Often located hundreds of miles away from land, offshore oil and gas platforms pose challenges with their unsheltered maritime environment, heavy weather, and risk of explosive, toxic, and corrosive atmospheres—with limited resources.
Sounds like conditions are ripe for robots on rigs.
In 14 years at Equinor, robotics researcher Anders Røyrøy has explored the application of robots in jobs that he describes as “dangerous, dirty, distant, or dull,” where use of a robot can serve to mitigate or eliminate safety risks for humans.
One of the highest priorities for robotic development and deployment, in view of their impact on inspection and maintenance routines, are remote operators for onshore and offshore platforms.
Failures in such harsh environments could jeopardize the lives of human operators, the environment, and process equipment. Semi- or unmanned operations can yield significant reductions in the risk of personnel exposure to dangerous chemicals. And in this age of social distancing, robots can be essential in providing contactless support.
Traditionally, bases of design have been focused on improving the safety of existing manned installations sites (brownfield)—those not designed with robots in mind—during potentially dangerous operations. Although it is possible to enhance safety, efficiency, and production availability on a brownfield site, French supermajor Total E&P is challenging that approach by developing remote or unmanned robotic solutions for specific functions on greenfield sites—that is, on automated, unmanned platforms designed to accommodate newly developed technology.
Generally unattended/unmanned installations are those that are visited only every 2 to 3 months. However, if the duration is pushed to one visit per year to perform annual maintenance tasks, it is possible to reduce the complexity of the platforms by removing equipment meant for human presence on site. There are several safety and cost advantages for operating remote production sites using robotics in place of crews.
For example, without the presence of personnel on site, an operator can often remove human-related systems such as living quarters, catering, evacuation boats, and staff transportation to and from its installation, along with inherent risks and high costs. Fewer boats, helicopters, and less road transportation leads to reduced operating costs and CO2 emissions. On such unmanned sites, Total is considering mobile, multipurpose, and ground robots that are ATEX-compliant (safe to operate in potentially explosive environments) and suitable for harsh and dangerous conditions.
A fully autonomous robot can gain information about the environment, move around and work for an extended period without human intervention, avoid harmful situations (unless those are part of its design specifications), and learn new ways to execute its tasks while adapting to changing surroundings.
Among Røyrøy’s projects is the HX cleaning robot built for onshore and offshore installations. The HX cleans and inspects tube heat exchangers, a job that sometimes exposes workers to dangerous chemicals and typically requires the heat exchangers to be taken out of service. The HX robots perform the task using high-pressure water hoses, removing the need for corrosive chlorine use and for human intervention, reducing HSE risk. What’s more, the heat exchangers continue to operate with no downtime.
Jean-Michel Munoz, Total’s Next-Generation Facilities R&D project manager, said, “Total has been very active on the field of ground robotics since 2014. After a successful proof of concept, Total is now engaged in the development of industrial-grade ARGOS-type (autonomous robot for gas and oil sites) robots.”
In 2013, following a gas leak at the Elgin-Franklin fields that resulted in a long shutdown and evacuation of personnel, Total partnered with the French National Research Agency to launch the ARGOS Challenge. Their goal was to design the first autonomous surface robot for oil and gas sites, in less than 3 years, to strengthen the safety of its workers. Five international teams dueled it out until December 2016, when the Argonauts’ robot won the challenge for the team representing Austria and Germany.
Total’s first development, the Offshore Ground Robotics Industrial Pilot (OGRIP) inspection robot, was first deployed in trials in April 2018, initially to work in an onshore gas plant before being sent to join the 120 workers on the North Sea Alwyn platform. In 2019, short-duration tests were performed for the calibration and integration of the robots in the plant. The robot is certified to work in gas environments without risk of ignition and can perform visual inspections, read dials, level gauges and valve positions, navigate through narrow pathways and up and down stairs, measure temperature and gas concentration, and detect and navigate around obstacles and humans.
Starting in 2019, through the ARGOS Joint Industry Project, researchers have been building fully autonomous ground robots to perform simple operational tasks that are generally done on wellhead platforms, such as isolating units, handling chemicals, and starting or stopping equipment for routine or downgraded situations. This robot will later be followed by one with more manipulation capabilities.
