As producers push logistical and technological limits to operate in deeper water and more remote locations, maintaining and repairing offshore structures can present a number of challenges unique to these environments. One of the costliest is corrosion.
While fixed steel platforms are designed on the basis that there will be external fouling (marine growth buildup), floating oil and gas facilities require routine maintenance and preventive solutions to control corrosion.
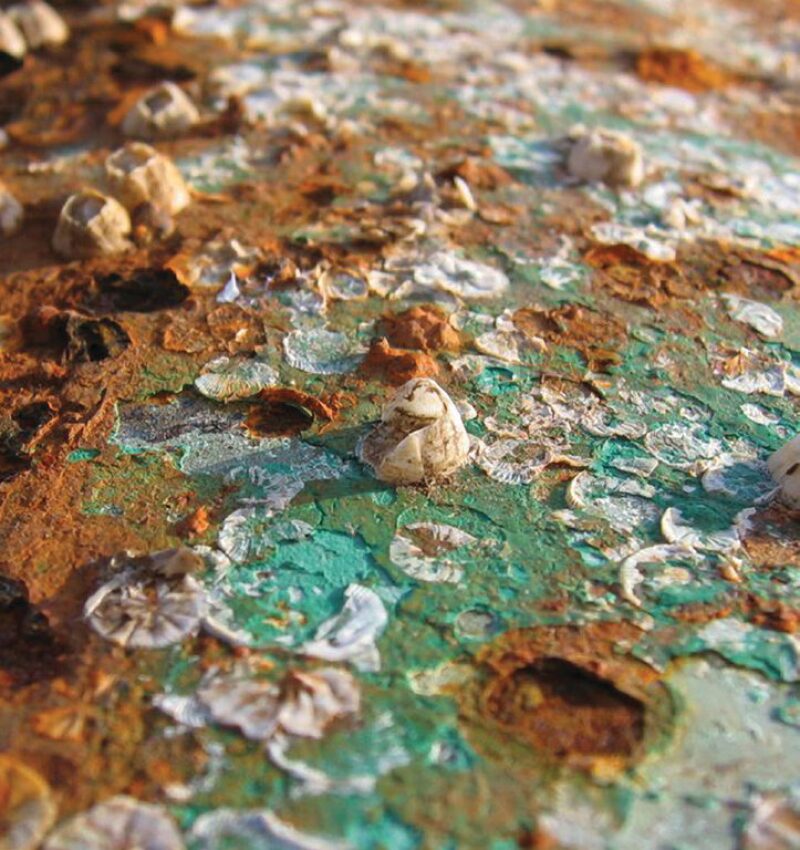
According to NACE International and other industry organizations, corrosion is costing the US oil and gas industry more than USD 25 billion/yr. The ramifications of corroding offshore structures can take the form of added costs for new construction, maintenance costs on aging/corroding equipment, inspections, structural integrity evaluations, and the correction of corrosion-related failures and outages. Unplanned downtime and other corrosion-related incidents can result in additional, often significant, expenditures in which there is already enormous investment.
Industrywide, there is a need to lower the risks associated with corrosion. Technical solutions and a life cycle approach to corrosion management must be integrated as part of the overall maintenance effort to protect older structures and to optimize future design life, strategy, and operational performance.
Working closely with industry partners and academic research institutions, ABS is investigating the fundamentals of corrosion management to provide up-to-date technical standards and guidance. In addition, ABS Group is studying a full life cycle approach to corrosion control that begins with preliminary design and follows through to life-extending applications for aging offshore facilities.
Guidance for Coatings InspectionNACE International has recognized the ABS Guidance Notes on the Inspection, Maintenance, and Application of Marine Coating Systems as quality introductory training material for marine coating inspectors. NACE governs the NACE Coating Inspector Program, which sets the benchmark for other coating inspector programs and is referenced by IMO MSC 215 (82). |
Protective Coatings
Coatings technology is the number one method used worldwide to protect floating offshore structures from corrosion, whether as a key preventive measure for carbon steel deterioration or for severe abrasion in harsh environments. Coatings and cathodic protection also are used to minimize the corrosion of metallic structures storing and processing hydrocarbons, such as crude oil storage in floating production, storage, and offloading (FPSO) tanks.
