Qurayyah seawater project in Saudi Arabia, which is the world’s largest seawater waterflood. In several North Slope facilities, iron sulfide, together with asphaltic crude oil and film-forming amine corrosion inhibitors, form a sludge that caused horrendous facilities and injectivities problems. The pasty sludge material was given the descriptive moniker schmoo. Iron compounds cause problems in ion exchange used for desalination in heavy-oil extraction. However, in all these applications, the concentration of suspended iron is much lower (roughly 2 to 10 mg/L) than encountered in shale produced water (roughly 20 to 200 mg/L—see below regarding accurate measurement).
In many shale producing fields, the only treatment that is applied to the produced water is coarse filtration prior to disposal in a saltwater disposal (SWD) well. Water injection in most cases is above the reservoir fracture pressure. In some cases, additional water treatment is applied to improve injectivity. This is typically a chemical treatment involving antiscalant and biocide.
In 2017, Nichols et al. (2017) published a technical and economic survey of treatment technologies for shale produced water. Their objective was to achieve a clean brine which involves removal of suspended contaminants without necessarily reducing the hardness or salinity. They determined that clarification is the most robust technology in terms of effectiveness and economics for produced water reuse. Their findings and approach to water treatment are entirely consistent with the mechanisms discussed here.
Between 2015 and 2018, Sharma and coworkers (Walsh and Sharma 2018; Sharma and Bjornen 2018; Sharma et al. 2015) carried out field studies of various technologies including a full-scale field test based on clarification and flotation. As part of that work, Walsh and Sharma (2018) investigated shale produced water properties in some detail. The objective was to develop a mechanistic understanding of why clarification is effective in treating shale produced water to a clean brine specification (turbidity < 10 NTU). Based on field and laboratory measurements, they found a relatively high concentration of colloidal particles. In agreement with the findings of Nichols et al., the ConocoPhillips field tests confirmed that clarifier-type treatment followed by dissolved air flotation (DAF) and filtration is a viable treatment strategy to generate a clean brine. Further confirmation of this strategy is given by the observation that equipment vendors find generally good success with clarifier/DAF technology in the Permian over other technologies.
Beyond these studies, not much has been published to link water characteristics to water treatment strategies. While these studies are consistent with one another, and they explain the mechanisms of treatment, there are still some unanswered questions:
- Are high concentrations of colloidal iron expected in shale produced water in general?
- Are size exclusion rules valid for shale produced water for disposal? If size exclusion rules are not valid, then how should disposal wells and their water treatment systems be designed?
- Are there opportunities for more sophisticated treatment technologies on the basis of fundamental colloid chemistry mechanisms?
Much of the initial motivation for asking these questions comes from a comparison of the performance of SWD wells in shale fields vs. waterflood injection wells in conventional offshore fields. As discussed by Bansal and Caudle (1992), in a cluster of waterflood injection wells, where treated seawater was injected, the injection wells achieved 8 to 10 years injection-well half-life, without remediation or acid treatment. In the Permian Basin some disposal wells are remediated three or four times per year. Obviously, there is a cost/benefit tradeoff that drives water treatment standards to a much higher level in the offshore case. On the other hand, size exclusion rules would indicate that significant plugging of SWD wells should not occur due to small particle size of the colloidal iron.
The main objective of this paper is to review the field data and laboratory literature to extract information to explain why colloidal iron causes plugging, impairment, and formation damage from injection of water with high concentrations of colloidal iron in shale operations.
Background Chemistry of Iron and Iron Oxides in Produced Water
Iron, together with sulfur and oxygen, can form many different compounds. These will be discussed briefly. Amongst the oxidized species of iron, there are two major groups: the iron oxides and the iron oxyhydroxides (Weatherill 2017: Hall and Dill 1988). Oxygen has an enormous impact on the physical and chemical state of iron in produced water.
In a typical shale development, the produced water is exposed to oxygen by two mechanisms. Hydraulic fracturing fluid almost always contains oxygen. Hydraulic fractures extend deep into the formation where the oxygen mixes with the produced water. The second mechanism of oxygen exposure occurs when produced water is processed in the surface facility. Typically, air blanketing is used instead of gas blanketing. These mechanisms are further elaborated below.
