In the quest to cost-effectively boost production, operators are experimenting with artificial lift methods and how digital tech can boost its performance.
Artificial lift experts are increasingly adding artificial intelligence (AI), machine learning (ML), and autonomous operations into their workflows because these data-driven technologies are demonstrating they can generate uplift when they are thoughtfully developed and deployed. Operators are also looking at the performance of high-pressure gas lift (HPGL) wells compared to wells using electrical submersible pumps (ESPs) for artificial lift. Finally, operators sometimes have to decide whether to risk replacing equipment that seems to be functioning, even if at subpar levels, in a bid to increase production.
Digital Boost
Optimized gas lift workflows and autonomously implemented ESP set points are helping ExxonMobil and Vital Energy produce more oil.
Gas lift is a popular artificial lift method partly because the system is simple, robust, and inexpensive to operate, but optimizing it has historically been time-consuming. SPE 219553 outlines ExxonMobil’s approach to automating gas lift optimization for wells in the Permian Basin. The resulting workflow, which relies on AI and ML, generated a 2.2% uplift in production at the more than 1,300 wells where it was deployed, without requiring changes to surface or downhole equipment or generating additional work for personnel.
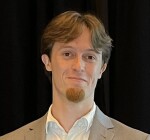
Derek Burmaster, production optimization engineer for ExxonMobil Upstream Integrated Solutions, said during SPE’s Artificial Lift Conference and Exhibition (ALCE) in August that one of the big benefits of applying the closed-loop iterative well-by-well gas lift optimization workflow is that it removes the need for an engineer or specialist to have to go into the field repeatedly to change injection rates and analyze the well’s data.
“For each well, that might take a few hours, at least,” he said. “We’ve done this on hundreds and hundreds of wells, and it happens every month without anybody, any manpower, or anything. So that’s one of the huge benefits of doing this in a data-driven manner.”
Gas lift is so robust that it can be challenging to diagnose if the system is operating in a suboptimal state, the paper noted. Changes in a well’s water cut or productivity can cause a previously optimized system to lose efficiency, which may not otherwise be known for years.
ExxonMobil was seeking a method to optimize gas lift that would continuously monitor the state of the system and respond immediately. The resulting closed-loop software iteratively performs multirate tests, analyzes the results, and remotely implements set-point changes to optimize the wells.
“The optimization process is most effective in an iterative form, in which each multirate test produces a model that suggests a given change,” the paper stated. While each model produces its own optimal injection rate, subsequent models may point to the same injection rate, and thus changes are not always made, Burmaster noted.
Even if an initially suggested set point is not optimal, it will “push the well in the right direction,” which improves the starting point for the next test and helps the well reach an optimal set point over the course of a few iterations, according to the paper.
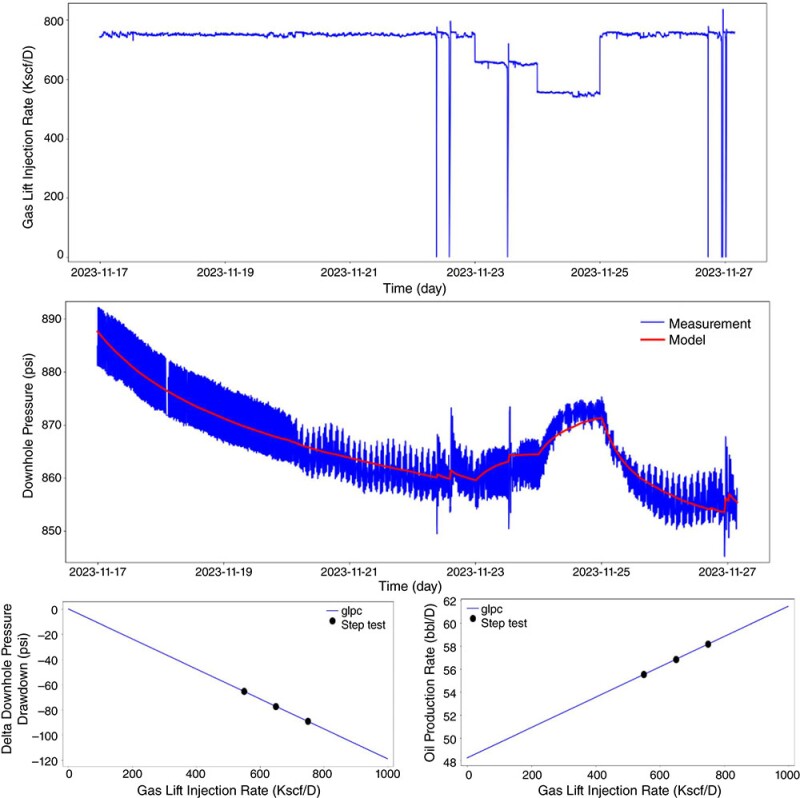
The workflow was tested in two different stages, with the first 3-month stage requiring manual approval of the recommended set points.