As part of an asset protection system, coatings are complex technical liquids that require constant monitoring and treatment. And if not selected and/or applied properly, coatings can degrade rapidly when exposed to corrosive environments, such as seawater and the marine atmosphere. The quality of the coatings applied to a floating offshore facility can directly affect its structural integrity, environmental performance, and value.
In offshore areas where saltwater or highly corrosive water chemistries can initiate fouling and bacterial contamination, heavy-duty epoxies are used in the corrosion control design of structures and facilities, which are constructed mainly of carbon steel.
Classification societies provide guidance for steel work used for the design, construction, and operation of offshore facilities. Rules are applied to vessels and facilities that fall under the structure’s class, with routine periodic surveys conducted to verify that these structures comply with the applicable rules and regulations. In addition, tankers and bulk carriers classed with members of the International Association of Classification Societies (IACS) and built under the common structural rules must comply with the Coating Performance Standard (CPS); any vessel type classed by ABS—regardless of size—that is built according to the International Maritime Organization (IMO) mandated Performance Standard for Protective Coatings (PSPC) (IMO MSC 215 (82)) during new construction receives the ABS CPS class notation. (MSC is the IMO’s Maritime Safety Committee).
Corrosion ConcernsBallast tank corrosion—It is difficult to maintain these coatings in practice. Unlike marine vessels that go to dry dock every 5 years, offshore facilities rarely return to dry dock for maintenance and repair once they are in operation. Operating conditions such as temperature and humidity and remote, stationary locations make maintenance and repair more difficult at sea.Anchor chains and mooring systems—Replacing anchor chains and mooring systems can incur huge costs for marine and offshore owners/operators. In its corrosion research of anchor chains offshore Indonesia, ABS discovered that chains in this environment can corrode up to five times faster than those in Arctic waters. Temperature is not the only factor; aquatic bacteria influence corrosion in this region. Antifouling coatings—Antifouling coatings have been continuously modified over the past 10 years to comply with increasingly strict environmental protection regulations, and some of the modifications have compromised coating effectiveness. Traditional marine antifouling coatings are designed such that they are cleaned by the speed and resistance of the water while the structure is en route. Because an FPSO or other floating offshore facility may be stationary, specialized antifouling coatings or systems are needed. |
Research and Development
Current research and development (R&D) efforts being carried out jointly between class societies and the marine and offshore industries include investigating coating friendly ship designs, improving application during the coating process, coating degradation and corrosion prediction modeling, and investing in emerging technologies, such as icephobic coatings.
In 2007, ABS established a coatings and corrosion group within its shared technology department that focuses on R&D. After assembling the coatings and corrosion team, an in-house coating inspection, testing, and training center was established to further coatings research within class. Also in 2007, the organization issued a revised and expanded edition of its Guidance Notes on Inspection, Maintenance, and Application of Marine Coating Systems to comply with the IMO PSPC standards. The document covers coatings technology as applied to ship structures and regulatory requirements for coatings in ballast tanks, void spaces, cargo tanks, cargo holds, and outer hull antifouling systems. Further updates to the Guidance Notes will be completed next year.
Addressing the need for offshore coatings-related guidance, ABS plans to release in 2014 new guidance notes providing best practices for the selection of protective coatings for both fixed and mobile offshore structures. This document will be the first of such resources provided by an independent source unrelated to any coating producer who is available to assist owners with calculating the net value of different coating types based on an asset’s expected life cycle, in-service conditions, and operating environment.
Ultra-High Temperatures
While there are existing epoxy coatings available for high temperature use, ultra-high temperatures and high-pressure environments will require best practices, guidance, and standardization in applying and selecting new materials to manage corrosion.
Offshore operators also must detect and manage the effects and potential risks associated with carbon dioxide (CO2) and hydrogen sulfide gas, which could cause sweet and sour corrosion, as these may be encountered during operations. The chemical reaction resulting from sour gas corrosion can cause coatings to blister and may introduce other integrity and safety issues.