Iron oxides in produced water are essentially the same as rust compounds such as hematite (a-Fe2O3 ferric Fe(II)) and magnetite (Fe3O4, mixed Fe(II) and Fe(III). These compounds are found as suspended solids and are relatively unreactive in produced water.
The iron oxyhydroxides occur in a wide range of structures, morphologies, forms, degree of crystallinity, degree of oxidation, and degree of hydroxylation. Specific compounds include:
- goethite a-FeO(OH)
- akageneite b-FeO(OH)
- lepidocrocite g-FeO(OH)
- ferric oxyhydroxide FeO(OH)•H2O
- ferrihydrite chemical formula is indeterminate
These compounds are all hydroxylated to one degree or another. They span a range of iron/ oxygen/ hydroxide interaction from loosely bound dissolved species to covalently bound precipitated mineral particles.
The iron oxyhydroxides have properties of typical colloidal particles. They have positively charged surfaces as measured by the pH at which zero surface charge occurs (PZC), which is in the range of 7 to 9. They precipitate as small particles (< 10 microns) which gives them a high surface area to volume ratio. This, and the high surface charge density, causes these species to bind to negatively charged surfaces such as sandstone. These iron oxyhydroxides are less dense than the iron oxides. Together, they tend to form the light, fluffy orange flocs that are seen throughout shale produced water facilities. These flocs tend to float due in part to their low density and the presence of trapped gas bubbles within the floc.
Origin of Iron in Shale Produced Water
Shale produced water has been observed to have total iron concentrations in the range of 20 to a 200 mg/L. As discussed below, iron in the produced water appears to be inherent due to the geologic formation of shale and mudstone basins. This is unique compared to conventional produced water where the iron comes from corrosion mostly and the concentration could be in the range of about 2 to 5 mg/L.
There is considerable evidence that most of the iron in shale produced water comes from the formation water itself and has origins in geologic processes. The initial process of a shale or mudstone deposit involves one or more geologic processes that creates a quiescent sedimentary basin. Over long periods of time, nearby rock structures erode and are washed into the basin as sediment. Depending on the surrounding terrain the sediment will contain varying quantities of quartz, carbonate, feldspar, clay, and organic plant matter. Shale and mudstone basins are unique in their high content of very-fine particles which settle out and are captured in the basin due to the presence of large stagnant zones. A compact, fine-grained, low-permeability organic-rich sediment (kerogen) is formed. Compaction and burial of the sediment occurs. Over geologic time a diagenetic process transforms the organic matter into low-molecular-weight-, low-viscosity oil constituents.
Measurement of Iron in Produced Water
One of the important issues surrounding iron is accurate measurement (Walsh 2019, Chapter 7). When a produced water sample is taken, volatile gasses such as CO2, H2S, and BTEX [benzene, toluene, ethylbenzene, and xylene] flash off. When CO2 and H2S flash off, the pH of the water increases. Iron compounds generally become less soluble when the pH increases. In samples that contain appreciable dissolved iron and sulfide anion, the sample will turn black after a minute or two due to the formation of iron sulfide. Also, unless special sampling methods are employed, air, or more importantly oxygen, will enter the sample. When this happens, iron hydroxides and oxides will form. In some cases, the sample turns orange or green depending on the pH and on the concentration of iron and oxygen. The sample will also cool to ambient temperature. This too will decrease the solubility of most iron compounds, with iron carbonate as an exception. Iron carbonate solubility increases as the temperature goes down.
In a 2019 paper, Flynn et al. make the point that there are relatively few studies of shale produced water that focus on the composition and concentration of suspended material. Many water analysis procedures start with a filtration step. When an industrial water laboratory receives a water sample, the first step is usually to filter the sample through a 0.45 micron Millipore filter. The filtered residue may or may not be analyzed. Yet, from a produced water treatment standpoint the filtered residue is the most important part of the sample. It will contain precipitated iron as well as other solids.
