Field-proven, nonmetallic, thermoplastic composite pipe (TCP) technology can now be found in every oil and gas region, globally. Fully qualified for flowline, jumper, and spool usage, TCP lines can be used for full wellstream service (hydrocarbons), water injection, chemical injection, methanol injection, gas lift, and intervention. TCP products can currently be installed and operate at pressures of up to 12,500 psi, and in water depths as low as 3000 m.
The focus is now on the development and deployment of TCP risers for extreme environments. Following the launch of a qualification program with Subsea 7 to certify TCP for dynamic riser applications, Airborne Oil & Gas is collaborating with engineering company SÍMEROS Technologies to deliver the first qualified TCP risers in the deepwater region of Brazil.
The program is receiving funding from a major operator in the region and is aimed at qualifying the TCP riser for pre-salt and highly corrosive conditions. As the world’s first fully-bonded, free-hanging composite riser, it is expected to save an estimated 30% on as-installed cost and be 45% less expensive than a flexible pipe in a lazy wave configuration.
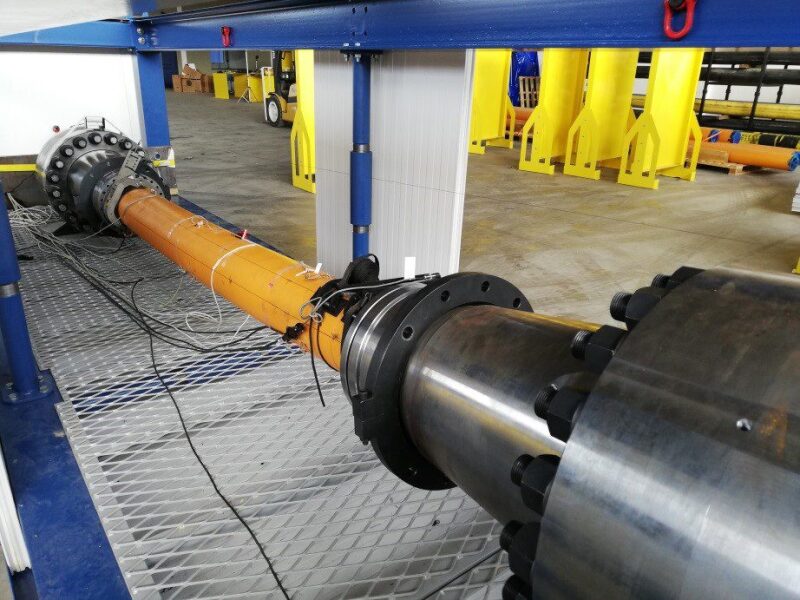
Lowest-Cost Solution for Total Installation
The qualification program, which began in mid-2018, investigated the potential for a disruptive new riser pipe technology for operators with international deepwaters.2 It involved the combination and development of the right thermoplastic matrix and fiber material for each application. This would aim to give operators maximum flexibilty in terms of subsea configuration and choice of installation vessel.
Ivan Cruz, technology manager at Subsea 7, believes the TCP riser can become a compelling solution for future deepwater fields. “As a fundamentally simple pipe, the technology has a disruptive potential. It is a straightforward solution that equally removes the need for bouyancy requirements.”
Airborne Oil & Gas employs a specific “staircase approach” for each of its clients, whereby operators can execute collaborative studies and pilots to optimize the disruptive potential and performance of TCP in their operations as well as build acceptance within the organization.
SÍMEROS Technologies is now supporting the company with local qualification, development, and manufacturing of the TCP end fittings and ancilliaries for the flexible pipe.
