This paper is Part B of a two-part series. Part A includes an introduction, background chemistry of iron and iron oxides in produced water, the origins of iron in shale produced water, measurement of iron in produced water, and field observations of iron in shale produced water.
Part B covers facilities problems caused by iron, injectivity problems caused by iron, and the mitigation of colloidal iron-related problems. Part A’s abstract is included, and the Conclusions section of Part B addresses both papers.
Abstract
This paper reviews the properties of iron compounds (such as iron oxides, iron hydroxides, and iron sulfides) and their impact in shale produced water treatment with an emphasis on the colloidal form of these compounds (small particle size, high surface charge). A wide range of problems is associated with these compounds in produced water including emulsion stabilization, oil-coated solids, pad formation in separators, pipeline solids, and plugging of water disposal formations. In conventional oil and gas production, the role that iron plays and the mitigation strategies for these problems are reasonably well known.
In the burgeoning shale industry, the situation is quite different. Not only are iron concentrations significantly higher than in conventional produced water, but the colloidal properties of iron compounds are only recognized by a handful of specialists. In addition, other colloidal particles such as clays and silts are also present at high concentrations in the produced water. Produced water treatment to remove solids in Permian shale produced water is rather hit or miss.
We were brought to this realization a couple years ago when testing formation plugging in Permian disposal wells. This was our first foray into produced water characteristics in the Permian. We measured produced water quality for about a dozen fields that had experienced declining injectivity. In nine of these fields the produced water contained high concentrations of small particles, tough biofilm in separators, and low-permeability filter cake formation according to the Barkman-Davidson test. It took almost a year to verify the iron-related mechanisms because data and knowledge of produced water characteristics in the Permian are scarce. This paper attempts to rectify the situation by pulling together knowledge of colloidal iron in produced water. Ultimately it is hoped that this work will help in the development of new cost-effective treatment strategies for produced water reuse and/or injection for disposal.
Facilities Problems Caused by Iron
In general, one of the most effective ways to eliminate problems related to suspended iron particles is to eliminate air intrusion in the facilities. By eliminating oxygen, the dissolved iron will remain dissolved in the produced water and will not cause plugging and other problems. This strategy is used extensively in conventional hydrocarbon facilities.
For example, the Chevron Kern River Facility in Bakersfield, California, experienced corrosion problems and difficulty meeting oil and water targets for once-through steam generator boilers in heavy-oil extraction. A 2-year project was implemented to upgrade the facilities to eliminate air intrusion at flanges, pumps, and gas blanketing systems and to replace air blanketing systems with gas blanketing. By eliminating air intrusion, corrosion rates went down from an average of several mils per year to less than one. This reduced the source of iron in the facilities, and it reduced the formation of iron-stabilized heavy-oil components, including oily solids. The removal of oil from the produced water improved.
Several examples are available from Shell facilities in the Gulf of Mexico where multistage horizontal flotation, using unpressurized Wemco units, are used. These flotation units have rubber gaskets that occasionally need to be replaced to provide a good seal against air intrusion. When the Wemco units are refurbished and new gaskets are installed, air intrusion and, hence, iron precipitation, is reduced, and the incidence of sheens and blooms is reduced.
It is not generally practical to eliminate oxygen from the water used for hydraulic fracturing of Permian shale. The water volumes are too large. The deoxygenated water would need to be stored in an oxygen-free environment. Thus, the hydraulic fracturing fluid contains oxygen and the initial flowback will contain oxidized iron. In addition, in most shale facilities, there is no attempt to eliminate oxygen in the oil/produced water separation facility. Air blanketing, instead of gas blanketing, of gun barrels and storage tanks is the general rule.