In order to obtain an accurate measurement of total ion, it is advisable to take triplet samples (three samples taken at the same location at the same time). One sample is treated with nitric acid which dissolves all of the various iron species. Another sample is not treated with any additive. The third sample is treated with potassium hydroxide. All three samples are then filtered with a 0.45 Millipore filter. The filter residue is digested (acidized, stirred, allowed to settle). The composition of the solution and the digested solid residue is determined by a variety of methods including ICP-OAS. The total iron is the sum of the iron in solution and the iron digested from the solid filter residue. All three samples should give the same total iron concentration. If this is not the case, then the procedure should be refined until it does. Analyzing triplet samples provides an internal consistence check. It ensures that the sampling and analytical procedure being used is at least consistent.
In order to refine the analytical technique, it is helpful to make up several batches of “known” (spiked) solutions, then vary the pH, carry out the filtration and digestion, and make the measurement. Analytical technique can impact the measurement and must be refined until accurate measurements are made. This not only helps to pinpoint problems with the analytical procedure, but it also helps to quantify the accuracy and precision. Triplet sampling and analyzing spike samples usually provide accurate measurements with quantifiable precision.
Field Observations of Iron in Shale Produced Water
In this section, field measurements of iron and iron oxides in shale produced water are given. The focus is on total iron (dissolved and precipitated in various forms). Bosch and Perry (2013) presented data on the water chemistry of shale produced water. Samples were taken at the wellhead. In most cases the samples were produced water. In some cases, the samples were a mixture of flowback and produced water. Histograms were constructed which give the frequency of occurrence over a range of iron concentration values. The histograms appear to be log normal with a clearly defined average and median value. As shown in the histograms, a large number of samples were taken.
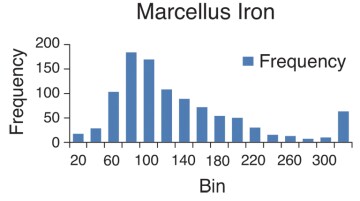
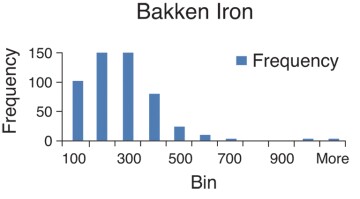
Table 1. Mean (Average) Values of Total Iron Concentration of Shale Produced Water
Shale | Total Iron (mg/L) Engle (2016) | Total Iron (mg/L) Bosch & Perry (2013) | Total Iron (mg/L) Taylor (1998) |
Wolfcamp (Permian) | 20–55 | 107 | |
Bone Springs (Permian) | 27 | ||
Eagle Ford | 69 | ||
Cline | 64–183 | ||
Bakken | 18–129 | 226 | |
Marcellus | 32–78 | 139 | 62 |
Antrim (Devonian) | 114 |
Particle size was measured in-situ at site using a particle sieve-type apparatus as well as an automated optical particle size analyzer. Ninety-five percent of the particle volume (or mass) was smaller than 10 microns. Fifty percent of the particle volume was smaller than 1.3 micron. This is very small compared to typical particle sizes found in treatment of conventional produced water (Walsh 2019). At least one-fifth to one-third of the particle mass was iron.
Vidic and coworkers (2005) measured the particle size distribution of hydraulic fracture flowback water and found iron-based colloidal particles with an average size of 0.2 micron. The measurements were part of an evaluation of membrane microfiltration technology. The particles caused rapid and severe membrane fouling and were found to be highly stable (nonsettling). The colloidal stability was attributed to a fine coating of organic material on the particle surface. Conventional coagulation and ballasted coagulation technology were proposed as alternatives to membrane microfiltration.
Lord and coworkers (Lebas et al. 2013; Ye et al. 2013) published a particle size distribution for produced water from a Permian shale. It appears that the water was sampled at the feed end of the gun barrel system since it contains a high concentration of larger particles that would likely settle out within the system. However, there is a significant quantity of small particles. Almost half of the particles are in the 1- to 10-micron range. In addition to the data presented here, some operators have confirmed, through personal communication (Gruber 2014), the presence of small iron and clay particles in shale produced water.
