It has often amounted to little more than background noise. Now, engineers with one of the largest shale producers in the US consider the water-hammer signal to represent a potential trove of insight into stimulation performance.
ConocoPhillips has spent almost 3 years developing a new approach to water-hammer analysis and recently shared the first public details of that work in a technical paper (SPE 204154). Perhaps the core takeaway is that, within a few minutes of post-stage data, a picture of reservoir and stimulation quality is available. The challenge lies in how to bring that picture into proper focus.
The water hammer is a pressure pulse that moves through the wellbore at the speed of sound in fluid, or around 5,000 ft/s, which is more than fourfold the speed of sound in air. Its name comes from the often-audible slam made on one end of the pipe when a column of moving fluid is slowed or halted.
One is usually generated as a valve is turned, or a pump slowed or stopped at the end of a fracture stage. This makes the water hammer ubiquitous in the context of hydraulic-fracturing operations the world over.
As the wave bounces up and down the wellbore it generates noticeable pressure spikes on wellhead gauges. These oscillating signatures have been the subject of industry intrigue for decades. They’ve also proven to be difficult to decipher and trust.
As such, the water hammer has not entered into the shale sector’s pantheon of fracture-design inputs. ConocoPhillips’ ongoing research and development project may help change that.
Based on a review of treatment data from more than 150 of the operator’s low-permeability wells from an unnamed field in North America, those with fast-decaying water-hammer signals amounted to the best performers, achieving an output equivalent to 94–110% of their estimated recoveries. On the other hand, wells with more prolonged or low decay rates commonly fell 10–20% below their original type curve.
“The high decay rates indicated more near-wellbore fracture surface area, which related to higher well productivity. While conversely, low decay rates mean less near-wellbore friction, longer fractures, lower well productivity,” explained Dung “Zoom” Nguyen.
Nguyen is a staff completions engineer at ConocoPhillips and coauthor of the paper that she presented at the annual SPE Hydraulic Fracturing Technology Conference in May. She elaborated that analysis on frac hits, or fracture-driven interactions (FDIs), supports the relationship between fracture geometry and water-hammer decay rates, i.e., low decay rates equate to fewer, longer, and less-complex fractures.
Using treatment and offset well pressure data, ConocoPhillips determined that a significantly higher percentage of low-decay-rate wells had FDIs as compared with high-decay-rate wells. In a sample of 68 wells with FDIs, low-decay-rate wells located “very near,” “near,” and at a “middle” distance from offset wells showed an FDI occurrence rate of 95 to 100% vs. 40 to 70% for high-decay-rate wells.
The operator’s process appears to have broad applicability, hence the extent to which it is being studied, but ConocoPhillips is cautioning that the early learnings shared above come from a single field.
In terms of proving that the lessons do translate across geologies, the company is in the middle of expanding the analysis to more existing and newly stimulated wells in North America and South America.
Happening alongside the validation effort is the development of an algorithm that will automate many of the calculations involved. This step is needed to deploy the analysis to the field where it can be run in real time, something which ConocoPhillips hopes to accomplish by year’s end but with no firm timetable.
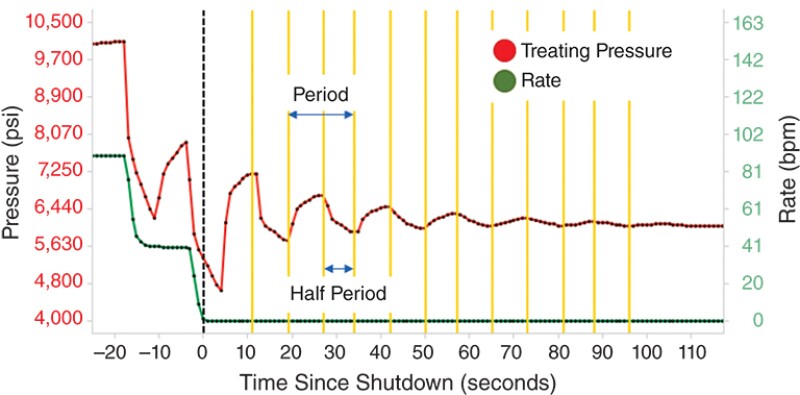
Testing the Limits
If the analysis could be used in real time, the prime objective would be to see if it can show whether FDIs are occurring with offset wells during the treatment. Depending on the interpretation, Nguyen said “we may perhaps decide to end hydraulic fracturing sooner or later.”
Averting unwanted FDIs is a clear value creator, but there are other nuances about downhole and reservoir activity that ConocoPhillips is confident it can wring out of water hammers. They include:
- Identification of treatment stage isolation. The water-hammer signal can help verify that fracture plugs are in fact isolating flow from previous treatment stages.
- Identification of casing failure depth. While treating conditions may be benign, stage-by-stage changes in the water hammer can point to fluid leaving the wellbore far above the current treating stage, potentially the result of a casing failure.
- Interpretation of fracture geometry and friction. The number of waves, or periods, and the rate at which they dampen is chiefly a factor of the water hammer’s physical contact with the fracture system beyond the pipe. This applies to a plug-and-perf scenario, a marquee use case for the water-hammer analysis but one in which ConocoPhillips is not attempting to quantify fracture geometry (i.e., length, height, or width).
The last point underscores that there are limits to this new approach.