When dissolved iron initially oxidizes, it forms a floc of iron oxyhydroxides. In addition to the iron floc, various gel-like, emulsified, and crosslinked compounds can form as a result of iron/EPS (extracellular polymeric substances) interaction. Bacterial EPS is part of the sessile biological habitat that grows in hydrocarbon processing facilities. Iron/EPS complexes can cause problems in the oil/water separation facility when they accumulate as a pad or mat at the oil water interface of the gun barrel separator or storage tanks. In conventional facilities, the installation of an “interface bleed” provides an effective tool for the operators to drain the interface periodically to eliminate the pad (Walsh 2019). When this is not done, the pad tends to “set up” (harden). This occurs as the iron becomes more oxidized and shifts from a soft, fluffy, floc-like or gel-like material to a highly EPS crosslinked, harder, and tougher material.
Injectivity Problems Caused by Iron
Iron compounds play a role in injectivity and formation damage problems in both disposal-well and in reuse applications. One of the important findings is that size exclusion rules used to predict pore throat blockage are not accurate predictors for colloidal iron particles in shale operations. According to accepted size exclusion rules, small particles should be “nonbridging.” In other words, particles that are small compared to the pore throat diameter of the formation should not be able to form a bridge across the pore throat. Yet, operational experience indicates that they do. Thus, colloidal particles do not obey the size exclusion rules.
An understanding of the situation is facilitated by looking at the origin of the size exclusion rules. In 1989, Pautz and Crocker carried out sandpack studies where the sand grain size and contaminant particle diameter were systematically varied. As a result of varying these two variables, pore diameter and permeability were indirectly varied as well. In Fig. 1, the pore diameter is plotted vs. the formation permeability.
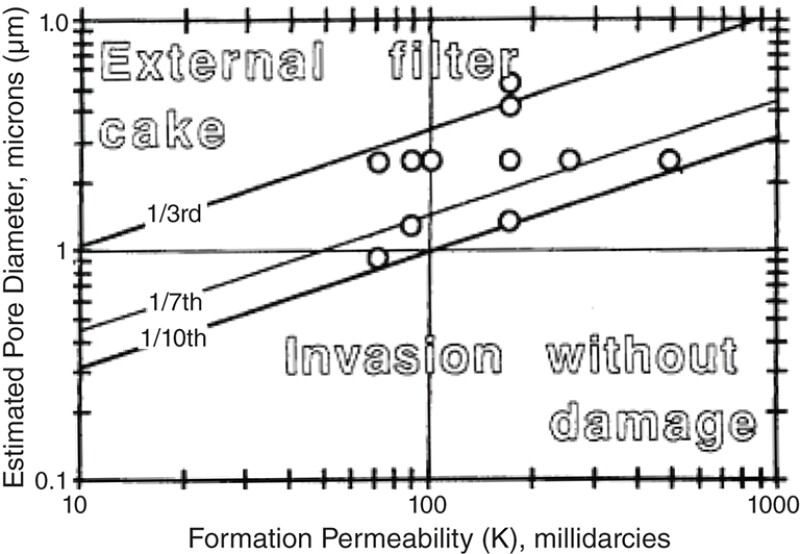
From about 1994 through 2000, Bennion et al. (1998, 2000, 1994) defined injection well impairment mechanisms and provided guidelines to prevent impairment and strategies for mitigating impairment when it nevertheless occurs. However, in providing such a comprehensive set of guidelines, one of the important details has been overlooked.
In Fig. 2, Bennion et al. (1998, 2000, 1994) claim that small particles (so-called “nonbridging solids”) do not cause plugging. Size exclusion is the only mechanism considered. This view ignores a large body of work which shows that colloidal size particles, smaller than 1/10th pore throat diameter can cause plugging due to the surface charge, solution chemistry, Brownian motion, and van der Waals forces involved with colloidal particles. Further, the impact of oil wetting of the particles and their transport though the porous media were not accounted for either. Both these factors must be considered for produced water transport through porous media in shale operations. In view of these considerations, size exclusion rules may not be applicable to predict injectivity decline of the saltwater disposal (SWD) wells where colloidal particles are present. The problem is that the Bennion view, which is 20 to 25 years old, is still applied in design work and referenced in the oil and gas literature.