Conclusions
This review of field data and laboratory colloid chemistry data demonstrates and ties together several important concepts involving the role of iron in produced water management. The most important concept discussed is the role of iron in pore blocking and formation damage despite the fact that suspended iron particles are typically much smaller than the limits set by size exclusion rules. Freshly precipitated iron is typically composed of colloidal particles (small and surface charged) which can attach to pore walls and build up over time. The particles can stabilize emulsions and can be utilized by microbes to build hard encrustations where sessile colonies can thrive despite harsh and toxic environments outside of the sessile colony.
Major conclusions from this study of iron in shale produced water are summarized below.
- Iron is present in shale formations at high concentration and in various forms but predominantly as very small particles of iron sulfide and iron oxyhydroxides.
- According to size exclusion rules, small particles should pass through the injection well formation as “nonblocking” solids. However, colloidal iron does not do so. Instead, colloidal particles stick to the formation surface, and to each other, and build up to form an impenetrable filter cake.
- Removal or passivation of colloidal iron particles can be achieved by conventional water treatment technologies such as coagulation, clarification, flocculation, chelation—followed by dissolved gas flotation and filtration.
- However, for chelation and other chemical treatment technologies to be effective in treating the large volumes of water involved in shale development, the chemicals involved in these treatments must become available at prices that are much lower than currently employed.
- If possible, oxygen ingress in shale production and processing operations should be prevented to keep iron in the soluble state (Fe++). This can help reduce its impact on injectivity decline of the disposal wells.
FOR FURTHER READING
P.J. Clifford, D.W. Mellor, T.J. Jones, “Water Quality Requirements for Fractured Injection Wells,” SPE 21439, paper presented at the SPE Middle East Oil Show, Bahrain (1991). https://doi.org/10.2118/21439-MS
K. Nichols, J. Sawyer, J. Bruening, “Development of a Large-Scale Water Recycling Program for the Delaware Basin, New Mexico,” SPE 186086, paper presented at the SPE HSSE&SR Conference, New Orleans (2017). https://doi.org/10.2118/186086-MS
J.M. Walsh, R. Sharma, “Fit-for-Purpose Water Treatment in Permian Shale—A Comprehensive Overview, Laboratory and Field Evaluations,” SPE 191529, paper presented at the SPE Annual Technical Conference and Exhibition, Dallas (2018). https://doi.org/10.2118/191529-MS
R.R. Sharma, K. Bjornen, “Systematic Approach for Developing a “Fit-For-Purpose” Treatment for Produced Water Reuse in Hydraulic Fracturing,” URTeC 2902544, paper presented at the Unconventional Resources Technology Conference, Houston (2018). https://doi.org/10.15530/URTEC-2018-2902544
R. Sharma, K. McLin, K. Bjornen, A. Shields, Z. Hirani, S. Adham, “Fit-for-Purpose Treatment of Produced Water for Hydraulic Fracturing—A Permian Basin Experience,” IPTC 18340, paper presented at the International Petroleum Technology Conference, Doha (2015). https://doi.org/10.2523/IPTC-18340-MS
K.M. Bansal, D.D. Caudle, “A New Approach for Injection Water Quality,” SPE 24803, paper presented at the SPE Annual Technical Conference and Exhibition, Washington D.C. (1992). https://doi.org/10.2118/24803-MS
J.S. Weatherill, “Iron Oxyhydroxide Formation in the Enhanced Actinide Removal Plant,” Thesis submitted to the University of Manchester (2017). https://www.research.manchester.ac.uk/portal/files/67403695/FULL_TEXT.PDF
B.E. Hall, W.R. Dill, “Iron Control Additives for Limestone and Sandstone Acidizing of Sweet And Sour Wells,” SPE 17157, paper presented at the SPE Formation Damage Control Symposium, Bakersfield (1988). https://doi.org/10.2118/17157-MS
J.M. Walsh, Produced Water, Vol. 1: Fundamentals, IngramSpark pub. (2019).
