As shale operators look for ways to survive amid the current downturn in oil prices, accelerating the refracturing of older horizontal wells is turning into one of the most attractive options. In years past, when oil prices were significantly higher, the more accepted proposition was to drill and complete new wells to increase production, book new reserves, and hold onto leases.
However, since late last year, the equation has been turned on its head. In many oil-rich plays, companies are realizing that refracturing is the more budget-friendly way to achieve cash flow. Compared with the USD 8 million to USD 16 million needed for a new well, most refracture jobs are reported to cost from USD 1 million to USD 3 million. In a well where all of the sunk costs have been recovered, the extra production and incremental reserves from refracturing can net several million dollars of added profit.
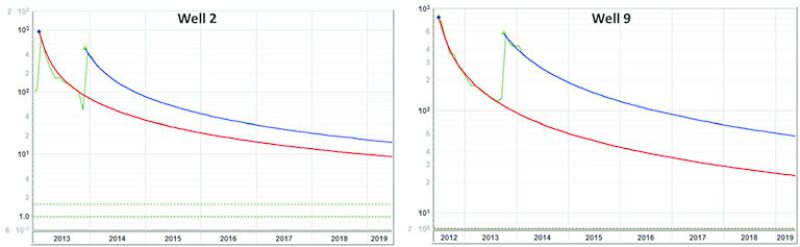
Tim Leshchyshyn, founder of FracKnowledge, said the current low-price market environment has become the biggest driver for companies to reinvest in their old oil wells. One operator that his company tracks is so sold on the idea that it is considering refracturing 500 to 1,000 wells this year.
“Refracturing is what everybody is banking on,” he said. “It is the thing they are trying to get figured out because there are going to be a lot of wells to do.” As operators and service companies climb their way up the learning curve, they are trying to determine which wells to refracture, which ones to bypass, and which plays it will work best in.
Only a few unconventional producers have published the results of their refracturing programs in oil-rich plays, and many others do not acknowledge having such programs at all. But there are years’ worth of case studies from gas-rich plays such as the Marcellus, Haynesville, and the Barnett, the birthplace of unconventional shale development, that indicate refracturing can be successfully applied in the oil-rich plays as well.
Mike Vincent, an independent consultant, is seeing unprecedented demand from operating companies for his courses on how, why, and where to do refracturing. While eager to learn all they can about refracturing, many of his clients are reluctant to discuss the topic publicly. “I think there are multiple reasons why there is radio silence right now,” Vincent said.
Companies still unsure of the success rate of refracturing may be trying to avoid overselling its potential to investors. Others are certain that it works quite well, Vincent said, but are staying quiet for competitive reasons, which includes the desire to buy out other operators’ offset wells and refracture them.
A recent field study by Baker Hughes offers a glimpse of the refracturing activity taking place in two of the highest oil-producing shale plays, and it appears to be going well. Based on the service company’s small sample of refractured wells in the Eagle Ford Shale in Texas and Bakken Shale in North Dakota and Montana, the study concluded that the process achieved an average increase in estimated ultimate recovery of 53% and 69%, respectively.