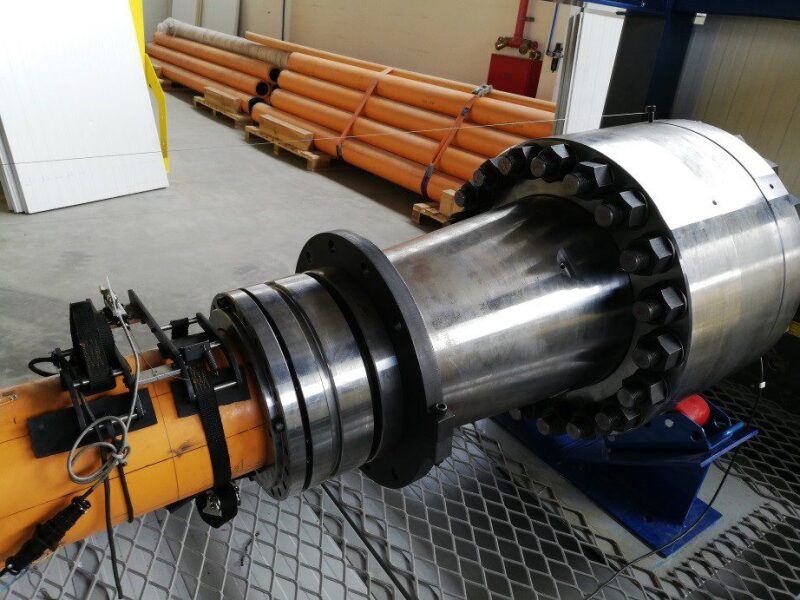
As a disruptive alternative to conventional risers on the market, the TCP riser is completely resistant to any form of corrosion, including corrosion stress cracking caused by high levels of CO2 and H2S.
Fabiano Bertoni, co-founder and director of SÍMEROS, said, “This exciting qualification program may change the face of the subsea industry in years to come. It involves rigorous testing with full monitoring by DNV GL and a clear ‘staircase’ approach, leading to qualified TCP risers for hydrocarbon and water and gas service, in deepwater and dynamic applications.”
Simplicity by Design
With innovation and lessons learned from the aerospace sector, TCP features a solid pipe wall constructed from glass or carbon reinforcement fibers and thermoplastic polymeric materials. The unique and proprietary melt-fusing manufacturing process results in a true composite structure, with the fibers fully embedded within the polymer matrix and ensuring the strongest interface possible between the different pipe layers.
The fibers are linear in behavior and typically do not show plastic deformation or yielding. This creates a robust spoolable pipe, 80% lighter than metallic equivalents, and adapted to customer-specific requirements.
Composite material for risers requires the highest purity, as well as resistance to solvents, acids, and hydrocarbons. Established in 2007, the Netherlands-headquartered company is conducting material modeling via simulations in order to predict and understand the behavior and longevity of composites.
To develop the most robust and reliable material for deepwater risers, combinations of carbon fiber with polyethylene, carbon fiber with PVDF (polyvinylidene difluorid), or glass fibers were investigated and tested virtually. It was found that PVDF, which already has a solid track record in production riser or flowlines, gives the best performance for deepwater risers in terms of mechanical performance, submerged weight, chemical resistance, minimum bend radius, ductility, and cost. It aims to be qualified for up to 8 in., 10,000 psi, and a temperature rating of 121oC (250oF), and has a design life of 30 years.
The combination of carbon fiber and PVDF material is extremely strong and stiff and is embedded in the thermoplastic polymer and oriented in one direction to deliver high tensile and axial strength. Minimal bend radius can be created by optimizing the angle at which the carbon fiber is placed and wrapped around the pipe, which also eases installation from the vessel.
To qualify this relatively new material, full-scale pipes were tested on critical load cases to prove the accuracy of the design predictions, hence proving that the design appropriately covers all single and combined loaded cases.
DNVGL-ST-F119 is the first standard for the requirements for flexible TCP for offshore applications and was spearheaded by Airborne Oil & Gas in 2015. The document supports operators in their choice of TCP instead of steel or traditional flexibles for pipelines or risers.
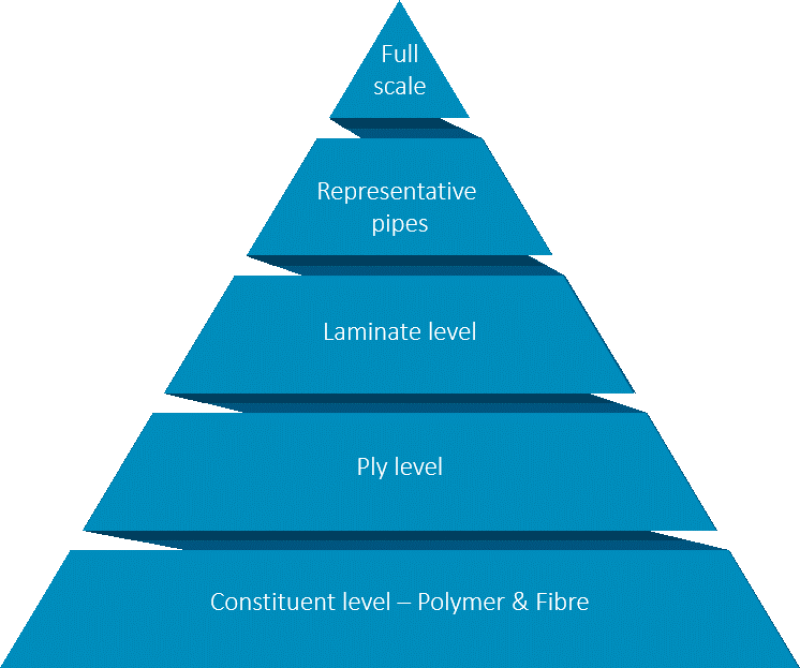
At the lower levels, material performance is measured and tested with infield conditions such as fluid, temperature, etc. Subsequently, the tested material performance is translated to validate a model based on fiber and polymer. Finally, the predicted pipe performance is validated by full-scale tests.
