This paper describes the use of a root-cause-failure-analysis (RCFA) process to improve artificial-lift-system performance in a project in Chad. The process was established with the objective of evaluating every failed pump system to determine the reason for failure, identify contributing factors, and monitor trends. The process has helped to reduce the failure frequency by more than 70% on electrical submersible pumps (ESPs) and by more than 50% on progressing-cavity pumps (PCPs), despite the fact that the ESP population has more than tripled and PCP installations have more than doubled.
Introduction
The Chad Project is in the central African country of Chad, approximately 430 km south of N’Djamena, the capital city. The vast majority of the wells are completed with 9⅝-in. production casing and perforated with 7-in. conveyed perforating guns at 12 shots/ft. The wells are surged to remove perforating debris and are gravel packed for sand control before the artificial-lift system is installed. Typically, ESPs are run with 4½-in. production tubing and PCP systems are conveyed with 5½-in. tubing (Fig. 1).
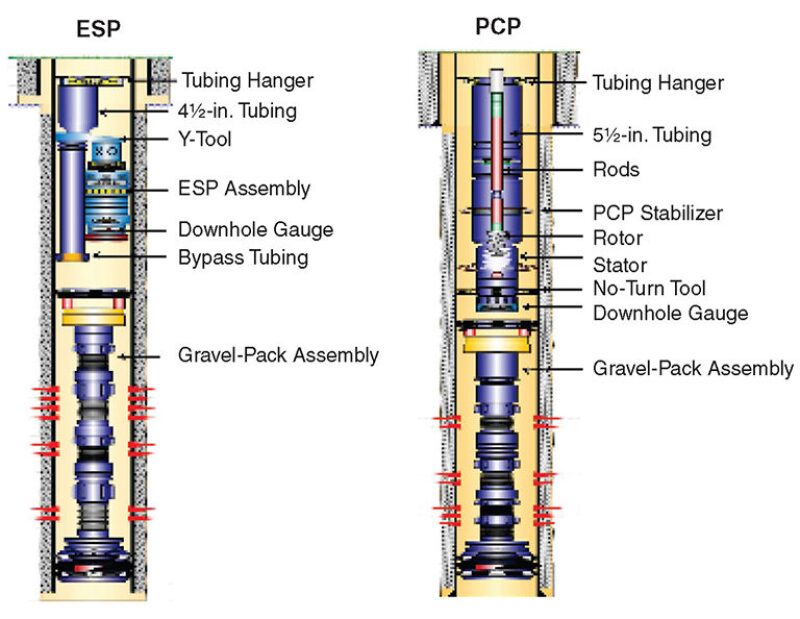
Formation properties are quite favorable, with permeability ranging from 0.5 to 10 darcies and porosity ranging from 24 to 28%. The hydrocarbon-bearing deposits are found at depths as shallow as 3,000 ft and as deep as 6,000 ft. The crude produced from these reservoirs has a gravity of 17 to 24°API, in addition to being heavily biodegraded and undersaturated, with viscosities ranging between 40 and 800 cp. Production is sweet, with no hydrogen sulfide or carbon dioxide, and reservoir temperature is low at 140°F.
High viscosities are encountered when water-in-oil emulsions are formed in the pump when the produced oil and produced water are mixed. At high water cuts, the mixture becomes an oil-in-water emulsion and ESP performance is not degraded. The inversion point varies because of stabilizing conditions but may be in excess of 80% water cut. The PCPs are not affected directly by the presence of severe emulsions; however, the emulsion typically creates higher flowline pressures, causing the pump to work harder because of higher backpressure and higher differential pressure across the pump.
Artificial-Lift Operations
Artificial-lift equipment in this project was first used in 2003, with the ESP being the primary type and the PCP being the secondary type. The decision to install an ESP or a PCP depends on the forecast production profile. Typically, if the total fluid production forecast is less than 850 BFPD, a PCP system will be selected; however, an ESP with a Y-tool is preferred when access to the reservoir is recommended for water shutoff, production logging, or special stimulation treatments.
In 2007, the average number of ESP failures per month was nine, with a total average active-ESP-well population of 242 (average failure frequency of 0.45 and peak failure frequency of 0.65). With the help of the RCFA process, the average number of ESP failures per month was six in 2013, with an ESP-well population of 615 (a failure frequency of 0.12). The average number of PCP failures per month in 2007 was six, with a PCP-well population of 155 (a failure frequency of 0.47). The average number of PCP failures per month as of July 2013 has been reduced to 3.7, with a PCP-well population of 210 (a failure frequency of 0.21). High artificial-lift-failure frequencies led to proliferated production downtime and a workover-rig backlog, with the majority of rig activity being pump repair.
A collaborative effort was initiated between the operator and equipment supplier to increase the reliability and performance of the artificial-lift equipment. This alliance resulted in the development of the RCFA process and a fully functional artificial-lift-equipment service center at the Chad field site.