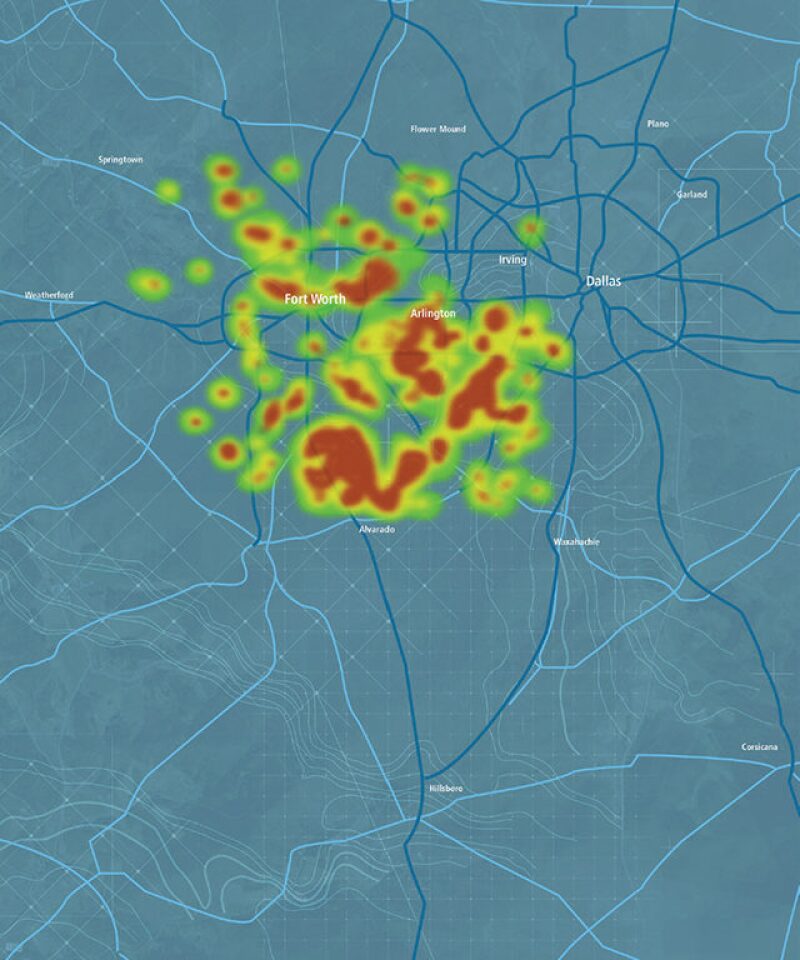
If refracturing proves to be successful on the scale of tens of thousands of wells, it will alter the shale industry’s status quo that requires the manufacturing-mode drilling of new wells to offset fast declining production from legacy wells. By contrast, the new take is that unconventional plays have stronger economics and will produce more hydrocarbons for a longer period of time than what conventional wisdom has held to be true for the past decade.
“It forces you to rethink your view on these plays,” said Dick Leonard, director of engineering diagnostics at Core Laboratories’ ProTechnics division. “It could be 30 years down the road, but we will look back and see that the vast majority of these unconventional plays will have a very large percentage of these wells restimulated. And in some cases, multiple refracs will be done.”
From Study to Service
To overcome the lack of available information from oil producers, Baker Hughes combined publicly available production data with an algorithm to identify potentially refractured, or recompleted, wells for its field study. Of the 16 oil wells in the Eagle Ford Shale and 22 in the Bakken Shale that were identified, every one of them showed incremental oil recovery after being refractured.
However, the results varied from well to well and between the two plays. Wells in the Bakken performed better, averaging a post-refracture production rate equal to 92% of the original rate. In the Eagle Ford, oil production after refracturing averaged 74% of the initial rate.
Why Refracture A Shale Well?The simple reason to refracture a well is to boost production. But to do that, operators need to pinpoint the problems they seek to remedy and then design the proper refracture treatment.
|
Based on its economic model, Baker Hughes determined that of the 38 oil wells examined, seven in the Eagle Ford and three in the Bakken suffered a reduction in estimated value. The remaining wells were all winners. After subtracting the capital costs of the refracture, state taxes, and royalty payments, the best Bakken well in the study was estimated to have turned a profit of USD 10.5 million. The profit figure for the best Eagle Ford well was USD 9.3 million.
The field study was completed using a suite of data mining and analytics technologies that are part of Baker Hughes’ new “rejuvenation” service, NextWave. Like the field study, the first aspect of the service involves identifying potential candidates using public data and a host of other proprietary data that covers every unconventional play in the United States.
“We do our homework,” said Sergey Kotov, a manager of integrated technology at Baker Hughes. “We start by looking at the overall field production, identifying the sweet spots, the locations of the wells, and then narrow it down to the performance of each particular well.” The process then applies a statistical analysis model to rank each well based on its overall probability of refracturing, or restimulation, success.
In cases where refracturing might not apply, Kotov said Baker Hughes’ screening service will help identify other ways to enhance production such as recompletion, chemical treatments, cleanouts, or even artificial lift installation. Because there are so many older shale wells completed before a given play’s best practices were discovered, refracturing will often be the primary solution.
