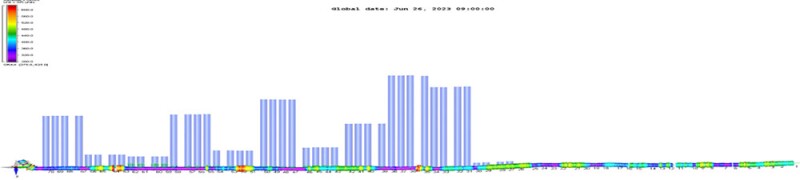
Production monitoring plays a critical role in the oil and gas industry throughout the production life cycle. It ensures optimal operational efficiency, safety, enhanced environmental compliance, and cost-effectiveness by identifying areas of production enhancement throughout the exploration and production processes.
The challenges of field development span from the exploration phase to multiwell developments and extend through enhanced oil recovery. When operating within harsh environments, such as deepwater or high-pressure systems, these challenges are amplified.
Deploying innovative tracers helps to solve the most difficult oil and gas production challenges related to geology, reservoir, production, and completions by providing specific subsurface measurements without the need for well intervention, shut-ins, or wires.
Phase-specific chemical tracers help track and characterize the flow, presence, and behavior of liquids and gases throughout the production process.
Innovative Approach To See Inside the Processes
Smart tracers are used to provide fluid-flow insights in both conventional and unconventional reservoirs, allowing customers to analyze well‑ and zone-specific production performance at a fraction of the cost of other monitoring tools and techniques.
The tracer production log eliminates the need to use expensive tools or wired systems to discover which part of a well is contributing each phase to the total flow. With this, water-entry points can be established and a water-cut profile can be provided along the wellbore with zero well intervention. The tracer production log information can then be used to develop and maximize the full reservoir field potential, as well as increase production.
Smart tracers also allow an operator to determine if a well cleanout program has been effective, indicate whether there is flow from all parts of the well, and assess lateral contribution in multilateral wells.
Oil-inflow and water-inflow measurement solutions, such as those delivered by industrial technology specialist Tracerco, provide a continuous picture of a well’s performance. They collect data on zone-specific production, cleanout effectiveness, water breakthrough, and plug, packer, or sleeve open or closed status.
Case Study: Production Optimization Through Tracer Technology
By partnering with Tracerco, an oil and gas reservoir development company in Oklahoma found success through the application of chemical tracers in its unconventional assets.
Tracers were used across two horizontal wells on a single pad to determine if there was flow along the entire lateral and to confirm whether the dissolvable fracture plugs had indeed dissolved.
The use of both water and oil tracers provided the verification of flow needed over the many months of production. The water tracers alone validated the need to allocate the resources and mill out the toe portion of the lateral.
Oil and water tracers also quantified the contribution along the lateral, which identified the production issues but also indicated different production trends related to changes made and the reservoir recovery.
Fig. 1 illustrates both wells and their stage numbers. One well had 70 stages and the other 71. Both wells were completed using a zipper stimulation technique, with individual water and oil tracers added every four stages.
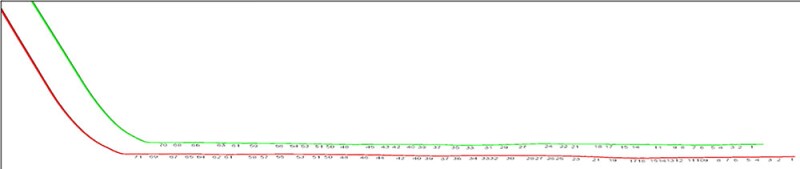
Both wells used dissolvable plugs in stages 1 through 30 and composite plugs in the remaining stages. After the stimulation, the composite plugs were drilled out, but all remaining dissolvable plugs were left in the wellbore. The well was shut in for a short period of time before being placed into production.
Fig. 2 shows the first well’s allotted production across the lateral after catching flowback samples and analyzing them for the individual tracers. Each bar chart is plotted against the wellbore path with colors illustrating the change in the gamma ray, as per the gamma ray legend. The bar chart displays the cumulative water production for each stage with the lower green bars illustrating oil production per stage.