“Somebody in the field would go through and say yes and no,” Burmaster said, and that resulted in an average uplift of 1.87% in the tested wells.
During the second 3-month stage, most changes were automatically approved and implemented. He said that approach improved the average uplift to about 2.2%.
“We’ve taken this to be a pretty significant success,” he said.
Vital Energy tackled optimization and automation of ESP set points as a method of removing a human bottleneck while increasing production. The operator traced its journey to autonomously optimize ESPs on wells in the Midland Basin through the use of ML, AI, and an artificial neural network in SPE 219528.
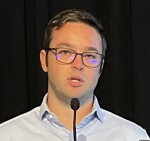
Ryan Erickson, operations engineer at Vital Energy, said during ALCE that Vital Energy created a machine-learning inference model (MLIM) that generates ESP set-point recommendations based on user-defined goals, such as maximizing oil or total liquid production. Solid data is necessary for optimization, so gauges and sensors collect values such as pump intake pressure, motor temperature and speed, and more every quarter-hour from the wells. The model uses that data to forecast a well’s production and make set-point recommendations for the ESP to safely maximize production.
In the early stages of the journey, petrotechnical experts approved or rejected the recommended changes.
But, Erickson said, to achieve “true, real-world AI, you actually need to take that a step further, have that autonomous piece, and take the human out of the loop.”
Once the MLIM was sufficiently trained on a dataset of 193 ESP-lifted wells, Vital Energy used it to generate set-point recommendations for about 60 wells, which was about one-quarter of the operator’s Midland Basin ESP-lifted wells. The MLIM was refined over 9 months before deployment expanded to more than 200 wells, or more than 80% of Vital Energy’s Midland Basin ESP‑lifted wells.
The operator then measured the quality of the MLIM set-point recommendations by calculating next-day uplift, with results indicating a mean program uplift of 2 to 4% after the recommendations were implemented, according to the paper.
Erickson said Vital Energy also wanted to compare results of implemented recommendations versus set-point changes that didn’t align with the MLIM recommendations.
“We saw an average of 1.8 times higher uplift when the recommendations were accepted versus when they were rejected, or when set-point changes that were counter to the recommendations were made,” he said.
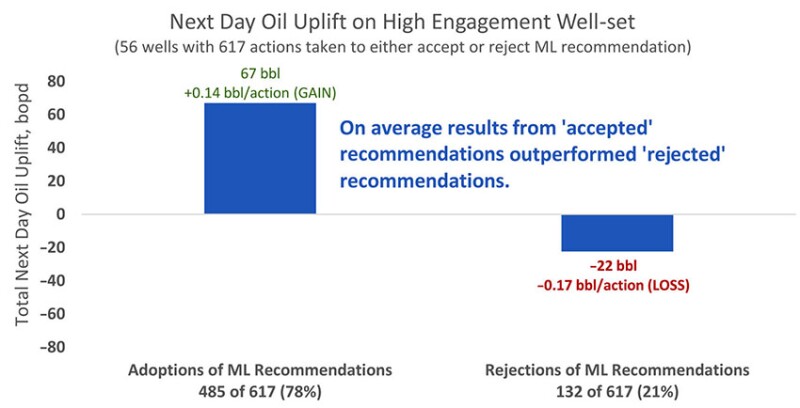
In addition to the increased uplift, Vital Energy also noted that ESP run lives improved year over year, that mean time to failure increased by 49%, and ESP uptime increased by about 4% in 2023 over 2022 rates.
“We don’t fully attribute that to the machine learning model, because we’ve got a lot of background efforts going on,” he said.
This deployment indicated the MLIM was possible to run at scale and, based on the increased uplift, it was effective at scale. Further, the scaled deployment didn’t place observable pressure on lease operating expenses while key performance indicators of ESPs improved year over year.