The RCFA process uses the results of dismantle/inspect failure analysis and capabilities of the Field Service Center to increase run life of the ESPs and PCPs.
Challenges
During failure-analysis review meetings, all collected data are reviewed to determine the root cause of failure. If additional data are required, action plans are discussed and responsible parties are assigned to gather and share the necessary data in a follow-up failure-analysis review meeting. Because of the remote location of the operations, delivery of equipment can take several months; this could have an effect on the performance of the artificial-lift equipment should replacement parts or new equipment be needed. Implementing new technologies and equipment also presents a challenge caused by the amount of time required for shipping; therefore, small trial programs were used to validate concepts.
RCFA Process
The RCFA process used in the Chad Project consists of gathering the data for each artificial-lift-system installation, performing dismantle/inspect failure analysis, and conducting a failure-analysis review meeting with the team. The purpose of the RCFA process is to review the information collected, identify the root cause of failure, share learnings, and provide recommendations to prevent recurrence. Reviews of the data gathered cover the entire artificial-lift process consisting of design parameters, installation reports, operational data, and dismantle findings. The key to a successful RCFA process is reviewing and inspecting all artificial-lift equipment regardless of type or run life.
Gathering Data. The collection and sharing of data have contributed to the foundation of success for the RCFA process. The data reviewed during the RCFA process include reservoir profiles and pump curves used in sizing and selecting the appropriate artificial-lift equipment. Operational data reviewed in the RCFA process include pressure, electrical readings, downhole temperature, well-test data, and parameter settings used in the surface controller.
Dismantle/Inspect Pump Analysis. After equipment is pulled from the well, it is returned to the service center and is subjected to all factory acceptance testing to validate integrity. If a piece of equipment fails testing, the component is dismantled and inspected for failure cause on a dismantle bench.
The dismantle/inspect process is completed by the service company, with a representative from the operator present to witness the findings. Inspection of the failed equipment entails verifying key dimensions and functional requirements of the equipment on the component-specific teardown sheets.
Failure-Analysis Review Meetings. A weekly failure-analysis review meeting to review all open failures is held by means of a teleconference among the operator, equipment supplier, and field operations personnel. The purpose of the review meetings is to guarantee transparency among the parties while ensuring that the root cause of failure is identified. The key to determining the true root cause is to focus on why the equipment failed and not on what equipment failed. It is important to know what component failed because this may help to provide insight concerning the cause; however, it is paramount to derive why the equipment failed and whether it is related to manufacturing, to design, or to operating or well conditions.
Service Center
The Service Center, located in the field operations, is designed to validate all acceptance tests performed after manufacture for ESP components. The ESP motors and seals are tested upon arrival in the country to ensure that no issues have occurred during shipping. All pulled equipment is retested to identify failed components and conduct further analysis. The Service Center is also capable of testing PCP systems.
ESP Capabilities. Testing capabilities for ESP equipment (Fig. 2) include efficiency, vibration, head, and brake horsepower. New ESPs are typically not tested; however, all pumps returned from service are tested before being placed back into inventory or being dismantled. The ESP cable and sensors are tested during final assembly.
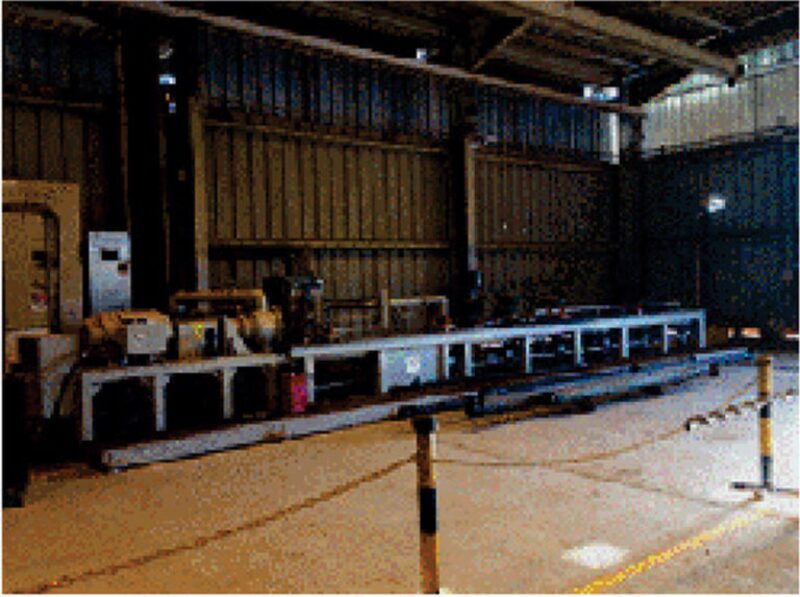
During a pull of an ESP string from the field, the motor and downhole sensor remain assembled when shipped to the Service Center. The attached sensor is tested through the motor by means of the sensor surface unit. This testing verifies that the sensor outputs are measured accurately. All ESP motors are fully tested before being run downhole and are tested again after being pulled. ESP seal sections are also tested to ensure that thrust loading, horsepower, vibration, and mechanical seals are within factory performance and functional limits.