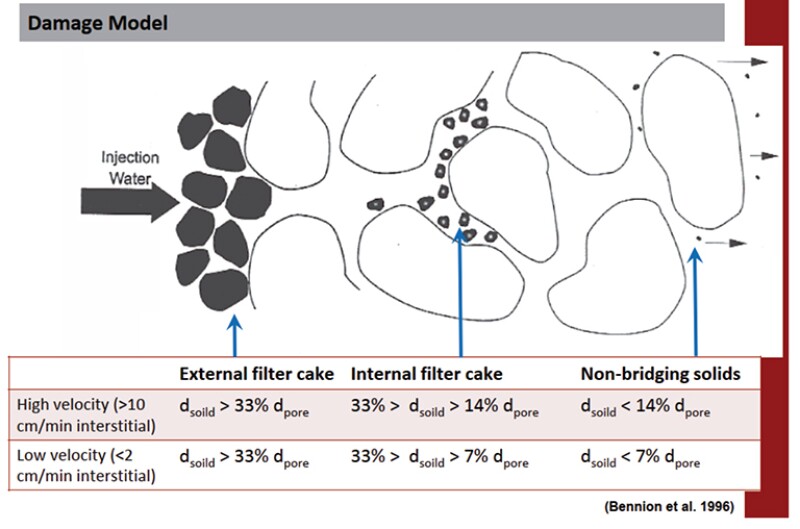
A simplified view of colloidal iron particles would be to say that they can be “sticky.” They stick to formation rock and they stick to each other. In an injection scheme, colloidal iron particles can build up over time and plug pores in the formation rock even though they would be considered to be nonbridging solids according to the size exclusion rules. Iron oxyhydroxides, iron sulfide, and clay particles are common examples of colloidal materials in produced water. Their impact on injection well impairment must be determined at an early stage of field development to avoid costly and frequent stimulation and remediation operations.
When iron initially oxidizes, it forms a floc of iron oxyhydroxides. These flocs tend to be orange in color, and they tend to trap gas bubbles which causes them to float on the water. They are ubiquitous in the Permian. The floc material cannot be removed by filtration since the filter will plug rapidly. Dissolved gas flotation has been found to work reasonably well. If this floc material is allowed to flow into the injection well, it will cause impairment eventually even though the particles are small. As discussed below, this is a consequence of the colloidal properties of the floc. When impairment occurs, the producer will order an acid job. There is a wide range of operating experience for the SWD wells in the Permian Basin. Some wells do not require frequent remediation to maintain injectivity. Other wells require an acid job every month or two. Note that in most of the water disposal operations, injection is at or above the reservoir fracture pressure.
A typical acid job (well remediation) takes only a few hours and is relatively inexpensive. However, it should be emphasized that the true cost of a remediation job must include costs associated with management of produced water during the time the well is shut in for treatment
Similar effects have been observed in waterflood operations. Potter and Dibble (1985) published a study on the impact of colloidal iron particles on waterflood injectivity. Pore throat plugging due to small iron particles followed the expected plugging behavior of colloidal particles rather than neutral particles that behave according to size exclusion.
From 1985 through 2000, Sharma and coworkers (Pang and Sharma 1995, 1997; Sharma et al. 1997, 2000; Iwasaki 1937; van Oort 1993; Sharma et al. 1985; Sharma Yortsos 1987) presented a mathematical model for injectivity that explicitly takes into account colloidal particle behavior. The model was developed to explain injectivity problems in a waterflood (Sharma et al. 1997). The model could explain field observations where the contaminant particles in the injected water behaved as colloidal particles (surface-charged and very fine 2 to 3 microns or less). The facility had been designed, prior to Sharma’s work, on the basis of size exclusion. Significant economic loss occurred.
Laboratory experiments helped establish the impairment mechanisms involved. Kuhnen et al. (2000) published a study on the transport and deposition of iron oxide particles in a column sandpack. The sand grains were more than 2,400 times larger than the contaminant particles. In such a system., size exclusion would have predicted essentially zero retention of iron oxide particles and zero plugging of the sandpack.