How many wells will be refractured in each play is dependent on many things. Perhaps the most important factors are the well’s location in the field, reservoir properties, and the original completion design. Production history and product prices are also key parameters. “Any well can be restimulated or recompleted,” Kotov explained. “But everything boils down to the economic analysis and technical feasibility.”
There are no absolutes when it comes to candidate selection. While many claim that the best candidates are generally the best performing wells, Kotov said that is not necessarily a reason to overlook lower performing wells. “If it is located in the core area, then we have to identify the reasons behind poor production. And it might be one of the best rejuvenation candidates,” he said.
Shale’s True Potential
In his review of 100 refractured wells in the Bakken Shale, Vincent identified candidates that could be refractured with an 85% to 90% success rate, similar to Baker Hughes’ finding in its smaller study. Also similar to the Baker Hughes’ study, he has seen less impressive results from 20 disclosed Eagle Ford examples, which he partly attributes to initial completion strategies.
In the Bakken, Vincent said many early wells were completed with uncemented liners and using what is called a “pump and pray” stimulation job, or had only a single-stage fracture treatment. “That category of well is very easy to go back, refrac, and make money on,” he said, adding that this is especially the case if low-strength sand or resin-coated sand were used on the initial completion. Early Eagle Ford completions were more sophisticated, often multistage, and benefited from more advanced designs, leaving fewer obvious refracture opportunities.
Putting the differences aside, the various case studies from dozens of plays have convinced Vincent that initial completions in horizontal wells have unlocked a small fraction of the recoverable reserves. In defense of the industry, he said the rapid development of these plays has left little time for engineers to slow down and find ways to create long-lasting fractures to dramatically improve recovery. In a nutshell, the shale industry seems to be just scratching the surface of what is possible.
“It is really hard to calculate the original hydrocarbons in place in some of these shale reservoirs; we do not even really know what qualifies as pay. We are drilling into stuff that is microdarcy and nanodarcy that 30 years ago we thought was a barrier. Now, we are developing it as a reservoir,” he said. “So we do not know if we are draining 10% of the oil in place out of a small box, or whether we are draining 5% of oil out of a bigger box.”
Over time, refracturing may reveal how big the box really is. Based on the decades of industry experience refracturing high-permeability vertical wells that are 30 or 40 years old, along with the more recent experience in low-permeability shale gas wells, Vincent said he has been shocked at how well the process has worked.
And if companies do the math on a risk-weighted basis, Vincent said there is almost no reason not to attempt a refracturing program. “They can do a small experiment and if it works, they get to repeat that concept 100 times on the next wells,” he said. Where it does not work, he said companies can simply stop doing them.
Vincent is trying to get companies to realize that there are several reasons to carry out a refracture, and that they should not marry themselves to just one. Sometimes a refracture achieves what is called reorientation, whereby the second injection will change a fracture’s direction and “touch new rock.”
In other wells, refracturing is needed to replace crushed or embedded proppant or address scale, salt deposition, or fines that may be hindering the flow of oil. Or it might be for half a dozen other reasons. “I think what most people fail to do is recognize that refracs work for at least eight or 10 different mechanisms,” he said. “And if you are only thinking about one reason, then it will lead you down to the wrong solution. You will design the wrong refrac.”
The other thing he stresses is that companies need not be afraid of trying to refracture their better wells. Too often, the tendency is to test the water on a poor performer.
“That rarely is the most economic candidate. In almost every field where we have done dozens of restimulations, and we can go back to rank them, the most profitable refracs were almost always on the best wells, not on the worst wells,” Vincent said. “It really does demonstrate that when you can take a good well and make it better that we have some opportunities.”