Engineers at ABS are investigating how corrosion from CO2 combined with ultra-high temperatures can lead to higher rates of corrosion. One objective is to use key findings to allow classification societies to develop guidance to inform owners and operators of potentially negative consequences. Ideally, this research might also trigger regulatory bodies, such as IMO, to initiate a review of currently existing mandatory test parameters for crude oil-resistant coatings to be applied under the existing regulation.
Crude oil-resistant coatings designed to operate under the IMO PSPC-COT, Annex 2, MSC.288(87) regime in crude oil cargo tanks must be prequalified as dictated by IMO up to a maximum of 140°F. However, because today’s loading and transport temperatures of crude oils are sometimes far above 140°F, some crude oil cargo tank coatings are failing prematurely, implying that different conditions and compositions could be contributing factors.
ABS is conducting a pilot project to provide a preliminary study of the state and condition of the high-temperature reservoirs and the effect the hydrocarbons have on the storage and transport of crude oils from ultradeep wells. The goal is to update the test criteria for crude oil tank coatings to prevent coating failures, minimize life cycle maintenance, and provide a baseline for IMO to initiate a review of mandatory test parameters for crude oil-resistant coatings being applied under the existing regulation.
Corrosion Control in Seawater Ballast TanksChao Wei, ABS Understanding the need to identify technical solutions related to corrosion control in offshore and marine environments, ABS is supporting efforts at the Antwerp Maritime Academy (AMA) related to ballast tank corrosion on board merchant vessels. In 2007, the nautical science division at AMA began a multiyear in-situ study on corrosion parameters in the ballast tanks of more than 150 ships, which were gathered without applying any selection criteria. An average corrosion rate was determined by using simple statistical regression. Defining and applying this value will be useful for improving planned maintenance. Since 2010, the research team has focused on determining how the quality of steel influences corrosion rates. According to the AMA team, the general corrosion rate of standard construction steel in normal atmospheric conditions is approximately 0.1 mm/yr. In a humid, hot, and saline environment, the corrosion rate can increase rapidly. And when considering local pitting corrosion, these rates can become even more alarming. The service life of a vessel is governed in part by the condition of the ballast tanks, and research targeting quality control of corrosion protection systems is significant to improving corrosion protection in ballast tanks in compliance with IMO standards. Today’s ships are constructed mainly of grade A or AH steel, neither of which is particularly corrosion-resistant. A combination of traditional protective epoxy coatings and sacrificial anodes can generate acceptable results if conscientiously applied, installed, and maintained. Currently, the AMA Nautical Science team is focusing on a line of research with a goal of making ballast tank coatings resistant enough to last a lifetime with little to no maintenance required. |
Risk-Based Corrosion Management
Corrosion of offshore structures can result in significant operational cost, especially as the structure ages. Key drivers for implementing a corrosion management process include the expectations for longer service life, the high cost of replacing complex infrastructure, and restrictions placed on conducting structural maintenance on stationary assets without losing production.
The common approach to providing corrosion protection is based largely on traditional maritime practices centered on the concept of periodic maintenance in shipyards or other shore-based maintenance facilities. The problem is that these practices do not carry over well for managing corrosion on offshore facilities, which sometimes remain on location for the entire duration of their service lives.
A risk-based approach to corrosion management can be a cost-effective and safety-driven solution to help increase the service life of offshore facilities, drive down maintenance costs, and enhance safety. Risk-based corrosion management programs begin with assessing the underlying causes of corrosion damage and consider the options for minimizing or eliminating the damaging corrosion. The approach taken in such studies has been to reduce the risk of failure during the operational life by designing long-term corrosion mitigation plans that are implemented at different life cycle stages, thereby optimizing the long-term maintenance needs.
Life Extension
To go beyond the originally approved design life, the operator needs to demonstrate that the facility can be maintained as fit-for-service for the new life span. Aspects that need to be considered include the integrity of the primary structure, the effectiveness of the corrosion protection systems, past and future corrosion wastage, fatigue life, and design code and environmental load changes. Because the factors are fundamental to the future survivability of the facility, they need the approval of the regulatory bodies and the classification society and can be addressed in a life extension program that includes structural upgrades, supplemental corrosion protection, and some form of enhanced monitoring.