ConocoPhillips has determined that the water-hammer signal simply lacks sufficient detail to identify fracture dimensions with certainty.
“That is outside of the realm of water-hammer analysis completely,” said Dave Cramer, a senior engineering fellow at ConocoPhillips and coauthor. “Is it going to give you insights on the qualitative aspects of your fracture? Yes, but you need to draw the line there.”
Catching Waves
Nguyen noted that the initial driver for this research effort was to “understand some of the myths or truths” associated with using the water hammer as a reliable decision-making tool.
Prior work with respect to hydraulic-fracturing diagnostics dates to the 1980s. Only over the past few years, though, have commercial solutions entered the market from academia and private technology developers.
ConocoPhillips has drawn on some of the accumulated knowledge, but in regard to the existing techniques, the authors concluded that “the optimization problem is ill-constrained, leading to nonunique solutions.”
This led the company’s engineering team to devise its own solution. Its chief distinction is that a physics-based simulator is used to account for the fluid mechanics (e.g., pipe friction) inside the pipe that contribute to the shape of the waveform.
Isolating this moving target depends on several factors, including but not limited to changing fracture-stage depths, fluid volumes, and rates. Not solving for these risks overweighting the influence of the hydraulic-fracture area on the signal, which is equal to overestimating the size of that area, according to the operator.
After modeling a more reliable signature, the focus boils down to counting the wave’s peak-to-peak spans, or what are called periods. In the North American study area (categorized into wells with two different average proppant loadings) the best performing wells averaged five periods or fewer per stage. The threshold for becoming a poor performer was crossed after six or seven periods. (These are, again, situational learnings that need to be calibrated for different geologies and fracturing designs.)
From an operational perspective, it can take up to 3 minutes at the end of each fracture stage to capture the wave’s round trips before it dissipates completely. This is not an insignificant amount of time in the fast-paced completions arena, however, and the authors note in the paper that it “may conflict with goals for reducing time between operations.”
In terms of how long it takes to analyze the data, Nguyen said it depends on the complexity of the questions being asked.
“On a single-stage basis to determine casing-failure depth, this is a simple analysis. As we move to treatment isolation, the identification of the period time manually is not too difficult, but there are some additional interpretations to properly identify sections,” she said, adding, “There is still more to do on the multivariate interpretation as we have to analyze a lot more data for statistical relevance.”
The paper offers recommendations on generating quality water-hammer data through consistent rate reductions. This raises another key point: a water hammer is not guaranteed on every stage, and its absence should raise flags.
“It requires good conductivity from the entry holes in that wellbore into your fracture system,” explained Cramer. “If you have a torturous flow path, the development of this boundary for water hammer—where you’re communicating into the high-capacity fracture system—is going to be really hard to see.”
He added that this will also be the case when proppant bridges over open perforations, causing a screenout.
Minding the Data Problem
At a high level, counting peak-to-peak events and correlating the numbers back to well production sounds straightforward. To the contrary, Nguyen assured her peers during the conference that it is “quite complicated.
“We’re working on some processes to make it a little bit simpler,” she said, adding that with faster simulator and modeling results, engineering teams will be able to identify “some of the juicy items sooner.”
Outside of the software work flow, ConocoPhillips had to address the myriad bottlenecks that exist at the data-acquisition stage. This explains why, in addition to covering practical applications, the operator’s 47-page paper on water-hammer analysis devotes several sections to recommending stricter field data practices.
The advice revolves around the operator’s drive to keep water-hammer analysis a low-cost diagnostic by relying on garden-variety wellhead pressure gauges. These are the gauges used by most of the industry’s pressure pumpers and they commonly take pressure data samples just once per second.
More sophisticated sensors take 50 samples per second which is useful for fine-grained research, but the authors said such resolution is not necessary to identify the pressure trend that is at the heart of its analysis.
“For water-hammer analysis, it is the ability to see change—the decay rate—that is more important than accuracy,” explained Nguyen.
That said, operators should be wary about taking for granted the data they rely on from standard gauges. The issue stems from both the hardware and problematic data-management practices on the pressure-pumping side of the business.
Out of 15,000 fracturing stages analyzed so far using its analysis, ConocoPhillips found about 20% suffered from poor data quality. As listed by the operator, those issues included: data acquisition halted before water hammer ended; incorrect representation of wellhead pressure; false injection rates; smoothed data; and data accuracy.
In one highlighted well, side-by-side use of high-spec sensors and a standard gauge showed that the latter measured 120 psi below the more sophisticated models for most of the stimulation. Furthermore, the standard gauge recorded false pressure drops and spikes while completely missing other subtle fluctuations in wellhead pressure.
Outside of the water hammer, the operator is looking into leveraging another end-of-stage data point called instantaneous shut-in pressure. In trying to solve for this metric, the measurement issues listed above become much bigger bottlenecks.
ConocoPhillips emphasizes that taking a more active role in working with service companies on data management is the key to correcting problems before they render the analysis into a data quagmire.
In addition to the recommendations listed in its paper, the operator is also encouraging the adoption of the contract addendum that was introduced last year by the nonprofit Operators Group for Data Quality.
For Further Reading
SPE 204154 Practical Applications of Water-Hammer Analysis From Hydraulic-Fracturing Treatments by D. Nguyen, D. Cramer, T. Danielson, ConocoPhillips, et al.