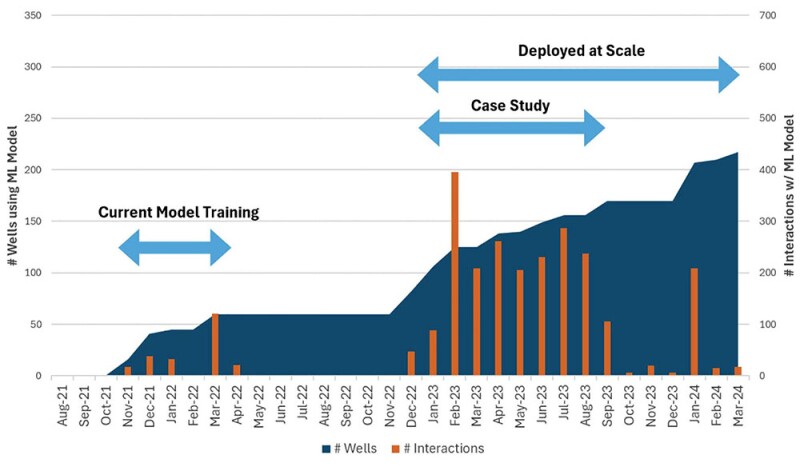
Based on this success, Vital Energy trialed full self-pumping (FSP) mode on nine wells, with the MLIM recommendations being autonomously written to field devices, he said.
The wells operating on FSP have autonomously produced more than 1.4 million bbl of total liquids and 500 MMcf of natural gas. Oil production for the six wells with the highest FSP utilization outperformed forecast expectations by more than 3%, and total liquid production outperformed forecast expectations by more than 5%.
According to the paper, the favorable results during an extended period of 100% FSP utilization indicate the FSP solution is accretive and does not lead to adverse effects for operations or equipment.
Erickson said that before the autonomous deployment, there was a “human bottleneck” because people couldn’t get to so many wells “multiple times a day to implement the changes.”
Instead, petrotechnical experts can focus on other tasks, he said.
They can “take (their) eyes off those wells for extended periods of time and free up that time to do something that’s more valuable,” he said.
HPGL, ESP Showdown
Operators often turn to ESPs to maximize production in wells with high water cuts. The downside is they are vulnerable to damage from reservoir solids and replacing a failed ESP costs money in addition to the lost production.
BPX Energy and DG Petro Oil & Gas both investigated how HPGL wells stack up against ESP wells.
A five-well BPX pilot aimed to see how HPGL compared to the operating costs and production rates of ESPs, an artificial lift method typically used in the Delaware Basin.
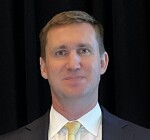
Speaking during ALCE, Kevin McNeilly, Permian Basin artificial lift optimization team leader at BPX, said the key question BPX sought to answer with SPE 219552 revolved around whether HPGL wells could achieve similar drawdowns as ESP wells in the area.
“That’s a question everyone has in their minds, and we were really excited to try. But along with that, (also) reliability, uptime,” he said. “Adding one more piece of kit in there with the compressor, that’s another big question. What will the reliability of these systems look like?”
The five pilot HPGL wells are all on the same pad and were drilled and put online at the same time. Each well in the pilot was connected to its own electric 150-hp high-pressure compressor, which was supplied by Estis Compression LLC. A nearby BPX-operated midstream facility provided the gas supply for the HPGL pad. For comparison, BPX selected nearby similar wells equipped with ESP that were on a different pad but brought online at the same time as the HPGL pilot pad wells. The paper noted the compressors had shown run time exceeding 99% after 6 months of service.
“We’ve been really impressed with the Estis compressors,” McNeilly said, noting only one trip was required over the first 10 months of operation. “Really happy with the uptime. The operators love it. I mean, it’s set it and forget it.”
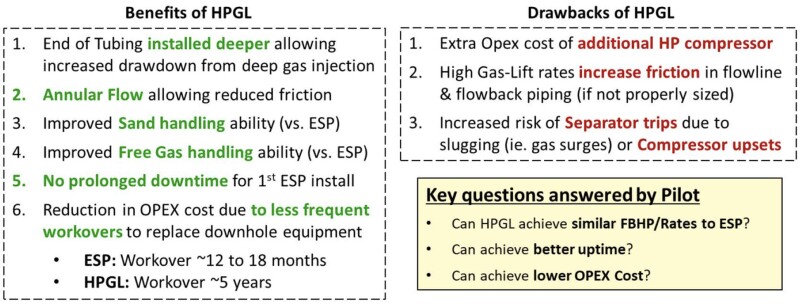
One of the big surprises the pilot delivered was the surface arrival temperature of production fluid from the HPGL wells. McNeilly said there was a “significant” drop in arrival temperature compared to ESP wells producing at similar rates, with produced fluids from the HPGL wells arriving at temperatures from 5°F to 8°F cooler than fluids from ESP wells.