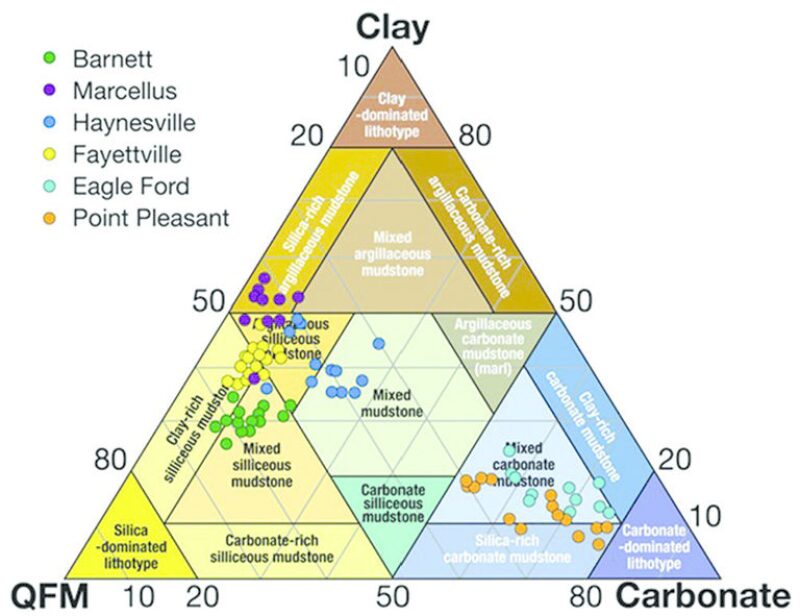
Shale is Creepy
Ibrahim Abou-Sayed, the president of i-Stimulation Solutions, agreed there are several reasons why a shale well needs to be refractured. However, he argued that the most common reason is fractures losing their connectivity to a shale reservoir because of rock creep. This happens when a formation under pressure begins to deform over time, eventually sealing off the fracture.
For shale wells, Abou-Sayed believes that rock creep is a fact of life and explains why a shale well’s production is reduced to a trickle after a few years of producing. The good news is rock creep also traps the reservoir pressure in the formation. He said the pressure may be measured with offset observation wells and will help deliver oil and gas into the wellbore once the fractures are reopened by refracturing.
Because each shale formation has a different mineralogy, creep seals fractures at different rates. New data show that one of the slowest rates is in the Barnett, with one of the highest rates being in the Haynesville. Found toward the middle of the creep spectrum is the Eagle Ford. “Those that have higher clay content are creeping the most and will be the first to go” and must be refractured sooner, Abou-Sayed said.
If companies learn about a play’s creep characteristics, he said, they can find ways to slow it down. The two best methods are to restrict a shale well’s production rate from day one, and to use more proppant in the completion phase to hold off the gradual deformation for as long as possible. In the end, Abou-Sayed said a refracture will still be needed—it is simply a matter of carrying it out at the optimal time in the well’s life.
Risky Business
Refracturing Risk FactorsWhile there are many reasons why an operator would want to refracture an older well, there are several reasons why it would not want to. Longtime producing wells are subject to wear and tear that may lead to a failure if high pressures are reintroduced in the well. The risk factors in refracturing are:
|
While there is no shortage of optimism on the topic of refracturing, there will be hiccups along the way. “Not every well will respond to refracturing. You are going to get some that were a total waste of money—almost like a dry hole,” Leshchyshyn of FracKnowledge said. “But then in other places, it will work just fine.”
He explained that as operators move forward, some are going to run into physical and technical barriers that will dictate success. It appears that this was the case for a few of the refractured wells in the Baker Hughes’ study. While the root causes were not explained, several incurred a decrease in estimated value of more than a million dollars, despite achieving incremental production. A worse outcome is a loss of production.
In his SPE webinar on refracturing in February, Abou-Sayed said in shale wells there is an optimum time to perform the refracture, and that operators should be aware of that. “Before which, you are not really adding anything,” he said, because the damage to the well’s fracture conductivity is not significant enough to warrant a refracture operation. “And if you wait too long, then there is a point where if you start fracking, you can lose the well.”
In a well that has been producing for years, the casing is not in the same condition that it was on the day it was installed. Older casings may be weakened for a number of reasons including corrosion, and a refracture may increase the risk of a failure. There may also be problems with the cement job, or a refracture may cause a negative interference with offset wells, called a “frac hit.”
