As the energy industry strives to reuse produced water and disposal costs of produced water increase, it has elevated the need for more accurate measurement to save money.
Measurement of produced water in the US unconventional market is impacted by paraffin deposition on the meters causing inaccurate readings of the volume of produced water. The industry is starting to address this growing issue by applying new technology solutions that enable lasting accuracy in the place of routine maintenance that provides a temporary solution.
Most oil and gas producers face paraffin buildup on the inside surface of their electromagnetic flowmeters. These meters are typically located on the produced-water leg, downstream of production and test separators. Paraffin, a waxy substance present in crude oil production, drops out of solution as the fluid cools from the wellhead through the surface equipment.
How Paraffin Affects Metering
As the fluid is transported through the pipes, it cools down, causing the paraffin to solidify and deposit on the walls of pipes and flowmeters. Separators that are designed to remove most of the paraffin via heat are still susceptible to the accumulation of small amounts of paraffin that may coat the pipe and measurement devices.
Electromagnetic flowmeters are used to measure the volumetric flow rate of conductive fluids in pipelines, such as produced water. They operate by generating a magnetic field across the flow path and measure the voltage induced by the fluid as it flows through the magnetic field.
The voltage is proportional to the flow velocity and the magnetic field strength, which is used to calculate the volumetric flow rate of the fluid. Electromagnetic flowmeters contain a minimum of two electrodes, composed of ceramic or metallic materials depending upon the manufacturer. The electrodes read the induced voltage of the produced water flowing through the meter.
An insulating liner is placed inside the meter between the conductive fluid and the metal body. This isolates the fluid being measured from the meter body, preventing the fluid from creating an electrical short circuit.
Paraffin buildup affects the accuracy and reliability of electromagnetic flowmeters as it nucleates on the electrodes and the liner of the meter. Over time, the paraffin deposition will increase around the electrodes, essentially insulating the electrodes from the fluid. At this point the conductivity of the fluid is artificially reduced, and the flowmeter will under read.
If the paraffin coating on the electrodes becomes thick enough, a flowmeter will be completely insulated from the produced water, which the meter interprets as zero flow. As the paraffin coating on the liner increases, the cross‑sectional area of the meter is reduced, creating a higher fluid velocity which results in the meter overreading the flowrate (Q = Av where A is the cross-sectional area of flow and v is its average velocity).
Status Quo: Maintenance and Downtime
Oil and gas producers may be aware of paraffin buildup issues in their electromagnetic flowmeters, especially if they have experienced problems with inaccurate measurements or flowmeter failures in the past.
It is estimated that tens of thousands of the electromagnetic flowmeters in service today in the oil and gas unconventional US market are susceptible to paraffin deposition. Many operators have developed strategies to mitigate paraffin buildup issues in their flowmeters, such as heating the meter to keep paraffin in a liquid state by using a heating system that maintains the temperature above the melting point of the paraffin.
Other strategies include chemical treatment programs that are used to dissolve paraffin buildup on the electrodes and liners, but these treatments are costly and require downtime of the meter. Some companies may also implement regular maintenance and cleaning procedures to ensure that the flowmeter is functioning correctly. However, regular maintenance and cleaning procedures are both time consuming and costly.
However, it is also likely that some oil and gas producers may not be aware of paraffin buildup issues in their electromagnetic flowmeters, especially if they do not have a comprehensive maintenance and monitoring program in place. In such cases, flowmeter errors may go undetected until they cause significant problems or downtimes.
South Texas Case
An oil and gas operator in south Texas was having to pull and clean its fouled meters every 60 days because it was unable to obtain a flow-rate reading from its meters.
Beginning in October 2021, the operator deployed what is now being commercially called the Aculon Measurement Integrity (AMI) treatment with distribution partner KopMan Industries to combat the paraffin buildup challenge on six of its electromagnetic flowmeters.
Flowmeters in production operations can be treated within 3 to 4 hours, per meter. New meters can be readily treated within an hour. There is no curing time or temperature requirement needed to treat these meters.
As a result of the AMI application, the operator was able to extend the time between maintenance of the meters from 60 to 540 days (i.e., 18 months) and counting.
Initially, the meters were physically inspected for fouling at 180 days and the electrodes were found to be free from paraffin deposition. The meters have not been pulled for maintenance due to fouling since, as the flow rates reported by the magnetic flowmeter have remained consistent with the operator’s daily volumes of produced water.
The AMI service consists of cleaning, preparing, and treating the surface of the magnetic flowmeter with omniphobic surface modification chemistries that repel both water and hydrocarbons. Aculon’s omniphobic chemistry is used to treat the ceramic or metallic electrodes and covalently bonds to the surface with a 2–5-nanometer-thick optically clear treatment.
The liner, typically composed of polytetrafluoroethylene, is treated with Aculon’s nano proof chemistry that is designed for nonmetal alloy surfaces. Such chemistry has been used outside of the oil and gas industry for over 2 decades.
Aculon has specialized in the synthesis and manufacturing of nano surface modification chemistries since the early 2000s and has developed more than 100 products to modify the surface energy of different types of substrates. In 2022, Aculon partnered with KopMan which had already been cleaning, prepping, and treating equipment using Aculon’s chemistry for 5 years and treated over 6,000 different pieces of equipment.
Together, the partners created AMI which was successfully used to extend the time between maintenance described here, six meters by a factor of nine. More operators are now beginning to allocate funding to the maintenance of the magnetic flowmeters to reduce the nonproductive time associated with the routine pulling and cleaning of magnetic flowmeters.
Since 2021, more than 250 electromagnetic flowmeters ranging from 2–10 in. in size have been treated with the AMI technology. Of the 250 meters treated, 200 were in produced water service that were pulled and cleaned in the field.
Today, there is less focus around the metering uncertainty of produced water as compared to hydrocarbons. However, this is changing as pressure mounts to ensure more accurate and reliable measurements of produced water in light of increasing handling and disposal costs, regulations, demand for recycling, and the need to improve leak detection. In summary, the field-proven AMI technology is capable of addressing these issues while improving long-term flow measurement performance.
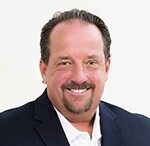
Clay Wernli, CEO and founder of KopMan Industries, is an industry leader in regenerating used equipment with complex geometries to “white clean” and application of surface property modification treatments. Since 1991, he has been in the industrial cleaning industry for the refinery market. In 2014, he entered the specialty services market consulting with operators on solving challenges associated with organic elements, fouling, and other issues disrupting production services. He worked with Ohmstede Industrial Services and Ohmstead LTD on building their ONE program in the refinery market. He is a graduate of the AIU Business School.
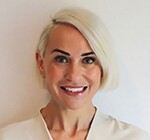
Elizabeth Cambre, SPE, is the global business development manager of energy at Aculon. She has 15 years of oil and gas experience working with both inorganic and organic scaling issues at Schlumberger in operations and technical sales in Oman, Qatar, and UAE. She was a former hydraulic fracturing and acidizing instructor and product champion of new technology at Baker Hughes. Additionally, she was the director of production enhancement at Tendeka. She has authored nine SPE publications and is the former co-chair of the SPE International Hydraulic Fracturing Technical Committee. She holds degrees in chemical engineering, mathematics, economics, international affairs, and Chinese (magna cum laude honors) from the University of Colorado at Boulder.