Instead, as shown in Fig. 3, strong colloidal forces caused rapid plugging, depending on the colloidal nature of the injected water. This is seen, for example, by the behavior of the open triangles. The horizontal nature of the open triangles indicates that nearly complete retention of the particles occurred. This would eventually lead to formation damage.
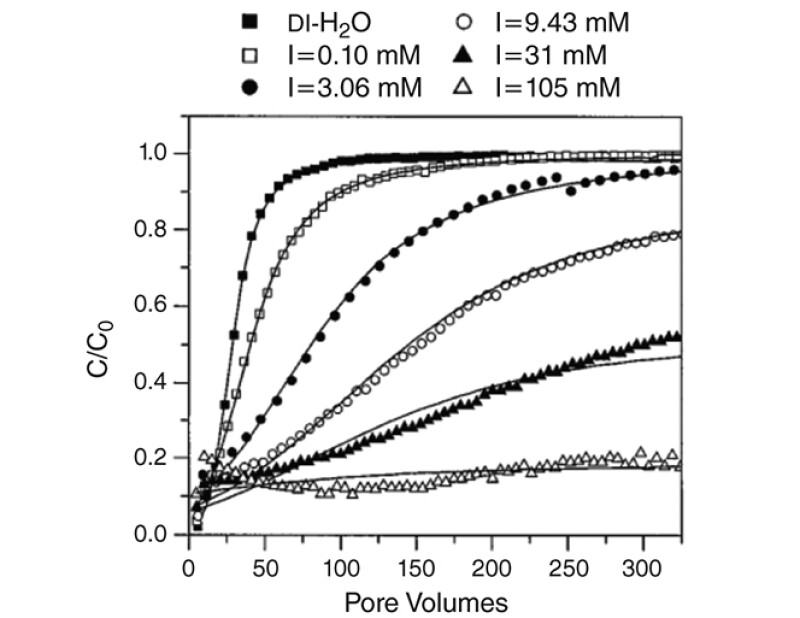
There are various established methods that can be used to determine if colloidal particles are present. First, the particle size distribution can be measured. Techniques include optical microscopy and benchtop measurements such as using a Coulter counter. In-line devices can also be used and are supplied by Canty, Jorin, Advanced Sensors, etc. Once the size has been established, filtration using Millipore filter can be measured to determine the permeability of the filter cake. Barkman and Davidson provide a standard test method that can be easily run in the field. Filter cakes formed from colloidal particles are typically very tight and nonporous. Mobile coreflood and sandpack test units are available. When these tests are run, various levels of water treatment can be evaluated to determine the required minimal water treatment quality specification. There is an abundance of information readily available once the possibility of impairment by small particles is recognized.
One takeaway message is that size exclusion rules work well for noncolloidal particles, but when the particles are small, with a high surface area to volume ratio, with significant surface charge, then plugging can readily occur. As discussed, this situation can cause problems in both water disposal and in waterflood. The latter case has potential to damage a hydrocarbon-bearing formation, which can be a very expensive problem. Most iron compounds form colloidal-size precipitates. These include the iron hydroxides and iron sulfide. These compounds together with clay have been found in relatively high concentrations in shale produced water which has potential for damage to the disposal well.
Oily Solids
To this point in the discussion, the focus has been on water containing suspended solids that are water-wet without the presence of oil on the particle surface. A seawater flood containing suspended clay, silt, and iron particles are examples. Also, corrosion products such as iron hydroxides and iron sulfide are examples. In the case of produced water reinjection, agglomeration of particles held together with sticky patches of oil can occur. Shale formations tend to produce light oil rather than oils containing asphaltene and resins which tend to be sticky. Nevertheless, agglomerates can occur even in shale production and can cause severe damage to the formation. Accurately predicting when this will occur is difficult. In such cases, coreflood experiments and pilot studies are usually required prior to finalizing the design. Once production commences, chemical treatment (wetting agents, asphaltene inhibitors) may be required which can be expensive.