“We saw this in every well,” he said.
Typically, Delaware Basin wells use rented cooling equipment during the early production period to ensure the fluid temperature is below the temperature rating of the export flowlines. With the fluids from the HPGL wells arriving at lower temperatures, the coolers weren’t needed as long, which resulted in an Opex savings, McNeilly said.
Another finding was that the wells on HPGL produced less sand than those using ESPs, he said.
“This one’s harder to explain than the temperature effect, but again, we did see it. We did see it on all five wells,” he said.
The upshot, he said, is that this phenomenon allowed BPX to remove the sand knockout flowback equipment on site, resulting in additional Opex savings.
“It’s something that we did see that we want to explore,” he added.
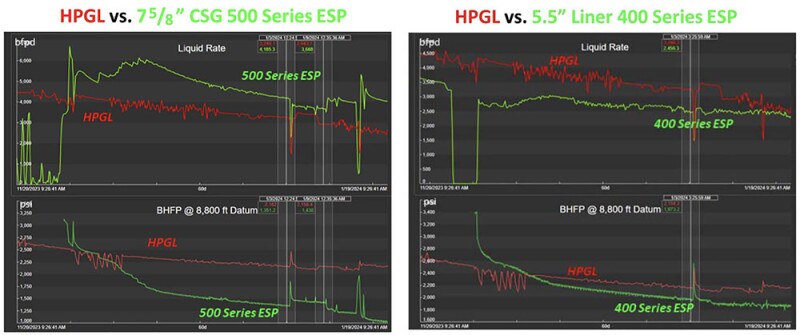
According to the paper, the overall results from the HPGL wells were satisfactory, with the company planning to consider HPGL as an artificial lift method moving forward.
When HPGL wells were compared to nearby similar ESP wells, the 7-5/8 in. CSG 500 Series ESP wells achieved slightly higher rates and drawdown than the HPGL wells, the paper stated.
“I don’t think this was a big surprise to many people,” McNeilly said.
On the other hand, when compared against 5.5-in. liner 400 Series ESP wells, the HPGL pilot wells achieved similar rates and drawdowns, the paper stated.
“Surprisingly, for a lot of people in my organization, high-pressure gas lift matched, outperformed … but it was very close to the 400 Series ESP in terms of rate and drawdown. This surprised a lot of people who said, ‘ESP is the best form of artificial lift,’” he said, adding the data from the pilot showed HPGL is competitive. “The big disclaimer is: It just depends so much on the well conditions.”
And while HPGL will be considered moving forward as an artificial lift method, McNeilly said BPX is “not giving up hope” for ESPs.
Elsewhere, DG Petro wondered whether HPGL might serve as a suitable alternative for high-water-cut wells, so the operator compared how the two methods performed in terms of Capex, Opex, run time, and hydrocarbon recovery for unconventional Wolfcamp wells and detailed the findings in SPE 219536.
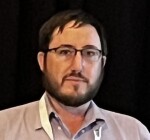
Speaking during ALCE, Stephen Fusselman, an asset manager for DG Petro Oil & Gas, said the experiment was carried out on a pair of Permian Basin wells that were drilled at the same time from the same pad to the same depth in Wolfcamp A, as well as a third well into the Wolfcamp B.
Wells 1 and 2, which were drilled and completed in 2018, had a water cut exceeding 95%, and were on conventional gas lift. In April 2022, the operator decided to upgrade artificial lift methods for the wells. An ESP was installed in Well 1 while HPGL was selected for Well 2.
The first well “looked good” at first, Fusselman said. According to the paper, Well 1 initial production exceeded Well 2 by 120%. But in May 2022, Well 1 output dropped by half and by the fourth month the ESP failed. Analysis of the ESP attributed the failure to reservoir debris, and a new ESP was installed in August 2022. An influx of reservoir solids led to ESP failure in November 2022. Discussions with offset operators indicated that ESP failures caused by reservoir solids and debris are common in the area, according to the paper, so this well was put on HPGL.