Through testing and risk analysis, companies can estimate what pressures to use in a refracture and also if that pressure will produce enough hydrocarbons to justify the job. “How high can we go before we say it is bad for the casing?” Abou-Sayed asked. “Initially, it may sustain 10,000 psi of surface pressure. But at a later time, it may only sustain 8,000 psi.”
Tracing Performance
After a refracture has been done, the next step is to find out how it went and apply the lessons learned to the next job. Mike Flecker, president of ProTechnics at Core Laboratories, said the company is mining its diagnostics data from the dozens of refracturing treatments that it has worked on using proppant tracer technology.
The company thinks that by identifying the correlations from the best jobs, it can help develop a refracturing prescription that might include how much proppant to use, pumping pressures to apply, what fluid volumes to pump, fracturing rate, and type of diversions needed. But just like a medical prescription, the exact nature of the treatment will depend on the patient. “There is not going to be one cookie cutter answer,” even for the same sections of a field, Flecker said.
Proppant tracers are often used to tell if an “undrained” area of the reservoir was accessed. This provides confidence that new reserves have been added as opposed to accelerating the production of existing reserves.
If an operator used proppant tracers in a well’s initial completion, then the data may be used to establish a baseline for future opportunities. When proppant tracers were not used, Flecker said, “it becomes even more important that you do it on the refrac because that is the one that has even more variables than the original frac job.”
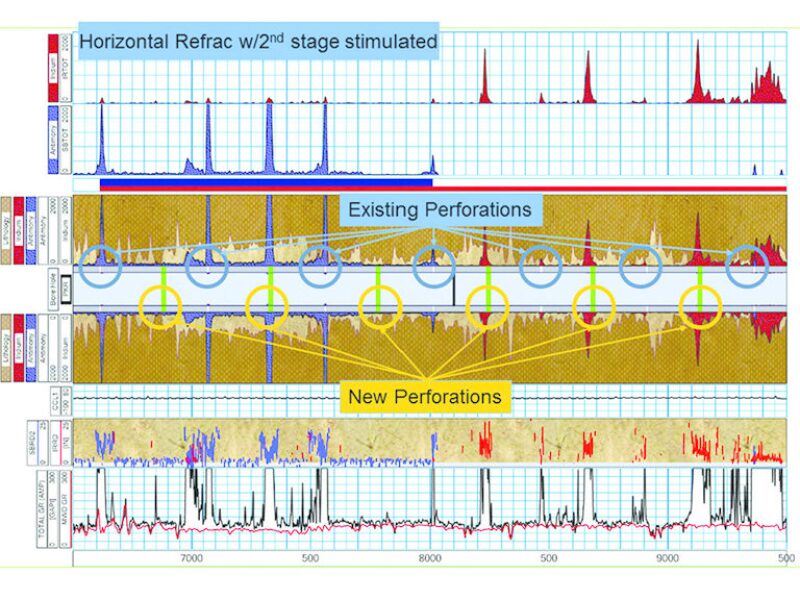
One of these variables involves the use of young diversion technologies. During a refracturing job, diverter balls or biodegradable materials are pumped downhole to temporarily block open perforations, thus diverting the refracturing pressure into new target zones. When these technologies fail to plug the old perforations, they may reduce the effectiveness of a refracture. A concern with diverter balls is that after the job, operators want to be sure that the blocked perforations are clear to allow production to resume.
Flecker said proppant tracers may be used to evaluate the performance of diverting agents. In a meeting with vice presidents and managers of completions from several operators, he said they expressed a strong interest in seeing diversion technologies improve beyond their current capabilities.
“If you can come up with a good diversion technique and have a formula for that, it would be absolutely huge,” he added. “You would be the big boy on the block. It is so important right now.”
For Further Reading
SPE 136757 CSUG/SPE 136757 Restimulation of Unconventional Reservoirs: When are Refracs Beneficial? by Mike Vincent.
SPE 173333 Refracturing on Horizontal Wells in the Eagle Ford Shale in South Texas—One Operator’s Perspective by Mamadou Diakhate, Pioneer Natural Resources, et al.
SPE 173340 Refracturing in Eagle Ford and Bakken to Increase Reserves and Generate Incremental NPV—Field Study by Yagna Deepika Oruganti, Baker Hughes, et al.