In another example, four robots developed by Robotic Drilling Systems will replace all manual and remotely controlled operations performed on the drill floor. They are dynamic in task execution, meaning they operate autonomously and at about the same speed as a crew under ideal conditions. This reduces both the need for crew members and the risk of accidents in the red zone on oil platforms.
And sometimes robots can take on tasks that humans simply aren’t built to perform. Take for example the OB7-Stretch robot by Productive Robotics. With its 1.25-m reach and 4-kg payload and fine dexterity, the arm can handle any pick-and-place task that requires a longer reach. The OB7-Stretch can tend multiple machines at one time when the robot needs to reach more than one machine or reach deeply into a machine.
Ramezani et al. (OTC 30694) see the promise of quadrupedal robots in navigating oil and gas facilities (climbing stairs, stepping over piping, and traveling through narrow passageways while performing inspection and monitoring tasks with minimal intervention by human operators). In field tests, their autonomous robot, the ANYmal, can accomplish tasks such as 3D mapping, monitoring of thermal buildup using thermal cameras, pressure sensing, and using color cameras to detect people and to carry out visual inspections.
“Having a reliable robot able to work in the harsh conditions of our industry is already a big achievement,” said Total’s Munoz. “However, benefits will come only once we master the management of a fleet of autonomous robots on a remote installation. Challenges are quite enormous since the integration of the robots in our operations requires that details have to be worked out thoroughly in advance.”
According to Emerj, an artificial intelligence (AI) research and advisory company, “AI robots are a promising area of interest particularly to help curb the risk of exposure to dangerous working conditions for many employees. While the US has experienced a downward trend of labor-related injuries or fatalities in the field in recent years, efforts to improve employee working conditions are a smart investment. We predict that improvements in robotic dexterity in any field (retail, agriculture, manufacturing, etc.) are likely to trickle directly to robots tasked with dangerous jobs such as those in oil and gas, and fire/rescue.”
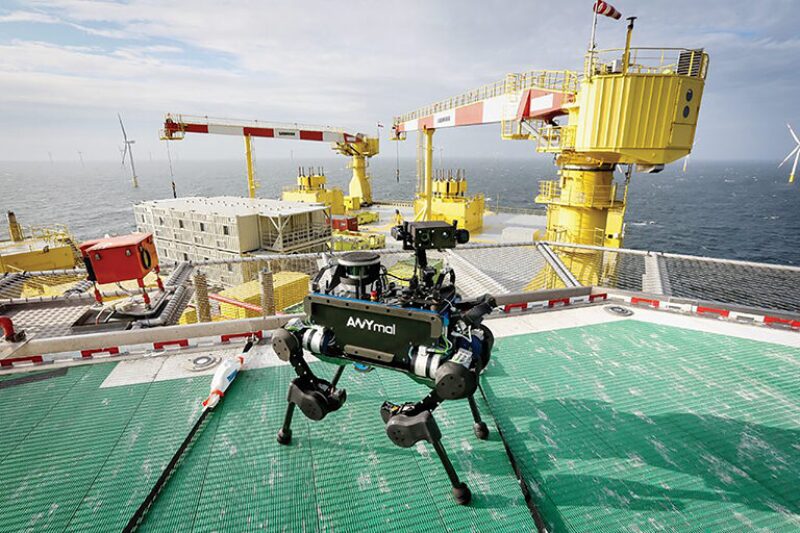
What Can a Remote Operator Do?
When considering different types of robotic solutions, it is important to assess what is needed in terms of mobility, durability, reliability, repeatability, accuracy, and safety vs. costs.
Robots are useful for improving working conditions, such as performing repetitive routine or monotonous tasks, in a manner that is faster, more accurate, and with less preparatory work. They can also be assigned specialized tasks such as contaminant removal from pressurized vessels, applying or removing paint, taking measurements, and investigating abnormal situations.
Cost savings are achieved through greater plant efficiency and longer uptimes, reduced downtime, less energy use, less travel, increased production, lower operating costs, and less emissions—like CO2—and waste.
According to SPRINT Robotics, a 5-year-old not-for-profit collaborative that promotes the development and application of robotics in inspection and maintenance, robots are also ideal for safety tasks such as first-line emergency response or replacing humans in hazardous environments. They can work at heights or in overboard activities, confined spaces, contaminated areas, pressurized areas, or in locations with either high (desert) or low (arctic) temperatures.