Successful life extension studies have demonstrated that careful re-evaluation of the design and extrapolations of expected future damage mechanisms—including fatigue and corrosion—contribute to successfully increasing the service life of offshore facilities. Research has involved developing novel solutions for rehabilitating and maintaining structural integrity, enhancing control of corrosion, and developing risk based on in-service inspection plans.
ABS Group was appointed to provide life extension services for an aging floating storage and offloading (FSO) facility for a major international oil company. The FSO was created by converting an aging oil carrier. The original design was for the facility to remain on station and in production until 2015. New oil reserve developments are causing the operator to consider keeping the FSO on station until 2020 or 2030, so a life extension program is needed. A feasibility assessment was undertaken to determine the work required to maintain ABS class for the extended period. ABS Group is also providing knowledge-based estimates for the extent of steel repairs and recommending corrosion mitigation plans to help achieve the extended life.
ABS Group also manages the ABS class and US Coast Guard (USCG) mandatory inspection programs for deepwater/floating permanent facilities in United States waters. The company develops work scopes, manages the on-site inspection program, and acts as a customer representative during the class and USCG visits to the facilities. If and when corrosion or other structural deficiencies are identified, the company serves as a technical adviser to provide solutions and obtain regulatory approval for repairs, if needed.
Through its Brazil Offshore Technology Center, ABS is working jointly with Petrobras on a major life extension project. The company has asked ABS to conduct an analysis based on localized offshore conditions (e.g., wave and salinity). The goal is to shed light on data to see how the operator can extend field life and extend FPSO life.
With an increasing number of offshore assets now reaching or exceeding the original design life and the economic pressures to maintain production, corrosion management will continue to be an integral component to maintain structural integrity and extend the life of an aging asset. Drilling in deeper water also will require new solutions, such as life extension for on-site facilities to avoid replacement costs.
Looking Ahead
As progress continues to be made in the practice of using coatings technology as a corrosion protection system, new methods will need to be developed to minimize corrosion damage to offshore structures and meet the demand for lifelong coatings. Advances in coatings technology can significantly reduce cost if developed and successfully demonstrated.
There is a need to address education and information sharing about corrosion across all engineering disciplines, with emphasis on improving technical specifications, enhancing the training and qualification of coating applicators, and stressing the importance of the complexities of successful coating application for long-term success.
Corrosion control is critical for preserving assets and the environment. Strategies that mitigate corrosion damage will require continual implementation of advanced technologies and updated policies, standards, regulations, and management practices to increase savings. Classification societies must help facilitate recommended design, practices, and technologies to promote better corrosion management across the marine and offshore sectors.
Nanoechnology Program: Icephobic CoatingsJames Bond, ABS ABS is providing funding to George Washington University, where a research team is investigating nanotechnologies in an effort to develop and test icephobic coatings to mitigate ice accretion. By profiling the surface at the nanoscale, researchers can modify the contact angle for water droplets so they do not adhere to a surface (or wet a treated surface). The value of this technology is that it could reduce the risk of ice buildup in Arctic conditions, thus mitigating a range of hazards. The goal of the research is to develop a testing standard to evaluate icephobic coating performance that includes ice adhesion, abrasion resistance, durability, and ultraviolet resistance. If researchers can overcome the challenges, the nanotechnology solution has the potential to expand the operational window of Arctic operations, thereby helping to improve safety. |
![]() | Brian Gibbs is the ABS consulting director of asset integrity management (AIM). He has more than 30 years’ experience in AIM related to the oil and gas industry. He is experienced in condition assessment, corrosion technology, failure analysis, corrosion prevention, maintenance strategy development, technical due diligence, risk assessment, management of in-service inspection plans, risk-based and prescriptive verification, and design and implementation of AIM programs. |
![]() | Edward Jansen is the ABS senior principal engineer of shared technology and heads the ABS coatings and corrosion group. He has more than 25 years’ experience acting as an expert witness and court surveyor in coating disputes on behalf of high courts in Europe, the United States, and the Far East. He represents ABS in the IACS expert group on coatings. |