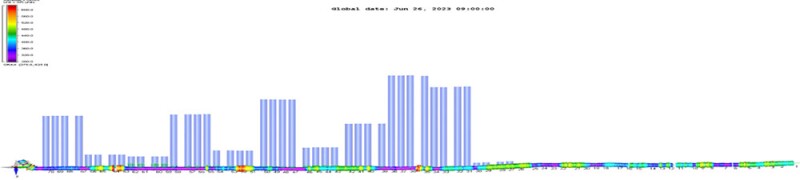
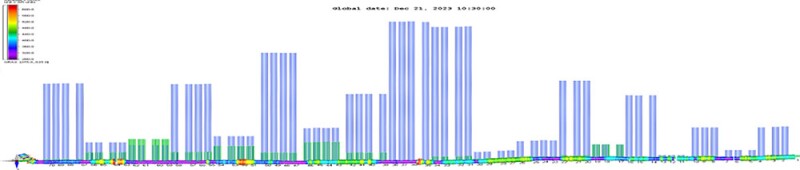
It is evident from the results illustrated in the upper chart of Fig. 2 that there was no production coming from stages 1 through 30, which is where the dissolvable plugs were located. The production on the chart is after 5 months, and the well had a bottomhole temperature of over 200°F.
At this point, the operator decided to go back into the well and drill out the remaining dissolvable plugs. The lower chart of Fig. 2 shows the allotted production shortly after the drillout. Substantial production was achieved after the obstructions were removed from the wellbore.
Figs. 3 and 4 illustrate the second well on the second well pad. Again, the results showed almost no production from stages 1 through 30 where the dissolvable plugs were located. After 5 months, the operator drilled out the dissolvable plugs and the well was placed back into production. As seen in Fig. 4, a significant increase in production was achieved.
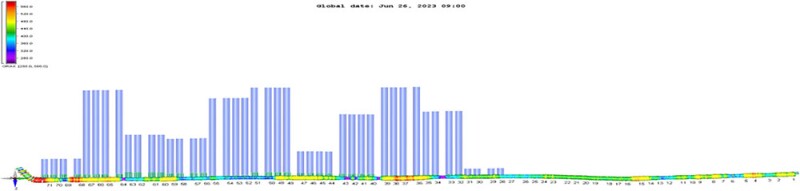
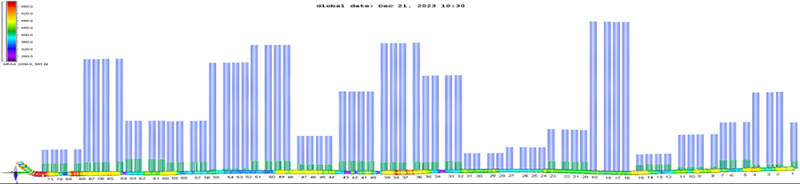
The improvement in results across both wells shows the effectiveness of tracers in identifying blockages within a horizontal wellbore.
Conclusions
As seen in this study, by using advanced chemical tracers, operators can pinpoint the exact location and nature of blockages, enabling quicker and more accurate diagnostics. This not only reduces downtime but also minimizes the need for costly interventions.
Choosing chemical tracers for conventional and unconventional wells provides precise and reliable tracking and analysis, allowing companies to optimize production, enhance operational efficiency, and make confident, data‑driven decisions.
The outlined approach enables monitoring of specific production phases, offering a way to quantify and measure factors that would otherwise be difficult to assess without intervention or costly permanent installations. By characterizing and measuring production over time, operators gain both short- and long-term data insights that support increased recovery, helping them stay competitive in today’s oil and gas industry.
For both conventional and unconventional wells, tracers offer a real-time understanding of well conditions, supporting optimal flow and improved production efficiency.
This case study highlights how a proactive approach enhances performance, boosts recovery rates, and reduces operational risks. Early issue detection leads to more informed decision-making and helps maintain the long-term health of the wellbore.
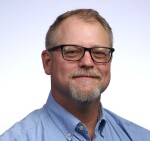
Patrick Hayes is Tracerco’s business development manager for North America. Having joined Tracerco in 2004, he has proven his expertise in chemical tracer technology by managing global multidiscipline projects with a focus on improving operator efficiencies and increasing customers' return on capital investments from upstream to downstream industries. While working in the North Sea, Europe, Middle East, and West Africa, Hayes’ innovative approach to applying novel measurement technologies has helped customers gain additional insight into the hydrocarbon production cycle, from subsurface to midstream and downstream refining. He is now focused on working with operators in North America to help them improve production efficiency through a better understanding of the relationships between reservoir characteristics, completions, and production.