Nayer, in the technical paper “Field Applications for Advanced Robotics” (OTC 25746), said, “Current robotics technology is sufficiently mature for near-term applications in surveillance, inspection, and maintenance operations for facilities and subsea systems. More sophisticated systems could be used in the future for challenging applications like autonomous well intervention, pipe inspection, and deepwater maintenance and repair.”
It is important to know each robot’s limitations and capabilities before integrating them into operations. Digital simulation can provide a risk-free tool for testing functionality within specific working conditions, improving the outcome of potential missions, and demonstrating safety to humans and to the environment. Yet, while there are benefits for using a simulation model as a supporting tool, its use cannot replace demonstrated performance in the real world.
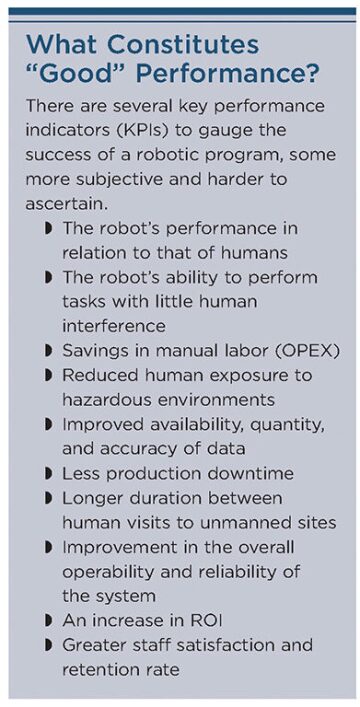
What’s in a Robot?
A complete robotic system consists of the robot itself and a human machine interface (HMI)—sometimes referred to as a graphical user interface (GUI)—that provides the ability to act and interact with humans and the environment. A range of gas, vibration, and heat sensors (cameras and positioning systems such as GPS/ LIDAR), a communication network, and data storage and processing systems may all be contained onboard.
The HMI brings simplicity through centralized, intuitive control and manipulation. Of course, this includes technology, but it involves far more than hardware and software. An HMI will manage/control the tasks, monitor performance (verification, feedback), collect data (processed or not), and program and teach the robots their mission, routes, actions, and reactions.
Robots are suited for nonstop data acquisition, processing, and storage/transmission. Ground robots can be equipped with mounted sensors to gather data, and an onboard CPU to connect to off-site servers that analyze data streams in real time. The data can be used with predictive algorithms to determine appropriate actions, again to improve the overall quality of operation and maintenance of a facility.
For this purpose, Total is developing among other tools a new function on the field architecture called the Operation Room. From there, multiple autonomous robots will be monitored and continuously provided with tasks according to their location, capabilities, and battery level.
And this all can be done in either a remote or tele-operated mode or even in autonomous mode, in which the robot executes its programmed mission by itself and can decide by itself if it is doing the right thing.
“As sensor machines, robots can gather operational data for any piece of equipment (such as motors, gears, pumps, generators, etc.). The data can be run through AI algorithms to better predict performance, prevent premature failures, or to optimize just-in-time maintenance schedules,” Dietsmann Robotics Business Manager Duco Drenth said.
And according to the ARC Advisory Group, adoption of AI in manufacturing and robotics is fueled by internal and external factors such as demand for greater variety, traceability, flexibility, production efficiency, speed, faster market dynamics, and lower operational costs.
To realize these gains, end users must first put in place a data strategy and management plan. That is, they must consider how to use the data, how and where to process, store, and secure the data, how to deal with changes in data, and how to verify and visualize the data.
Developers must understand in which cases a computer makes as-good or better and faster decisions, for example which tasks are prone to human error, and in what cases humans are needed for their feelings, emotions, norms, and values. The HMI between the robots and operators is important for efficiency, effectiveness, safety, and operator confidence.