Reuse and Recycle for Hydraulic Fracturing
One of the quality specifications of hydraulic fracturing makeup water is the removal of total iron. When hydraulic fracturing is carried out using slickwater, removal of iron is required to prevent degradation of the polymer. Sharma and Bjornen (2018) discuss different methods for removing iron in the flowback and produced water. One effective process is to precipitate and remove the iron using an oxidizer such as hydrogen peroxide, ozone, or hypochlorous acid. A clarifier/flotation unit can then be used to remove the iron floc.
Prevention and Mitigation Measures
Some mitigation methods have already been discussed. Some operators have problems with the oil/water interface. As mentioned above, first and foremost is the need to practice rigorous microbiological control strategies to reduce the production of EPS and reduce corrosion. Operators will inject some mineral acid such as HCl to the top of the gun barrel separator. The acid dissolves some of the iron, helps to break up the pad. Also, raising the interface and pushing the pad out of the top of the gun barrel and “rolling” the contents are all means of dealing with the problem. Draining the interface using an interface bleed works well. Frequent removal of this material greatly facilitates the performance of the oil/water separation train. The application of aromatic solvents, mutual solvents, and chelating agents also works well but can be somewhat expensive. Solugen Inc. has developed chelating agents based on natural products with reduced cost.
Sophisticated chemical approaches for eliminating iron problems are available. In an early study, Crowe (1985) showed that citric acid, EDTA (ethylenediaminetetraacetic acid) and NTA (nitrilotriacetic acid) can hold up to 3,000 mg/L of Fe+3 in spent acid at high temperature. Chelated iron behaves like dissolved iron and will not block pore spaces. While chelating chemicals are very effective in gathering up and binding to iron, they are expensive and mostly suited to the high-iron environment of well acidizing.
It is difficult to estimate the number of wells/facilities that are contaminated with EPS/iron matrix with any accuracy. Service companies report that the EPS/iron material forms an oil-in-water emulsion that does not clean up with mineral acid treatment. Combinations of organic solvents, surfactants, in stages with chlorine dioxide, hypochlorite, or other oxidative chemistries can be effective in removing this emulsion. Also, combinations of oxidative chemistries together with surfactants can be used. These treatments are more expensive than acid jobs. If multiple stages are required, they also require more shutdown time. Nevertheless, they are typically able to recover injectivity at reduced injection pressure and remain effective for up to 6 months or more.
Some selective learnings can be imported from other problematic production regions such as Western Canada. The primary plugging mechanisms identified are mostly colloidal iron and colloidal paraffin wax. Slickwater fracking programs, using recycled production brine, often contain a certain amount of corrosion-based iron. The handling and pumping of proppant from tanks and through piping during the fracking process will inadvertently pick up a large amount of iron caused by abrasion. Since some brines are acidic, typically having a pH of 5.5 to 6.8, a lot of this corrosion-based iron will return to surface on frack flowback. Oil-wet iron solids, along with silicates and salt, cause grey, waxy emulsions which form pads and cause a host of phase separation problems. In the presence of oxygen, compounds such as iron oxyhydroxides, iron oxides, and iron sulfides (in sour systems) will precipitate and begin to drop out of solution (or become tied up with organic scale such as maltene resins and/or paraffin wax) which can form surface sludges. A combination of colloidal iron and wax, in an electrokinetically stabilized suspension, can be carried in brine (often passing through micron-sized bag filters) into the injection pipeline system. With subsequent cooling and pressure changes, this colloidal suspension will begin to aggregate, forming larger precipitates which can plate out in the pipeline and/or form downhole skin damage in disposal wells. VerdeChem Technologies has developed several customized antifoulant chemistries to effectively treat and mitigate the damaging effects of these colloidal suspensions (see product descriptions and case histories at www.verdechem.com). The continuous injection of SCi7775 (antifoulant chemistry) and CD100i or CD235i (paraffin wax solvent/dispersants) has cost effectively mitigated the often-expensive operating costs associated with frequent filter changes, plant upset/shutdowns, and associate trucking costs.
Conclusions
This review of field data and laboratory colloid chemistry data demonstrates and ties together several important concepts involving the role of colloidal iron in produced water management particularly in shale fields where iron content is usually high. The shale field data are reasonably current. The lab data that defines the behavior of colloidal iron are decades old. Thus, one of the hoped-for outcomes of this article is to tie together these parallel ideas.