Well 2, put on HPGL in April 2022, on the other hand, had a runtime efficiency over 99.5%, with downtime associated for regular maintenance. It surpassed Well 1 oil production after 4 months and its gas production after 8 months.
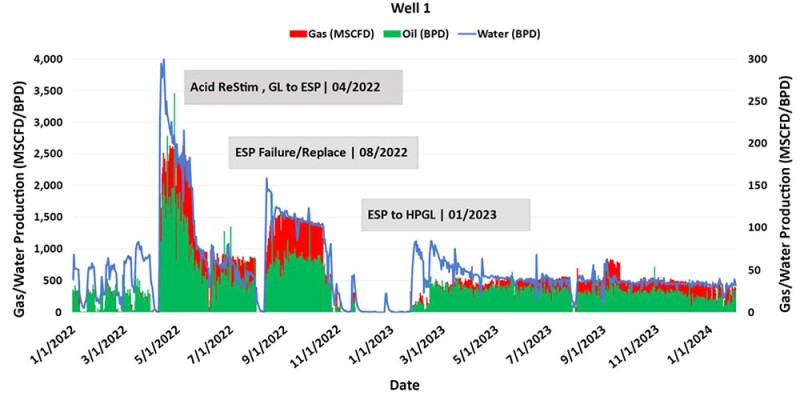

Well 3 was drilled and completed in Wolfcamp B in September 2018 and had been on an ESP that failed in June 2022. In August 2022, it was replaced by an identical ESP, but that ESP was later lost in the well due to bolt-stress failure. Fishing was unsuccessful, and the operator opted to place this well on HPGL as well. It had a higher gas/oil ratio and lower water cuts than Wells 1 and 2 and so was considered a better HPGL candidate.
On HPGL since January 2023, both Wells 1 and 3 have experienced similar uptimes to Well 2.
Well 3 “exhibited remarkable per-lateral-foot production” given that only about 4,933 ft of the total 11,847-ft length was thought to be contributing to the production, translating to a “substantial improvement” over ESP production, according to the paper.
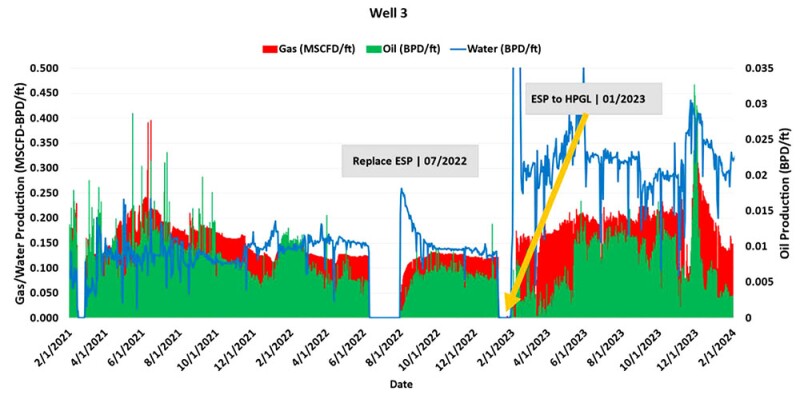
“This was a good success story for our company. After having lost a lot of value in the lateral, to be able to restore more production than we were making for that half of the lateral prior,” Fusselman said.
Between April 2022 and January 2024, Well 2 had achieved about 2.4 times return on investment due to its lower initial Capex, lack of workover expenses, and the operational efficiency of HPGL. Well 1, which suffered multiple ESP failures before being placed on HPGL, was nearing breakeven as of July 2024, according to the paper.
The three wells that are now on HPGL have not had to be worked over, he said, and production rates have remained flat.
“We are considering or have considered and installed high-pressure gas lift now in wells that we’ve had solids issues on, wells that didn’t have great cleanouts, or had a lot of sand issues, or a lot of solids,” he said. “It’s continued to be a very, very positive lift method for us.”
Early to mid-life applications of HPGL have generated good results, Fusselman said, and next, “we are looking to start trialing some potentially late-life” wells that are producing with rod pump lift systems.
If It’s Not Broken, Should You Fix It?
When Petrobras faced the question of whether to replace a seemingly functional gas lift valve in a deepwater well, it had to weigh the risk and cost of the intervention against the uncertainty of how much additional production might result.
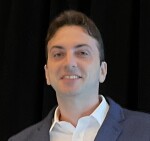
Tiago Perovano, a production engineer at Petrobras, said during ALCE that the valve had been in operation for more than a decade and seemed to function although signs of degradation in 2016 indicated the valve could compromise the well’s production stability.