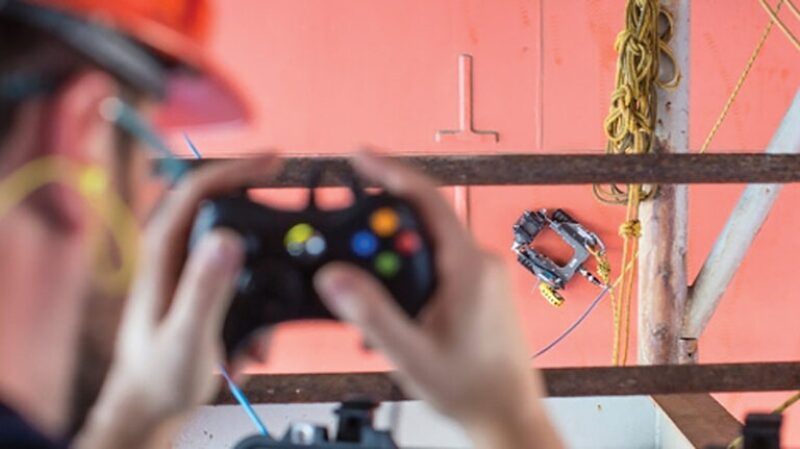
What’s in the Way?
“The development of technology is not the issue,” said Steven Trevino, program manager for the North American chapter of SPRINT Robotics. “In fact, technology is maturing much faster than business readiness—that is, compared to the end user’s business processes, worker training, cultural acceptance, and infrastructure to accommodate the solutions.”
He added, “It still requires not only technical but organizational advancements to be readily accepted and supported by the industry.” End users and technology developers need to align on goals and priorities to close the gaps.
It appears that large-scale deployment is currently hindered by the expertise of staff members, limited budgets, conservatism, risk avoidance, limited leadership, and lack of industry-wide R&D cooperation. Solutions still require real-life testing and integration into daily operations.
Some companies are implementing an MVP—minimum viable product—approach, where they start with the minimum functionality that still delivers a solution for a problem. Deploying MVP technology will give the whole value chain the ability to learn, improve, and ultimately accept robotics as fundamental inspection and maintenance tools—in turn, success with the MVP builds confidence and revenue for more complex deployments.
For advanced development there exist some further challenges.
- People/cultural (e.g., acceptance and trust, perceived threat to the staff’s personal safety, job security, or mental health; conservatism of decision makers/end users; and lack of industry-wide cooperation)
- Business (e.g., adapting working processes)
- Possible obstruction by industry regulators and governments to accept the “new normal” as standard
- Global delivery and service capabilities (of contractors/service suppliers)
- A working environment that requires ATEX-proof robot design
- Technology issues (such as network coverage, bandwidth/latency, battery management, cybersecurity, data management, offshore access, and secure data storage)
- Costs for retrofitting facilities and limited budgets by end users
Dietsmann’s Drenth asserted that the greatest antagonist to change is company culture, and the industry’s vision on automation, digitalization, and robotization—along with the willingness to act and invest accordingly.
According to a December 2018 Pew Research Center survey, about eight in 10 US adults (82%) said that by 2050, robots and computers will definitely or probably do much of the work currently done by humans, Nearly six in 10 Americans said in 2017 that there should be limits on the number of jobs that businesses can replace with machines, even if those machines are better and cheaper. A large majority (85%) said they would support restricting workforce automation to jobs that are dangerous or unhealthy for humans to do.
Given the mixed feelings about the new technology, effective change management will be crucial, according to Trevino. A company that wishes to adopt this technology must be clear in the reasons why it wants a robot and create suitable work processes in line with the robot’s limitations and in conjunction with its operating environments.
For example, through “cohabitation,” humans and robots could be working on different tasks within the same environment; in a collaboration scenario, humans and robots (“cobots”) work together on the same task.
Another issue is the limitations of workers where skill gaps exist for qualified robot operators, technicians, and engineers.
One alternative is a mobile robot, provided its interface is intuitive and it can be used as a daily tool with minimal expert knowledge. For the near future, operators will need the skills to program the robot’s routes, sequential actions, tasks and sub-tasks, and accept complete missions. They will also need to program safety actions in the event of a malfunction or an encounter with an obstacle.
“Technology will unlock employees’ ability to grow and take on new roles,” Drenth said, “but it must be presented in a positive way. When leaders are careful to lay the foundation for the best implementation of automation, employees will want to join in. They grew up with computer games, online shopping, and an endless range of social media applications, blogging and vlogging their way into adulthood.
“When they see where the technology is headed—in terms of specific projects and the overall company vision for digital solutions—they will react favorably.”