In recent years, the oil and gas industry has placed significant emphasis on digital transformation. For most early adopters, this journey began with real-time monitoring and remote operation of equipment. This has been followed by the increasing application of modern data science techniques in order to extract actionable insight from the growing volumes of data. The emergence of highly scalable data storage and compute power has provided a step change in the ability to derive actionable insights from data and perform simulations at a scale previously inaccessible. What we derive from this combination allows us to deliver new levels of performance and efficiency. But, in addition to these now well recognized elements of the digital transformation, there is a need to evolve our industry hardware through the application of enhanced edge computing and the application of intelligence at the edge.
There will, of course, continue to be engineering innovation in our hardware, resulting from creative new designs that result in new functional features, cost efficiency, enhanced reliability and greater operational performance. But there are now myriad opportunities to enhance hardware in ways that maximize the value of data capture. Thus, the emergence of connected, intelligent hardware is key to realizing the vision of the digitalized oil field.
Connected, Intelligent Hardware Explained
Much conventional hardware has little to no digital enablement or means of monitoring its own function or state. In a first step, it is largely trivial to make it connected to cloud-based data stores, thus enabling the use of modern data analysis techniques such as artificial intelligence (AI) and machine learning (ML). Each piece of hardware in this scenario will benefit from remote intelligence to enrich its capabilities.
Intelligent hardware takes the “connected” concept in another direction and refers to equipment with embedded edge computing that can host models and algorithms, creating capabilities beyond remote intelligence. These machines can now take advantage of both edge and cloud digital capabilities to learn and gain intelligence, thus continuously improving operational performance and service delivery.
By populating oil fields with connected and intelligent hardware, operators gain access to optimized, secure, and sustainable operations. Connected and intelligent hardware enables advanced planning, real-time performance optimization, and higher levels of automation and health management. It is a critical part of a broader architecture that is adapted to problems where latency, communications fallibility, and system reliability are important considerations that make a central command-and-control approach inappropriate.
Developing Intelligence
Intelligence in this context is mostly based on models that describe equipment status and operational behavior. These models, depending on their intention, may be hosted in the cloud or at the edge, and can be considered to constitute a virtual representation of the equipment, often referred to as an avatar.
These models are frequently described as being driven by data, which means they adapt as more data are acquired and nuances in behavior emerge that better describe the true nature of the equipment. Models may require a combination of operational data, life cycle data, such as manufacturing and maintenance, and contextualization data, such as location and environment, to provide the best representation. They are also best generated by the application of expertise and understanding from data science, applied technical domains, and the physical sciences.
The industry is still in the early stages of developing and deploying avatars. Currently, when an avatar is used, it is quite often one core function of the hardware that is virtualized, and models lack predictive and prescriptive capabilities that capture complex interactions of functions. As the richness, quality, and quantity of data increase, combined with domain and science expertise, more advanced models will emerge.
Barriers to Adoption
For the industry to fully embrace connected and intelligent hardware, it must rethink how hardware is developed and how data openness is perceived.
From an engineering perspective, hardware designers typically seek mechanical or electronic solutions to develop new hardware or improve existing design. Moving forward, digital features must be central to hardware design, not just attachments or added features. Such a change will deliver enhanced product performance and minimize costs. To achieve this, engineering teams must engage digital stakeholders in the early stages of product development.
The availability of data largely influences the industry’s digital journey and directly affects engineering innovation. The industry’s steps toward open-sourcing a data ecosystem or environment are crucially important to this journey. They will provide the right environment and standards for organizing data—the first step toward collecting, integrating, managing, and enriching data, thus accelerating digital progress. In 2019, Schlumberger formally announced its commitment to open-sourcing its data ecosystem and contributing to the Open Group Open Subsurface Data Universe (OSDU) Forum. Our contributions, combined with others within the industry, are providing unique capabilities and experience that are revolutionizing exploration and production (E&P) workflows.
Practical Application
The entire E&P value chain stands to benefit from the performance enhancements and equipment efficiency that digital hardware will deliver.
In the drilling domain, Schlumberger developed an at-bit steerable system (ABSS) for drilling horizontal wells in a single run. The ABSS utilizes digital technology by combining trajectory-control algorithms with machine learning and data analytics to improve planning and execution that adapts itself to the nature of each specific run.
In the reservoir characterization domain, we have introduced a connected and intelligent wireline formation testing platform—the industry’s first integration of downhole hardware and cloud native software—that delivers a step change in reservoir evaluation. Intelligent planning enables “look ahead” during operations, while real-time operations control utilizes edge technologies and automation for continuous quality control and high-precision fluid sampling and analysis. Contextual insights provide detailed 2D and 3D visualizations on interactive dashboards to assist in making informed decisions.
For oil and gas processing facilities, acid-gas membranes are widely used for removing CO2 from natural gas. Changes in operational practices or conditions of natural gas feed streams can result in damage to these complex systems, which leads to undesirable product gas specifications. To address this challenge, we are utilizing a data-enriched performance service that digitally enables dynamic forecasting of future performance of acid-gas membrane systems. The service uses a secure, cloud-connected, ruggedized edge computing device to collect and extract meaningful insights from data streams. This reduces the time and interactions between detection, diagnosis, and the resolution of unplanned shutdowns.
Environmental Stewardship
As the global community calls upon the oil and gas industry to deliver safer, environmentally sustainable operations, digital enablement provides a significant opportunity for the industry to drive long-term change. For example, an integrated, data-driven strategy that combines intelligent hardware, edge computing, and cloud-based greenhouse gas applications can improve upon asset integrity for oil and gas processing facilities, which is core to curbing fugitive methane emissions. Furthermore, by providing data access via cloud environments, remote control, and automation, we can significantly reduce trips to the field, thus directly decreasing our carbon footprint and improving overall safety.
Digital Is the Present
Our industry’s digital transformation is well under way and the challenges of the current commercial environment are an added impetus for accelerating change. Amongst the many other aspects of this transformation, connected, intelligent hardware is a critical element driving our innovation and strategy. By industrializing and scaling it, the future of the industry will soon look very different. It will be proactive, agile, efficient, safer, sustainable, and more customized to customer needs than ever before.
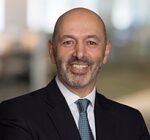
Demos Pafitis is the chief technology officer at Schlumberger, a position he assumed in February 2020. He is responsible for Schlumberger New Technology Development, Digital Technology Development and Manufacturing. Prior to his current appointment, Pafitis served as senior vice president of Schlumberger 4.0 Platforms. He joined Schlumberger in 1991 and worked in the research and engineering organization in Cambridge, UK, and Houston. In 2000, he assumed responsibility for marketing and technology introduction of Schlumberger rotary steerable systems and directional drilling services. He later held research management positions in Boston, Massachusetts, and Cambridge. In 2007, Pafitis was appointed vice president engineering for Schlumberger Oilfield Services. In 2012, he assumed the position of GeoMarket manager for Malaysia, Brunei, and Philippines. In 2014, he served as global vice president engineering, manufacturing, and sustaining. He holds a bachelor’s degree in materials science and engineering from the University of London and a doctorate in materials science and engineering from the University of Cambridge. He is a Chartered Engineer in the UK.