But when downhole equipment is working, even with subpar performance, intervening to replace it is a costly choice. The question Petrobras faced was: “If it’s not broken, should you fix it?” In SPE 219537, the operator detailed how it approached that question for the well in 1365-m water depth offshore Brazil.
The well had shown instability since 2018, but it worsened in 2020 with more-frequent instability, Perovano said.
According to the paper, initial signs of instability were evident through observed increases in injection pressure, but subsequent delays in achieving stable gas injection followed, with instability in the well’s production, particularly following periods of shutdown, becoming noticeable.
To confirm and resolve the issue would require an intervention, which would run millions of dollars as well as the opportunity cost of using an intervention rig for this well meant delaying operations in other high-yield wells that were not producing or in a well with an immediate integrity risk, Perovano said. Beyond that, intervening involves its own risks, the paper said, noting problems with subsea equipment has sometimes significantly delayed intervention time, resulting in increased costs.
“Sometimes, when you get in a well, you discover other problems,” he said.
A well intervention would only be done if the expected increase in production value exceeded the cost of the operation. But estimating that number was tricky because of the inherent uncertainties of numerical simulations, particularly because production instability was a factor.
Despite the escalating injection problems, the valve was still operational and performing its safety function, as the well was producing and there was no flow from the tubing to the annulus. For the time being, in 2020, it was determined that intervening in the well was neither cost-effective nor beneficial.
In September 2021, the well’s valve became significantly blocked, leading to lost production.
“We had no choice but to try something,” Perovano said.
Petrobras attempted to clear the blockage, suspected to be caused by a check-valve inversion, by decreasing and increasing the well’s annular pressure to dislodge the check-valve mechanism and return it to its operational position, Perovano said.
The approach worked, but the next week, there was another complete blockage and shut in.
“We almost had a heart attack,” he recalled.
The block was subsequently reversed, but it became evident that the problem would be recurring. The potential benefits and risks of well intervention were clearer now, he said, especially given the risk that a future block might not be reversible. Petrobras greenlighted the intervention, which was carried out 5 months later.

Perovano said the team’s suspicions about damage to the gas lift valve were backed up when the valve was retrieved. Inspection revealed a damaged check-valve mechanism due to disintegration of the elastomer ring. The check‑valve darts were also found to be damaged. Together, this damage impeded the check‑valve’s movement.
The decision to conduct the $5.45-million intervention resulted in increased revenue of more than $2.5 million per month for the first 3 months, followed by sustained gains exceeding $1.5 million per month in subsequent months.
In other words, Perovano said, intervening in this well despite the equipment’s seeming functionality “paid off fast.”
For Further Reading
SPE 219528 Autonomous ESP Optimization Using Machine Learning Demonstrated in the Permian Basin by R. Erickson, R. Ramos, J. Meek, and D. Benham, Vital Energy; B. Haapanen, B. Hicks, and C. Wheeler, ChampionX; and B. Vasylyshyn, Softserve Inc.
SPE 219536 High-Pressure Gas Lift (HPGL) as an Alternative to Electric Submersible Pumps (ESP) in Wolfcamp Unconventional Wells—An Operational, Economic, and Production Performance Comparison by P. Dalamarinis, C. Hons, S. Fusselman, and I. Reese, DG Petro Oil & Gas; and B. Pepple, S. Schwin, W. Nelle, and R. Reynolds, Estis Compression.
SPE 219537 If It’s Not Broken, Should You Fix It? A Case Study on the Replacement of a Functional Gas Lift Valve in a Deepwater Well by T.G. Perovano, A.W. Quintino, B. Renato, and S.X. Bastos, Petrobras.
SPE 219552 Learnings From Successful Permian High-Pressure Gas Lift Installations by K. McNeilly, BP America; L. Harms, Optimization Harmsway LLC; and R. Reynolds, W. Nelle, and S. Schwin, Estis Compression LLC.
SPE 219553 Gas Lift Optimization in the Permian Using Machine Learning and Artificial Intelligenceby P. Movahed, D. Burmaster, E. Karantinos, and A.L. Villarreal, ExxonMobil Upstream Integrated Solutions Company; M. Memarzadeh, S.G. Vela, and S.C. Tapley, XTO Energy Inc.; and C. Newlin and T.A. Banes, ExxonMobil Global Services Company.