The most important concept discussed is the role of iron in pore blocking and formation damage even though suspended iron particles are typically much smaller than the limits set by size exclusion rules. Freshly precipitated iron is typically composed of colloidal particles (small and surface charged) which can attach to pore walls and build up over time.
Major conclusions from this study of iron in shale produced water are summarized below.
- Iron is present in shale formations at high concentration and in various forms.
- Iron is present in the produced water in various forms at high concentration.
- Iron precipitates to form very small particles (colloidal particles).
- According to size exclusion rules, small particles should pass through the injection well formation as “nonblocking” solids. However, colloidal iron does not do so. Instead, colloidal particles stick to the formation surface, and to each other, and build up to form an impenetrable filtercake. They contribute to disposal well plugging.
- In hydraulic fracturing operations using slickwater, removal of total iron is required to prevent degradation of the polymer.
- Removal or passivation of colloidal iron particles can be achieved by conventional water treatment technologies such as coagulation, flocculation, chelation followed by dissolved gas flotation and filtration.
- However, for chelation and other treatment technologies to be effective in treating the large volumes of water involved in shale development, the chemicals involved in these treatments must become available at prices that are much lower than currently employed.
- Coarse filtration, along with chemical treatment in some cases, are the primary technologies used in treatment of shale produced water for disposal. These technologies are known to be not very effective (in view of complex shale water chemistry) in reducing injection well remediation frequency. Extensive developmental work is necessary to evaluate various treatment technologies for application.
- If possible, oxygen ingress in shale production and processing operations should be prevented to keep iron in the soluble state (Fe++). This can help reduce its impact on injectivity decline of the disposal wells.
For Further Reading
A Reassessment of the Role of Colloidal Iron in Produced Water from Shale Operations—A Review of Field Data and Literature (Part A), J.M. Walsh and K.M. Bansal, JPT, Oil and Gas Facilities.
J.M. Walsh, Produced Water, Vol 1: Fundamentals, IngramSpark pub. (2019).
J.F. Pautz, M.E. Crocker, “Relating Water Quality and Formation Permeability to Loss of Injectivity,” SPE 18888, paper presented at the SPE Production Operation Symposium, Oklahoma City (1989). https://doi.org/10.2118/18888-MS
D.B. Bennion, D.W. Bennion, F.B. Thomas, R.F. Bietz, “Injection Water Quality—A Key Factor to Successful Waterflooding,” J. Canadian Pet. Tech., PETSOC-98-06-06 (1998). https://doi.org/10.2118/98-06-06
D.B. Bennion, F.B. Thomas, D. Imer, T. Ma, “Water Quality Considerations Resulting in the Impaired Injectivity of Water Injection and Disposal Wells,” PETSOC-2000-067, paper presented at the Canadian International Petroleum Conference, Calgary (2000). https://doi.org/10.2118/2000-067
J.M. Potter, W.E. Dibble, “Chemical Aspects of Iron Colloid Plugging in Quartz Sands and Implications for Formation Damage,” SPE 11801, J Pet Technol, v.37, 1682–1688 (1985). https://doi.org/10.2118/11801-PA
J.H. Barkman, D.H. Davidson, “Measuring Water Quality and Predicting Well Impairment,” SPE 3543, J Pet Technol v. 24, p. 865–873 (1972). https://doi.org/10.2118/3543-PA
S. Pang, M.M. Sharma, “A Model for Predicting Injectivity Decline in Water-Injection Wells,” SPE 28489, peer review paper published in SPE Formation Evaluation, p. 194 (1997). https://doi.org/10.2118/28489-PA