PCP Capabilities. In the early stages of the project, PCP systems were tested for flow, pressure, torque, and revolutions per minute on a bench, as seen in Fig. 3 PCP systems were tested before being run in hole to validate the factory bench test and to verify that no damage was caused to the unit during shipping. Because of the nature of the PCP failures, most PCP systems do not receive a bench test after being pulled from the well. The independent testing capability for PCP systems enables testing of pumps before and after being pulled, if needed. The key dismantle/inspect checks include verifying model numbers, serial numbers, component lengths, and component condition.
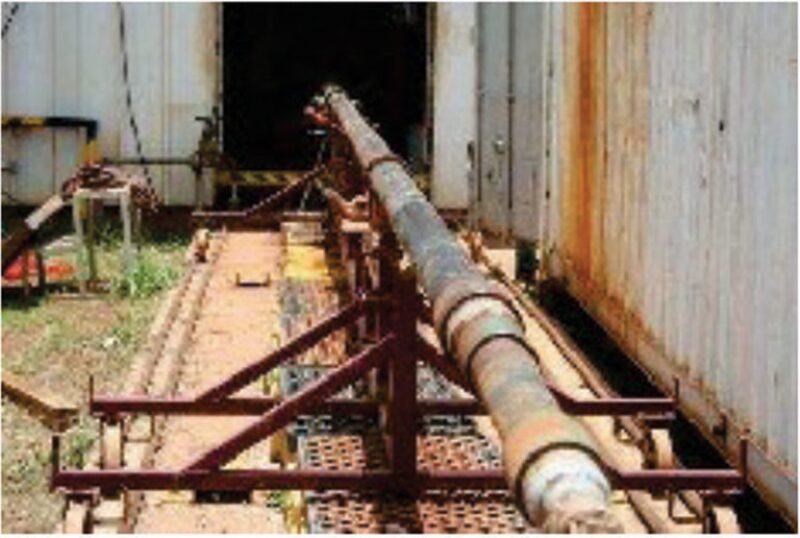
The PCP inspection also includes inspecting torque anchors and providing analysis of the rotor and stator after the unit has been run.
Performance Monitoring
In order to provide clear communication to all parties involved, recurring overview meetings are held among the operator, the service company, and the field operations staff discuss current run-life statistics and to make recommendations for improving or extending the run life; hence, this team has been named the Extended Run Life Team (ERLT). These ERLT meetings consist of technical and operations staff from all parties, including management from each party, focused on action items identified by the RCFA team. Key performance indicators are discussed in these meetings to confirm that the metrics established are being managed to optimize pumping performance. Constant monitoring of the failure data and frequent failure-analysis review meetings have improved performance of the artificial-lift systems, as shown in Fig. 4 By reviewing the current failures, the ERLT has also been able to make application improvements with the ESP seal sections and motor.
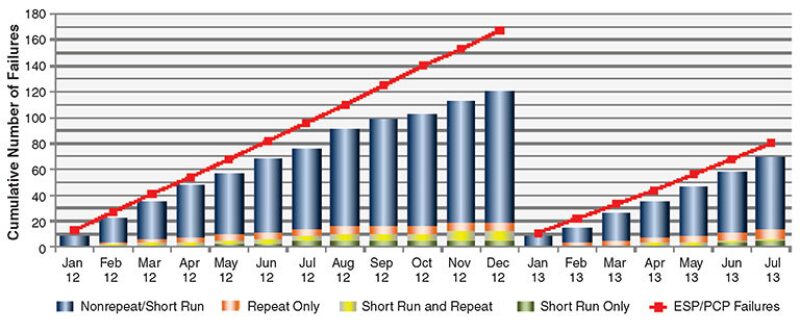
The primary focus of the ERLT is correcting issues with short runs (consisting of failures less than 90 days) and with repeat failures within 365 days, as seen in Fig. 4. This figure shows that the RCFA process has helped to focus on short-run and repeat failures; it also shows that actual failures are below forecast. For instance, in October 2012 there were only three failures with approximately 800 active wells.
A study of these failures helps to identify opportunities to improve operations and procedures that are causing the failures. Once the opportunities are identified, a development plan is put together and implemented to improve pump performance and extend equipment run life. Further data analysis is conducted on the long-run wells to explore ways to extend run life of ESP and PCP equipment.
This article, written by Special Publications Editor Adam Wilson, contains highlights of paper IPTC 17230, “Artificial-Lift-Performance Enhancements by Applying Root-Cause Failure Analysis,” by S.G. Lapi, SPE, and M.E. Johnson, SPE, ExxonMobil Production Company, and B. Arisman, SPE, GE Oil & Gas, prepared for the 2014 International Petroleum Technology Conference, Doha, Qatar, 20–22 January. The paper has not been peer reviewed. Copyright 2014 International Petroleum Technology Conference. Reproduced by permission.