Eliminating Fatigue
Before the introduction of TCP more than a decade ago, steel catenary risers (SCRs) with buoyancy support were the traditional type of riser for deep and ultradeep waters. Over the past 20 years, more than 275 have been installed globally.
With more extreme production conditions and a trend toward tiebacks to older floaters, the use of lazy wave SCRs has been gaining popularity due to their reduced payload on the host vessel and their ability to control strength and dynamic response along the riser. However, costly design challenges such as weight, shape optimization, and fatigue performance have opened the door for a more innovative and alternative solution.
To achieve a free-hanging catenary at 2400 m water depth, the Airborne Oil & Gas performed a detailed study on a 6-in. water alternating gas line for a major operator in a large pre-salt field, 240 km off the Brazilian coastline, using a spread-moored FPSO. This involved the top of the TCP being optimized for high tension, while the bottom riser was enhanced to comply with the high curvature.
As the composite solution is significantly lighter than conventional steel risers, it thereby reduces the tension load by 50% at the hang-off point. Therefore, as fatigue is not driving the cross section of the design, the bottom riser is essentially the same as a flowline. Being lightweight, TCP reduces the loads on the FPSO. As a result, this allows the future design of FPSOs to be smaller, or a normal FPSO can be used but with more processing equipment installed. A combination of both is also possible (slightly smaller FPSO with a bit more processing equipment).
Likewise, the low weight, spoolabilty, and flexibility of TCP combined reduces the loads on subsea structures and connectors.
Also, fatigue loading often requires operators in deep water to replace part of the flexible risers during their lifetimes—often every 3 to 5 years for pre-salt fields where fluid composition (high CO2 and H2S) is very challenging for conventional solutions. This ultimately eliminates both the cost of the buoyancy modules themselves as well as the installation. Furthermore, TCP requires fewer connections to be made offshore, which further reduces installation time.
As part of the qualification program in Brazil, Airborne Oil & Gas is also investigating the development of weight-coating technology to ensure the system is stable when filled with water or gas while minimizing top-tension loads. The weight-coating compound is the combination of a heavy filler and PVDF materials as the base polymer.
Detailed engineering as well as installation and preliminary assessments so far shows feasible in-place configuration and installation for TCP risers in deep and ultradeep-water environments and importantly, a large margin of safety.
Long-term Cost and Environmental Savings
TCP risers up to 7.5-in. inside diameter, 121oC (250oF), and 10 ksi working pressure can be installed by existing flexlay and reellay vessels and be deployed in the flexible and more cost-effective free-hanging catenary mode as the shortest distance to the seabed.
Installed in free-hanging catenary configuration, the lightweight and fatigue-insensitive TCP riser provides the opportunity for significant savings on typical pre-salt developments, through faster installation and avoiding the need to use buoyancy modules. Compared to flexible risers in lazy way configuration, based on total installed costs, operators can save between $160 million to $200 million per FPSO, based on around 20 risers per facility.
It is antipated that, compared to steel, the whole manufacturing process to create and install fully composite pipes can deliver a 30% reduction in carbon footprint.
teamlead structural design and has held the position of engineering manager since
2014. Before joining Airborne Oil & Gas, Henk spent 13 years in advanced
lightweight engineering in various roles and the past 8 years as chief operational
officer. He holds a doctor's degree in mechanical engineering from Delft University of
Technology. He may be reached at h.deboer@airborneoilandgas.com.