M.M. Sharma, S. Pang, K.E. Wennberg, L. Morgenthaler, “Injectivity Decline in Water Injection Wells: An Offshore Gulf of Mexico Case Study,” SPE 38180, paper presented at the SPE European Formation Damage Conference, The Hague (1997). https://doi.org/10.2118/38180-MS
T. Iwasaki, “Some Notes on Sand Filtration,” J. Am. Water Works, v. 29, p. 1591 (1937). https://awwa.onlinelibrary.wiley.com/loi/15518833/year/1937
E. van Oort, J.F.G. van Velzen, K. Leerlooijer, “Impairment by Suspended Solids Invasion: Testing and Prediction,” SPE Production & Facilities, p. 178–184 (1993). https://doi.org/10.2118/23822-PA
M.M. Sharma, Y.C. Yortsos, “Fines Migration in Porous Media,” AIChE J., v. 33, p. 1654 (1987). https://doi.org/10.1002/aic.690331009
F. Kuhnen, K. Barmettler, S. Bhattacharjee, M. Elimelech, R. Kretzschmar, “Transport of Iron Oxide Colloids in Packed Quartz Sand Media: Monolayer and Multilayer Deposition,” Jo. Coll. Int. Sci., v. 231, p. 32 (2000). https://www.journals.elsevier.com/journal-of-colloid-and-interface-science
S.A. Bradford, J. Simunek, M. Bettahar, M.Th. van Genuchten, S.R. Yates, “Modeling Colloidal Attachment, Straining, and Exclusion in Saturated Porous Media,” Environ. Sci. Technol. v. 37, p. 2242 (2003). https://doi.org/10.1021/es025899u
S.A. Bradford, M. Bettahar, “Concentration Dependent Transport of Colloids in Saturated Porous Media,” J. Contaminant Hydrology, v. 82, p. 99 (2006). https://doi.org/10.1016/j.jconhyd.2005.09.006
C.W. Crowe, “Evaluation of Agents for Preventing Precipitation of Ferric Hydroxide From Spent Treating Acid,” SPE 12497, J. Pet. Technol, p. 691 (1985). https://doi.org/10.2118/12497-PA
H. Kim, M. Lee, W. Chae, T.D. Ezeh, S.L. Walker, “Coupled Effect of Input Concentration and Solution Ionic Strength on Colloid Transport in Saturated Porous Media,” 2011 2nd International Conf. Env. Eng. Appl., IPCBEE, v. 17 (2011). http://www.ipcbee.com/vol17/37-L10034.pdf
J.H. Barkman, D.H. Davidson, “Measuring Water Quality and Predicting Well Impairment,” SPE 3543, J Pet Technol v. 24, p. 865–873 (1972). https://doi.org/10.2118/3543-PA
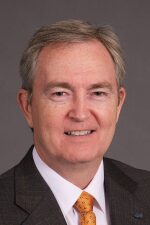
John Walsh, PhD, SPE, has worked as a water specialist for the upstream oil and gas industry for more than 30 years. He has recently published a book, Produced Water. He is currently a principal technologist for Worley, Advisian. Prior, he was the director of R&D for CETCO Energy Services. In 2010, he retired from Royal Dutch Shell where he worked for 21 years. He was the global upstream water subject matter expert. Until recently, he was the president of the Produced Water Society. He served on the SPE Board of Directors and is a designated instructor for SPE courses. He holds a PhD in chemical engineering from the Johns Hopkins University. He can be reached at jmwalsh924@gmail.com.
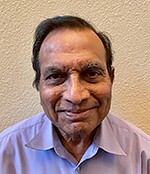
Kris M. Bansal, PhD, SPE, has expertise in developing optimum engineering solutions requiring system integration and interface with multiple disciplines from reservoir to the topsides in upstream oil and gas operations. He recently retired as an Engineering Fellow from ConocoPhillips after 30 years of service, where he was a global subject matter expert in upstream water management. He taught waterflood school and presented problem-solving seminars for technology transfer to operations and engineering. Before joining ConocoPhillips, Bansal spent 6 years at Saudi Aramco in operations engineering, 3 years in activated-carbon research at Calgon, and 8 years in academic research. He has taught SPE courses on water management in shale operations. He holds an MS and PhD in physical chemistry and an MS in chemical engineering. He can be reached at Krismbansal@yahoo.com.