S.L. Flynn, K. von Gunten, T. Warchola, K. Snihur, T.Z. Forbes, G.G. Goss, M.K. Gingras, K.O. Konhauser, D.S. Alessi, “Characterization and Implications of Solids Associated With Hydraulic Fracturing Flowback ad Produced Water From the Duvernay Formation, Alberta, Canada,” Environmental Science: Processes & Impacts, Vol. 21, p. 242–255 (2019). https://doi.org/10.1039/C8EM00404H
R. Bosch, R. Perry, “Variations in Water Chemistry in High-Volume Fracturing Operations,” PowerPoint presentation to the SPE Global Integrated Workshop Series, Fort Worth (2013).
M.A. Engle, F.R. Reyes, M.S. Varonka, W.H. Orem, L. Ma, A.J. Ianno, T.M. Schell, P. Xu, K.C. Carroll, “Geochemistry of Formation Waters From the Wolfcamp and “Cline” Shales: Insights Into Brine Origin, Reservoir Connectivity, and Fluid Flow in the Permian Basin, USA,” Chemical Geology, Vol. 425, p. 76 (2016). https://doi.org/10.1016/j.chemgeo.2016.01.025
K.C. Taylor, H.A. Nasr-El-Din, M.J. Al-Alawi, “A Systematic Study of Iron Control Chemicals Used During Well Stimulation,” SPE 39419, paper presented at the SPE International Symposium on Formation Damage Control, Lafayette (1998). https://doi.org/10.2118/39419-MS
R.D. Vidic, “Final Technical Report: Sustainable Management of Flowback Water During Hydraulic Fracturing of Marcellus Shale for Natural Gas Production,” US Department of Energy project no.: DE-FE0000975, April 2005. https://www.netl.doe.gov/sites/default/files/2018-02/fe0000975-final-report.pdf
R. LeBas, P. Lord, D. Luna, T. Shahan, “Development and Use of High-TDS Recycled Produced Water for Cross-Linked-Gel-Based Hydraulic Fracturing,” SPE 163824, paper presented at the SPE Hydraulic Fracturing Technology Conference, The Woodlands, Texas (2013). https://doi.org/10.2118/163824-MS
X. Ye, N. Tonmukayakul, P. Lord, R. LeBas, “Effects of Total Suspended Solids on Permeability of Proppant Pack,” SPE 165085, paper presented at the SPE European Formation Damage Conference and Exhibition (2013). https://doi.org/10.2118/165085-MS
E. Gruber, “Recycling Produced and Flowback Wastewater for Fracking,” published by Ecologix Environmental Systems LLC (2014). https://www.ecologixsystems.com/wp-content/uploads/2018/12/recycing-flowback-and-produced-water.pdf
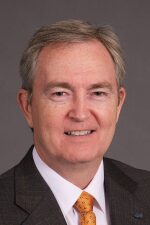
John Walsh, PhD, SPE, has worked as a water specialist for the upstream oil and gas industry for more than 30 years. He has recently published a book, Produced Water. He is currently a principal technologist for Worley, Advisian. Prior, he was the director of R&D for CETCO Energy Services. In 2010, he retired from Royal Dutch Shell where he worked for 21 years. He was the global upstream water subject matter expert. Until recently, he was the president of the Produced Water Society. He served on the SPE Board of Directors and is a designated instructor for SPE courses. He holds a PhD in chemical engineering from the Johns Hopkins University. He can be reached at jmwalsh924@gmail.com.
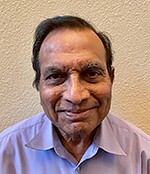
Kris M. Bansal, PhD, SPE, has expertise in developing optimum engineering solutions requiring system integration and interface with multiple disciplines from reservoir to the topsides in upstream oil and gas operations. He recently retired as an Engineering Fellow from ConocoPhillips after 30 years of service, where he was a global subject matter expert in upstream water management. He taught waterflood school and presented problem-solving seminars for technology transfer to operations and engineering. Before joining ConocoPhillips, Bansal spent 6 years at Saudi Aramco in operations engineering, 3 years in activated-carbon research at Calgon, and 8 years in academic research. He has taught SPE courses on water management in shale operations. He holds an MS and PhD in physical chemistry and an MS in chemical engineering. He can be reached at Krismbansal@yahoo.com.